1. 引言
在数字经济背景下,船舶行业以数字化为基础,向着高端、绿色、智能等技术方向发展,智能船舶因其安全、经济、环保等特点,已成为未来船舶发展的必然方向 [1] 。船舶的数字化智能化离不开船舶设备的数字化,现阶段,船舶设备数字化水平参差不齐,设备数据体量、数据产生频率差距显著 [2] ,船舶设备数据集成具有典型的多源异构数据,难以采用单一的数据集成交互和存储模式。另一方面,船舶海上运营的工况条件和海事卫星为主的通信方式决定了船岸信息交互具有网络通信延时高、带宽小的特点 [3] ,传统的基于云平台的工业互联网解决方案难以直接在船舶设备智能化场景落地应用,需面向船舶设备数字化现状和数据应用需求设计一种适配船舶异构数字化设备的数据集成采集方案和系统,提升船舶数据中心对船舶异构设备的数据集成、管理和分析能力。
早在上世纪80年代,国外知名船舶自动化产品生产企业已经着手开始研发综合性船舶设备监管平台,许多舰艇和商船上已经部署安装了船舶设备管理系统,使舰船自动化程度有了较大提高 [4] 。经过近20年的反复试验和努力,国外综合性船舶设备管理平台技术已经发展地相当成熟,并已进行了广泛的实船应用。
在国内,船舶设备数据集成的主流架构是上位机和PLC专用采集控制器结合现场总线通信构成的设备监控系统,存在监测对象单一、协议适配能力差等不足。随着应用场景的差异化出现,各设备制造商制定了各种不同的现场总线标准,导致不同厂商不同设备之间的通信非常不便,也为船舶设备之间的信息互通筑起了天堑 [5] 。因此在缺乏面向全船的综合资源与信息管理平台的情况下,自主研发异构设备数据集成系统是国内船舶智能化发展的大势所趋。
2. 船舶设备数据集成需求分析
通过对船舶甲板设备、舱室设备、动力设备、通导设备数字化水平和集成能力的调研分析 [6] ,船舶设备数字化能力分为四类:
1) A类设备:设备需集成管控的信息已接入船舶统一平台,例如智能船主辅机数据接入船舶机舱监测报警系统(AMS, Alert Management System)。
2) B类设备:设备具备外部数据通信接口(通常是串口或以太网口),但监测信息不满足集成管控要求,如部分船舶锅炉管控系统具备以太网通信接口并支持ModbusTCP协议的数据交互,但是面向船舶设备能效管理的需要,缺少流量、压力等信息的数据监测。
3) C类设备:设备具备数据采集模块且监测信息满足集成管控需求,但设备独立运行,不具备外部数据通信接口,如部分液货船舶气体浓度监测系统能实现船舶各限制区域的气体浓度监测和报警,但是相关信息仅能在系统面板显示,不具备共享发送给其他系统的能力。
4) D类设备:设备集成管控信息未接入船舶统一平台系统,现有监测信息不满足设备集成管控需求,且不具备外部数据通信接口,例如船舶滑油泵、海淡水冷却泵、压载泵作为船舶主要耗能设备之一,面向船舶设备监测评估需要,存在监测信息不足且集成接口缺失的问题。
面向各类船舶设备集成管控需要,设备数据集成方案应充分借助船舶现有设备及系统相关数据监测与采集能力,借助现有的网络条件,减少设备级、网络级、系统级的硬件改造工作量。同时,设备监测采集与接口方案不可影响现有设备的性能、寿命、可靠性和船舶安全性。基于上述原则,船舶设备数据集成需求方案如下:
1) A类设备:数据集成系统作为船舶统一平台的系统工具之一,不对本类设备额外进行数据采集,本类设备保持原始的数据采集方案。
2) B类设备:在原有设备控制系统中新增采集模块,并基于现有的网络和接口条件实现与数据集成系统之间的信息交互。
3) C类设备:在设备端新增通信模块(适用于新增点位较多的设备,一路输出减少布线改造工作量),以实现与数据集成系统之间的通信。或者将传感信号直接接入数据集成系统输入输出模块(适用于新增点位较少的设备,成本更低),通过输入输出模块实现数据采集。
4) D类设备:在设备端新增采集模块和通信模块,以实现数据采集与集成(适用于新增点位较多的设备,一路输出减少布线改造工作量)。或者在设备端新增采集模块,并将将传感信号直接接入数据集成系统输入输出模块(适用于新增点位较少的设备,成本更低),通过输入输出模块实现数据采集。
3. 船舶设备数据集成架构
针对不同类型设备集成接入的需要,船舶设备数据集成方案如图1所示,设备数据集成系统向下具备多协议解析和数据采集能力,向上具备与船载平台的集成能力。各类设备借助已有的接口或通过设备集成采集系统发送到船载统一平台,实现设备集成管控各项功能。

Figure 1. Architecture of ship equipment data integration design
图1. 船舶设备数据集成方案
因此,设备数据集成系统自下而上应包括三层:
连接层:通过各类通信手段接入不同设备、系统和产品,包括在传统设备基础上新增控制模块、采集模块和传感装置等,实现设备运行状态信息提取和控制指令下发,并通过工业以太网、工业总线等工业通信协议,将现场设备统一接入到平台边缘层。
适配层:依托协议转换技术实现多源异构数据的归一化和边缘集成,一方面运用协议解析、中间件等技术兼容ModBus、OPC、CAN、Profibus等各类工业通信协议和软件通信接口,实现数据格式转换和统一,另一方面利用HTTP、MQTT等方式从边缘侧将采集到的数据传输到云端,实现数据的远程接入,同时支持设备控制指令的下达。
边缘层:对于高频、特征识别、滤波等需要的采集数据利用边缘计算模块实现底层数据的汇聚处理,并实现数据向云端平台的集成。基于高性能计算芯片、实时操作系统、边缘分析算法等技术支撑,在靠近设备或数据源头的网络边缘侧进行数据预处理、存储以及智能分析应用,提升操作响应灵敏度、消除网络堵塞,并与云端分析形成协同。
船舶设备数据集成架构如图2所示。
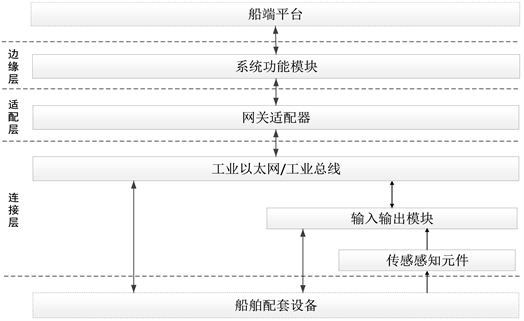
Figure 2. Architecture of ship equipment data integration system
图2. 船舶设备数据集成系统架构
4. 船舶设备数据集成系统设计
船舶设备数据集成系统向下实现异构设备监测信息的集成采集,向上实现与船舶统一平台的数据分发,功能需求包括:
I) 面向异构设备集成采集需要:
1) 能根据集成采集到的各类设备监测状态信息,匹配映射到目标设备对象,便于上游系统进行设备数据分析;
2) 能配置数据采集频率,满足设备数据分析计算的采样要求;
3) 能实时显示设备数据监测实时值和监测异常状态,帮助船员排查集成异常问题。
4) 能查询历史的数据集成异常情况。
II) 面向设备集成数据分发需要:
1) 能按照约定的报文格式将数据接口信息发送到船舶统一平台;
2) 能对数据上传接口异常进行识别与报警,帮助船员排查集成异常问题。
3) 能查询历史的接口异常情况。
基于上述功能需求分析,船舶设备数据集成系统功能清单如表1所示:
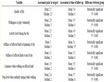
Table 1. Ship equipment data integration system function table
表1. 船舶设备数据集成系统功能表
4.1. 系统硬件组成
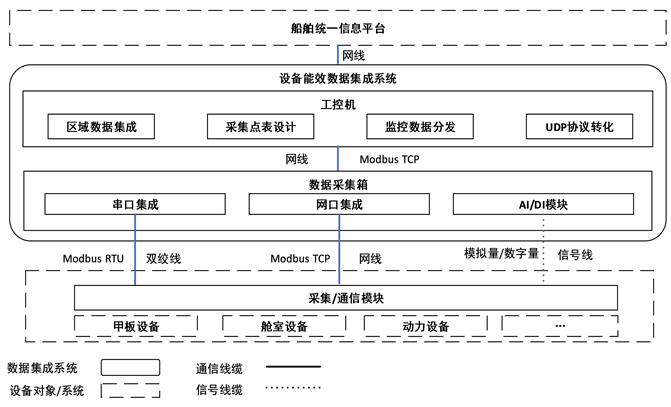
Figure 3. Construction of ship equipment data integration system
图3. 船舶设备数据集成系统组成
船舶设备数据集成系统硬件组成结构如图3所示,包括采集/通信模块、数据采集箱和工控机,设备端通过采集/通信模块将设备监测信号汇集,然后接进指定位置的集成采集箱内,集成采集箱与工控机之间通过网线进行数据传输。
采集/通信模块部署部署于设备端,根据各类设备的接口条件布置相应的采集与通信模块。
集成采集箱面向不同设备的接口要求可实现Modbus RTU、Modbus TCP、Profinet等数据通信以及通过传感器硬线的信号采集。
工控机面向能效信息、报表、监测点位人工输入的需要,搭载设备数据集成系统软件,可实现对设备报表信息的导入和监控信息前台化人工录入。
最终船舶各类设备数据集成信息通过工控机数据接口发送至船舶统一信息平台实现数据应用。
4.2. 系统软件功能
4.2.1. 集成状态分析
集成状态分析功能实现设备在线状态、系统集成状态的直观显示。
其中,设备在线情况的判定逻辑为:设备采集到的所有点位信息均为空值,则判定设备离线;存在非空的点位采集信息,则设备为在线。设备在线情况判定在解析集成接口信息时进行分析处理,如图4所示:
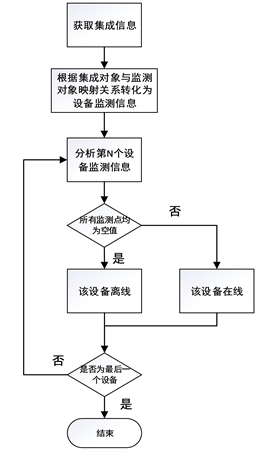
Figure 4. Equipment online status determination flowchart
图4. 设备在线状态判定流程图
集成状态的判定逻辑为:当集成数据接口中接收到对象数据报文且报文中isconnect属性为true且存在至少一个监测点位非空,则判定为在线;其他情况(未接收到集成对象报文、isconnect为false或集成对象所有点位均为空)判定为离线。集成状态分析的业务处理逻辑在解析集成接口信息时进行,如图5所示:
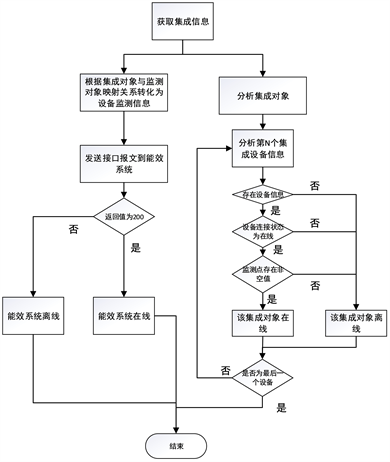
Figure 5. System integration status judgment flowchart
图5. 系统集成状态判定流程图
4.2.2. 设备实时监测
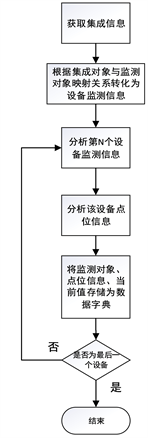
Figure 6. Real time flowchart of equipment status monitoring flowchart
图6. 设备实时状态监测流程图
实时监测功能以设备结构树的形式,按压力/流体组件、加热/冷却组件、机械设备组件分类分区域显示设备监测点位实时状态。
系统获取的实时状态数据通过静态数据字典方式存储,系统在解析集成接口信息时同步更新监测设备实时状态数据字典参数,使用数据时根据监测对象和监测点位信息获取相应的实时值,实时状态监测逻辑如图6。
4.2.3. 异常追溯
异常追溯功能按监测设备和集成对象的维度显示当前在线情况,包括当前状态、连续在线时间、离线次数、上一次离线时间,便于维护人员关注设备异常问题。
异常追溯功能业务逻辑如下:
1) 在线状态:取数逻辑和综合管控界面的在线状态一致,解析集成接口信息时记录并在界面显示。
2) 连续在线时间:取数逻辑为“当前时间–最后一次离线记录的恢复时间”,如果最后一次离线记录不存在,则为“当前时间–系统初始化时间”。
3) 离线次数:取数逻辑为记录该设备离线的所有数据的条数。
4) 最近离线时间:取数逻辑为最后一次离线记录的最新更新时间。
4.2.4. 监测点映射
监测点映射功能可根据集成采集的设备对象及点位信息,设置分析的监测设备对象及监测点位名称。
监测点映射配置功能设计包括:
I) 自动搜索匹配:搜索栏选择采集对象,系统自动匹配对应的采集点位名称及配置好的监测设备和监测对象;同样的,选择其他下拉框,各下拉框联动,自动匹配映射关系。
II) 修改映射:修改监测设备及点位映射信息后系统自动校验,校验逻辑包括:
1) 同一监测设备的监测点位不重复;
2) 一对多映射时,监测设备的数量和监测点位的数量需一致。
3) 自动映射:系统支持自动识别“_”,当采集点位命名规则符合“监测点位_监测设备”时,可自动生成监测点位和监测设备。
5. 船舶设备数据集成系统应用实践
5.1. 船舶设备能效管理系统应用实践
船舶设备能效管理系统通过对船舶上设备运行数据的采集、计算、评估、预警,对于在船人员进行及时报警提醒,合理调整设备运行数量或参数,达到节能减排的目的,对于降低碳排放和营运成本、提升船舶设备能效管理水平具有重要的意义。
船舶设备数据集成系统面向船舶主要耗能设备的能效监测与计算需要,实现了对能耗设备所需的所有采集数据进行集成,为船舶设备能效管理系统功能实现奠定数据基础,具体的集成设备信息如表2所示:
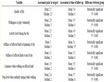
Table 2. Integrated list of ship equipment for energy efficiency management
表2. 面向能效管理的船舶设备集成清单
5.2. 液货船安全监控系统应用实践
液货船安全监控系统通过面向液货运输与作业场景的安全管控需求,从操作人员状态、作业环境、作业流程、货物状态以及设备状态五个方面,通过作业安全要素的监控与分析,实现液货作业安全要素的可视化监测和预报警。
船舶设备数据集成系统面向液货船安全要素监测分析需要,实现了人员、设备、货物、环境的要素的综合集成,为液货安全监控系统功能实现奠定数据基础,具体的集成设备信息如表3所示:
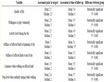
Table 3. Integrated list of ship equipment for liquid cargo safety
表3. 面向液货安全的船舶设备集成清单
6. 结语
随着船舶向绿色、智能方向发展,船舶异构设备集成互联和数据采集的需求日益迫切。本文以不改变船舶原有设备可靠性和船舶现有的网络架构为前提,提出了一种经济、可靠的船舶异构设备的数据集成方案,并基于该方案实现了一套船用设备数据集成系统。通过船舶能效管理系统和液货船安全监控系统应用实践,证明了该方案及系统可有效满足船舶异构设备数据集成与分析应用的需求。后续,方案将进一步提升设备数据集成系统对定制化协议和多种设备接口类型的拓展能力,更好的适应更多类型船舶对异构设备的集成需要。