1. 引言
金属基复合材料(metal matrix composites),简称(MMCs)是以金属及其合金为基体,与一种或几种金属、非金属增强相人工结合成的复合材料,按照增强方式可以分为纤维增强型和颗粒增强型复合材料。铝基碳化硅(SiCp/Al)复合材料具有高比强度、高比模量、良好的耐磨性和耐高温性,因而广泛应用于航空航天、电子通信、军工等领域 [1] [2] [3] 。不同SiC颗粒含量的SiCp/Al复合材料所具有的性能也不同,导致其在各个领域都有不同的应用。15~25%体积分数的SiCp/Al被用作承载件;30~50%的SiCp/Al复合材料主要用于制作光学等领域的精密仪器;55~75%的SiCp/Al复合材料由于含有大量的碳化硅颗粒,其主要用于电子封装、热控装置等 [4] 。
在过去的几十年里,SiCp/Al复合材料作为难加工材料,增强颗粒SiC的引入给刀具带来较高的磨损率,从而导致工件表面质量恶化。Huang等 [5] 分析比较了PCD刀具,TiC基金属陶瓷刀具,TiN涂层刀具和硬质合金刀具的切削性能和磨损机理,并对PCD刀具进行干、湿式高速铣削实验,结果表明,PCD刀具是最适合长期高速铣削体积分数较高SiCp/Al复合材料的刀具。
实验受限于成本、设备等因素,具有一定的局限性。有限元仿真在金属去除机理,表面缺陷以及工艺优化等方面有着不可替代的作用。王进锋等 [6] 对SiCp/Al复合材料使用仿真与实验相结合的方法,研究了车削在不同切削参数下切削力的变化规律。Zhou L等 [7] 采用有限元分析和实验相结合的方法,研究了高体积分数SiCp/Al复合材料的正交切削加工性能,包括加工表面质量、刃口质量和亚表面残余应力分布。
本文建立了45%体积分数的SiCp/Al复合材料的二维正交切削模型,分析SiCp/Al复合材料的切削去除过程和表面形貌,不同切削参数对切削力的影响,并以仿真结果为依据,采用PCD铣刀对45% PVFs SiCp/Al复合材料进行多因素正交铣削试验。实验获得的切削力变化及波动与仿真结果一致,偏差均小于20%,验证了有限元模型的有效性,为后续继续研究刀具磨损、工艺优化提供参考。
2. 有限元模型
2.1. 有限元几何模型的建立
本文通过ABAQUS有限元软件对切削过程进行模拟,二维正交切削SiCp/Al复合材料仿真模型如图1所示,工件尺寸为1.5 mm × 0.8 mm,模型中包括Al基体、增强相SiC颗粒以及基体–颗粒界面层,分别对基体、颗粒、基体–颗粒界面层三相材料建模,赋予材料属性。通过python二次开发实现增强相SiC颗粒随机分布,其体分比为45%,平均粒径为20 µm~30 µm,从而建立一个完整的SiCp/Al本构模型。
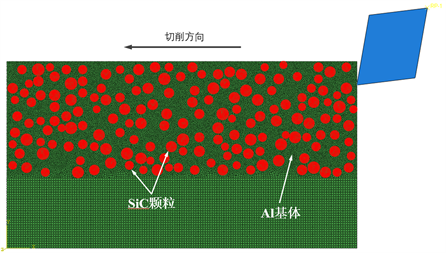
Figure 1. Two-dimensional orthogonal cutting SiCp/Al simulation model
图1. 二维正交切削SiCp/Al仿真模型
切削过程是一个动态、非线性并且大变形的复杂过程,采用ABAQUS/explict求解器中动力–显式位移分析步对有限元模型进行求解。切削SiCp/Al复合材料一般采用PCD刀具,在切削过程中,考虑到PCD刀具高硬度,切削变形小的特点,故在仿真中将其定义为解析刚体,并在刀具上设定参考点,以便输出反作用力即切削力。将SiCp/Al复合材料工件底面和左面完全固定,通过给PCD刀具参考点设置一个向左的切削速度,来实现SiCp/Al复合材料的切削过程。为了更高效准确地进行切削仿真,对切削层中SiC颗粒及其周围的Al基体进行网格细化,不参与切削的Al基体内没有进行SiC颗粒的随机分布,以降低有限元模型的计算量。
增强相SiC颗粒与Al基体通过COHESIVE内聚力单元连接,在通用接触中设置内部单元面的自接触,可以防止刀具与工件穿透,切屑穿透未加工表面的现象。设计工件与刀具之间的接触为面–面接触,将切向摩擦定义为罚摩擦,摩擦因数设置为0.15。法向摩擦定义为“硬”接触。
2.2. 本构模型及切屑分离准则
(1) Al基体材料
铝合金具有流动特性,应变、应变速率和高温对其影响很大,因此本文采用Johnson-Cook本构模型,模型中的参数如表1所示,本构模型可以表示为 [8] :
(1)
式(1)中:Tm、Tr分别表示室温(K)和材料熔点(K);
、
分别表示等效塑性应变率和参考应变率;m为材料热软化系数;A表示材料室温下的屈服强度;n、C分别表示材料应变及应变率强化系数。
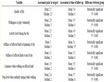
Table 1. JC parameters of Al matrix [9]
表1. Al基体的JC参数 [9]
(2) 增强相SiC颗粒
SiC颗粒是一种不同于Al的脆性材料,在SiCp/Al复合材料的切削过程中容易发生脆性断裂失效现象。因此采用ABAQUS中的脆性断裂模型,对SiC颗粒的断裂失效行为进行模拟。
SiC颗粒在断裂前处于弹性状态,应力–应变关系遵守胡克定律,其断裂开始的判断准则采用最大正应力准则,即:
(2)
式(2)中
为主应力分量(Mpa);σ0为材料的抗拉强度(Mpa)。
在SiC颗粒发生断裂失效后,其演化规律遵循断裂能准则,可以表示为:
(3)
式(3)中uno为破坏时的法向位移(µm),Gf,Gtu分别表示I型断裂能和断裂应力初始值。Al基体、SiC颗粒以及PCD刀具的材料属性见表2。
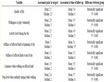
Table 2. Al matrix, SiC particles and PCD cutting tool material properties
表2. Al基体、SiC颗粒及PCD刀具材料属性
(3) 颗粒–基体界面层
颗粒–基体界面层采用粘性单元法,牵引分离响应。连续牵引下,粘性表面之间的牵引力会随分离距离的增加呈先增大后减小的趋势。粘性域单元的应力–位移曲线可以由三个物理参数中任选两个来确定,即界面强度、界面完全失效时的最大位移和界面断裂能。界面断裂能和界面完全失效时的最大位移之间存在以下的关系:
(4)
式(4)中,Gc为界面断裂能。
3. 实验条件与设计
3.1. 实验条件
实验工件为45%体积分数SiCp/Al复合材料,工件尺寸均为120 mm × 70 mm × 3 mm的长方形块料,颗粒的平均边缘尺寸为20 μm。45%体积分数SiCp/Al复合材料的详细材料组成和力学性能分别如表3、表4所示。
实验装置示意图如图2所示,高速铣削实验在德玛吉DMC650V立式加工中心上进行。Kistler三向压电式测力仪连接到电荷放大器固定在夹具下进行采集,采样频率为2000 Hz。
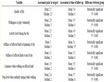
Table 3. Material composition of different VFs SiCp/Al composites
表3. 不同体积分数SiCp/Al复合材料的材料组成
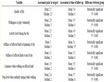
Table 4. Mechanical properties of different VFs SiCp/Al composites
表4. 不同体积分数SiCp/Al复合材料的力学性能
3.2. 实验设计与方法
在本文中,实验条件为干式铣削,符合绿色制造理念。为了验证有限元仿真模型的有效性,采用正交试验能最大限度地减少实验次数,采用PCD铣刀对45%体积分数SiCp/Al复合材料进行多因素正交铣削实验,每次铣削长度为50 mm。选定切削速度、每刃进给量及进给速度3个因素,每个因素取3个水平,通过Kistler三向压电测力仪测量三向切削力。铣削参数和水平设置如表5所示。
4. 结果与分析
4.1. 仿真结果分析
4.1.1. 切削去除过程
为了模拟45% SiCp/Al复合材料的切削去除过程,采用和实验参数相同的SiCp/Al工件,把切削过程简化为二维正交切削模型。在切削去除过程中,PCD刀具与SiCp/Al接触的应力分布情况如图3所示。
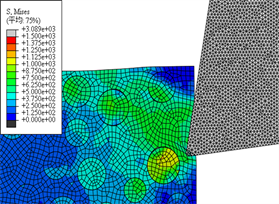
(a) 塑性去除 (b) 应力集中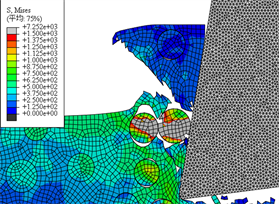
(c) 颗粒破碎 (d) 颗粒相互作用
Figure 3. Simulation of cutting removal process
图3. 切削去除过程仿真
图3(a)中,PCD刀具首先与Al基体发生接触,发生塑形变形,应力较小,将其中的SiC颗粒一并带出,形成切屑,在前刀面形成粘结磨损。(b)中PCD刀具还未接触到SiC颗粒时,SiC颗粒出现了应力集中的现象,说明Al基体和SiC颗粒会产生相互作用力。(c)中当PCD刀具进给并切削到SiC颗粒时,SiC受到压应力发生脆性断裂并破碎,产生较大应力。(d)中SiCp/Al复合材料在与PCD刀具接触时,Al基体和SiC颗粒承受着不同的应力,出现了颗粒相互挤压作用,同时对前刀面造成二体滑动摩擦,随着PCD刀具沿着切削方向切入工件,当刀具与SiC颗粒接触时,SiC颗粒受到压应力而到达颗粒脆性断裂准则时,会产大较大应力并发生剥离、发生破碎。随着切削的进行,破碎的SiC颗粒会随着被切除的Al基体一起沿着刀具前刀面流出成为切屑的一部分。当颗粒位于切削路径上时,最大Mises应力主要出现在刀具前刀面与第二变形区以及SiC颗粒周围。
4.1.2. 仿真表面形貌
由于Al基体和SiC颗粒具有不同的材料属性和力学性能,在加工SiCp/Al复合材料时,主要取决于这两种不同材料的失效形式,其中SiC颗粒的失效去除方式是影响切削表面形貌的重要影响因素 [10] 。仿真表面形貌如图4所示,主要有颗粒破碎、凹坑、颗粒拔出、颗粒脱粘、基体撕裂等表面缺陷。当SiC颗粒靠近刀具路径,颗粒受力较大,往往会发生破碎甚至被切断的现象,当颗粒在刀具前刀面上方时,往往会随着Al基体塑性去除的同时被带出工件。另外,当颗粒之间接触产生挤压的相互作用时,颗粒也有可能出现破碎。

Figure 4. Surface topography in simulation
图4. 仿真表面形貌
4.1.3. 切削速度对表面形貌和切屑形成的影响
切削速度是切削过程中关键加工参数之一,不同切削速度下的表面形貌和切屑形成如图5所示。固定进给深度0.1 mm,切削速度为250 m/min,300 m/min,350 m/min。
当其它条件不变的情况下,随着切削速度的增大,刀具对SiC颗粒会有更频繁的冲击碰撞,会快速产生切屑,导致切削温度升高,使得Al基体软化,SiC颗粒更容易切削。从图中可以看出高速切削获得的加工表面质量明显比低速切削的更好,故在实际加工中采用尽量高的切削速度能获得更好的表面质量。
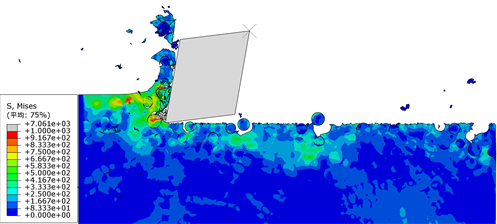
(a) Vc = 250 m/min, ap = 0.1 mm
(b) Vc = 300 m/min, ap = 0.1 mm
(c) Vc = 350 m/min, ap = 0.1 mm
Figure 5. Surface topography and chip morphology at different cutting speed
图5. 不同切削速度下的表面形貌和切屑形成
4.1.4. 进给深度对表面形貌和切屑形成的影响
图6为固定切削速度,改变进给深度下的应力变化情况,可以看出切屑的尺寸随着进给深度的增大而增大,同时刀具与Al基体,SiC颗粒碰撞机会更加频繁,会出现大量SiC颗粒的挤压、拔出、碎断等现象,使得刀具–切屑接触面积增大,表面质量变差,切削力明显增大。切屑脱落的过程中,前刀面容易受到切屑的强烈摩擦和挤压所造成的二体滑动摩擦和三体滚动摩擦。
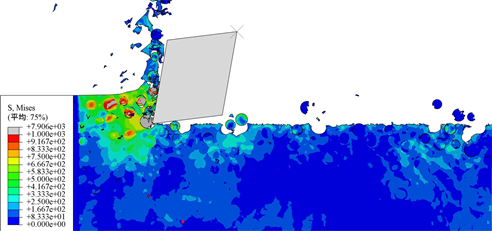
(a) Vc = 300 m/min, ap = 0.1 mm
(b) Vc = 300 m/min, ap = 0.2 mm
(c) Vc = 300 m/min, ap = 0.3 mm
Figure 6. Surface topography and chip morphology at different feed depth
图6. 不同进给深度下的表面形貌和切屑形成
4.2. 切削力分析
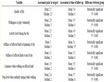
Table 6. Deviation table of 45% SiCp/Al cutting force experimental and simulation value
表6. 45% SiCp/Al切削力实验值和仿真值偏差表
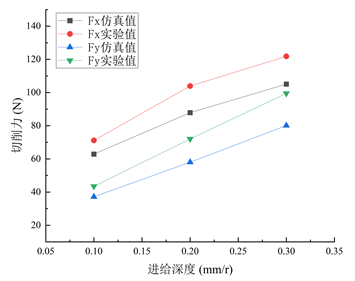
Figure 7. Related curve between feed depth and cutting force (Vc = 300 m/min)
图7. 切削力随进给深度变化曲线(Vc = 300 m/min)
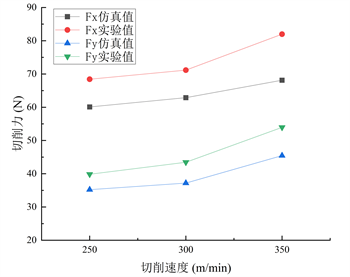
Figure 8. Related curve between cutting speed and cutting force (ap = 0.2 mm)
图8. 切削力随切削速度变化曲线(ap = 0.2 mm)
为了对比分析SiCp/Al复合材料切削力仿真与实验结果,选取第1、2、3、5、7组实验进行仿真模拟,各种仿真的切削参数与对应实验切削参数一致。将相同切削条件下的仿真结果与实验结果进行对比,并进行偏差分析,具体的切削力仿真值与切削力实验值的偏差表如表6所示。
通过仿真值和实验值偏差分析可以看出,切削力仿真值和实验值偏差均低于20%,基本在可接受的范围内。从图7、图8可以看出,仿真切削力与实验切削力变化趋势一致,随着切削速度和进给深度的增加,Fx和Fy均随之增大,这是因为切削速度和进给深度的增大使得刀具与复合材料中增强相SiC颗粒的碰撞机会增大,从而使得切削力增大,切削力与切削参数有显著的关联性。随着进给深度的增大,Fx和Fy明显增大,且Fx大于Fy,而随着切削速度的增大,Fx和Fy缓慢增大,表明切削力对进给深度的变化更加敏感。切削时的波动特性与仿真相似,但是实验值均大于仿真值,可能与铣削加工过程中的振动,刀具磨损等因素有关。
5. 结论
本文通过ABAQUS建立了二维正交切削SiCp/Al复合材料模型,对不同切削速度,进给深度条件下进行仿真分析,并结合正交试验方法验证,得出以下结论:
(1) 颗粒破碎、凹坑、基体撕裂是影响表面形貌的重要因素,在实际加工中应采用较高的切削速度和较小的进给深度。
(2) 切削力与切削速度,进给深度呈正相关,进给深度对切削力的影响更加显著。
(3) 通过切削力实验值和仿真值偏差分析,验证了模型的准确性,进而为研究刀具磨损、加工表面完整性提供参考。
参考文献