1. 引言
碳化硅颗粒增强铝基复合材料SiCp/Al融合了金属和陶瓷的材料特性,具有高比强度、高比刚度、高耐磨性、高耐腐蚀性、良好的导热导电性能及高抗疲劳性能等特点,在各种领域中被广泛应用,并在航空航天、国防军事以及半导体等行业中具有巨大的应用前景 [1] [2] 。当涉及到SiCp/Al复合材料的加工,由于基体中存在大量的SiC增强颗粒,材料的各向异性和非均质性导致其加工性能较差,加工成本高、精度低和表面粗糙度值大等问题,使得材料加工面临着诸多挑战 [3] [4] [5] 。目前常用的碳化硅铝基复合材料加工方法包括磨削、切削和铣削加工等,其中,磨削是实现材料高效、优质的主流加工方法之一,国内外学者对SiCp/Al复合材料的加工性能进行了丰富的研究。Tao Wang建立了二维微观有限元模型,研究了SiCp/Al复合材料微观的铣削过程中SiC的破碎、脱落、微裂纹是缺陷形成的主要机制 [6] 。Jie Zhang采用Camisizer XT粒度分析装置和随机顺序吸附算法进行了材料的三维微观结构重构,探究了金属基体弹塑性损伤、增强颗粒的脆性破坏和界面的牵引分离的本构行为 [7] 。Junwei Liu建立有限元模型研究了在加工过程中,切削速度和刀具与颗粒的相互作用位置对表面形成的影响。目前大部分研究工作集中在低体积分数铝基复合材料的切削加工中,对于高体积分数铝基复合材料磨削方法的加工研究较少 [8] 。
本文对高体积分数(55%) SiCp/Al复合材料进行仿真模拟以及实验对比,对加工过程中的磨削力、能耗进行评价,讨论了磨削参数对材料失效形式、磨削力的影响。这些研究结果为利用磨削技术实现SiCp/Al复合材料的精密加工、绿色制造提供重要指导。
2. 仿真实验过程
2.1. 有限元仿真模型的建立
本研究使用ABAQUS软件,建立如图1所示的SiCp/Al复合材料以及刀具二维微观有限元模型,对材料进行有限元分析并提取不同加工参数下的磨削力。模型基体材料为Al,尺寸为1 mm × 0.5 mm,基体内离散地分布着SiC增强颗粒,颗粒粒径为40~60 μm四至六边形。磨削过程所用磨粒为三棱锥形金刚石磨粒,研究中忽略磨粒磨损,故在二维模型中将磨粒简化为顶角为50˚的三角形,且定义为解析刚性。仿真过程中,工件X、Y方向的位移被限制,金刚石磨粒以10~100 mm/min的恒定速度沿X方向划擦移动。工件自身的铝基体和碳化硅颗粒始终保持自接触,磨粒会在划擦运动时和工件不同位置产生表面接触。
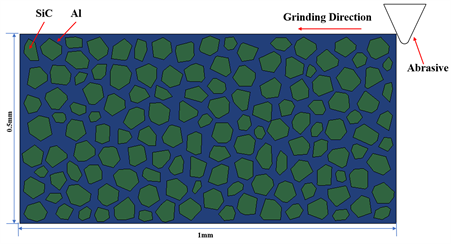
Figure 1. 55% volume fraction SiCp/Al finite element model
图1. 55%体积分数SiCp/Al有限元模型
2.2. 材料本构模型建立
由于SiCp/Al为复合材料,涉及软质铝基体和硬脆性碳化硅颗粒两种材料,二者的物理和力学性能差异较大,具体参数见表1。
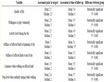
Table 1. Physical and mechanical properties of Al matrix and SiC particles
表1. Al基体和SiC颗粒物理力学性能参数
Al基体由于其较低的杨氏模量,在磨削受力状态下会弹塑性变形,同时磨削过程中会由于机械能的转换和磨粒与材料之间的摩擦,容易产生温升效应。考虑到材料的这些特点,选择描述材料热–弹(粘)塑性关系的本构模型Johnson-Cook [9] 来定义Al基体的力学属性,其本构方程如下式:
(1)
(2)
式中:σ–流动应力(MPa);A–屈服应力(MPa);B–幂指前系数;n–材料硬化系数;c–应变率强化指数;m–温度敏感常数;
–应变率敏感系数(s − 1);
–应变速率(s − 1);ε–应变;θr–环境温度;θm–熔点温度。本文所使用的J-C模型参数如表2所示。
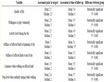
Table 2. Parameters of the Johnson-Cook constitutive model of Al matrix
表2. Al基体Johnson-Cook本构模型参数
选择可以获得磨削过程中的断裂失效行为的JH-2模型 [10] 来作为SiC增强颗粒的本构模型,该模型考虑了裂纹拓展和破碎的过程,此外该模型还考虑了应变率、温度和压力对材料的性能影响。模型标准化无损应力的表达式为:
(3)
标准化破碎应力的表达式为:
(4)
式中:A–初始强度常数;B–断裂强度常数;C–应变速率常数;M–断裂强化指数;N–初始强化指数;T–标准化抗拉强度 破碎材料标准化应力还需要限制为
,选用
可以更好的为模型提供灵活性。本构模型参数如表3所示。
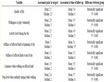
Table 3. Parameters of SiC particle JH-2 constitutive model
表3. SiC颗粒JH-2本构模型参数
2.3. 磨削仿真方案
本模型并不考虑主轴振动,材料本身的不同合成方式以及刀具磨损等因素,只考虑工件的进给速度以及磨粒的磨削深度这两种变量。仿真参数如下表4所示。
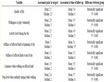
Table 4. Grinding simulation parameters
表4. 磨削仿真参数
2.4. 磨削加工方案
磨削实验所用样品为体积分数约55%的SiCp/Al复合材料,增强SiC颗粒等效粒径为40~60 μm,工件尺寸50 mm × 50 mm × 2.7 mm如图2所示,在德国DMC650V高速立式加工中心(如图3所示)上使用ER25刀柄安装直径为12 mm的电镀金刚石砂轮,砂轮磨粒粒度为400目(38 μm),并采用Kistler测力仪采集磨削过程中的X、Y、Z三轴力信号,磨削加工参数如表5所示。
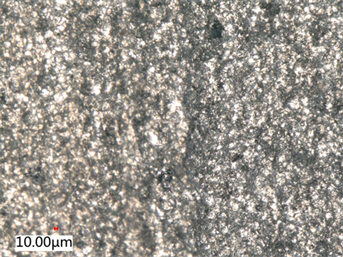
Figure 2. Microstructure of SiCp/Al composite
图2. SiCp/Al复合材料的微观结构
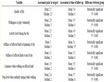
Table 5. Grinding processing parameters
表5. 磨削加工参数
注:*磨削速度1.57 m/s、3.4 m/s、5.23 m/s分别由砂轮直径12 mm和主轴转速3000、6500、10,000 r/min换算得到。
3. 结果与分析
3.1. 有限元仿真结果
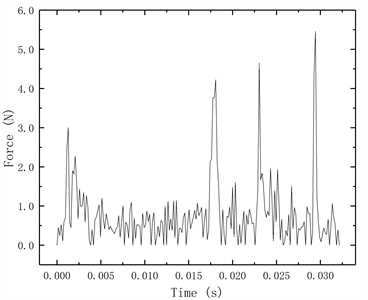
Figure 3. Time sequence diagram of grinding force simulation
图3. 磨削力仿真时序图
通过将金刚石磨粒设置为磨削力采集点,获得每组加工参数时不同的切向与法向磨削力分量,通过数据处理得到总磨削力时序图如图4所示。磨削力随磨削力、进给速度之间的关系如图5所示,当磨削深度一定时,磨削力随着进给速度的增加呈现增加趋势,但在进给速度较小时(vf = 10~30 mm/min)磨削力的上升趋势较为缓慢,这可能是在此进给速度范围下,增强颗粒的失效形式未发生较大变化导致;在中进给速度下(vf = 30~70 mm/min)磨削力上升速度根据不同磨削深度有所变化,但整体趋势向上,这其中可能包括增强颗粒的弹塑性失效转变,从磨削深度和进给速度两方面产生的失效差异性;在vf = 80 mm/min时三种不同磨削深度的磨削力都出现了下降的情况,这可能是由于该进给速度下增强颗粒被拔出现象严重,在仿真过程中,磨粒将会出现不与材料接触的情况;最终在高进给速度(vf = 80~100 mm/min)下磨削力极速上升,可能是由于在此进给速度下,增强颗粒的失效形式累加,导致材料在单位时间内失效加剧。
图6为进给速度60 mm/min,磨削深度为30 μm时的SiCp/Al材料不同磨削时间(接触位置)的工件形貌图。如(图6(a))所示,磨粒在未接触到增强颗粒前,颗粒保持形态完整(红色虚线标注处),最大磨削力出现在增强颗粒靠近磨粒尖端处,此时铝基体在磨粒的进给与压入作用下发生塑性变形(本章设置材料超过变形理论后单元删除)。随着磨粒的进给,磨粒划擦过铝基体接触至界面,此时界面将会收到拉压应力,最终出现界面损伤,将会使增强颗粒暴露出来,最大磨削力出现在增强颗粒的大片区域内(途中红色圆圈标注),这将会是增强颗粒断裂的前兆如(图6(b))。随着磨粒继续进给,界面所受应力超过失效值,铝基体与增强颗粒将会出现界面分离现象,磨粒会与增强颗粒进行接触,增强颗粒的表面被磨粒的锐角处破开裂纹,铝基体也在界面破坏下出现牵连损伤,并在颗粒内部(刀具接触点垂直于颗粒边线上)出现最大磨削力如(图6(c))。最终,当磨粒进给到增强颗粒的中间,裂纹将会沿上述最大磨削力出现位置与刀具顶角连线快速增大,使颗粒从内部破碎直至磨粒离开增强颗粒区域,此时磨削力最大值出现在距离刀具顶角最远处的磨粒边线上(图6(d)),磨粒还将继续与铝基体进行接触,直到下一轮的颗粒失效。
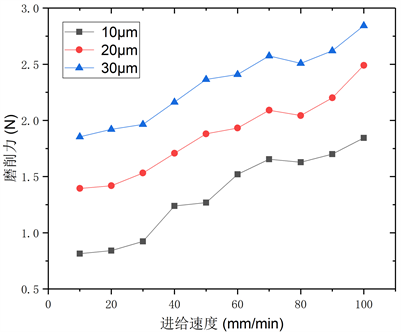
Figure 4. Relationship between grinding force and machining parameters
图4. 磨削力与加工参数的关系
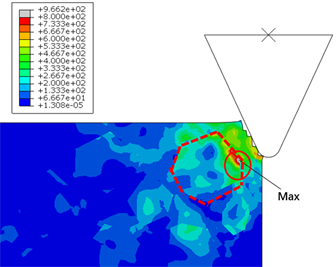
(a) 磨粒接触到增强颗粒前
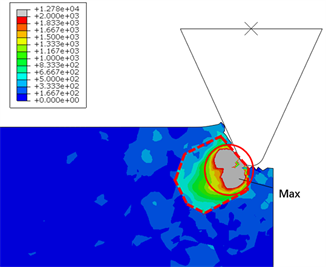
(b) 磨粒与增强颗粒初始接触
(c) 颗粒随裂纹扩大出现内部破碎
(d) 磨粒离开增强颗粒区域
Figure 5. Mixed area of aluminum matrix and reinforced particles removed by abrasive particles
图5. 磨粒去除铝基体和增强颗粒混合区域
3.2. 磨削实验与仿真实验对比
使用表5中的加工参数,对SiCp/Al复合材料进行磨削加工并采取过程中的磨削力,不同磨削参数下的实验结果见表6。
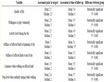
Table 6. Grinding parameters and results
表6. 磨削加工参数及结果
将仿真所得磨削力与实际磨削加工所产生磨削力进行对比,结果如图6所示。结果表明,随磨削深度和进给速度的增加,仿真与实测磨削力均呈现上升趋势,且仿真结果与实测结果误差介于7.7%~15.7%,证明二者吻合度较高,仿真对实际磨削力有参考意义。
通过超景深显微镜(VHX-6000, 600×)观测加工后的表面形貌如图8所示,并记录其表面粗糙度大小见表6。
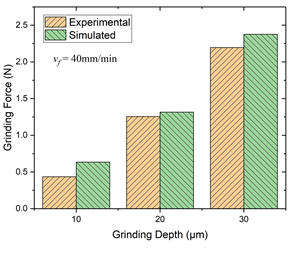
(a) 进给速度对磨削力的影响 (b) 磨削深度对磨削力的影响
Figure 6. Changes of grinding force with processing parameters
图6. 磨削力随加工参数的变化规律
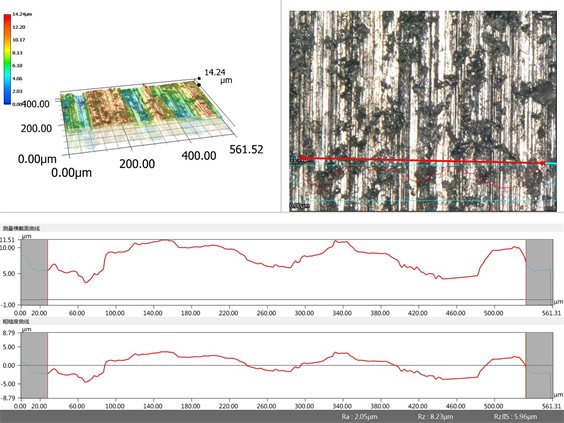
Figure 7. SiCp/Al surface morphology under 3D reconstruction
图7. 三维重构下的SiCp/Al表面形貌
3.3. 磨削参数对磨削能耗的影响
引用传统磨削的比能的经验公式 [11] 如式(5),其中b为磨粒在工件中的去处宽度,ETG是磨削过程中单位体积材料去除的能耗。将上文实验所得数据带入公式,可建立磨削参数与磨削比能与表面粗糙度的双曲线图如图8所示。从图中可得,在相同进给速度和主轴转速下,磨削比能与表面粗糙度随着磨削深度增加而增加(8096.25~10,098 J/mm3);在以进给速度为变量时,磨削比能与进给速度大体呈反比关系,在vf = 40~70 mm/min时磨削比能从8383.12 J/mm3降到了5493.42 J/mm3,在vf = 70~100 mm/min时磨削比能有小幅增加至5732.4 J/mm3,但表面粗糙度在进给速度的增加下逐步增加;在以主轴转速为变量时,磨削比能与主轴转速为正比关系,变化范围为(2721.70~6483.33 J/mm3),粗糙度随着主轴转速的上升而下降。综上,主轴转速的变化对磨削比能的影响最大,其次是进给速度,最后是磨削深度。从绿色制造的角度来看减少磨削深度、主轴转速或增加进给速度可以有效减少磨削过程所需的能耗,更加满足节约能源和绿色制造的要求。结合表面粗糙度来看,使用小磨削深度以及适中的进给速度与主轴转速,可以在获得较优表面粗糙度的同时减少磨削能耗。
(5)
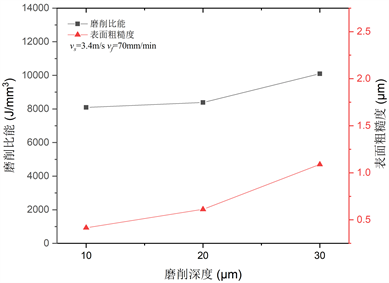
(a) 改变磨削深度
(b) 改变进给速度
(c) 改变主轴转速
Figure 8. Grinding specific energy obtained by different grinding parameters
图8. 不同磨削加工参数得到的磨削比能
4. 结论
结合有限元仿真和磨削比能公式,本研究深入探讨了SiCp/Al复合材料(SiC体积分数为55%,SiC颗粒粒径40~60 μm)在不同磨削参数下的磨削力及其影响因素。仿真结果与实测相符,表明磨削力随磨削深度和进给速度增加而增加。关键影响因素依次为磨削深度、进给速度,主轴转速的影响相对较弱。降低磨削深度、主轴转速,提高进给速度有助于降低表面粗糙度,提升加工质量。磨削比能的变化主要受主轴转速、进给速度和磨削深度的影响,从节能绿色制造的角度考虑,选择适宜参数可有效减少能耗,同时获得优越表面粗糙度。建议在实际应用中选择小磨削深度、较大主轴转速和适中进给速度,以在实现高质量表面加工的同时降低能耗,符合绿色制造要求。
参考文献