1. 引言
我国煤矸石累计堆存已超过70亿t,占地面积约70 km2,并以每年3.0~3.5亿t的速度增长,占工业废弃物总量的40%以上 [1] 。随着矸石排放量逐年递增,大量堆积造成对土地资源的破坏与占用,矸石山中的细小浆料颗粒会随风形成沙尘,污染环境 [2] 。煤炭开采中对生态、地表造成严重破坏,采空区地面沉陷严重,地面建筑物受损,这些问题严重制约煤炭资源高效开采与生态环境保护可持续发展 [3] 。矸石充填开采技术是一种环境友好型绿色开采技术,既能够解决地面煤矸石、粉煤灰等大量堆积、污染环境问题,还能够减少上覆岩层的移动、有效控制地表沉陷,为煤矿企业从煤矿开采中带来经济效益和环境效益,在“三下”压煤开采中得到广泛推广,具有良好的应用前景 [4] [5] 。近几年来,山东科技大学的宋振骐院士 [6] 对无煤柱开采进行了深入的研究。采用煤矸石充填采空区的技术,既能降低煤矸石的排放量又能达到决绝因采空带来地表下沉量的问题。胶凝材料选取、充填材料配比参数优化对采空区充填力学性能稳定性有很大影响,对有效控制地表沉陷至关重要。粉煤灰是燃煤火力发电过程中产生的浆料废渣,含有大量活性物质,广泛应用于建材、混凝土、水泥、农业、采空区充填等方面 [7] 。
2. 试验材料选取
试验所用煤矸石、矿井水均来自淮南某煤矿,煤矸石产生于为采煤掘进过程中,呈灰色,由于煤研石粒度直接影响到充填体质量,因此,煤研石必须破碎至合适的粒度。粉煤灰为矿区火电厂的工业废料,水泥为市售普通硅酸盐水泥。用XRF能谱分析煤矸石、粉煤灰化学成分和含量,结果列于表1、表2中,根据XRF分析可知,该煤矸石中主要化学成分为SiO2、Al2O3,化学性质稳定,有利于用作充填材料。用筛分法对煤矸石破碎前、后进行颗粒分级,煤矸石破碎前、后的粒度分析,结果列于表3中。
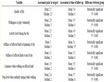
Table 1. Chemical composition of gangue/Wt%
表1. 煤矸石化学组成/Wt%
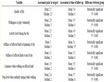
Table 2. Fly ash chemical composition/Wt%
表2. 粉煤灰化学组成/Wt%
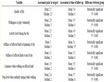
Table 3. Gangue particle size distribution
表3. 煤矸石粒径分布
3. 试验方案
为研究不同固体质量浓度、煤矸石含量、粉煤灰含量对矸石充填体物理性质的影响,设计了九组矸石充填体试样按照一定的配比将材料混合均匀后(浆料配比如表3所示),分出一部分料浆进行流动性、沁水率测试(测试结果如表4所示),剩余的料浆装入正方体模具中,制备成长 × 宽 × 高为70.7 mm × 70.7 mm × 70.7 mm的标准正方体试块,用于进行单轴抗压强度测试。料浆被装入模具后,将开口磨具放置于干燥室内条件下进行养护,24 h后,试块实现初凝,将试块脱模后继续放置于干燥室内条件下养护,试验方案设计的养护龄期分别为:16 h,4 d,27 d。
分别针对试验方案中不同配比、不同养护龄期的矸石充填体试块进行单轴抗压强度测试,测试方法依照中国国家标准GB/T 23561进行。采用YAW-50微机控制电液伺服岩石直剪仪进行单轴压缩变形试验,按照力值控制加载,加载速度为0.2 KN/S。每组测试重复3次,取其平均值作为测试结果。
4. 试验结果与分析
通过上述试验获得9组煤矸石充填体流动性、强度、沁水率如表4所示:
4.1. 固体质量浓度的影响
固体质量浓度较低时,充填体强度随固体质量浓度增大逐渐增大,基体黏度增大,粗骨料矸石的沉降率降低,后期强度增加,但是当浓度超过80%时基体游离水的减少会抑制水化反应的进行,强度降低 [8] 。所以选取76、78、80三种浓度进行试验。当浆料成分一定时,料浆质量浓度是影响浆体输送性能以及后期充填体强度增长的主要因素 [9] 。
试验证明当矸石比例不变,水泥粉、煤灰比例基本不变时,固体质量浓度和试块单轴抗压强度成正相关。例如试块6、8、9,矸石的质量比为90%,水泥粉煤灰质量比波动在1%以内,如图1,试块6比试块9在4 d和27 d的抗压强度分别提高了313%、57.3%,试块8比试块9在4 d和27 d的抗压强度提高了129%、71%。试验结果显示,当矸石含量不变、胶结料结构基本不变时,提高固体质量浓度可以在很大程度上提高煤矸石充填体的抗压强度。
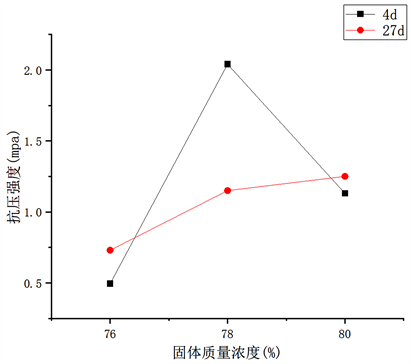
Figure 1. Comparison of the strength of test blocks 8, 6 and 9
图1. 试块8、6、9强度对比
其原因大致包括两个方面:一方面固体质量浓度大时,试块内部有更大的粘度,可以在很大程度上防止粗大颗粒的沉降。同时由于砂浆中水量减少,而使沉降速度降低,缩短了大小颗粒沉降的差距,提高颗粒分布均匀度,确保了试块的强度。另一方面:质量浓度越高的试块沁水率越低,试块8对比试块6、9在沁水率有极大的降低,由于沁水率低,试块可以在同样的时间内快速硬化,提高试块的密实性从而提升试块强度。
4.2. 煤矸石水泥比例的影响
试验结果表示,当固体质量浓度不变、粉煤灰占比基本不变时,提高试块的水泥占比能很大程度上提高煤矸石充填体的流动性指标抗压强度。例如试块4和7;2和6;3和9,试块7、2、3在27 d时强度相比试块4、6、9提高了82.5%、236%、262%。这是因为水泥的作用主要是四点:
1) 包裹骨料,减少骨料颗粒之间的摩擦阻力,增加拌合物的流动性。
2) 水泥浆还能减小充填骨料间的空隙,使试块密实,耐久性好。
3) 保证硬化后试块的强度。
4) 作为胶凝材料主要起到胶结作用,在凝结硬化过程中,将骨料胶结成具有一定形状的整体。
根据图2,当矸石水泥比为80:14时(试块7),27 d单轴抗压强度最大,为4.6 MPA,该试块流动性指标、沁水率同样达到最佳,当矸石水泥比例为85:10.5时(试块2),4 d单轴抗压强度最大,为2.08。由于试块6相比试块2掺入更多水泥,试块6在流动性、沁水率指标表现更好,同时由于水泥掺量高,在更长的养护临期中,试块6的内部流动性更强、空隙更小、试块密实度更好。
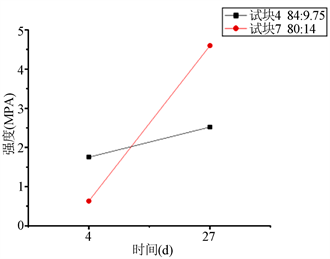
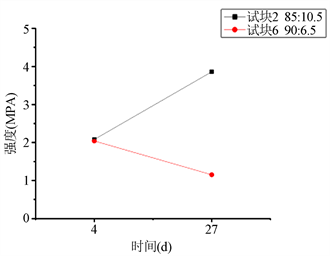

Figure 2. Comparison of test block strength
图2. 试块强度对比
4.3. 胶结料成分影响
试验结果表示,当固体质量浓度基本不变,煤矸石占比不变时提高胶结料中粉煤灰比例可以提高煤矸石充填体流动性、沁水率指标,但会影响单轴抗压强度。由于当煤矸石骨料占比为90时,充填体各项性能都会受到严重影响,故分析胶结料成分时,只分析煤矸石占比为80和85的试块。
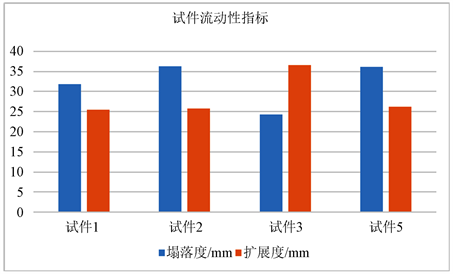
Figure 3. Test block fluidity comparison
图3. 试块流动性对比
图3表明试块2相比试块1,试块5相比试块3都有着更好的流动性,试块2、5胶结料的粉煤灰比例都达到了25%以上,试块1、3粉煤灰比例低于24%。煤灰对胶结充填体的影响有利有弊,适量的粉煤灰可以使流动性和减少泌水率达到最佳效果,粉煤灰过多则容易导致强度下降,如图4在提高胶结料粉煤灰占比后,试块2在4 d、27 d的单轴抗压强度比试块1降低0.724、0.52 MPA,试块5在4 d的单轴抗压强度比试块3降低1.03 MPA。
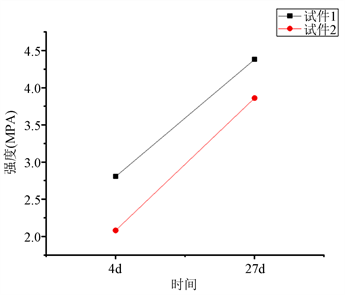
Figure 4. Comparison of test block strength
图4. 试块强度对比
5. 结论
1) 固体质量浓度对于煤矸石充填体抗压强度有非常大的影响,在骨料、胶结料一定的情况下,固体质量浓度越接近80%,充填体强度越高,并且固体质量浓度的提高也可以带来更低的沁水率。
2) 在固体质量浓度一定的情况下,提高煤矸石水泥比例中的水泥占比能很大程度上提高煤矸石充填体的流动性指标、抗压强度,随着养护临期的增加,掺入更多水泥的充填体内部流动性更强、空隙更小、试块密实度更好。
3) 添加粉煤灰可以利用其特性替代部分水泥,改变充填体的粒级组成,但粉煤灰对充填体的影响有利有弊,它可以提高煤矸石充填体流动性、沁水率指标,也会在一定程度上影响充填体的强度。
4) 在试验的9种配比方案中,当固体质量浓度为80,煤矸石水泥粉煤灰比例为80:14:6时,浆料流动性、沁水率指标以及充填体27 d强度达到最佳,对煤矸石充填体在真实工况下的实际应用有一定的参考价值。