1. 引言
X气田投产初期所产天然气其组分中除了含有甲烷、乙烷等常见的烃类,还含有较多的C14、C18、金刚烷、甲基萘、联苯、甲基联苯、二甲基联苯、蒽、菲等重组分,在低温分离过程中易形成固态蜡,导致脱水脱烃装置低温分离器蜡堵 [1] ,严重影响X气田天然气处理系统的正常运行。目前解决天然气处理设备结蜡问题常用的做法包括电伴热法 [1] 、热水洗蜡法 [2] 、蒸汽洗蜡法 [3] 、分子筛吸附法 [4] 、注入凝析油融蜡法 [5] ,基于已有天然气处理设备除蜡方法,许爱华 [6] 等人采用Unim Design和HYSYS软件模拟,通过实验室融蜡试验,发明了一种利用“相似相融”原理,注入凝析油作为融蜡剂吸收天然气中蜡组分的脱蜡工艺,解决了低温分离结蜡的问题。
目前X气田天然气处理厂投产3套脱水脱烃装置,三套脱水脱烃装置均选用在空冷器前加注迪那轻烃融蜡。投产中后期天然气中易形成蜡的重组分含量明显下降,对此处理厂采取了降低凝析油注入量作为降低融蜡成本的措施,但在降低注油基数后总体生产成本仍然较高,为进一步节省物料消耗,降低生产成本,本文通过数据模拟计算及现场论证,从改变凝析油油品、优化装置运行参数、注入凝析油循环利用三个方面进行注油融蜡效果提升的研究。
2. 改变凝析油油品
2.1. 融蜡剂全组分对比分析
目前距离X气田天然气处理厂较近的Z厂在采气及处理过程中每日可分离出10 t左右的凝析油,其油量可满足天然气处理厂一套脱水脱烃装置的融蜡需求,现分析第一套脱水脱烃装置注入Z厂凝析油的可行性,若可行,可大大减少运输成本及购买成本。
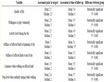
Table 1. Comparison of Dina light hydrocarbons with the whole components of condensate oil from Z plant
表1. 迪那轻烃与Z厂凝析油全组分对比
从组分上分析(表1),迪那轻烃中轻组分C2~C6占比26.65%,Z厂凝析油中轻组分C2~C6占比18.76%。Z厂凝析油中轻组分占比迪那轻烃轻组分低,该部分的回收率较低,绝大部分填补到外输干气中。所以注入Z厂凝析油轻组分的损失可明显降低 [7] 。
Z厂凝析油的有效融剂组分占比65.02%,虽然低于迪那轻烃有效融剂组分占比71.66%,但是融蜡效果具有一定的可行性。
因此,通过组分对比分析,注入Z厂凝析油是可行的,而且可以降低损耗。
2.2. 现场冷冻试验
由于X气田天然气处理厂低温分离温度在−15℃,为保证注Z厂凝析油实验工艺顺利实施,首先应保证注入的油品在该低温工况下不会发生凝固。因此,需首先对Z厂凝析油样品开展冷冻试验,确定该油品能否满足工艺需求。
(a) Z厂凝析油常温样品(b) −17℃冷冻实验
Figure 1. Condensate oil freezing test results of Z plant
图1. Z厂凝析油冷冻试验结果
从图1可看出Z厂凝析油在−17℃时,未出现凝固现象。因此通过室内冷冻实验分析,可以注入Z厂凝析油。
2.3. 工艺模拟软件模拟计算
根据Z厂凝析油组分建立处理厂脱水脱烃装置模拟模型,在原料气空冷器前加注油品,并计算出低温分离器形成蜡的温度 [8] 。
根据原X气田天然气气质组分,空冷器前无轻烃注入时,J-T阀后蜡析出的预测温度为−9.8℃;在空冷器前注入迪那轻烃时,J-T阀后蜡析出的预测温度为−52℃;在空冷器前注入等量的Z厂凝析油时,J-T阀后蜡析出的预测温度为−30℃,注Z厂凝析油及迪那轻烃J-T后析蜡温度均小于−15℃。
因此,通过软件模拟计算,注入Z厂凝析油是可行的。
2.4. 现场试验
在天然气处理厂检修前对第一套脱水脱烃空冷器前注入Z厂凝析油进行试验,实验过程中密切关注生产运行参数,在处理量一定的前提下,如果低温分离器差压有变化,装置处理能力不会受到影响。
取样化验Z厂凝析油水含量及饱和蒸汽压,根据化验结果调整参数至凝析油饱和蒸汽压达标。将处理厂为第一套脱水脱烃装置准备的凝析油储罐液位降至最低,并准备一辆灌满X站凝析油的罐车备用。往第一套脱水脱烃装置的凝析油储罐中灌入80吨Z厂凝析油并取样化验凝析油含水量。调整装置处理量进行试验,具体参数如表2所示:
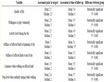
Table 2. Processing parameters of the device adjusted by the test
表2. 试验所调整装置处理参数
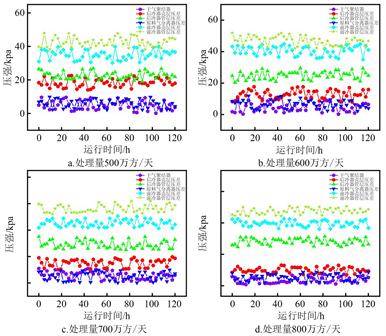
Figure 2. Parameter variation curve of condensate oil in Zhongqiu station under different treatment capacity
图2. 加注Z厂凝析油在不同处理量下参数变化曲线
通过对第一套脱水脱烃装置现场试验,记录关键设备压差变化,与历史设备运行参数比较,如在相同处理量下运行过程中压差上涨超过10 kPa,立即注入备用迪那轻烃。根据记录现场参数压差变化如图2所示。
从图中分析可知,在加注Z厂凝析油时关键设备压差较稳定,没有出现大幅上升或下降,判断此时容器管道内未出现蜡沉积,即注入Z厂凝析油融蜡方案可行。
3. 优化装置运行参数
基于已建HYSYS模型进行模拟计算,发现降低进站压力和提高制冷温度可以降低析蜡点,从而减少凝析油的加注量,因此针对脱水脱烃装置注入迪那轻烃融蜡时,对进站压力以及J-T阀后温度进行分析从而优化注油参数,降低凝析油消耗量 [9] 。目前天然气进站压力为11.23 MPa,处理量为600万方/天,制冷温度为−14.78℃,水露点为−14.33℃。
3.1. 进站压力优化
通过已建模型模拟进站压力对J-T阀前、J-T阀后析蜡温度的影响,具体分析结果如图3所示。从图中分析可知在同一注油量和制冷温度下,随着进站压力的降低,J-T阀后析蜡温度逐渐降低,其部分具体值如表3所示。
基于以上变化规律,J-T阀前以及J-T阀后析蜡温度应该低于现场实际参数−3℃左右。因此,结合站外集输单井管网压力情况,确定降低集气装置进站压力降低至10.9 MPa运行。
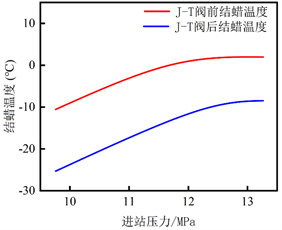
Figure 3. HYSYS simulates the change trend of inlet pressure and wax precipitation temperature after J-T valve
图3. HYSYS模拟进站压力与J-T阀后析蜡温度变化趋势
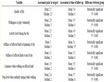
Table 3. Analysis of inlet pressure and wax precipitation temperature before and after J-T valve
表3. 进站压力与J-T阀前、J-T阀后析蜡温度分析
3.2. J-T阀后制冷温度优化
利用已建模型,在同一进站压力、注油、注醇量下,通过HYSYS软件模拟计算J-T阀前、后不同温度对析蜡温度的影响 [10] [11] ,分析结果如表4所示。
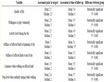
Table 4. Effect of temperature before and after J-T valve on wax precipitation temperature
表4. J-T阀前、后温度对析蜡温度的影响
通过分析发现适当提高J-T阀后温度,析蜡点变化不明显,但可以增加制冷温度与析蜡点之间的差值,在一定程度上可以缓解蜡的沉积,当J-T阀前温度高于8℃时,J-T阀后将发生蜡堵;当J-T阀前温度低于−1℃时,J-T阀前将发生蜡堵;通过表中数据分析得到J-T阀前合理的操作温度范围为1℃~6℃之间。
根据以上模拟结果,调整进站压力在10.9 MPa,J-T阀后温度在−12℃,在此基础上再次模拟注油量对析蜡温度的影响,得到结果如图4所示。
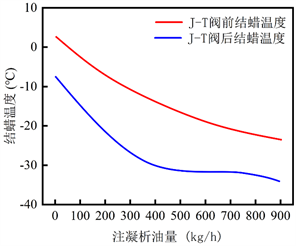
Figure 4. The variation of wax injection amount and wax deposition temperature before and after J-T valve
图4. 蜡剂注入量与J-T阀前后结蜡温度变化规律
通过软件模拟:凝析油加注量在500 Kg/h~700 Kg/h,J-T阀后的结蜡温度始终保持不变,结蜡温度均低于运行温度20℃左右。按照处理量与注油量的关系计算,选择最佳注入量为每83 Kg/百万方。
3.3. 优化参数研究现场试验
在装置检修前1周,选取第二套脱水脱烃装置摸索注油量与处理量关系,开展降低注油量的运行考核,调整参数后,将注油量(X站)从原来每小时99 Kg/百万方逐渐下调至90 Kg、85 Kg、80 Kg、75 Kg四个台阶运行。具体注油量调整计划如表5所示:
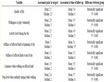
Table 5. Oil injection adjustment plan
表5. 注油量调整计划
应急措施:与一、三套装置对比前后冷器、原料气分离器、低温分离器压差,如果压力在运行过程中上涨超过10 KPa,立即将凝析油加注量提升至每小时90公斤/百万方以上,装置运行状况如图5所示。从图中分析可知当注油量逐渐降低的时候现场能够平稳运行。截止目前,X站注油量在每小时80 Kg/百万方条件下天然气处理站能运行平稳。
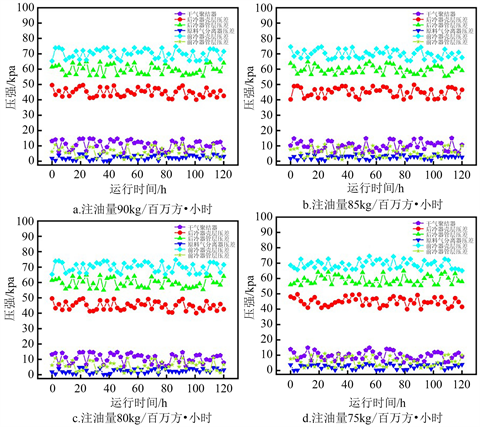
Figure 5. Reducing the change of pressure difference with oil injection after Dina light hydrocarbon injection
图5. 降低迪那轻烃注入后压差随注油量变化情况
4. 注入凝析油循环利用
为进一步节省物料消耗,降低生产成本,现进行回收凝析油循环注入脱水脱烃装置提质增效研究。
4.1. 回收凝析油组分分析
对回收后凝析油进行组分分析,并与迪那轻烃全组分进行对比,如表6所示。
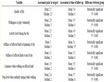
Table 6. Recovery of condensate oil and X station condensate oil component analysis
表6. 回收凝析油与迪那轻烃全组分分析
从全组分上分析,回收凝析油有效组分占比63.02%,迪那轻烃有效组分占比70.56%,但回收的凝析油含有6.88%的金刚烷以及8.36%的萘、联苯、蒽、菲等重组分,从相似相融的角度来判断回收凝析油具有融蜡的效果。
4.2. 回收油品冷冻试验
取生产分离器与原料气分离器液相混合油样和低温分离器、干气聚结器混合油样,以及上述样品的混合油样置于冰箱中长时间观察如图6所示。试验发现生产分离器及原料气分离器混合油样出现凝结,而低温端油样及原料气分离器和低温分离器混合油样在−18℃未出现凝结现象,说明低温端回收凝析油可以循环注入。
4.3. HYSYS模拟理论计算
从低温分离器、干气聚结器分离出的液体经乙二醇装置富液缓冲罐、醇烃液三相分离器后,将油腔分离出来的油进行循环注入分析脱水脱烃单元蜡形成温度。天然气处理量600 × 104 m3/d,进站压力11.23 MPa,原料气分离器温度25℃,低温分离器温度−14℃,乙二醇注入量625 kg/h,轻烃注入量为轻烃补充量为0~50 kg/h。利用已建模型,分析J-T阀后天然气蜡形成温度与补充烃量关系如表7所示。
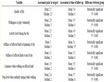
Table 7. Relationship between natural gas wax formation temperature and added hydrocarbon amount in the scheme of oil injection before air cooler and circulation
表7. 在空冷器前注油且循环方案天然气蜡形成温度与补充烃量关系表
分析表中数据可知,当不往流程中补充烃液时,整个流程中凝析油循环烃量为486 kg/h,此时J-T阀前蜡形成温度为−19.3℃,远低于J-T阀前温度,装置管道中不会出现蜡堵现象。同样J-T阀节流后蜡形成温度为−31.5℃,远低于节流温度−14℃,能够避免蜡析出堵塞设备管道。而随着补充烃量的增加,流程中循环烃量增加,J-T阀前后蜡形成温度都小幅度下降。因此可以分析出当将低温分离器分离出的烃液从空冷器前循环注入时,即使不补充烃液也能够融解原料气中的易结蜡组分防止管道装置中出现蜡堵现象。
为了考察将低温分离器产生烃液在空冷器前循环注入时金刚烷、菲、联苯等物质在循环流程中会不会累积在装置中,计算分析原料气分离器以及低温分离器入口气相以及出口气相中金刚烷、菲、联苯等物质的变化情况,结果如表8所示。
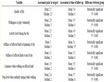
Table 8. Comparison table of wax content of each key point medium injected into the front cycle of raw gas air cooler
表8. 原料气空冷器前循环注入各关键点介质蜡含量对比表
对比表中数据可知,原料气中的金刚烷、菲、联苯等物质在原料气分离器中将大量分离出来,分离器内部没有出现内部累计的过程。
4.4. 凝析油回注现场实验
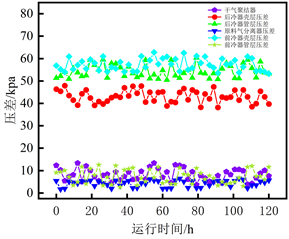
Figure 7. Change of pressure difference of reinjected condensate oil
图7. 回注凝析油压差变化
选择对第一套装置进行凝析油回注,其回注基数为80 kg/百万方小时,日处理量600万方/天。与二、三套装置对比观察前后冷器、原料气分离器、低温分离器压差,如果压力在运行过程中上涨超过10 KPa,则立即注入迪那轻烃。压差对比如图7所示。分析图中结果发现在回收凝析油注入后现场装置能够平稳运行。
5. 结论
通过对目前脱蜡工艺分析,主要从融蜡替代油品分析、注油融蜡参数优化以及注入凝析油循环利用评价三个方面进行提质增效研究,降低注入成本以及降低了凝析油损耗。
方案一,使用Z厂凝析油代替迪那轻烃。Z厂凝析油完全代替第三套脱水脱烃装置迪那轻烃,每百万方注入100 kg/hZ厂凝析油,3#装置处理天然气20亿方/年。
方案二,优化X站油注入量。降低加注量,从99 kg降至83 kg/百万方天然气每小时,处理厂共处理天然气40亿方/年。
方案三,回收凝析油循环注入代替部分迪那轻烃。初步估算回收凝析油回收率能达到16.5%。
根据上文所提出脱水脱烃装置融蜡效果提升研究所提出方案及预期达到的目标,进行经济效益分析。目前迪那轻烃每吨价格为510元,X处理厂距离天然气处理站约170公里,装车运油费约0.432/吨公里;Z厂凝析油不考虑成本,Z厂距天然气处理站约53公里。通过计算得,用Z厂凝析油代替迪那轻烃注入第三套脱水脱烃装置(每年处理量约为20亿方)时节约成本约315万元;优化脱水脱烃装置(每年处理量约为40亿方)参数,降低其注入量时,节约生产成本180万元左右;回收凝析油循环注入代替部分迪那轻烃可以节约成本约150万元。则通过优化脱水脱烃装置脱蜡工艺共计节省645万元。
基金项目
重庆市研究生科研创新项目资助(YKJCX2220102)。