1. 引言
管道带压开孔封堵式施工作业是目前管道行业最常采用的维修改造方法 [1] [2] ,在对钢制管道进行开孔作业时会产生铁屑,铁屑会掉落在管道内壁的底部,影响后续的封堵作业严密性,极易造成封堵时管内介质泄漏 [3] ,给管道动火连头工作带来极大的安全隐患。同时,对于一些特殊输送管道,如航油、汽油、柴油等成品油管道,以及制药行业原料输送等净度要求高的管道,更不允许施工作业后的管道内残留有铁屑等杂质。当前,全球管道上每年都有近万个点要进行带压开孔封堵施工作业,随着对开孔后封堵严密性和安全性的深度要求,以及特殊管道对内部清洁度的要求,国内外都开展过管道带压开孔残余铁屑回收装置的开发工作,但普遍仍停留在理论或模型阶段,与实际生产结合的实用性不强,相关的铁屑回收原理方法有软泥粘黏、网布缠黏、磁力吸取和负压抽吸等。我们的研究团队广泛验证国内外相关的技术研究方法,最终借用磁力吸取的原理但结合,通过自主开发试制出了一套实用的铁屑回收装置,保证了管道封堵作业的可靠压密性和安全性,更好的服务于管道业主的维修作业生产需求。
2. 铁屑回收装置的研制
通过国内外钢制管道铁屑回收装置技术调研和技术查新,发现国内外没有实用的带压管道铁屑回收装置 [4] [5] ,几无可借鉴的成功经验,需要自主研发该铁屑回收装置。根据钢质管道铁屑掉落分布模拟实验,筛选磁力吸取式铁屑回收装置的实用方案,进行铁屑回收装置的结构设计和零部件材料的筛选,随后进行组装调试和试验改进,直至最终达到预期铁屑回收效果。
2.1. 管道内铁屑掉落分布情况模拟实验
在设计铁屑回收装置之前,首先进行了大量的钢质管道开孔试验,掌握不同介质、不同压力、不同流速情况下铁屑的分布状况(见图1)。
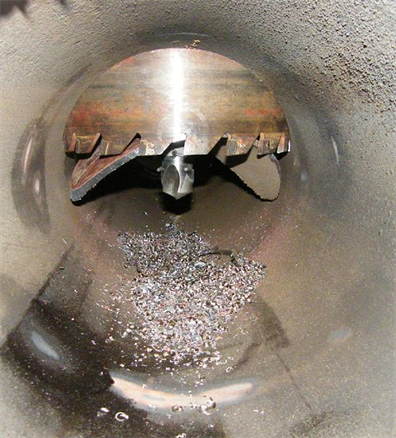
Figure 1. Distribution of iron filings in Hot-tapping test
图1. 开孔试验的铁屑分布情况
经多次试验,掌握不同工况铁屑分布情况:
1) 大量铁屑成碎片状伴有两条带状铁屑(整个鞍形板掉落时形成);
2) 落在开孔圆周垂直管线方向两侧的下方。这两条带状铁屑是铁屑回收的最重要目标;
3) 管线内无介质流动的情况下,开孔时切削产生的铁屑堆积在开孔下方两侧;
4) 如果对管线一端进行气体吹扫(模拟介质流动),开孔时产生的铁屑仍有部分堆积在封堵位置;
5) Φ323.9 mm的管径开孔试验中掉落范围为:沿着管线所开孔的两侧,每一侧范围大约为400 mm,分析得出掉落铁屑范围最大分布于封堵三通的护板长度上。
6) 不同管径管道开孔铁屑分布规律为沿管道轴向分布长度为开孔直径的2倍,即与封堵三通护板长度相同,就可以确保铁屑被取走。
2.2. 确定铁屑回收方案
1) 通过对管道内铁屑堆积情况的具体试验,考虑运营管道内的带压和输送各种介质的情况,经过推扫、夹爪、磁吸等多个方案得比对,最终确定在磁铁吸取方案为最佳方案。
2) 采用强力磁铁作为主要的吸取工具,进行铁屑收集。磁铁具有对铁屑的吸附作用,而且高温高压下不影响磁铁的正常工作,铁屑回收操作方便也更为安全。
3) 最终确定研制一套适用于最大管径φ323.9 mm (任意壁厚均可),工作压力P ≤ 10 Mpa,工作温度T ≤ 80℃,铁屑回收量达到实际开孔铁屑总量的98%的管道开孔铁屑回收装置。
2.3. 铁屑回收器的结构设计和材料筛选
1) 连接装置结构设计
从经济效益、操作性考虑,不再另行设计制作专门的动力操控设备,铁屑回收器和公司现有封堵器相配套,从而降低研究设计加工的成本,提高操作可行性,保证在带压管线上施工作业的安全性,使该装置操作简便,安全。设计专用过渡轴套与封堵器主轴相匹配。
2) 铁屑回收装置材料选取
由于整个铁屑回收装置是采用磁铁吸附的原理 [6] ,所以各部件的材料不能和磁铁吸附粘连,整套装置须承受铁屑回收器的重力和取出的铁屑的重量产生的力,强度需满足铁屑回收器和铁屑重力,故选择不锈钢1Cr18Ni9Ti [7] 。
3) 铁屑回收装置支架结构设计
首先要考虑铁屑回收器可进入管道开孔内部,且进入管道后要覆盖铁屑散落的面积,而且要确保超出管口范围的铁屑取出。因此考虑采用两个折叠式旋转支架结构(见图2),既可以从所开圆孔内深入管道内部,打开覆盖铁屑掉落区域,又可折叠提出管线,满足使用状况的要求。
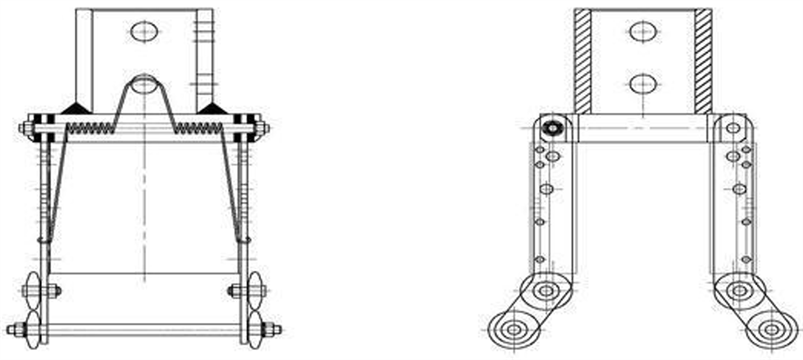
Figure 2. Fold the scaffold rotation structure
图2. 折叠支架旋转结构
折叠旋转支架的折叠过程,只靠重力是不能保证的,考虑到铁屑回收器的总体结构和空间问题,决定采用弹簧来实现(见图3)。弹簧一端固定在铁屑回收器的底座轴套上,一端固定在折叠式旋转支架上,在平时保持铁屑回收器处于一个折叠收拢的状态。当操作铁屑回收器进行铁屑回收时,折叠式旋转支架在进入管道后可以在导向轮的引导下展开,铁屑回收完成后,在专用弹簧的作用力下,两块折叠式旋转支架再次折叠收拢。
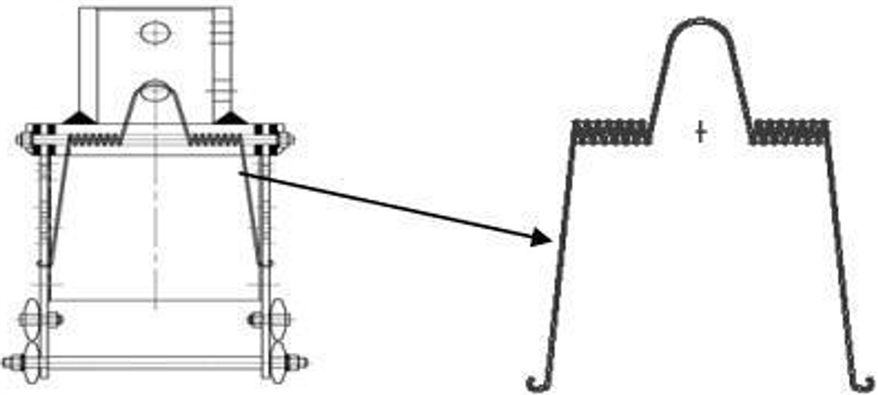
Figure 3. Install a spring on the folding rotating frame
图3. 折叠旋转架上加装弹簧
4) 行走轮设计
折叠式支架打开和折叠的过程只凭借支架和管线的硬性摩擦滑行是无法完成的,需采用滚轮实现。在铁屑回收器的每个折叠式旋转支架上安装两个大小相等形状相同的导向轮,通过反复试验和模拟更换了不同的行走轮直径和轮毂薄厚(见图4),最终解决了下放行走过程中卡堵的问题。
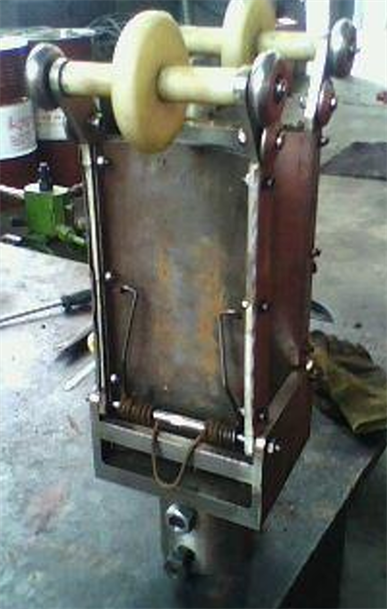
Figure 4. Non-metal and metal combination form of different size wheel
图4. 非金属和金属材质组合的不同尺寸行走轮形式
3. 强力磁铁选取和结构设计
在整个铁屑回收装置中强力磁铁是关键部件,铁屑要通过磁铁吸附上来,来实现铁屑收取,因此磁铁的磁性就是一项重要的性能指标,项目组成员经过调研,咨询相关专家,磁铁磁性强度最终定为3900高斯 [8] 。
为了使磁铁能够最大限度吸附铁屑,磁铁最好是和管线内径接近的圆弧形,所以磁铁就只能是小块磁铁的拼接实现,同时还要依附于板子和底座来实现,称之为铁屑吸附板和磁铁底座,对小块的磁铁进行排布和支撑,铁屑吸附板和磁铁底座与折叠式旋转支架通过螺栓进行机械是的连接,这样就实现了磁铁和折叠式旋转支架的整体装配(见图5)。吸附板两侧材料最初选用的是铁板和不锈钢板,经过多次试验,最后两侧均采用铁板,铁板对于磁性的传导效果比不锈钢板要好 [9] ,自身被磁化后磁力分布较之不锈钢板要更为均匀。
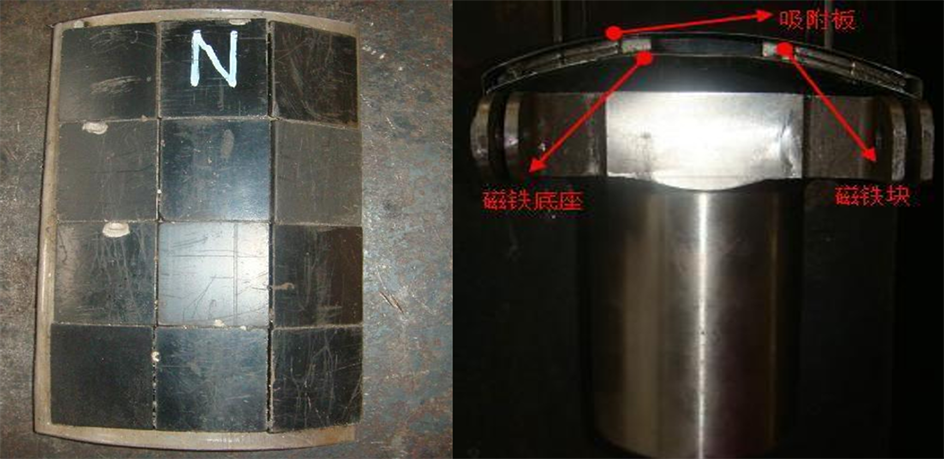
Figure 5. Magnet distribution and the arrangement of the adsorption plate/base
图5. 磁铁分布及与吸附板/底座的布置情况
磁铁过于紧密连接的排布形式,会导致磁铁极性乱,部分磁铁因磁性作用 [10] ,在取铁屑时不能吸附铁屑,通过咨询和反复试验采用间隙型磁铁分布形式,此种方式磁力分布较为均匀,也能更好的使一次铁屑回收量达到验收标准及铁屑回收目的。
经过大量的调研研究试验和改进,最终完成铁屑回收装置的整体外形设计(见图6),由底座轴套、折叠式旋转支架、强力磁铁、铁屑吸附板、磁铁底座等部件组成。铁屑回收器的底座轴套和折叠式旋转支架通过机械式连接,折叠式旋转支架与装有强力磁铁的铁屑吸附板相连,安装在封堵器主轴的前端,操作封堵器来实现铁屑回收器的下行和上升。在封堵器下行过程中带有铁屑吸附板的折叠式旋转支架通过其上的导向轮可以平稳打开,将掉落堆积的铁屑吸取上来。
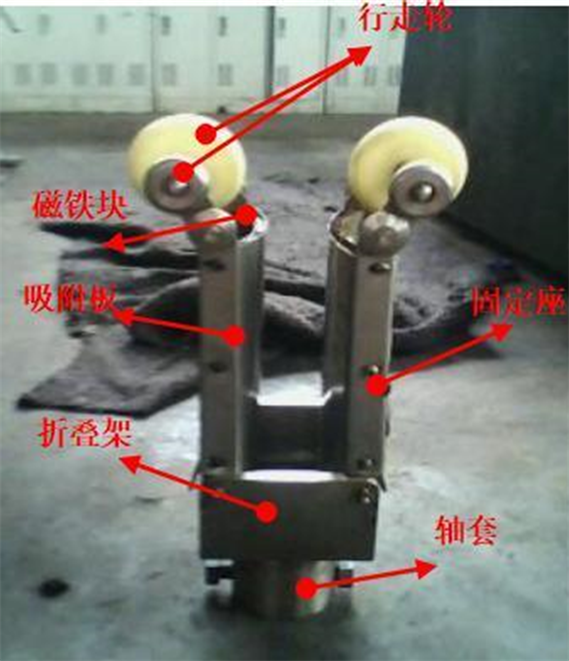
Figure 6. Overall structure of the iron scrap recovery unit
图6. 铁屑回收装置总体结构
4. 铁屑回收装置试验
回收装置研制组装完成后进行了大量的铁屑回收试验(见图7),试验中逐步修改完善磁铁块的布置形式、行走轮的设置和轮毂的大小。在空管铁屑回收和吹扫铁屑回收试验中,开孔铁屑总重的称量和吸取后铁屑重量的称量,验证铁屑回收率达到了98%以上(见图8)。
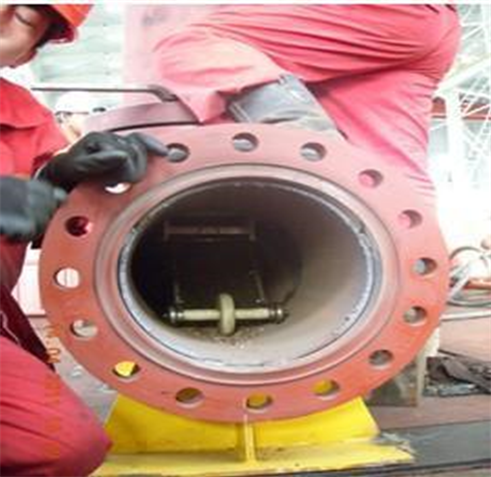
Figure 7. Lower down test of iron scrap recovery device
图7. 铁屑回收装置下放试验
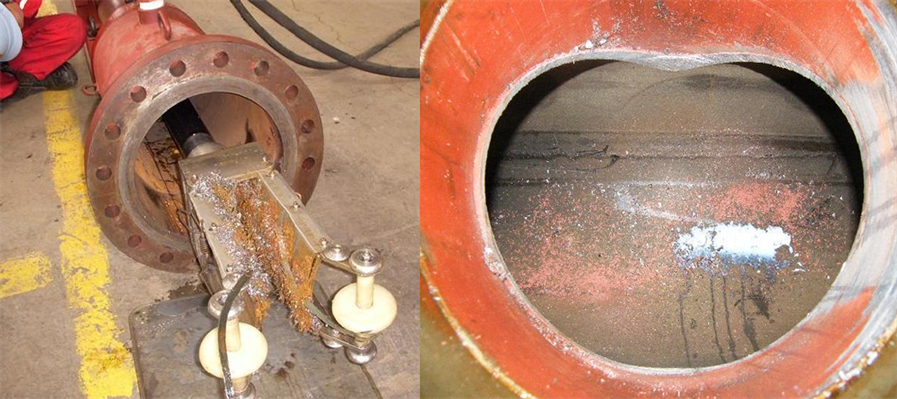
Figure 8. Effect of iron scrap recovery test completed
图8. 铁屑回收试验完成的效果
分析铁屑回收器磁铁对管道的磁化影响并提出消磁措施:在铁屑回收装置运行到位处于正常工作状态下和铁屑回收操作完成撤离铁屑回收装置后,分别利用磁力测试仪器,对铁屑回收器在管道磁化影响区进行磁场定量测试(见图9)。
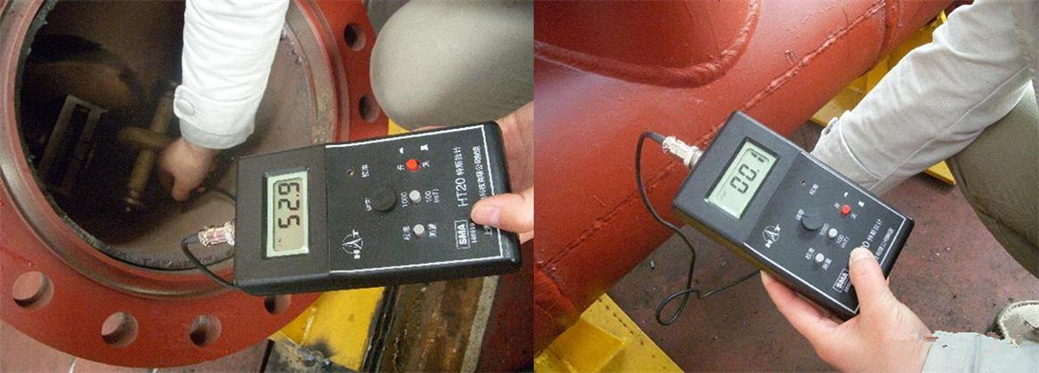
Figure 9. Normal operating condition of the recovery device and residual magnetic measurement after recovery
图9. 回收装置正常工作状态和回收后的剩磁测量
5. 结论
1) 铁屑回收装置研制成功后,进行了大量的铁屑回收试验,铁屑回收率达到了98%以上,尤其是针对两条带状铁屑的回收,无论是在试验中还是在现场应用中都达到了令人满意的效果;
2) 为了提高铁屑的回收率,个别情况下需要反复多次的收放回收装置,在此过程中需避免铁屑掉落至三通管件的卡环等伸缩部位,回收装置与开孔腔径的比例不能过大,要预留足够的通过间隙;
3) 通过试验和实际应用效果可以看到,铁屑回收装置的磁铁对管道的磁化影响较小,铁屑回收后的管道剩磁量不会对后续施工造成影响 [11] ;
总之,铁屑回收装置的成功应用,确实提高了封堵作业的严密性,有效减小了封堵介质的泄漏,降低了安全隐患风险,整体提高了管道封堵作业的安全性和可靠性,值得大力推广应用。