1. 引言
现有的运载器级间分离通常采用热分离方案,级间段上须开排焰口来满足发动机点火的排焰需求,对于蒙皮桁条铆接部段,排焰口设置在相邻桁条和中间框之间,为矩形结构 [1] 。为保证排焰效果,排焰口数量较多,一个级间段产品上多达上百个排焰口。某产品一二级级间段排焰口位置如图1所示,位于级间段靠近下端框处,沿周向进行布置。级间段产品采用壁板方式装配 [2] ,先在壁板自动钻铆设备上完成壁板的自动钻孔和铆接,再在铆接型架上完成壁板的组装。为保证开口位置的准确性,排焰口通常在蒙皮与桁条铆接完成后再制出。
排焰口的传统制造方法为手工钻孔后再铣磨,但这种方式存在精度差、效率低、工人劳动强度大等问题,同时壁板结构产品无法采用普通的数控加工设备进行装夹。随着自动钻铆技术的应用,在进行壁板自动铆接后可以利用壁板设备的铆接末端拓展铣切功能,直接进行排焰口自动铣削,无需进行装夹,从而提高加工效率和铣切质量。诸多学者对自动钻铆进行了工艺研究,得出钻孔、铆接最优工艺参数 [2] [3] ,但尚缺乏对部段状态下铣削窗口的工艺研究,本论文为国内首次利用壁板自动钻铆设备进行在产品壁板状态下进行铣切。目前研究进展为成熟应用阶段,形成了完备的工艺技术。
2. 手工铣切工艺方法
排焰口的传统手工铣切方法如图2所示,根据图纸或者安装样板划出排焰口位置线,使用风钻沿排焰口轮廓连续钻孔,使用榔头锤掉排焰口蒙皮,使用风铣刀一点点把排焰口修齐,打磨切口直至符合设计尺寸及光洁度要求。该方式存在以下不足:精度差,尺寸难以保证。操作过程完全靠手工保证,定位精度差,且对人员熟练度要求较高。效率低、劳动强度大。需使用风钻将开排焰口部位轮廓密密麻麻地钻出孔,上百个窗口通常需要4名操作者连续工作3天才能完成。操作过程中需要高强度的重复性劳动,操作人员极易疲劳。存在损伤产品风险。操作过程人工操作,容易出现工具脱手损伤蒙皮的问题。

Figure 2. Flow chart of traditional production process of drain port
图2. 排焰口的传统制作工艺流程图
3. 自动铣切工艺方法
3.1. 壁板定位
级间段壁板在壁板自动钻铆设备上的定位如图3所示,在自动钻铆设备上完成壁板的自动制孔和铆接后,产品不下架,更换铣刀进行排焰口的铣切。
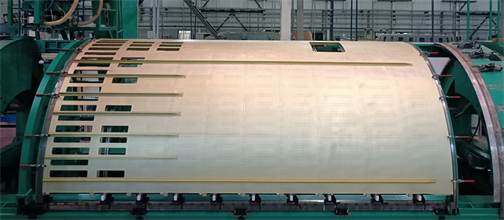
Figure 3. Positioning of inter stage panel on panel automatic drilling and riveting equipment
图3. 级间段壁板在壁板自动钻铆设备上的定位
产品长达四米,桁条在这个长度上直线精度非常差,而排焰口均位于各个桁条间,若沿着桁条边直线铣切排焰口边缘会伤到桁条或者排焰口距桁条过远。设计要求窗口铣切精度为±1 mm,采用手工铣切时可用样板或人工划线来保证,但自动铣切时,由于桁条定位精度为±1 mm,同时考虑设备本身精度、壁板定位精度等,很难保证窗口铣切精度,因此亟需进行技术攻关。
3.2. 铣切工艺参数研究
影响铣切质量的因素主要有:主轴转速、进给量和刀具半径。主轴转速是铣切的重要工艺参数之一,合理选择设备主轴转速参数不仅能提高加工效率,同时可以减少毛刺产生,保证铣切质量 [4] 。结合生产经验,初步选择转速4000 r/min~10,000 r/min作为试验参数。采用试验件进行铣切工艺参数研究。铣切时切削效率与主轴转速、进给量有关。如果进给速度过大,容易产生毛刺等缺陷,造成铣刀烧蚀、折断;但进给速度过小,铣切效率低下,初步选择进给量0.03 mm/r~0.08 mm/r。刀具半径影响铣刀径向跳动,进而影响切削性能、铣切质量。初步选择刀具半径R10。综上,初步确定的铣切试验工艺参数范围如表1所示。
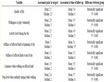
Table 1. Product inspection refined management process description
表1. 产品总检查精细化管理流程描述
针对表所列工艺参数范围按照三个参数水平进行细化,3项参数运用L9(33)正交表设计试验,如表2所示(其中L代表正交表,角标9代表试验次数,角标3表示因素个数,3表示因素的水平数)。
铣切试验初选方案见表3所示,以铣窗口余料平均毛刺高度作为定性评价指标,依据试验方案确定的参数组合试验铣切,重复10组,取均值作为该组试验的最终结果进行分析,见图4。
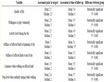
Table 3. Milling test parameter primary scheme
表3. 铣切试验参数初选方案
初选铣切试验结果如表4所示,对结果数据采用极差分析法进行分析。根据余料平均毛刺高度结果数据:对比
、
、
,最优的刀具半径参数为
,且对比
、
之间的差距较小,更优的主轴转速参数在A1与A2之间;对比
、
、
,最优的主轴转速参数为
,且
与
之间的差距较小,更优的主轴转速参数在B2与B3之间;对比
、
、
,最优的进给量参数为
、,且
、
差距较小,更优的进给量参数在C1与C2之间。综上,初选试验得出的最优铣切参数为A2B2C1,且进一步优选试验的参数选择范围界定为(A1~A2)、(B2~B3)、(C1~C2)。
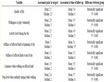
Table 4. Primary test results and analysis
表4. 初选试验结果及分析
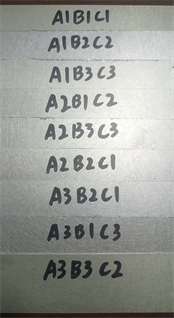
Figure 4. Results of primary test and optimal test
图4. 初选试验、优选试验结果
根据初选试验结果,在选定的参数范围内再次细化参数水平进行优选试验,具体过程不再赘述,铣切工艺参数试验得出的最佳铣切参数如表5所示,依据表5的参数进行验证试验,进行排焰口铣切,平均毛刺高度符合要求,无需单独的毛刺清理工序。
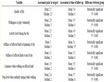
Table 5. Milling process parameters
表5. 铣切工艺参数
3.3. 基于线激光校准的桁条高精度定位技术
壁板自动钻铆设备自带线激光器,可充分利用线激光定位器来提升桁条定位精度,将线激光器定位于壁板自动铆接设备预装配平台的定位框的轴向方向上,利用线激光器打出的直线与桁条轴线进行对比,保证桁条轴线与线激光线重合,如图5所示,通过此方法,桁条定位精度可提升至±0.5 mm。
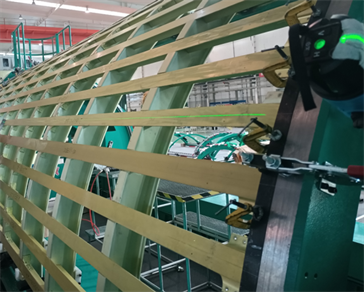
Figure 5. Line laser positioner calibrates the truss axis diagram
图5. 线激光定位器校准桁条轴线图
3.4. 粗铣留余量–精铣角度补偿法技术
桁条装配精度大幅提高,但依然无法使用数控程序一次铣切到位,为此借助了粗铣加精铣的方法,通过粗铣后测量排焰口左右两侧余量差,在精铣时用主程序来补偿角度,实现排焰口精准自动铣切。
如图6所示,图中红色轴线作为主程序的窗口理论中心,同一种窗口使用相同的子程序,但理论中心线与实际窗口中心线往往不重合,所以粗铣子程序的加工范围一般留余量1 mm~2 mm,通过粗铣后测量两侧余量,将精铣程序主程序轴线做偏心处理,以实现精准铣切。
铣切后的排焰口处蒙皮掉落,容易出现蒙皮飞出伤人、卡停设备等问题,通过分析掉落模式和程序编制的便易性,在每个排焰口两侧各留余量,保证铣切后蒙皮仍丝连于产品,统一拆除,提高了铣切的安全性和效率。
3.5. 基于程序嵌套的快速编程技术
排焰口编程量很大且排焰口拐角程序难以实现,为此借助了程序嵌套的方法,将排焰口分类为若干类型,各自形成子程序,主程序定位各个排焰口角度,同时定制异型铣刀,实现一键铣切。
实例如下:
G55
SOFT
FFWON
S8000 M3
M27
G90 G01 A=-1.224 F80
G01 X=4183 F60000
ZZ1002 %根据排焰口中心角度调用子程序
。。。
ZZ1002 %子程序走该类型铣切路线
G0 U=-196.135 Z5
G90 G01 Z=-7 F30
G91 G01 X=400 F500
G91 G01 A=1.94 F20
G91 G01 X=-400 F500
G91 G01 A=-1.94 F20
G90 G01 Z=3 F3000
G153 G0 Z0
M17
进行关键技术攻关后,排焰口的自动铣切工艺流程如图7所示,首先进行桁条轴线激光校准,保证桁条装配精度±0.5 mm,再在壁板自动钻铆设备上自动钻孔和铆接,然后进行粗铣排焰口,根据排焰口窗口两侧余量进行角度补偿,补偿后再精铣排焰口,最后进行排焰口的手工统一拆除。

Figure 7. Flow chart of the milling process of the outlet
图7. 排焰口的铣切工艺流程图
4. 手工铣切与自动铣切结果对比
某型号级间段共140个排焰口,将手工铣切与自动铣切进行了对比,结果见表6。
铣切效率:采用手工铣切需4名操作人员用时3天完成(工时为96小时),采用自动铣切需1名操作人员用时2天完成(工时为16小时)。采用自动铣切效率提高5倍。
铣切精度:手工铣切精度±1 mm,自动铣切精度±0.5 mm,优于设计指标要求,且一致性好,杜绝了手工铣切损伤蒙皮的风险。
一次合格率:手工铣切一次合格率95%,自动铣切一次合格率100%,避免工人返修造成的费时费力,进一步提升效率和精度。
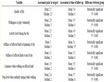
Table 6. Parameters table of burr free hole making process
表6. 无毛刺制孔工艺参数表
由分析得采用自动铣切效率提高5倍、铣切质量一致性好、产品一次铣切合格率高,满足航天产品高质量、高效率、高效益的“三高”发展要求,可推广至所有箭体舱段操作口在部段状态下需铣切的产品。
5. 结束语
本文对运载器排焰口的自动铣切进行了工艺研究,突破了基于线激光校准的桁条高精度定位技术、粗铣留余量–精铣角度补偿法技术和基于程序嵌套的快速编程技术,实现了排焰口的自动铣切,并与手工铣切进行了对比,得到如下结论:
1) 手工铣切需96小时,自动铣切需16小时,自动铣切效率提高5倍。
2) 手工铣切精度±1 mm,自动铣切精度±0.5 mm,自动铣切精度高、质量一致性好。
3) 手工铣切一次合格率95%,自动铣切一次合格率100%,自动铣切合格率高。
本文的自动铣切方法可推广至所有箭体舱段操作口在部段状态下需铣切的产品。
NOTES
*通讯作者。