1. 引言
航天领域运载器的装配是根据尺寸协调原则,采用装配工具、工装和设备等将各种零件或组件按照设计和技术要求,并按一定的方法和顺序进行组合、连接的过程。以运载器舱段为例,其结构一般为铝合金薄蒙皮、周向按角度分布桁条、大梁,航向分布中间框、端框等组成的半硬壳结构,涉及零部件数量庞大、结构复杂、工序流程长,且由于其对接协调性、互换性要求,装配过程中引入大量工艺装备,使得舱段的装配工艺过程极其复杂 [1] ;为适应航天产品小批量多品种的订单需求,实现快速响应,降低生产成本,提高生产效率,众多的制造企业构建了柔性化混流生产线或柔性制造系统以实现制造资源的快速重组和复用。围绕运载器装配过程,形成了大规模的、极其复杂的制造资源集合。如何发掘单点失效资源,并根据资源的关重程度进行扩能建设,在降低成本的同时又能保证制造系统的鲁棒性和可靠性,是众多航天产品装配企业关注的问题之一。
复杂网络是由大量的节点和节点之间的连接构成的复杂拓扑结构,随着其理论的发展,小世界网络和无标度网络 [2] [3] 相继出现,扩展了解决现实问题复杂性的新途径,并为制造过程复杂性问题探索了新的方向。Hu等通过建立制造复杂性指标,采用熵函数描述装配过程及装配供应链的复杂性 [4] ;孙惠斌等将复杂网络理论引入多工序加工过程中,揭示了多工序加工过程中的工件误差传递机理 [5] ;祁国宁等研究了大规模定制中的零部件关系网络特性 [6] [7] ;从以上文献可知,复杂网络理论在解决复杂系统建模和优化问题上具有天然优势,适用于制造系统复杂性问题的研究与分析。
本文从全局视角出发,将其复杂网络应用到运载器装配过程的制造资源网络建模与分析中,通过建模和分析研究网络的结构和物理特性,为制造资源的重构和再优化及网络可靠性提升提供支持。
2. 制造资源网络的拓扑模型
2.1. 制造资源网络的定义
从装配工艺角度分析,舱段产品在装配过程中体现出工序流转关系,不同工序之间存在串行或者并行的关联特性,随着装配过程的进行形成有向的工序流或网络,如图1。
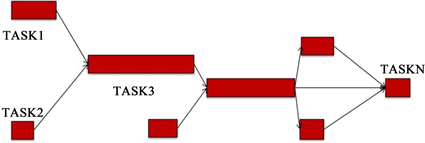
Figure 1. Schematic diagram of assembly process flow
图1. 装配工序流示意
工序流是一种网络,而运载器舱段由于特殊的装配过程和冗长的装配流程,其工序流相比一般的装配件会复杂的多。各级工序内容需要依靠各种制造资源完成,如:某零件制孔需要制造资源包括:钻孔机、钻头、定位卡块,某组件铆接组合需要的制造资源包括:定位螺钉、夹紧钳、压铆机、铆模等;制造资源形成制造工位,众多的制造工位随着任务的迁移串联起来,最终形成以工序流组织的制造资源链条,由于制造资源的重复引用,单向链条充分耦合形成制造资源网络,成形过程如图2。
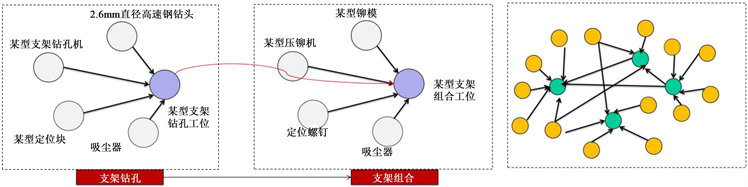
Figure 2. The evolution process of manufacturing resource network
图2. 制造资源网络的演化过程
本文把复杂网络相关理论引入复杂产品装配过程,采用图论的方法建立制造内容的有向图模型,据此对形成的制造资源网络进行特性分析。
现将制造资源网络的拓扑模型定义如下:
(1)
式中
——制造资源节点集,可以是钻头、机加工中心,也可以是制造系统,如某零件加工中心、某组件装配单元、某部段装配系统;
——制造资源网络中的第i节点;
——制造资源网络的边集,其中eij表示vi向vj提供制造资源;
——网络的边权重,表示不同层级制造资源之间关系强度;
——表示vi向vj提供的制造资源总量;M——表示vi向vj提供制造资源次数;
——第r个制造任务执行过程中,vi向vj提供的制造资源量,为制造资源使用时长乘以制造资源提供数量。
邻接矩阵定义如下:
(2)
式中:aij——制造资源i、j之间的有无提供关系;
;N——网络节点的规模。
2.2. 制造资源网络的构建
由制造资源网络的特点可知,基于产品制造工序流的制造资源网络创成方式,是在以制造任务为核心的星型结构基础上进一步分解,将星型结构扩展开来形成的组织架构。首先,对动制造资源节点的基本阶段组织结构进行划分。按制造服务资源节点内容的层级结构,将制造资源分为核心结构、次级结构和三级结构三个阶段。定义如下表1。
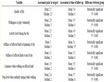
Table 1. Basic elements of manufacturing resource networks
表1. 制造资源网络的基本元素
各围绕某产品BOM制造过程形成的星型网络,通过子网络合并形成制造资源网络。
(3)
式中:k——星型结构的数量。
该合并过程算法可由两个基本步骤完成:
步骤1:将G(1)中的所有节点
逐个加入到网络G中,如果某个节点在多个G(i)中都有出现,仅保留一次。
步骤2:将G(i)中的所有向边
逐个加入到网络G中,如果某条边在多个G(i)中都有出现,仅保留一次。
本部分通过采用3.1节中的决策方法,提取了某航天产品铆接舱段1个重点部件的20个制造资源关系。在此基础上将实际的制造关系抽象成为虚拟网络模型,并分类建立了如表1所示的3种基本的核心结构、次级结构和三级结构关系。通过上文提出的网络组织及创成方法,将4个基本的星型结构网络合并成了一个制造资源网络,如下图3所示。
2.3. 制造资源网络的特性
为分析制造资源网络的拓扑和物理特性,本文定义了如下7种度量指标:
1) 节点度:表示节点vi的局部重要性,记为ki。由入度
和出度
两部分组成。
(4)
式中,
表示节点vi作为任务执行方与其他节点连接的数量;
表示节点作为vi任务需求方与其他节点连接的数量。
2) 鲁棒性:制造资源网络鲁棒性表示该系统抵御风险和抗击破坏的能力,记为RBi。代表SMS节点vi对制造系统稳定性的影响程度,节点vi被移除后的网络效率如下式所示:
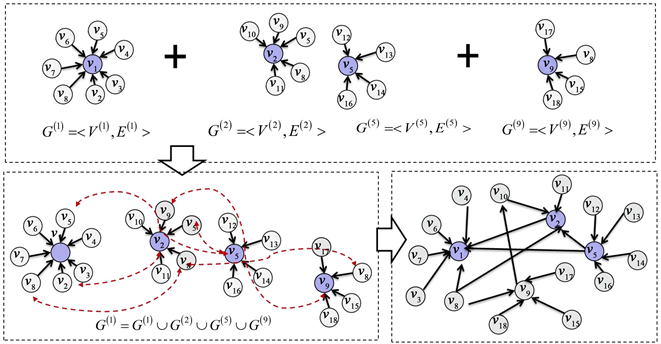
Figure 3. Network organization and creation methods
图3. 网络组织及创成方法
(5)
式中:
——移除制造系统节点vi及其关联边后,节点vm和节点vn之间的最短路径。
3) 负载系数和负载饱和度:制造资源网络中,节点vi的节点制造任务负载系数记为LDi,负载饱和度记为
,表示节点vi向完成邻接节点下达的制造任务的能力。
(6)
式中:
——在第r个制造任务执行过程中,制造系统vi完成vj下达的制造任务的总成本;
在第r个制造任务过程中,制造系统vi完成vj下达的制造任务的成本阈值;vi——vi完成制造任务的能力阈值,以制造成本表示(制造成本为时长*数量);M——制造任务的总数。
3. 运载器舱段制造资源网络实例分析
3.1. 案例构建
以某航天运载器产品典型舱段的装配过程为案例,搜集整理其制造任务关系。提取该类产品的3个重点部段BOM,125个对应的制造任务以及150个制造执行系统。在此基础上建立网络关系,将实际的制造任务链条和制造资源服务关系抽象成为虚拟的制造资源网络模型。表2给出了部分制造执行系统的制造资源需求信息及建立的任务链条信息。
为保证大数据量下计算的稳定性,本文采用了复杂网络分析软件UCINET进行节点建模和可视化分析。将邻接矩阵和权重矩阵以“节点 + 属性”的关系分别录入到复杂网络分析软件UCINET中,并在NetDraw可视化软件中显示其网络节点关系,如图4所示。红色节点代表制造系统,连线的粗细代表权重。
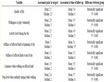
Table 2. Partial manufacturing resource demand and task chain
表2. 部分制造资源需求及任务链条
3.2. 案例分析
1) 节点的度
制造资源网络各节点度如图5所示(前70)。制造服务系统ZY5002节点度最高为210,表示该节点是核心制造资源。而实际上,该节点为承担舱段壁板组件装配任务的核心设备–壁板自动钻铆系统,与分析结果相符。
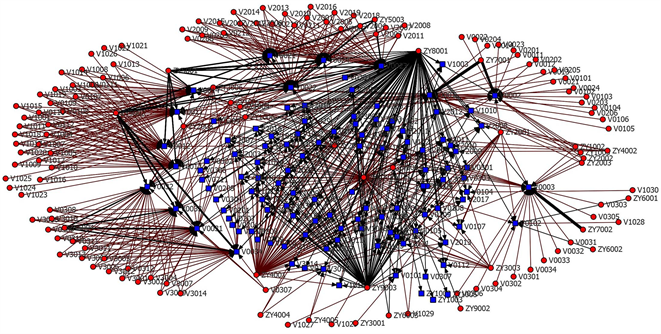
Figure 4. Topological structure of typical cabin manufacturing resource network for carrier products
图4. 运载器产品典型舱段制造资源网络拓扑结构
2) 鲁棒性特征
制造资源网络中节点的破坏会影响整个网络和局部网络特性。若节点vi被破坏,很可能造成以vi为集散节点的两个制造系统不能有效进行制造任务交互或使进行制造任务对接的路径增大。图6显示当节点vi失效时网络的鲁棒性曲线。与初始的网络最短路径相比较,节点V0002,ZY1001,ZY5002对网络鲁棒性具有较大影响。结合图5中各节点度值分析可知其原因:V0002是大型核心制造系统,向后续节点发布大量的制造任务需求,ZY1001、ZY5002是主要的制造资源。此二类节点在网络中有较大影响力,要维持制造资源的整体性能,一方面需加强对此二类节点的防护,另一方面保障该类制造资源充足。
3) 负载系数和负载饱和度特性
制造资源网络各节点的负载系数、负载饱和度分别如图7、图8。
由图7可知,系统较多节点的负载量达到2000小时左右,其中V3007、ZY1001、ZY7001节点负载接近或超过2500小时,说明其工作时间较长;结合负载饱和度分析该3个节点并未具有较大的负载系数,说明其资源总量较为充裕;ZY5001、ZY9002节点负载饱和度接近1,已经接近饱和负载,不能再继续承接制造任务。此时,任务下达方双方须适时调整制造任务匹配策略:一方面,下达方可考虑其他制造资源来完成其制造任务,另一方面,可考虑增加节点资源数量,分摊制造压力。此外,达到饱和状态的节点需尽量提高产能,降低任务工时损耗,实现降本增效。
4. 结论
本文从网络构建与分析的角度,分析了制造资源网络的创成机理,并基于复杂网络理论建立了运载器舱段制造资源网络模型,进而定义了其结构和物理特性指标。最后,结合某典型运载器舱段制造过程案例进行抽象化建模与分析,验证了网络分析方法的有效性,并揭示了大型复杂产品装配资源控制的一些现象与规律。综合本文分析结果,可得出以下结论:
1) 大量的、离散的制造执行系统通过制造任务关系建立连接,形成制造资源网络,对该网络的演化过程分析和特性分析有助于制造企业进行制造资源的决策和配置优化;
2) 将实际的制造资源集群映射为一个物理上的制造资源网络,并采用复杂网络分析方法研究该网络的整体和局部特性,有助于搜索关键资源节点和任务链接关系,有助于指导制造执行系统的规划,构建以及管控。