1. 引言
目前,全球95%以上的H2生产是通过化石燃料的蒸汽重整、气化或氧化获得的 [1] [2] 。为了满足日益严格的碳排放政策,必须考虑到CO2捕获、储存和净化的高昂成本。氨分解制氢具有不含COx、SOx、NOx等有害物质的特点,不会排放CO2,不会危害生态平衡,是其他含碳原料制氢所不能比拟的 [3] 。由于氨的氢含量高(重17.8%,体积密度为121 kg H2m−3,10 bar),且不含碳,因此常被认为是化学储存的可行选择。它的能量密度为13.6 GJ m−3,这个值介于氢和汽油 [4] [5] [6] 之间。如果用可再生资源生产氨,则整个制氢过程的碳足迹很低。氨气在20℃下、8.6 bar的低压下便可液化,因此运输和储存相对容易 [7] 。在安全问题上,氢气的爆炸极限为4%~75%,氨气在空气中的爆炸极限较窄,为16%~25%,低至5 ppm的浓度很容易被嗅觉检测到 [8] 。
NH3的分解反应为吸热反应,2NH3(g)→N2(g) + 3H2(g) ∆H = 46.22 kJ/mol,需要高的工作温度才能使氨分解反应完成,从而产生纯度很高的氢 [4] 。分解反应需要的高温导致了能量供应的必要性,因此,正在开发适当的催化剂以在较低的温度下以高效率运行氨分解反应 [9] 。最近文献中已经出现了大量关于氨分解催化剂的研究,有一个普遍的共识,那就是Ru是氨分解反应活性最好的金属 [10] [11] [12] [13] [14] 。Ganley等研究了Al2O3颗粒上负载的许多金属,他们报告了氨分解催化剂活性遵循的顺序:Ru > Ni > Rh > Co > Ir > Fe > Pt > Cr > Pd > Cu [15] 。金属催化剂上氨分解反应机理目前得到了广泛的研究 [15] [16] ,普遍认为的是NH3开始吸附在金属活性位点上,然后NH3分子上的3个N-H键开始逐步断裂,H原子脱附在金属表面,最后吸附在金属表面的H原子和N原子再分别重组脱附生成H2和N2。
CuO作为氨常用的检测器,在室温下对氨具有高灵敏性和选择性,同时广泛用于氨的选择性氧化。众所周知,二氧化铈(CeO2)作为一种稀土氧化物,可以产生丰富的氧空位,与金属之间的具有强相互作用,以及Ce元素可以在Ce3+和Ce4+之间变换。Ce可以阻碍Cu的烧结,在CuO-CeO2结合处形成强相互作用,增强热稳定性 [17] 。因此,将Ce掺杂至CuO用于氨的分解或许会显示出较好的性能。Wang等采用表面活性剂模板法将活性Cu掺杂到CeO2中,发现细小而高分散的CuO物种是NH3分子的主要吸附位点,在CuO-CeO2催化剂中近表面区域化学态的快速变化和强电子态的相互作用下,NH3(ad)可被氧化活化为NHx物种 [18] 。
因此,本研究通过水热法制备了CuCex载体,采用浸渍法将Ru负载于载体上,制备了Ru/CuCex催化剂用于氨分解反应,与CuO负载Ru相比,掺杂Ce的Ru/CuCex催化剂具有高活性,其中Ru/CuCe50在450℃以下显示出较高活性,Ru/CuCe12在450℃以上表现出最高的氨分解活性。
2. 实验
2.1. 催化剂制备
2.1.1. 铜铈氧化物载体制备
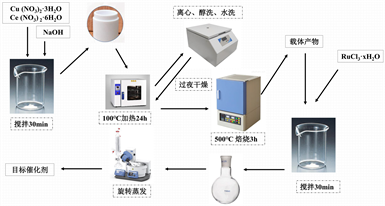
Figure 1. Preparation diagram of Ru/CuCex catalyst
图1. Ru/CuCex催化剂制备图
图1为催化剂制备流程图。具体操作如下:称取4.0 mmol Cu (NO3)2·3H2O溶解在30 ml去离子水中,在搅拌下滴加6 mol/L NaOH水溶液,搅拌30 min;将溶液转移至聚四氟乙烯内衬的不锈钢高压反应釜中,100℃加热24 h。将沉淀通过离心,去离子水和无水乙醇洗至性;得到的产物在80℃过夜干燥,并以2℃/min升温至500℃,在500℃下煅烧3 h得到CuO。
不同摩尔比的CuCex (x = 0.5/1/5/12/50)制备,称取计算量的Ce (NO3) 2·6H2O、Cu (NO3)2·3H2O于烧杯中,按照上述方法制备CuCex载体。
2.1.2. Ru/CuCex催化剂制备
浸渍法制备Ru/CuCex:称取计算量的上述不同载体于30 ml的去离子水中;量取计算量的RuCl3·xH2O于上述溶液中,加搅拌子常温搅拌30 min;去除搅拌子,将溶液转移至旋转蒸发仪的烧瓶中,用适量去离子水冲洗烧杯内壁残余溶液,使用旋转蒸发仪去除水分,待水分蒸干,收集烧瓶内壁材料得到Ru/CuCex。
2.2. 催化剂的表征方法
X射线衍射(XRD)使用DX-2700B X-ray Diffractometer,以CuK为辐射源,电压为40 KV,电流为30 mA,扫描范围为5˚~90˚,扫描速率为0.5˚/min。
H2-TPR表征是在沃德VDSORB-91i中进行的。在进行测试分析之前,先将100 mg (20~40目)的样品置于U型石英管中,并放置化学吸附仪器内;设置Ar为除去样品中H2O、CO2等杂质的保护气,同时对样品以10℃/min的升温速率从30℃升到300℃并保温1 h以达到充分去除吸附杂质的目的;接着将温度降为50℃后将Ar换为10% H2/Ar的混合气,其流速为30 ml/min;最后化学吸附仪以10℃/min的升温速率从50℃升温至600℃进行催化剂的氢气升温还原。
NH3-TPD表征是在沃德VDSORB-91i中进行的。试验前,100 mg样品在300℃的He中脱气30 min,然后冷却至100℃,随后在NH3气流(1%,20 ml/min)中吸附40 min,然后气体切换为He,流速20 ml/min进行吹扫,最后在He中以10℃/min的速率从100℃升温到600℃进行催化剂的氨气升温脱附。
CO2-TPD表征是在沃德VDSORB-91i中进行的。在进行测试分析之前,先将100 mg (20~40目)的样品置于U型石英管中,并放置化学吸附仪器内。设置He为除去样品中H2O、CO2等杂质的保护气,同时对样品以10℃/min的升温速率从30℃升到300℃并保温30 min;然后以10℃/min的速率将温度降为40℃,将He切换为CO2,其流速为30 ml/min,在40℃下吸附60 min;然后气体切换为He,流速30 ml/min,吹扫60 min,最后化学吸附仪以10℃/min的升温速率从40℃升温至600℃进行催化剂的二氧化碳升温脱附。
原位红外表征是在赛默飞(NICOLET Is50 FT-IR)光谱仪上采集一系列原位漫反射红外傅里叶变换光谱(In Situ DRIFTS),扫描次数32,分辨率为4 cm-1。采用1000 ppm的NH3/Ar进行原位红外表征,测试前,以10℃/min的速率升温到300℃,使用Ar,流速为30 ml/min进行吹扫60 min;随后,以10℃/min的速率升温到350℃使用H2/Ar (10 ml/min)进行还原60 min;随后将气体切换为Ar,流速30 ml/min并在降温时进行背景采集,每50℃为一个采集点;随后从100℃~300℃进行催化剂的原位漫反射红外傅里叶变换光谱采集。
2.3. 催化剂活性评价方法
在常压固定床反应器上对催化剂进行氨分解活性测试。通常情况下,0.1 g催化剂(筛分20~40目)被放入内径为8 mm的不锈钢反应器。在300℃下Ar气氛下进行吹扫1 h,之后以5℃/min的速率升温至350℃,气体换为10% H2/Ar进行1 h还原;随后将气体换为Ar,并降温至300℃吹扫30 min;最后向反应器内通入10% NH3/Ar (50ml/min),将反应器加热至所需温度,用气相色谱仪(GC9790Ⅱ)对产物进行分
析,检测温度范围300~600℃,每50℃取一个活性测试点。氨气转化率计算
:
表示氨气的转化率,
表示反应前氨气的峰面积,
表示反应后氨气的峰面积。
3. 结果与讨论
3.1. 催化剂的活性评价结果
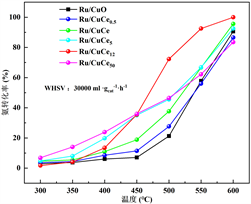
Figure 2. Ammonia decomposition conversion of Ru/CuCex catalyst
图2. Ru/CuCex催化剂的氨分解转化率
活性测试如图2所示,可以看出,Ce的掺杂可以提高氨分解的转化率。同时450℃是氨分解活性的一个温度转折点,450℃以下,氨分解的转化率顺序如下:Ru/CuCe50 > Ru/CuCe5 > Ru/CuCe12 ≈ Ru/CuCe > Ru/CuCe0.5 ≈ Ru/CuO;而450℃以上,Ru/CuCe12氨的转化率最高。氨分解活性不仅随掺杂量变化,同时还有反应温度的影响。在WHSV为30,000 ml gcat−1·h−1和温度达到600℃时,氨的转化率可以达到99%。
3.2. 催化剂的表征结果
3.2.1. XRD
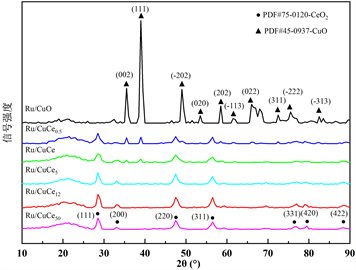
Figure 3. XRD spectra of Ru/CuCex catalyst
图3. Ru/CuCex催化剂的XRD图谱
Ru/CuCex催化剂的XRD图谱如图3所示,Ru/CuO可以检测到明显的CuO的衍射峰,9个明显的特征峰对应于CuO的(002)、(111)、(−202)、(020)、(202)、(−113)、(022)、(311)、(−222)、(−313)晶面,衍射峰都较尖锐,说明样品结晶性较好。而随着Ce掺杂量的增加,CeO2的衍射峰强度逐渐增加,CuO的衍射峰逐渐变得不明显,Ru/CuCe0.5、Ru/CuCe只能明显看出有(002)、(111)两个衍射峰;当Ce与Cu的摩尔比为5时,可以清晰看到,与未掺杂的催化剂相比,CuO的衍射峰已经几乎不显示,取而代之的是CeO2的衍射峰,且衍射峰并不尖锐。总体来说,随着Ce掺杂量的增加,载体中CeO2与CuO得到组合导致样品的结晶度下降,逐步只显示出CeO2的衍射峰。未观察到RuO2或者Ru金属的衍射峰,可能是Ru物种颗粒小于仪器检测,或者是通过浸渍法较好的均匀分散负载在载体上。
3.2.2. H2-TPR
Ru/CuCex催化剂的H2-TPR如图4所示,Ru/CuO催化剂还原区域为200~500℃,如此较大的氢吸收范围说明不止是活性组分Ru的还原,较高温度的还原峰归因于Ru/CuO中活性组分Ru与载体CuO之间的强相互作用。随着Ce的加入,氢消耗峰逐渐往低温方向移动,且峰面积在减少,说明Ce的加入极大的改变了活性组分与载体的相互作用,从而更容易被还原。Ru/CuCe12在低温区域氢的消耗峰呈现出多峰的趋势,说明低温区域的还原峰为高分散状态Ru物种的还原,可以将其归因于Ru与载体的弱相互作用。
Ru/CuCe50氢的消耗峰在200~350℃,趋于中高温区,说明载体此时主要由CeO2为主导,Ce的大量加入增强了Ru与载体的相互作用。CeO2易于产生氧空位,Zhang等的研究表明:部分还原的CeO2−x可以通过下列反应式传递电子给钌原子表面,从而有利于氮的解离吸附,Ce4+(O2−)2−x (e−)2x + Ru→Ce4+(O2−)2−x + Ru(e−)2x;并且部分还原的CeO2−x表面与钌原子簇的界面上可以形成新的活性中心(SMSI)。
H2-TPR结果表明活性组分与载体之间的相互作用是影响氨分解活性的因素之一。
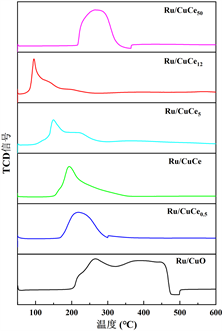
Figure 4. H2-TPR of Ru/CuCex catalyst
图4. Ru/CuCex催化剂的H2-TPR图
3.2.3. NH3-TPD
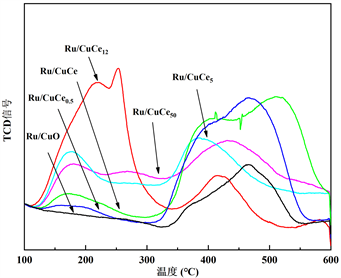
Figure 5. NH3-TPD of Ru/CuCex catalyst
图5. Ru/CuCex催化剂的NH3-TPD
Ru/CuCex催化剂的NH3-TPD如图5所示,NH3作为本反应唯一的反应物,催化剂对其的吸附脱附能力可以直接影响催化剂在反应中的活性。脱附峰的温度代表酸性位点的强弱,脱附峰的面积代表酸性位点的数量。Ru/CuO有一个脱附峰,位于350℃~550℃之间大量的强酸性位点。掺杂Ce后,低温下NH3脱附峰有明显变化,Ru/CuCe5、Ru/CuCe50低温和高温下有中等强度的脱附峰;Ru/CuCe0.5、Ru/CuCe低温下有较小的脱附峰,而高温下脱附峰的峰面积大大增加,说明这两种样品的NH3脱附峰主要位于高温。而Ru/CuCe12主要是低温下的脱附峰显著增加,说明Ce的加入增加了弱酸性位点的密度,而高温下的脱附峰略有下降。脱附量越多,也代表吸附量越多,Ru/CuCe12在低温下的高吸附量使得其在高温下有额外的NH3补充,这可能是其高温下具有高活性的原因。
NH3-TPD结果表明,NH3的吸附量可能是影响氨分解活性的因素之一。
3.2.4. CO2-TPD
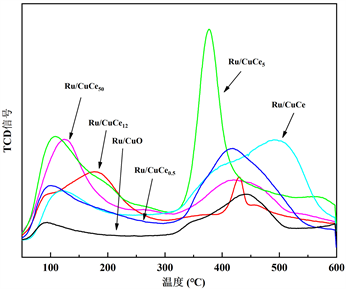
Figure 6. CO2-TPD of Ru/CuCex catalyst
图6. Ru/CuCex催化剂的CO2-TPD图
氨分解催化剂中,催化剂的碱性有利于氨分解,一般来说,碱性越强,催化剂活性越高。脱附温度表示碱性位点的强度,脱附面积表示催化剂表面碱性位点的数量。本文采用CO2-TPD表征催化剂表面碱性位点的分部情况。由图6可知,每个催化剂主要存在三个CO2脱附峰,分别在约100℃、约375℃、约500℃。结果表明,催化剂具有一定数量的弱碱性位点和强碱性位点,对于不同含量的Ce掺杂来说,CO2的脱附是不同的,Ru/CuCe5、Ru/CuCe50在低温下具有较高和较宽面积的脱附峰,说明其弱碱性位点较多,而高温下的脱附峰较低,说明其强碱性位点较少,其氨分解的活性测试也显示相同的趋势;Ru/CuCe5在中高温下具有极高的CO2脱附量,但其活性不是最高,说明中碱性位点的数量对氨分解的活性基本没有什么影响。Ru/CuCe0.5、Ru/CuCe在高温下有较高的脱附量,但其氨分解的活性并不突出,说明强碱性位点在这个体系里并不是影响氨分解活性的主要原因。
CO2-TPD结果表明,碱性位点的数量不是氨分解活性的主要影响因素。
3.2.5. 原位红外
为阐述反应过程中的吸附物种,关键中间物种和反应路径;探究反应过程中的反应机理。本文通过原位红外表征对Ru/CuCe12进行测试。对于催化剂Ru/CuCe12,在100℃下进行NH3吸附,记录不同时间的NH3吸附情况,如图7所示。1210 cm−1处的峰归因于NH3的Lewis acid sites;1360 cm−1处的峰归因于amide (−NH2)的摆动,说明氨分解过程中的中间产物有−NH2生成。1402 cm−1归因于单齿硝酸盐,说明在氨分解过程中有N吸附于催化剂表面的氧上,形成硝酸盐;1463 cm−1处的峰归因于NH3吸附的Brønsted acid sites;1600 cm−1是NH3位于Lewis acid sites上化学吸附的非对称弯曲振动。3152、3314 cm−1处的峰都属于NH3中N-H的伸缩振动。3654 cm−1处的峰归因于O-H的伸缩振动。说明氨脱附的氢可能吸附在催化剂表面的氧上。

Figure 7. In situ DRIFTS diagram of Ru/CuCe12 catalyst with NH3 adsorption time at 100℃
图7. Ru/CuCe12催化剂在100℃下随NH3吸附时间变化的In situ DRIFTS图
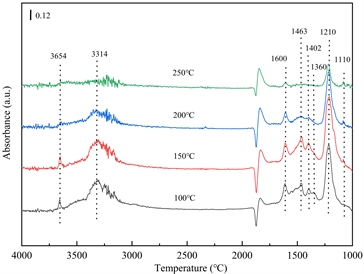
Figure 8. In situ DRIFTS of NH3 adsorption on Ru/CuCe12 catalyst at different temperatures
图8. Ru/CuCe12催化剂不同温度NH3吸附的In situ DRIFTS图
图8是催化剂Ru/CuCe12,在100℃、150℃、200℃、250℃不同温度下的NH3吸附情况。
随着温度的升高一个新峰生成,位于1110 cm−1,将其归属于NH3在Lewis acid sites上的化学吸附。1210 cm−1处的峰归因于NH3的Lewis acid sites。1360 cm−1处的峰归因于amide (−NH2)的摆动,说明氨分解过程中的中间产物有−NH2生成,同时提高反应温度,amide在减少,说明提高反应温度可以促进反应的进行,减少中间产物的生成。1402 cm−1归因于单齿硝酸盐,说明在氨分解过程中有N吸附于催化剂表面的氧上,形成硝酸盐;1463 cm−1处的峰归因于NH3吸附的Brønsted acid sites;1600 cm−1是NH3位于Lewis acid sites上化学吸附的非对称弯曲振动。3152、3314 cm−1处的峰都属于NH3中N-H的伸缩振动。3654 cm−1处的峰归因于O-H的伸缩振动。说明氨脱附的氢吸附在催化剂表面的氧上。
由不同温度的In situ DRIFTS图可以看出,随着温度升高,所有的峰强都在逐渐减小,表明随着温度的升高NH3分解率提高,Brønsted acid sites、Lewis acid sites吸附了H+而逐步减少。Amide (−NH2)随温度升高而减少,说明中间物种减少,氨分解的更彻底了,提高温度有利于氨的分解。
4. 结论
本文通过水热法制备了一系列载体,通过浸渍法进行Ru的负载,制备出了Ru/CuO和Ru/CuCex催化剂。通过比较不同摩尔比的Ce/Cu的催化剂的催化性能,并进行了X射线衍射(XRD)、H2–程序升温还原(TPR)、CO2–程序升温脱附(TPD)、NH3–程序升温脱附(TPD)和原位漫反射红外傅里叶变换光谱(In Situ DRIFTS)进行表征:
1) 活性测试发现Ru/CuCe50在450℃以下表现出最高的氨分解活性;Ru/CuCe12在450℃以上表现出最高的氨分解活性,在600℃、常压条件下,Ru/CuCe12氨分解转化率可以达到99%,高于其他样品。
2) 综合各项表征结果表明Ce的掺杂可以改变Cu的结晶性;Ru/CuCe12催化剂的表面氧更易被还原,部分还原的CeO2−x可以提高对Ru的电子转移,说明Ce的加入能改变活性组分与载体之间的相互作用,而这是影响催化剂氨分解活性的主要因素;同时催化剂Ru/CuCe12在低温下表现出更强的氨吸附能力也可能影响其高温下的催化活性。碱性位点的数量不是影响氨分解活性的主要因素。
3) 原位漫反射红外傅里叶变换光谱结果表明,高温可以促进氨分解反应,减少中间产物amide (−NH2)的生成;在反应过程中氨脱附的氢很有可能吸附在催化剂表面的O上,形成OH;同时一些脱附完的N没有形成N2脱离表面而是吸附在催化剂表面的O上形成硝酸盐,而提高反应温度有利于硝酸盐的减少,促进N2的重组脱附。
4) 综合考虑催化剂活性组分与载体的相互作用和反应温度是影响氨分解催化剂活性的主要因素。