摘要: 飞机液压导管受机体变形、发动机开车以及带应力装配等因素影响,应力状态频繁变化,严重影响到液压系统功能的实现,甚至会给飞机安全带来隐患。针对飞机高压液压导管应力数据难以采集、数据分析方法选择困难及结构优化依据缺乏等问题,开展导管应力分析及结构优化研究。首先,分析飞机高压液压导管应力分析及结构优化全过程,考虑数据采集、数据分析及结构优化不同要素,提出一种基于实测数据的飞机高压液压导管应力分析及结构优化框架模型;然后,在飞机液压导管应力准确测量的基础上,通过数据预处理、数据转换、特征识别等数据分析方法判定应力超限导管,进而实现导管结构优化;最后,以一种飞机的高压液压系统为例,验证了所提方法的可行性和有效性。
Abstract:
The stress state of aircraft hydraulic pipe changes frequently due to the body deformation, engine driving and stress assembly, which seriously affects the function realization of the hydraulic system and even brings hidden dangers to the aircraft. In view of the difficulty in stress data acquisition, data analysis and structure optimization, the research of stress analysis and the structural optimization for hydraulic pipe is carried out. Firstly, the whole process of stress analysis and structural optimization for high-pressure hydraulic pipe is analyzed, and a frame model based on real data is proposed considering different elements of data acquisition, data analysis and structure optimization. Then, after stress data of aircraft hydraulic pipe is measured accurately and reliably, stress overlimit pipes are determined through data preprocessing, data conversion, feature recognition and other analysis method, so as to optimize the pipe structure. Finally, taking an aircraft high-pressure hydraulic system for example, the feasibility and effectiveness of the proposed approach are verified.
1. 引言
近年来,高压液压能源系统凭借其高效优势促进了飞机的轻量化,逐渐成为飞机液压系统的主流趋势。然而,由于液压导管工作环境恶劣,内外压差大,工作环境温度高,且受机体变形、飞机加速度、发动机开车引起的结构振动以及带应力装配等因素影响,致使应力频繁变化,不同应力状态可能会使导管发生变形、疲劳破裂,严重影响液压系统功能的实现,甚至给飞机带来安全隐患。因此,导管应力分析及结构优化对高压液压能源系统的正常工作乃至飞机的安全至关重要。
不少学者通过理论分析方法对导管应力展开了诸多研究。刘娟等在构建大型客机高压导管模型的基础上,通过理论计算管路应力与位移变形,借助分析补偿方法及位置对导管应力性能的影响完成了管系结构的优化 [1] 。权凌霄等通过理论计算、仿真与实验三种方法对机体形变与压力冲击两种载荷耦合作用下的一段飞机回油导管应力进行对比分析,指出仿真比理论计算方法准确性更高 [2] 。赵伟志等针对民用飞机提出了一种液压导管强度分析方法,可以指导导管设计优化 [3] 。
利用仿真分析方法对导管应力的研究也取得颇为丰富的成果。施红等在对导管载荷、约束等详细分析的基础上,提出了一种基于有限元的管道应力分析、补偿与核验方法,为飞机空气管理系统的设计优化提供了参考 [4] 。沈祥等运用Patran 2010对民用飞机高压管路建立有限元模型,计算其载荷和应力结果,总结了高压导管力学性能设计的一般规律及设计方法 [5] 。周艳丽等针对飞机导管的不同构型建立有限元分析模型,与试验应力数据对比,验证了该仿真分析方法的有效性 [6] 。
综上,目前国内外对飞机液压导管应力分析及结构优化的研究大多采用理论计算或仿真手段,然而,理论计算方法存在考虑因素不全面,选取安全系数容易造成冗余或不足等问题;仿真分析方法具有建模难度大、参数难以确定等特点;采用上述两种方法构建的模型均存在误差大等不足,而基于实测数据的研究方法几乎处于空白状态,特别是针对高压压力体制的飞机液压能源系统。因此,为实现液压导管应力地正确可靠分析并实现其结构优化,本文提出了一种基于实测数据的飞机高压液压导管应力分析及结构优化方法。
2. 飞机全机高压液压导管应力分析与结构优化框架
基于实测数据的飞机液压导管应力分析及结构优化框架模型主要包括应力数据获取、导管应力分析及导管结构优化三部分内容,即在准确、可靠采集飞机整机液压导管应力数据的基础上,对飞机液压测量数据进行数据分析,进而对飞机液压导管结构进行优化(图1)。
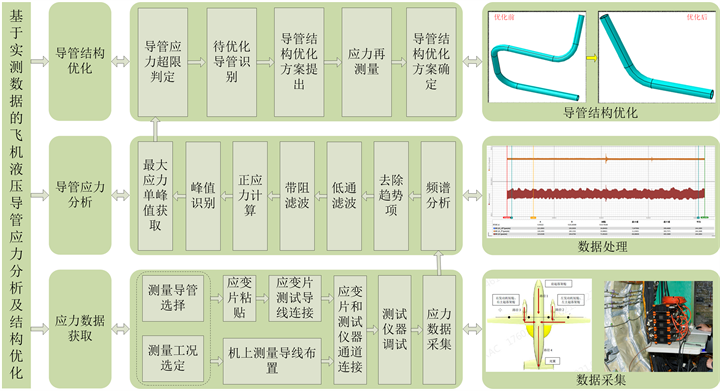
Figure 1. The framework of stress analysis and structural optimization on hydraulic pipe for aircraft based on real data
图1. 基于实测数据的飞机液压导管应力分析及结构优化框架
3. 飞机全机应力数据获取
飞机全机高压液压导管应力的准确测量是分析与优化的前提条件,全机应力测量主要包含应力测量点的选择、测量位置的确定、测量工况的选定、应变计及测量导线的布置等。
(1) 代表性应力测量导管的选择
液压导管贯穿于发动机短舱、机翼、尾翼以及机身等各个区域,不同区域液压导管操纵的对象不同,工作环境差异较大,所受载荷大小及种类也有所不同,选择全机所有导管进行测量是不现实的,因此选择具有代表性的导管进行应力测量是非常关键的。
(2) 测量位置的确定
在飞机液压系统持续工作中,液压导管在不同温度下会承受液压油的压力脉冲、振动及加速度冲击等多种载荷,多种载荷耦合作用下,不同部位的液压导管应力是不同的,因此,选择合理的位置对液压导管应力测量是非常重要的。
(3) 应力测量工况的选定
考虑到液压系统涉及副翼、襟翼、升降舵、方向舵、前轮转弯、起落架收放等系统构件的动作,液压导管应力测量工况的选择需涵盖每个系统构件在各个状态下的动作,主要分为在地面液压源供压和发动机开车时飞机内部液压源供压两种情况。
(4) 应变计的选择和测量导线的布置
为满足飞机开车状态下的测量,应变测量数据采集场地应为机舱内部工作舱,由此,机身内部的应变计连接导线需通过机身内部与测试仪器连接并进行相应的固定,短舱、机翼及尾翼液压导管应变计连接导线可通过相应的口盖孔拉出,再在机体上固定并通过机身应急门进入机身,完成和测试仪器的连接。
4. 飞机高压液压导管应力数据分析模型
液压导管应力测试信号往往是与干扰噪声共存的,除了在测试系统的硬件上增强有用信号,抑制干扰噪声,提高测试信号的信噪比之外,对测试信号进行滤波也是提高信噪比的有效手段。在对采集的液压应力数据处理中,有用的信号频带与干扰噪声的信号频带是有差异的,在保证有用信号不失真的前提下,使用滤波的方法抑制噪声的频率分量而保留有用的信号分量,从而提高应力数据的准确性。
双栅应变计是应力采集的一种有效传感器。鉴于液压导管应力测量需使用0˚和90˚方向的双栅应变计,因此,为获取可以直接使用的导管应力值,在对采集到的液压导管应力数据进行滤波后,需对轴向和周向数据进行转换,转换方法如式(1)和(2)所示。
(1)
(2)
式中:ε测x、ε测y——X向、Y向所测得的初始应变值;ε校x、ε校y——测试仪器X向、Y向零点漂移量;E——导管材料弹性模量,单位MPa;K0——测试系统灵敏系数;K——应变片灵敏系数,取自粘贴应变片的出厂履历。
液压导管应力测量需获取每一个应变测点的最大总应力单峰值,根据公式(3)求得总应力单峰值。
(3)
式中σ𝑥与σ𝑦分别为轴向和周向的最大应力值。
在获取液压导管最大总应力单峰值后,就可以对液压导管超限问题进行判定。液压导管应力超限判定条件为:高压导管应力单峰值大于高压力阈值、低压导管应力单峰值大于低压力阈值的导管。当液压导管的最大应力峰值超过设定阈值,则被认为该导管不满足设计要求。
5. 试验验证
5.1. 应力测量
按照飞机全机应力测量需求,选定飞机中具有代表性的54根导管进行应力测量,位置涵盖了机身、机翼、尾翼、发动机短舱等所有液压操纵系统。
受飞机液压系统工作的环境及工作方式的影响,液压导管的应力值是不断发生变化的,为能抓取到液压系统持续工作中的应力峰值,满足数据分析及优化的需求,本次试验测试采用Dewesoft 640通道动态数据采集系统,采集频率为10 kHz,应力数据采集如图2所示。
液压导管应力测量工况的选择需涵盖不同系统构件在各个状态下的动作,试验项目分为基础安装应变测量、油泵车供压时应力测量、飞机开发状态下应力测量三大项。
为满足液压导管应力测量要求,本次应变计选用0˚和90˚方向的双栅应变计,适用于150℃以内的应力分析,测量导线可耐受温度为250℃,应变计粘贴方式如图3所示。
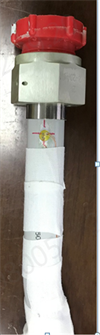
Figure 3. Typical attaching position and drawing of double gate strain gauge on pipe
图3. 双栅应变计在导管上的典型粘贴位置图及粘贴图
5.2. 应力分析
在实际数据处理过程中,首先对原始测试数据进行频谱分析,结合信号来源进行信号与噪音的判别,再根据实际需求选用相应的滤波方式,最终得到有用的信号。
详细地,对所有采集的试验数据进行频域分析后可知负载动作导致的导管振动频率集中在0~500 Hz,结合脉动频率不超过1500 Hz、油液压强致应变属于趋势项,试验数据中干扰噪声为2000 Hz以上频段的电磁干扰和50 Hz工频干扰,因此在有效数据提取时选择2000 Hz低通滤波和49.5 Hz~50.5 Hz带阻滤波,保证尽可能不损害有效信号的完整性。
在对采集的数据进行滤波后,对飞机不同状态下共54根液压导管开展应力计算,寻找高/低压导管应力单峰值大于设计设置的高/低应力阈值导管,发现大多数液压导管应力响应都满足设计要求,只有个别导管在个别工况下出现了应力单峰值(σ总)大于高压力阈值的情况,如表1所示。
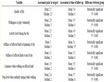
Table 1. Stress over-limit results of pipe
表1. 导管应力超限结果
从液压导管应力超限结果表中可以看出,34号导管在油泵车供压状态起落架收放工况、47号导管在油泵车供压时主起落架收放工况和左发至地面慢车,右发至飞行慢车,升降舵动作工况下应力峰值均超出高压力阈值,存在风险,需对导管结构进行优化。
5.3. 导管结构优化
针对34号导管进行结构优化,设计了两种方案,其导管优化前后的结构如图4所示;对47号导管优化后的结构如图5所示。对优化后的导管分别进行应力测量,其最大应力峰值如表2所示,从表2可以看出34号导管的两个优化方案均满足设计要求,最终选定其中应力较低的方案二作为结构优化结果;47号导管优化后的最大应力峰值也小于高压力阈值。
试验结果不仅说明优化后的飞机液压系统导管结构能够满足设计要求,验证了导管结构优化方案的有效性,更进一步表明了基于实测数据的飞机液压导管应力分析及结构优化方法的可行性。
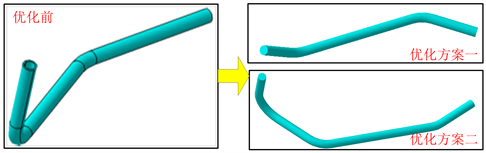
Figure 4. The composition of No. 34 pipe before and after structure optimization
图4. 34号导管优化前后结构对比

Figure 5. The composition of No. 47 pipe before and after structure optimization
图5. 47号导管优化前后结构对比
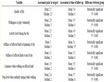
Table 2. The maximum stress peak after structure optimization of No. 34 and 47 pipes
表2. 34和47号导管结构优化后最大应力峰值
6. 结论
飞机液压导管应力分析及结构优化对液压能源系统的正常工作乃至飞机的安全至关重要。本文针对高压力体制的飞机液压能源系统,围绕其导管应力测量及结构优化难题,提出一种基于实测数据的导管应力分析及结构优化方法,试验结果表明,优化后的导管应力均符合设计要求,验证了本文所提方法的可行性和有效性。