1. 引言
爆炸冲击的轻量化防护目标对于结构的比刚度和比强度提出了越来越高的要求,防护结构须在满足抗冲击要求的情况下最大程度减小重量。相比于传统的单层结构,多层结构具有结构简单、抗爆效率高等优点,已在舰船底部防护、空间碎片防护等领域获得广泛应用 [1] [2] 。在爆炸冲击加载下,多层结构可通过提升各层的抗爆效率来实现结构的轻量化。
作为典型的多层结构,间隔结构通过结构大范围塑性变形、拉伸撕裂、剪切破坏等多种破坏模式进行吸能 [3] 。安宣谊 [4] 的研究结果表明,在相同的加载模式下双层靶的间隔显著影响靶板变形破坏特征,且随着靶间距增加后续靶板变形明显减小。郭君等 [5] 通过数值模拟研究了爆炸冲击波载荷在双层结构中的传播并分析了双层底结构的破坏过程。Liu等 [6] 使用改进的二阶双重渐进近似方法研究了冲击波载荷在充水双层壳体结构间的传播机理。古滨等 [7] 建立了通过流固耦合计算模型探究了不同板间介质对冲击波载荷传播的影响规律。陈岩武 [8] 结合实验和数值计算研究了舰船双底部结构在水下爆炸载荷的毁伤特性。然而由于冲击波与结构作用的复杂性,上述研究主要针对双层结构,对于三层甚至更多层的间隔结构涉及较少。与此同时,杨新河 [9] 研究了波纹及角锥迎爆面的抗爆性能,结果表明角锥迎爆面抗爆效果显著优于普通抗爆墙,但是该研究主要针对单层角锥结构。为了对比多层间隔结构与多层及角锥结构的抗爆能力,本文选取了间隔铝板结构与间隔铝锥结两类结构,通过爆轰实验观察二者在爆轰加载下的变形响应,为类似抗爆结构的设计提供建议。
2. 实验试件与方法
2.1. 试件
实验在爆炸容器内开展,试件为6061铝合金加工而成的间隔铝板结构与间隔铝锥结构,其外径均为Φ580 mm,铝锥锥角约100˚。间隔结构件图1,间隔铝板结构自迎爆面到背爆面分别为25 mm铝板/15 mm铝垫环/25 mm铝板/10 mm铝垫环/10 mm铝板,间隔铝锥结构自迎爆面到背爆面分别为两层12 mm铝锥/15 mm铝垫环/两层12 mm铝锥/10 mm铝垫环/一层12 mm铝锥。间隔铝板与间隔铝锥整体厚度相同,其前两层厚度基本相当。
2.2. 装置及布局
本文主要考察两类结构在爆轰加载下的变形行为,所采用的炸药为Φ200 mm × 480 mm的柱形TNT,其当量约24 kg,炸药通过雷管和传爆药在两端起爆。实验布局见图2,间隔铝板结构与间隔铝锥结构通过盖板及螺栓分别紧固于法兰内,法兰可以提供侧向约束。法兰与容器焊接,焊接后间隔铝板与间隔铝锥结构对称分布在炸药两侧,且二者迎爆面到炸药中心的距离均为1400 mm。上述结构中,盖板的压紧宽度为30 mm,铝板及铝锥可自由变形区域直径约520 mm。
(a) (b)
Figure 1. Specimens. (a) Spaced plate; (b) Spaced cone
图1. 试件结构。(a) 间隔铝板结构;(b) 间隔铝锥结构
3. 结果与讨论
3.1. 整体破坏情况
图3(a)展示了实验后间隔铝板状态,第一层迎爆面可见爆轰产物,由此可区分出铝板的约束区及自由区。三层铝板均出现明显变形,其中第一层25 mm铝板整体弯曲,且变形沿约束边缘到中部逐渐增大。图3(b)展示了实验后间隔铝锥状态,第一层迎爆面同样可见爆轰产物。前两层铝锥锥体未见整体压垮,锥面从约束边缘开始出现凹陷;后三层铝锥未见明显变形。由上可见铝板以整体大变形为主,铝锥以局部破坏为主,而间隔铝锥的破坏程度弱于间隔铝板,且防护效率更高。
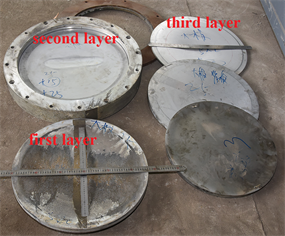
(a) (b)
Figure 3. Overall damage. (a) Spaced plate; (b) Spaced cone
图3. 整体破坏情况。(a) 间隔铝板结构;(b) 间隔铝锥结构
3.2. 局部破坏情况
图4展示了间隔铝板各层变形情况,三层铝板中心部位面外变形挠度分别为34 mm、20 mm和10 mm。第一层和第二层的挠度分别大于第一层与第二层15 mm间隔、第二层与第三层的10 mm间隔,导致第二层和第三层出现清晰压痕。由于第一层铝板未发生破裂,第二层铝板并未受冲击波作用,其响应主要靠第一层铝板的变形驱动,并以此实现能量传递。可见,后端铝板响应与前端铝板的变形程度及间隔距离密切相关。
(a) (b) (c)
Figure 4. Damage of spaced plate. (a) First layer of plate; (b) Second layer of plate; (c) Third layer of plate
图4. 间隔铝板变形情况。(a) 第一层铝板;(b) 第二层铝板;(c) 第三层铝板
图5(a)展示了第二层铝板出现的横向压痕,压痕横向长度约30 cm,呈带状分布,其宽度约10 cm。图5(b)展示了第二层12 mm铝锥表面出现的横向压痕,压痕在锥体与锥面连接处最为明显,但是并未呈明显的带状分布。
3.3. 结果分析
两类结构均以塑性变形的方式吸能冲击能量,但间隔铝锥的总体吸能效率高于间隔铝板。为了进一步明确两类结构的破坏机理,对载荷作用过程进行了数值模拟。数值模拟采用AUTODYN软件,空气采用Ideal Gas状态方程,炸药采用JWL状态方程,空气与炸药均采用欧拉算法。由于数值模拟主要对比爆炸载荷特征,计算模型可简化为二维轴对称模型。为避免实验尺度过大影响计算效率,数值模拟对实验进行1:4缩比,缩比后的炸药尺寸为Φ50 mm × 120 mm,迎爆面到爆心距离为350 mm,锥体高度约42 mm,模型两侧施加无反射边界条件。如图6所示,平面结构从中心沿X轴每5 mm选取一个高斯点进行压力监测,锥形结构高斯点沿锥体与平面结构高斯点的投影重合,两类模型高斯点各选取17个。
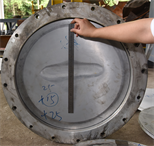
(a)
(b)
Figure 5. Indentation on the spaced structures. (a) Indentation on the second layer of plate; (b) Indentation on the second layer of cone
图5. 间隔结构压痕情况。(a) 第二层铝板压痕;(b) 第二层铝锥压痕
(a)
(b)
Figure 6. Numerical model. (a) Model of plate; (b) Model of cone
图6. 数值模型。(a) 平板模型;(b) 铝锥模型
图7展示了起爆后爆轰波到达结构前的形貌,初始阶段两端起爆点附近为高压区。图8展示了冲击波在中部汇聚后与平面的作用过程,图9展示了冲击波在中部汇聚后与锥面的作用过程,可以看出冲击波到达平面时发生正反射,到达锥面时发生绕射,作用过程有明显差异。
图10展示了铝板高斯点的压力历程,中心点1和距离中心5 mm的点2压力显著高于其他部位,从距离中心10 mm的点3开始载荷大幅下降,主要由于汇聚冲击波在中心点区域发生了正反射后形成了高压区,这可以解释铝板压痕呈带状分布的现象。
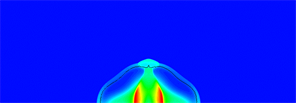
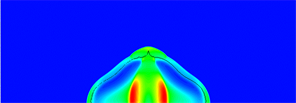
Figure 7. Morphology of the shock wave before reaching the structure
图7. 到达结构前冲击波形貌
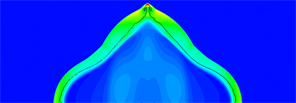
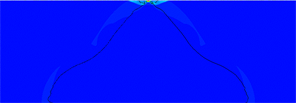
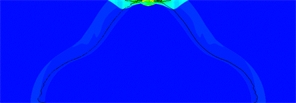
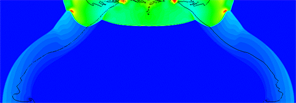
Figure 8. Morphology of the shock wave after reaching the plate
图8. 到达平面后冲击波形貌
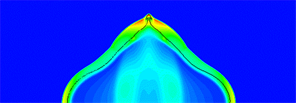
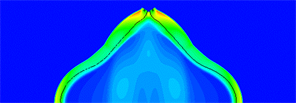
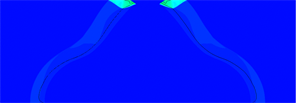
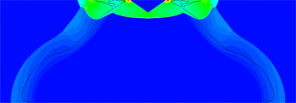
Figure 9. Morphology of the shock wave after reaching the cone
图9. 到达锥体后冲击波形貌
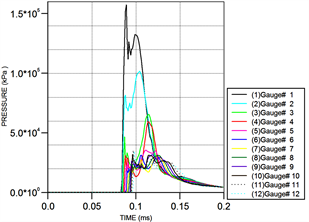
Figure 10. Pressure history of Gauge points on plate. (a) Pressure history of Gauge 1~12 on plate; (a) Pressure history of Gauge 13~17 on plate
图10. 铝板高斯点压力历程。(a) 铝板高斯点1~12压力历程;(b) 铝板高斯点13~17压力历程
图11(a)展示了锥体高斯点的压力历程,冲击波出现前小后大的两道波峰,且首道冲击波峰值随到爆心的距离而呈减小趋势。根据作用时间及两道峰值出现的时间差可以分析出锥体附近首道波为入射冲击波,第二道波为反射后形成的冲击波。锥体高斯点未见压力显著高于其他部位的现象,这与未出现带状压痕的实验结果一致。与此同时,上述高斯点两道冲击波强度均明显弱于平板中心部位强度,表明锥面可以通过降低首道冲击波载荷、延缓后续冲击波作用时间实现冲击波的有效卸载,进而减小铝锥结构响应。图11(b)展示了锥面附近高斯点压力历程,均呈典型的反射冲击波特征,其载荷水平与铝板相当,但是首道冲击波峰值远大于锥体首道冲击波峰值。
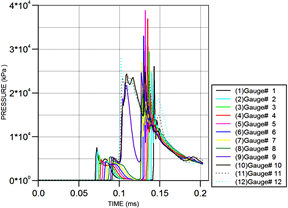
Figure 11. Pressure history of Gauge points on cone. (a) Pressure history of Gauge 1~12 on cone; (a) Pressure history of Gauge 13~17 on cone
图11. 铝锥高斯点压力历程。(a) 铝锥高斯点1~12压力历程;(b) 铝锥高斯点13~17压力历程
4. 结论
本文通过设计爆轰实验,观察了间隔铝板结构和间隔铝锥结构在柱形炸药两端起爆加载下的变形破坏模式。实验结果显示,间隔铝板出现了大面积塑性变形,且由挠度大于间隔距离引发了后端结构变形,且压痕呈带状分布;间隔铝锥体未出现坍塌,而锥面出现了弯曲变形。结合实验及数值模拟结果可进一步分析到,柱形炸药两端起爆加载下,汇聚冲击波与平面作用会出现高压带,而锥形结构可有效卸载冲击波且避免高压带出现。本文的研究对于间隔铝板与铝锥结构设计有以下启示:
1) 间隔结构可以充分利用塑性变形吸能,但在设计时应基于预估的结构变形量给出合适的间隔距离;
2) 在合适的刚度、强度下,间隔铝锥可以通过卸载冲击波提高防护效率,但需避免锥面等薄弱部位整体剪切破坏引起防护失效。
基金项目
国家自然科学基金资助项目(11932018、12072332)。
NOTES
*通讯作者。