1. 引言
化合物半导体硅、锗、铁电聚合物、玻璃、陶瓷等是半导体器件制作材料中较为普遍的一种,目前芯片材料中最常用的是半导体硅,由于玻璃的绝缘性和力学性能都很好,并且可以与硅片实现键合,因此键合后的器件具有较小的分布电容和热噪声,如MEMS,光学透镜,传感器制造等。
目前,传统硅–玻璃的粘合多以阳极粘合为主,该技术实施过程中需要施加电场和高温加热,高温高压会引起较大键合残余应力,导致器件结构变化或性能衰减,对半导体器件应用有较大局限性。伴随着采用硅–玻璃异质材料键合器件需求不断增加,结构设计越来越复杂,采用传统的阳极粘合技术已无法满足当前需求。
晶圆低温键合技术克服了传统阳极键合技术的缺陷,该技术又称为氢氧化物催化键合技术,是一种在室温环境下通过在键合界面形成硅酸盐网状结构进行两体键合的可靠的固体胶合方式。与阳极粘合技术相比,这种方法对界面的要求不高,对晶片及器件损伤小、无中介层污染、无需外部电场辅助,键合力更强,抗温度冲击,而键合界面与传统阳极键合一样均匀、透明,可广泛应用于石英、光学玻璃、光学晶体等异质材料两体键合。
20世纪90年代美国斯坦福大学在美国宇航局的资助下,开展了低温键合技术的研究,主要用于满足其重力探针B (GP-B)项目中恶劣的发射和使用条件,研究获得了良好的键合特性 [1] [2] 。自此以后,低温键合技术得到了国外多家研究机构的高度重视,包括德国肖特公司、英国格拉斯哥大学、美国斯坦福大学、NASA、洛克希德马丁公司等研究机构一直对该技术进行研究,并在多个领域得到应用。
在基础科研领域,在引力波测量领域应用低温键合技术悬挂大质量光学元件是目前的研究重点,Virgo和GEO600通过使用低温键合技术,获得了良好的高强度特性和低额外机械损失 [3] [4] ;在航空航天领域,James、Webb空间望远镜(JWST)、激光干涉仪空间天线(LISA)等计划中,其精密光学器件的制造和连接通过利用低温键合技术,键合精确度和抗低温冲击性能得到有效提升 [5] [6] ;在强激光领域,由于低温键合界面的组成与玻璃本体接近,能够有效降低同光路径上的热聚集,减少光元器件损伤的机率并能抑制多模效应,广泛用于制造光学腔和输出镜 [7] 。此外,低温键合技术还在混合波导基底、大型轻质光学元器件、薄型可变形反射镜等领域得到广泛应用 [8] [9] [10] 。
2. 硅–玻璃低温键合原理
硅–玻璃低温键合原理如图1所示。首先,采用O2等离子体轰击SiO2表面,以此激活介质表面的Si-O键,使其具有亲水性。其次,采用去离子水清洗介质表面,处于亚稳态的Si-O键很容易与H2O结合形成OH-悬挂键,以此在介质表面形成一层水分子膜。接着将两枚完成表面激活处理的硅片相互正面对准,并将硅片表面接近到亚毫米级的距离,先后从硅片中心到边缘进行介质表面键合,以此排出空气,获得理想的键合效果。由于SiO2介质表面存在OH-悬挂键,氢键的范德华力会使两枚硅片的介质表面相互粘合在一起,获得一定强度的临时键合。最后,采用一定退火温度处理两小时,将键合面的OH-键还原成水分子,形成键合力更强的Si-O-Si键合面,并排出水气,实现范德华力到共价键的转化,从而大大增加了硅片间的键合强度。

Figure 1. Principle for fusion bonding of silicon-glass
图1. 硅–玻璃低温键合原理
3. 工艺设计与实施细节
本文对硅–玻璃低温键合工艺进行设计,并对关键工序的工艺参数进行了分析和试验。
硅–玻璃低温键合工艺具体实施步骤如图2所示。
3.1. 异质材料来料分析
直接键合要求晶圆表面具有高度的平坦度、平行度和光滑度,同时也必须保证表面干净,没有颗粒、有机物及金属污染,否则将会影响键合界面的结构及电学性能。
因此,玻璃晶圆材料选择可提供各种厚度和光滑度较高的硼硅酸盐玻璃,总厚度偏差小于1.5 um,粗糙度小于0.5 nm,弯曲度小于30 um。硅晶圆材料选择可提供各种厚度和难以置信的光滑度的硅晶圆,总厚度偏差小于1.5 um,粗糙度小于0.5 nm。
3.2. 异质材料表面镀膜
键合的原理是键合设备先对晶圆进行等离子体活化,等离子体处理后的晶圆经过去离子水清洗使得活化的Si-O键与H2O结合形成OH-悬挂键 [11] 。二氧化硅薄膜稳定性好,膜层牢固,可以经过离子水清洗使得活化的Si-O键与H2O结合形成OH-悬挂键,没有沉积薄膜,无法形成稳定性好,膜层牢固的键合晶圆。
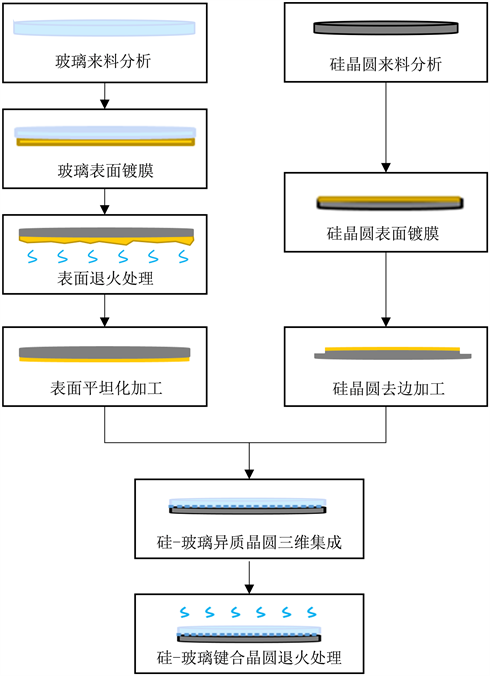
Figure 2. Flow chart of fusion bonding
图2. 低温键合实施步骤
3.3. 退火处理
PECVD制备SiO2膜的反应过程很复杂,是一种无机聚合反应,PECVD的反应原理是利用气体辉光放电,一般在200℃~300℃,生长速率快 [12] ,但是要想得到目标键合力的键合表面,单纯PECVD长出来的薄膜还不够致密,相对较疏松,通过退火处理可以获得更加致密的SiO2膜。
3.4. 化学机械研磨平台化处理
晶圆SiO2膜沉积后还需要进行晶圆化学机械研磨后续工艺,化学机械研磨工艺中的关键在于对SiO2均匀度的控制 [13] ,通过研磨液种类,转速,压力,研磨液流量等工艺优化,研磨到预期SiO2厚度,均匀度控制在3%以下。
3.5. 硅晶圆去边处理
去边工艺的目的是防止硅片减薄时边缘由于减薄力的作用发生崩边和边缘裂片,来降低边缘缺陷,并且有助于键合气泡的排出,去边工艺效果如图3所示。可以看出,如果去边不好,在去边处的边界会有不同程度的凹坑出现,如图3(b)所示,这样会直接导致后续工艺过程中硅片边缘出现键合气泡等缺陷,键合力不够等不良效果。
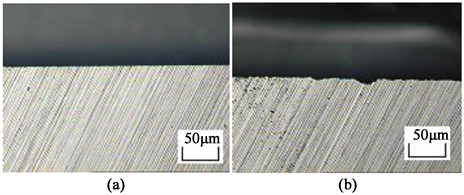
Figure 3. Process effect after trimming
图3. 去边后工艺效果
3.6. 异质晶圆键合三维集成
由于玻璃的翘曲度高于硅晶圆,要求采用不同位置进行低温形成临时键合,玻璃的膨胀系数也高于SiO2,要求先在较低温度下完成临时键合,然后在较高温度时通过退火工艺实现玻璃永久键合。
玻璃–硅片键合工艺完成后,需要在不破坏硅片的前提下对玻璃–硅片的键合界面处进行缺陷检测,利用超声波扫描显微镜可检验界面处是否有气泡、硅片边缘处是否有灰边等。如图4所示,如果两片硅片表面没有紧密的结合,在界面处就会有大的气泡出现,如图4(a)所示,这些气泡会在后续的工艺过程中破裂,从而可能会导致后面的机台受到污染,如此的键合硅片是无法进行后续工艺的。
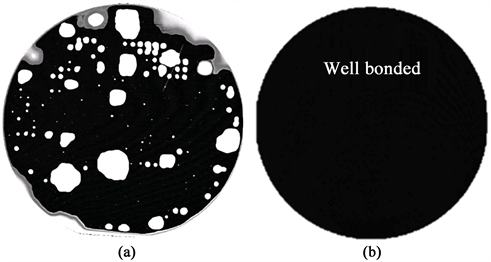
Figure 4. Diagram of surface quality of silicon wafer after bonding
图4. 硅片键合后硅片表面质量示意图
3.7. 键合晶圆退火处理
键合过程结束后对复合晶圆在200℃~400℃进行退火处理,将晶圆间的氢键连接转化为共价键连接,进一步增大键合强度 [14] 。
对于经过等离子体腔预处理的键合晶圆及未进行等离子体激活的晶圆分别进行退火后的键合力测试,结果表明400℃加热条件下3小时,经过活化处理的晶圆在退火1小时后即可表现出大于2 J/m2的键合强度,而未经等离子体处理的晶圆退火3小时后键合强度仍小于1 J/m2,如图5所示。这一结果表明键合前的等离子体激活是很有必要且不可缺少的。
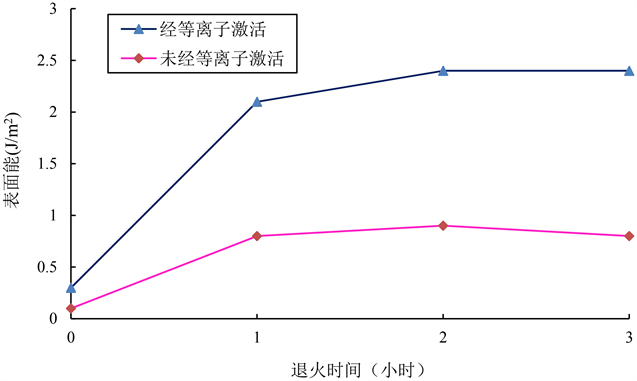
Figure 5. Bond force test curve of 12’ bonding wafer with (without) plasma treatment
图5. 有(无)等离子体处理的12寸键合晶圆键合力测试曲线
4. 实施效果
表征晶圆键合的主要参数有键合力及键合缺陷比例 [15] ,采用国家智能传感器创新中心的键合力测试推裂仪设备CT103,通过取晶圆90度/180度/270度三个位置,分别用刀片插入5 mm的深度,通过裂纹法测试键合力公式计算不同位置的键合力,然后取平均值即可得到该片晶圆的键合强度。
对上述工艺方法加工出的玻璃–硅异质晶圆,实验通过选取6对键合材料键合力进行测试,测试结果如表1和表2所示:
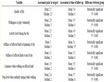
Table 1. Measurement results of wafer bonding force
表1. 玻璃–硅异质晶圆材料晶圆键合力测量结果
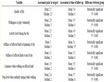
Table 2. Measurement results of wafer bonding force of Pair 1
表2. Pair 1 玻璃–硅异质晶圆材料晶圆键合力测试结果
测量结果显示,采用上述工艺方法后,所有键合力平均值2.19 J/m2,大于1.8 J/m2。
采用超声波扫描显微镜,通过选取6对键合材料键合力进行测试,分别测量每对键合晶圆的缺陷区域、最大缺陷、键合良品率,对上述工艺方法加工出的玻璃–硅异质晶圆材料键合空洞缺陷进行测试,测试结果如表3所示:
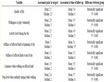
Table 3. Measurement results of wafer bonding hole defects
表3. 玻璃–硅异质晶圆材料晶圆键合空洞缺陷测量结果
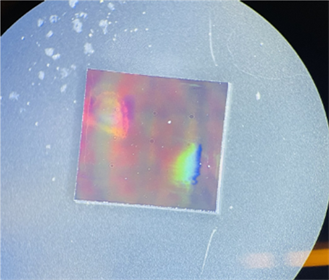
Figure 6. The bond outlived the substrate in the cracking test
图6. 键合后键合界面状态(良好)
测量结果显示,键合空洞缺陷 < 5%。
经过切片结果显示,键合后键合界面状态良好,如图6所示。
5. 结语
本文设计了一种针对硅–玻璃为衬底的异质材料的低温键合工艺,通过在玻璃衬底沉积氧化膜,预键合时界面间形成氢键连接,经过后续退火氢键转化为共价键,实现硅–玻璃衬底间的紧密键合,最终成品键合界面均匀、透明,键合界面空洞缺陷率小于5%,键合力大于1.8 J/m2,实现硅–玻璃晶圆的永久键合,大大增加了硅–玻璃键合工艺的应用范围。