1. 引言
S136D模具钢由于其优异的耐磨性、耐腐蚀性、机械加工性以及能获得高光滑表面等特性,广泛应用于生物医药、航空航天零部件制造中。随着航空航天技术的不断发展,作为航天器核心的航空发电机,其制造材料已由全金属结构发展为以复合材料为主。航空发动机主机和短舱在一些高性能、低重量要求的非主承力构件上,已使用新型纤维增强树脂基等复合材料。S136D模具钢是新型复合材料部件成型制造的关键模具材料,因此,其表面质量和机械性能对航空航天产品的性能及其使用寿命具有至关重要的作用 [1] [2] 。
抛光是工件在加工过程中获得更光滑表面形貌的工序,主要是通过机械作用使工件表面产生塑性变形,同时还结合化学及电化学作用使工件表面更光滑 [3] [4] [5] ,抛光是模具制造行业的重要加工工序 [3] [6] ,能明显提高模具钢表面的质量和精度。而现阶段模具制造领域,制造所需时间的一大部分消耗在终抛光工序,总体占据制造时间的20%以上 [6] [7] ,且目前该过程大多数是采用人工进行,导致不仅抛光精度差、生产成本高、交货时间长 [8] ,而且该过程需要经验熟练的工人去完成,工人技术要求高。传统的抛光局限于材料损失、成本高、抛光率低以及废物处理等问题。近年来已有研究表明,与传统抛光方法存在的诸多局限性相比,激光抛光作为一种新型的抛光技术具有无污染、无接触、自动化高效率以及加工范围广等优势 [9] [10] [11] [12] ,且加工时不仅没有任何材料损失,还可实现自由曲面抛光 [5] 。其次,激光抛光技术不只局限于抛光金属材料,如:不锈钢、工具钢、模具钢、钛合金、铝合金以及镍合金等其他金属材料,还能应用于氧化铝陶瓷、碳化硅陶瓷、氧化锆陶瓷、石英玻璃等非金属材料的抛光 [3] [4] [13] 。
针对金属材料的激光抛光,Souza等人 [14] 采用固体激光器抛光316 L不锈钢来研究激光抛光对316 L不锈钢的表面粗糙度和湿润性的影响。研究结果表明:经过激光抛光后,样品表面平均表面粗糙度降低了86%。并且由于表面质量的提高也会影响样品表面的湿润性,接触角的数值显示激光抛光后的重熔表面呈现出各向异性的湿润性。Chen等人 [15] 采用波长为1064 nm的皮秒激光器抛光ASP23模具钢来降低样品的表面粗糙度。通过实验发现经过皮秒激光抛光后的样品表面粗糙度降低到了0.163 μm,降低了28.2%,而且在样品的截面明显观察到熔融区、热影响区以及基体材料区。Zhou等人 [16] 利用1070 nm的连续激光器将钛合金样品从初始表面粗糙度7.3 μm降低到0.6 μm。研究结果还表明由于马氏体相的形成使得抛光后样品表面的微观硬度增加了约25%,此外,由于抛光表面晶粒尺寸的增加会使得样品表面的耐腐蚀性能增加。
针对非金属材料的激光抛光,Zhang等人 [17] 采用1064 nm的皮秒激光器来抛光Al3O2陶瓷材料,研究结果表明参数优化后的激光抛光能够将样品的平均表面粗糙度降低至0.32 μm。而且,抛光后样品表面具有致密的细晶结构,孔隙率和力学性能较好,激光抛光后样品的断裂强度提高了25%。Zheng等人 [18] 利用飞秒激光抛光来提高SiC陶瓷的表面质量,研究结果显示激光频率过低或者过高均不利于提高样品表面质量,通过参数优化发现当脉冲激光频率为40 KHz、脉冲能量为40 μJ时,样品表面可以获得无裂纹、凹坑和碎屑的优质表面,并且样品的平均表面粗糙度降低至0.79 μm。
近年来,针对激光抛光研究,主要集中在单束激光抛光,关于双束激光抛光对样品表面质量影响的研究鲜有报道。本文采用连续激光抛光S136D模具钢,研究了不同激光能量密度对S136D模具钢表面截面的微观结构、微观硬度、杨氏模量、表面物相、残余应力以及表面耐腐蚀性的作用效果。此外,结合连续激光和脉冲激光研究了双束激光对样品表面物相、残余应力以及耐磨性的影响。
2. 实验材料与方法
2.1. 实验材料
本次实验所使用的是尺寸为120 × 115 × 5 mm3的模具钢,每个样品的激光抛光范围为9 × 9 mm2。这些样品在进行激光抛光之前经过退火热处理。为了降低样品环境对实验结果的影响,在进行抛光实验之前,对样品表面进行超声波清洗30 min,然后吹干。
2.2. 实验装置和检测设备
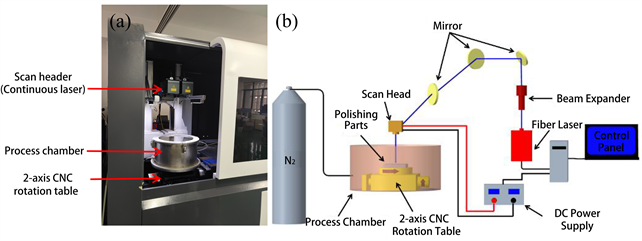
Figure 1. (a) Principle of experiment device; (b) Experiment device
图1. (a) 实验装置原理;(b) 实验装置
实验装置及原理如图1所示,双激光抛光系统主要包括连续波激光器和脉冲激光器。连续激光器的波长为1064 nm,最大的激光功率为1000 W,聚焦后的光斑直径为0.3 mm。脉冲激光器的波长为1064 nm,最大的激光功率为50 W,最大的激光频率为100 KHz,聚焦后的光斑直径为0.2 mm。整个抛光过程在充满氩气的环境下进行,防止模具钢在抛光过程中被氧化。
采用线切割将样品制备成9 × 9 mm2的小金属块,然后利用砂纸和磨抛机打磨样品截面,最后用配比为硝酸:盐酸:水 = 3:1:4的王水稀释液腐蚀样品截面30 s,然后采用型号为Tescan Mira 3 XH的扫描电镜观测抛光后样品截面的微观组织结构。采用型号为ContourGT的纳米压痕仪来测量抛光样品截面的微观硬度以及杨氏模量,压入载荷是10 mN,保载时间是2 s。采用型号为advance d8的X射线衍射仪来对抛光样品表面进行物相分析。采用型号为LXRD的高速残余应力测试仪来测量抛光后样品表面残余应力。最后采用型号为PARSTAT MC的电化学工作站来测量激光抛光前后样品表面的耐腐蚀性能,测量期间电解液选择溶液浓度为3.5%的NaCl溶液,参比电极选择饱和甘汞电极,辅助电极选择铂片。
3. 结果及分析
3.1. 不同能量密度下的微观组织结构及微观硬度
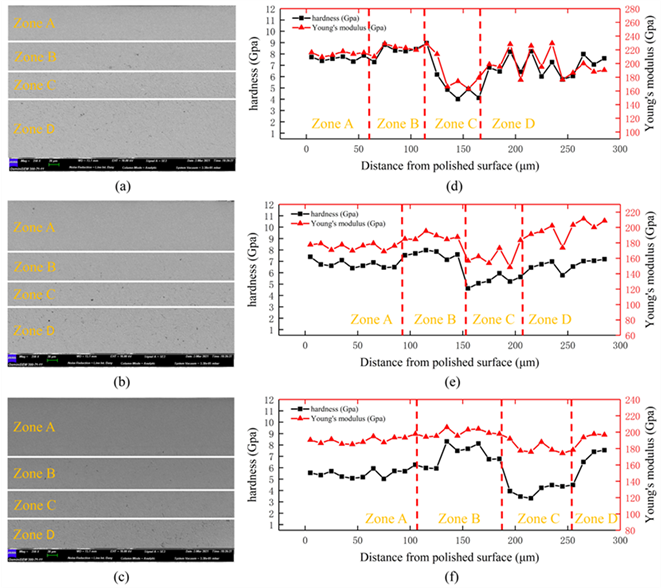
Figure 2. (a), (b), (c) The microstructure in polished sample cross section with different energy densities; (d), (e), (f) The hardness and Young’s modulus of each region in the polished sample cross section
图2. (a)、(b)、(c) 不同能量密度下样品截面的微观结构,(d)、(e)、(f) 抛光样品截面各区域的硬度和杨氏模量
图2揭示了不同能量密度下,抛光样品亚表层的微观组织结构、微观硬度以及杨氏模量。图2(a)、(b)、(c)分别是能量密度为1500 J/cm2、3000 J/cm2、4500 J/cm2抛光区域显微组织结构。从图3中可以发现,经过激光抛光后,样品抛光截面主要包括4个区域,其中区域A是熔融区、区域B和C是热影响区、区域D是基体材料。Marimuthu等人 [19] 也观察到了相同的结果。由于温度不同会导致显微组织结构发生变化,发现区域A的显微组织结构非常致密,而且该区域的孔隙和裂纹也较少。随着熔池深度的增加,截面显微组织区域的孔隙和裂纹逐渐增多,显微组织结构逐渐变得粗疏。表1是不同能量密度的截面区域A、区域B和区域C的尺寸。随着能量密度的增加,可以发现截面熔融区和热影响区的尺寸不断增加,尤其是熔融区A的尺寸从63.5 μm增加到112.5 μm,增加了77.2%。由于随着能量密度的增加,样品表面聚焦的能量增多,导致熔融区深度明显增加,同时更多热量传导到热影响区,使得热影响区的深度也随之增加。
图2(d)、(e)、(f)是不同能量密度下,抛光样品截面各区域的硬度和杨氏模量的变化图。结合三个折线图中杨氏模量与微观硬度与杨氏模量的变化趋势,可发现二者具有相同的变化趋势,且杨氏模量与微观硬度成正比。表2为不同能量密度下工件加工表面亚表层的各区域平均杨氏模量及平均硬度。从中可发现在能量密度为1500 J/cm2的条件下,由区域A到区域B样品截面的平均杨氏模量以及平均微观硬度有轻微的增加,其中区域A的平均杨氏模量和平均微观硬度为213.51 Gpa和7.56 Gpa,区域B的平均杨氏模量和平均微观硬度为224.82 Gpa和8.55 Gpa,产生这种变化是由于激光抛光能量密度低,工件表面冷却速度快,过冷度大,导致重熔区的柱状晶细小,因此硬度较高。但是从区域B到区域C,样品截面的平均微观硬度以及平均杨氏模量有明显的降低,而且该区域的平均微观硬度以及平均杨氏模量均低于初始样品。主要是由于在激光能量会对样品表面进行二次加工,而由于抛光层不同区域的温度不同,形成的微观组织不同,导致微观硬度以及杨氏模量发生变化。由于区域A和区域B的温度高,导致在抛光层一部分残余奥氏体会转变为马氏体,使得其的微观硬度要高于区域C的微观硬度。而区域C的硬度和杨氏模量要低于初始样品,主要是由于区域C温度低,产生退火,使得该区域的硬度杨氏模量降低。能量密度为3000 J/cm2的样品和1500 J/cm2的样品抛光层具有相似的平均微观硬度和平均杨氏模量变化趋势。但是相比于前两种能量密度,在能量密度为4500 J/cm2的条件下,样品截面区域A的平均微观硬度以及平均杨氏模量明显降低。
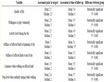
Table 1. Sizes of each zone under different energy densities
表1. 不同能量密度下的各区域尺寸
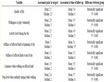
Table 2. Average hardness and Young’ s modulus of polishing subsurface at different energy densities
表2. 不同能量密度下加工表面亚表层的各区域平均硬度和平均杨氏模量
3.2. XRD和残余应力分析
图3是五种样品表面的XRD图,从上到下依次为初始样品表面、1500 J/cm2、3000 J/cm2、4500 J/cm2的能量密度以及双激光抛光作用下的样品表面。双激光中连续激光能量密度为3000 J/cm2,脉冲宽度为200 ns,激光频率为100 KHz,脉冲激光功率为30 W,扫描速度为20 mm/s。从图中可以看出,初始样品主要是由体心立方晶格的α-Fe和面心立方晶格γ-Fe组成。此外,当扫描角度2θ为35˚时,在初始样品表面发现了Fe2O3,主要是初始样品表面部分被氧化产生了Fe2O3,经过激光抛光后,氧化层被去除。而且,由于材料熔化后快速冷却导致部分α-Fe转变为γ-Fe,从而使得α-Fe的峰值有所降低而γ-Fe的峰值有所提升。
由于S136D模具钢的晶粒尺寸远大于100 nm,在XRD测量中,晶粒的变化直接反映在衍射峰的峰宽上,当测量尺寸大于100 nm,峰宽对于晶粒变化的敏感度下降,因此XRD只局限于测量尺寸在100 nm以内的晶粒,但可以通过衍射峰半峰宽去对比抛光前后晶粒的粗细。从图3中可以看出,不同能量密度抛光后的三个样品的半峰宽均要小于初始样品,所以抛光前的晶粒尺寸要小于抛光后的晶粒尺寸。
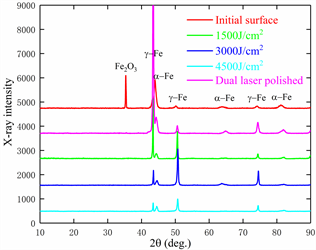
Figure 3. XRD patterns of different samples
图3. 不同样品的XRD图
图4显示了不同能量密度下以及双激光作用下各样品的残余应力。图4纵坐标中的负号代表残余应力的类型为残余压应力。由图4可知,增加激光抛光的能量密度,会增加样品内的残余压应力。主要原因是不均匀的温度场导致工件表面产生局部热效应,使得熔池冷却后产生了残余应力。而激光能量密度越大,加工过程中温度梯度越大,导致抛光后产生的残余应力越大。
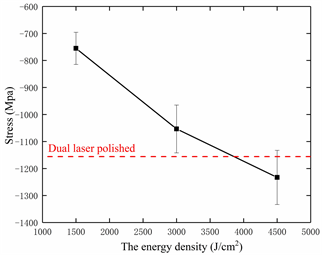
Figure 4. Residual stress of different samples
图4. 不同样品的残余应力
3.3. 耐腐蚀性能分析
图5显示了所有样品的极化曲线,材料的腐蚀与自腐蚀电位成正比,与自腐蚀电流密度以及腐蚀速率成反比。而激光抛光后的样品表现出了更低的自腐蚀电位、自腐蚀电流密度以及腐蚀率,这说明了激光抛光能够提高样品表面耐腐蚀性。而且通过对比自腐蚀电位以及自腐蚀电流密度可以发现,双激光抛光样品具有最低的自腐蚀电位和电流密度,说明双激光抛光样品具有最好的耐腐蚀性能。
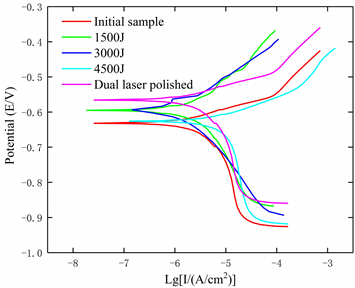
Figure 5. Tafel curves with different samples
图5. 不同样品下的塔菲尔曲线
4. 结论
(1) 经过激光抛光后,样品亚表面会形成三个主要的区域分别是:重熔区、热影响区以及基体材料。经过激光抛光后,重熔区和热影响区具有更加致密的微观结构,具有更高的微观硬度以及杨氏模量。然而,随着激光能量密度的增加,样品亚表面的微观硬度以及杨氏模量有所降低。
(2) 初始样品表面主要由α-Fe和γ-Fe组成。在经过激光能量的作用后,由于温度梯度的影响使得样品表面的一部分α-Fe转变为γ-Fe。同时,由于高的冷却速率,导致样品表面过冷度大,从而产生残余压应力,并且随着激光能量密度的增加,样品表面的残余应力逐渐增大。
(3) 采用激光抛光可以提高模具钢表面的耐腐蚀性。与能量密度4500 J/cm2相比,能量密度1500 J/cm2和3000 J/cm2时的抛光样品耐腐蚀性能更优。通过对比腐蚀电位、腐蚀电流以及腐蚀速率,双激光抛光后的样品表面具有最佳的耐腐蚀性能。