1. 引言
随着我国塑料加工技术走向成熟,人们对塑料的性能要求越来越高,多层共挤吹塑这一成型技术最主要的特点就是改善中空吹塑产品的阻隔性能和塑料产品的综合性能。多层共挤吹塑技术生产出的容器与其他单层容器、单层化学表面处理瓶、玻璃、金属的有阻渗性能的容器相比具有高复合阻渗性,且具有高性能、低成本等的特点 [1] 。绝大多数多层应用的特点是在附加层之间嵌入具有特殊阻挡性能的层,从而提高其阻隔性。
这其中,吹塑机头的主要任务是将挤出机提供的熔体流转向垂直向下流动,并形成具有均匀周向壁厚分布的熔体管。多层吹塑机头的设计紧凑才能满足产品的要求 [2] ,多层吹塑机头与单层吹塑相比,更加复杂,设计难度更高,而五层共挤吹塑的机头设计是一大难点,本文将从这一难点入手。
2. 机头的结构设计
2.1. 机头的整体结构
中空吹塑机头的类型一般分为连续式和储料式两种,但储料式由于结构形式的局限性,一般只应用单层或双层型坯挤出。当型坯层数大于双层时,宜采用连续共挤式机头。无论储料式,还是共挤出式多层机头,关键在于熔体分配均匀,各层压力、流速相当,以保证料流在稳定状态下流动。特别是各层汇合后的流动,一定要注意防止出现不稳定的流动 [3] 。
本次设计的产品为200 L化工桶,根据大型容器的,设计要求及设计准则,确定五层吹塑机头为连续共挤式机头,其结构为嵌套式结构,即五层流道由内到外依次嵌套组合 [4] 。
多层共挤机头主要由芯模、口模、机头外筒、内芯棒、流道筒、模头、模嘴等组成。其主要结构如图1所示。
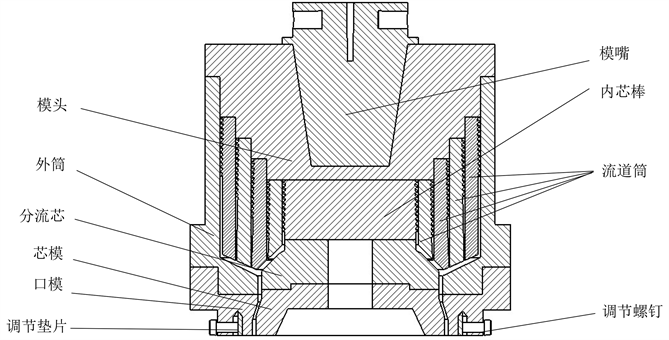
Figure 1. Main structure diagram of the machine head
图1. 机头主要结构图
在设计中,由于型坯挤出的特点各不相同,所以不同零件的尺寸以及其参数都会有所不同,为了保证模具质量和良好的成型工艺,本次设计采用45钢,五层熔体为HDPE/LDPE/EVOH/LDPE/HDPE。
2.2. 流道设计
机头中流道设计是一大难点,其设计包括流道形状的设计、流道位置的设计、入料口的位置设计以及五层流道汇合流道的设计。
流道的类型分为衣架式流道、螺旋式流道以及衣架螺旋式流道。衣架螺旋式流道是将衣架流道与螺旋流道结合,使熔体在机头内经过衣架式流道和螺旋式流道的两次分配,变得更均匀,避免了衣架流道包络产生的熔接痕。本次设计选用的正是衣架螺旋式流道,其结构如图2所示。
衣架螺旋式流道,它的工作原理是是熔融物料从进料孔进入后首先被分成十二股料流,然后物料到达十二股螺纹中各螺槽的起点处,分配通道以多线程的方式并入汇合流道。并且这些螺旋槽的深度在流动方向上减小,而两个流道之间的间隙增大。通道和间隙的几何形状相互匹配,使单个部分流动在流动方向上重叠,从而使熔流得到进一步充分有效的混合,使熔料在口模圆周方向上的压力、温度和速度分布基本达到均匀一致的目的,于是也就保证了熔体薄膜的均匀厚度。
衣架式螺旋流道的优点包括:
1) 可确保螺旋槽中对称的熔体进给,从而使型坯的壁厚分布均匀。
2) 适用于各种材料,且设计紧凑,重量轻。
3) 设计价值高,成本低。
该类型的螺旋流道头数,根据流道的直径以及流道筒的尺寸来决定,具有周期性,其数量增加有助于改善流体分布,使其分布更均匀,同时减少对零件的压力,减少其损耗。本设计的螺旋流道数为12,其结构如图3所示。
2.3. 其他主要结构设计计算
1) 口模的设计
口模是确定型坯轮廓尺寸的重要模头零件,其结构图如图4所示。
吹塑模头口模的尺寸与产品尺寸以及吹胀比有关系,考虑到熔体膨胀效应、流道末端效应、冷却收缩效应及自重下垂效应,引入修正系数α,α的大小与熔融物料的流速、温度,口模定型物料的相对分子质量等有关。
式中:D为口模直径;α为修正系数,一般为0.5~1.0,本文取0.7;DZ为制品直径,本设计为580 mm;b为吹胀比,对于大型或薄壁制品b取为1.5~3.0,通常为1.5,本文取1.5。由此得口模直径为265 mm。
当吹塑任何类型的容器或模制部件时,型坯的直径是恒定的。然而,由于吹塑成型料坯的直径通常不是恒定的。为了在整个制品中获得均匀的壁厚,必须相应地调整型坯的壁厚。这是在型坯头部的模具中完成的。所以模下端出料口的位置,为了调节挤出型坯的薄厚度,增加了36个M14的调节螺钉,以此来对料坯进行微量调节,如图5所示,通过内六角扳手对螺钉进行调节,改变口模内壁形状,从而调节口模内壁与芯模之间的距离。
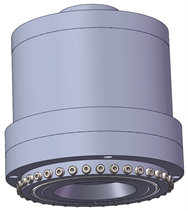
Figure 5. The final assembly diagram of the head
图5. 机头总装图
并且为了减少损耗,在口模下端设计U型凹槽,并添加垫片,减少模具的损耗,垫片尺寸如图6所示。
2) 芯模的设计
芯模同样是确定型坯轮廓尺寸的重要模头零件,其尺寸与产品的尺寸有关,且可由口模决定。其结构图如图7所示。
3. 关键部位有限元强度分析
本文利用ANSYS静力学分析版块对口模、芯模进行了有限元强度分析。
3.1. 口模强度分析
口模与芯模在实际生产过程中,主要受到的压力为来自聚合物熔体的压力以及调节螺钉的压力,而该压力的方向为流道壁的法向方向,使用传统的强度校核公式难以分析,故使用有限元软件对其进行分析,分析的步骤如下。
1) 首先是前期初步计算后建立口模的三位模型,如图8所示。
2) 然后打开ANSYS Workbench工作台,选择静力学分析版块(Static Structural)。
3) 将模型导入并选择材料属性。本次设计的材料属性为:45钢杨氏模量:200 Gpa泊松比:0.3。
4) 划分网格,本次网格采用四面体网格,如图9所示。
5) 设置分析步,并施加约束和载荷。口模所受到的载荷主要为聚合物熔体的压力,大小为40 Mpa。然后确定约束条件,口模上端与机头外壁连接,并通过长螺钉紧固连接,故对该面设置固定支撑。
求解与分析结果如图10所示。
从结果可得,口模在工作状态下最大变形为0.18 mm,最大应力为239.35 Mpa,其钢结构屈服极限为460 Mpa,在口模上表面边缘,故满足设计要求。
3.2. 芯模强度分析
芯模的材料同为45钢,在实际生产过程中,其主要收到的压力同为熔体的压力,作用在内壁,其分析步骤与上述相同,网格划分如图11所示。
其分析结果如图12所示,由结果可知,其最大应力为256.26 Mpa,作用在出料口末端,因其壁厚最薄,承受能力更弱,最大变形为0.06 mm,满足设计要求。
4. 结论
本文主要对五层共挤吹塑机头的整体以及关键部位进行了设计说明,重点设计了流道系统,并增添了壁厚控制结构,使其成型更可控。最后通过ANSYS仿真分析软件对机头出料口的关键部位进行了有限元强度校核,经分析对比,确定其符合设计要求。
注释
文中所有图片均为作者自绘或者自摄
NOTES
*通讯作者。