1. 前言
精度是数控机床最重要的技术指标,直接决定了加工产品的质量。影响数控机床的加工精度主要来源于加工时机床的准静态误差和动态误差 [1] 。准静态误差为机床原始误差,在机床在制造和装配过程中,机床母机由于制造精度不足和装配过程中造成的几何误差 [2] ,以及加工过程中主轴升温变形导致的热误差 [3] 。动态误差相对于静态误差而提出,关于机床动态误差,国内外学者做了大量研究,目前依然没有关于动态误差严格准确的定义 [4] 。
数控机床误差测量方法有很多,大致可分为两种:1) 通过精密仪器测量机床的误差,2) 通过测试工件检测机床的加工精度 [5] 。
常用的测量仪器主要有:激光干涉仪 [6] 、球杆仪 [7] 、平面光栅 [8] 、R-test装置 [9] 等。采用激光干涉仪、干涉镜和平面反射镜组合测量方法,其光路调节是一个耗时的工作,且操作人员需熟练掌握机床几何误差相关知识。球杆仪可通过简单的圆轨测试,能快速有效的测量机床运动中相当于参考长度的变化量,但其无法直接得到单一误差,会遗漏一些误差源信息,难以实现机床精度高效和自动化检测。平面光栅的检测局限在平面上,无法得到五轴联动切削过程中的空间误差。R-test兼具检测精度高和检测效率高的优点,其较球杆仪器成本高,不易获取,难安装。上述误差测量方法都是在机床静止或低速空载情况下完成的,未考虑机床在实际加工过程中的动态误差,均具有一定的局限性。
基于上述精密仪器测量机床误差的不足之处,考虑由于切削力、进给速度及加速度等因素变化,引起的机床结构变形及振动等实际切削情况,切削测试工件无疑是一种较好检验机床实际加工精度的方法。常见的典型测试工件,如ISO10791-7试件,四角锥台和圆锥台试件,NCG2004和NAS979标准件等经典试件 [10] ,以及中国“S”形检验试件 [11] 。切削试件虽然能够更精准地反映机床的加工精度,但刀具误差、伺服误差、机床振动等多种因素耦合在试件的加工误差中,仅反映机床整体加工性能,无法准确获取单一轴误差源。因此学者们设计了不同的特征试件,这些设计的特征试件不同特征是在不同加工模式下切削而成,能将机床的整体加工误差分解成单一轴或较少轴的加工误差。在某一特定加工模式下,切削得到的特征只对一个轴或较少轴的一个或较少项误差元素敏感,因此可比较该特征的实际加工尺寸与理论尺寸来辨识该特征所对应加工轴的几何误差。常见的试件特征有:孔 [12] 、槽 [13] 、阶梯 [14] 、圆弧 [15] 等,也有将这些单一特征进行合成一体的组合特征工件 [16] 。
以上基于特征工件测量机床误差的方法中,虽然考虑到使用单一轴或较少轴在特定模式下切削不同特征,避免耦合,但未将影响机床的动态误差和准静态误差进行分离。因此,为从根本上提高机床加工精度,既考虑到从单一轴或较少轴切削不同几何特征,避免误差耦合、难以辨识的问题,又考虑将影响机床加工精度的准静态误差和切削过程中的动态误差进行分离,提出了基于切削特征工件辨识与分离机床动态误差和准静态误差的方法,旨在精确高效测量机床误差。
2. 特征工件设计
本文在一台型号为JDGR400AC双转台五轴数控机床上开展实验。该机床工作台尺寸500 × 300 mm,X/Y/Z轴行程885/800/500 mm,A轴转动范围−120˚~30˚,C轴转动范围−180˚~180˚。
特征工件的设计思路:工件所包含的特征能充分地辨识五轴数控机床所有的误差。其中平动轴有21项几何误差,旋转轴有8项位置无关误差(PIGEs)和12项位置有关误差(PDGEs)。此外,特征工件的尺寸应可能给覆盖机床实际加工过程中常用加工区间。
根据该机床的具体结构、实际的加工区间以及五轴数控机床加工的工艺特点,本文设计一个包含阶梯、斜面、圆锥和圆柱等特征的工件,如图1所示。该工件由200.00 × 200.00 mm × 10.00 mm、160.00 mm × 160.00 mm × 10.00 mm两个长方体,长宽均为120.00 mm、坡度为10˚的楔体,底面半径为40.00 mm、圆锥角为30˚、倾斜10˚的圆锥以及底面半径为25.00 mm、高度为10.00 mm、倾斜10˚的圆柱组成。根据特征工件包含的不同特征,本文能辨识五轴数控机床平动轴、旋转轴若干项误差,如图2、图3所示。图2、图3中误差符号所对应的名称如表1所示。如图4所示,在辨识准静态误差的同时,也能分离出动态误差。
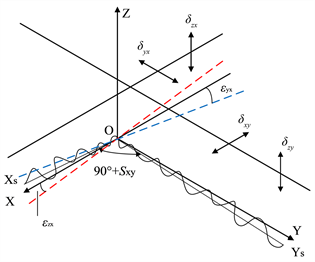
Figure 2. Schematic diagram of translational axis error
图2. 平动轴误差示意图
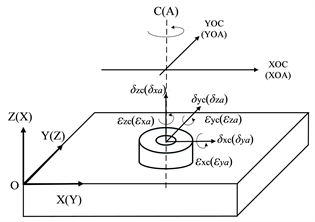
Figure 3. Schematic diagram of rotary axis error
图3. 旋转轴误差示意图
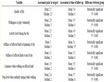
Table 1. 15 geometric errors based on feature artifact separation and identification
表1. 基于特征工件分离与辨识的15项几何误差
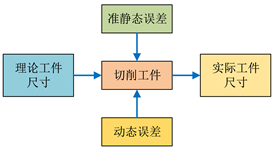
Figure 4. Dynamic and static errors affecting the machining accuracy of machine tools
图4. 影响机床加工精度的动静态误差
3. 误差辨识与分离原理
3.1. 构建特征映射关系
通常情况下,特征工件的加工特征受多误差元素综合影响,为同时辨识出准静态误差和动态误差,所设计的特征应包含尽可能少的误差元素。在切削特征工件过程中,不同特征的切削由数控机床单一轴加工完成,因此,通过采集并处理不同特征上的数据点,能辨识数控机床所对应的加工轴若干项误差。
根据以上所述,建立工件特征与所对应加工轴的误差映射关系。如图5所示,阶梯槽和斜面特征包含平动轴的定位误差、直线度误差、垂直度误差和角度误差。利用旋转轴旋转切削而成的圆柱面和圆锥面能分别反映A、C轴轴线的位置偏差和倾角偏差。
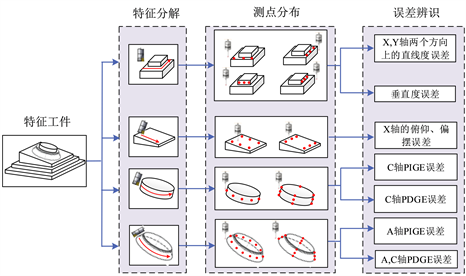
Figure 5. Relationship between feature and error mapping
图5. 特征与误差映射关系图
3.2. 误差辨识原理
根据工件特征映射关系,将实际切削工件分解成若干典型子特征,如阶梯、圆柱、圆锥台和斜面。基于子特征的加工误差,辨识子特征所对应的几何误差,分离影响机床加工精度的准静态误差和动态误差。
3.2.1. 平动轴误差的辨识
平动轴误差主要包括:直线度误差、垂直度误差和角度误差。在此对平动轴误差的辨识过程作详细说明:
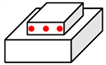
① 直线度误差辨识:以X轴为例,选取如上图所示测量点数据,分析在Y和Z方向上的误差值,即可得到X轴在Y和Z向上的直线度误差;类似地,可以得到Y轴在X和Z方向上的直线度误差。
如图6所示,机床X、Y轴方向的滚珠丝杆安装过程不是垂直的,导致切削过程中,在XOY平面存在垂直度误差。
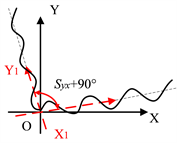
Figure 6. X-axis relative to Y-axis perpendicularity error
图6. X轴相对于Y轴垂直度误差
② 垂直度误差辨识:同时将X轴在Y方向、Y轴在X方向上的测量点拟合成一条直线,根据两条拟合直线的夹角即可得到垂直度误差。
如图7所示,Y轴安装在X轴之上,当X轴存在绕着Z轴转动的偏摆误差
时,仅有当Y轴运动时,机床在X方向上会产生
角度误差。当X轴存在绕着Y轴转动的俯仰误差
时,仅有当Y轴运动时,机床在X方向上会产生
角度误差。
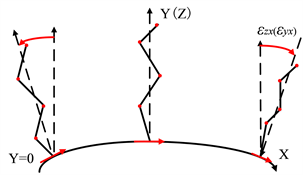
Figure 7. Influence of X-axis deflection and pitching errors on Y-axis motion
图7. X轴偏摆、俯仰误差对Y轴运动的影响
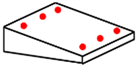
③ 俯仰、偏摆误差辨识:以X轴为例,X轴的俯仰误差会对Y轴的运动产生在Z方向上的偏差
;X轴的偏摆误差会对Y轴的运动产生X方向上的偏差
。如上图所示,在不同X位置分别测量Y轴运动点在Z和X方向上的误差并拟合得到斜率值,即为X轴在不同位置处的俯仰和偏摆误差。
3.2.2. 旋转轴误差的辨识
两个旋转轴共有8项PIGE和12项PDGE,在此对旋转轴的若干项误差辨识过程作详细说明:
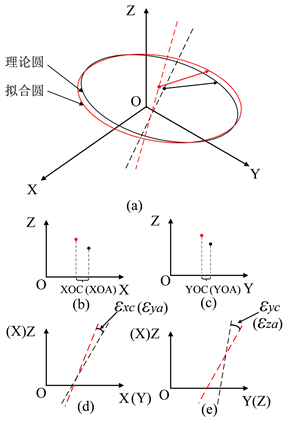
Figure 8. A, C-axis error principle diagram
图8. A、C轴误差原理图
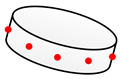
① 圆柱面的测点:保持所有平动轴和A轴倾斜10˚且静止,仅C轴转动切削圆柱面。如上图对圆柱面进行测量并对数据进行圆拟合,确定圆柱面的圆心位置。如图8所示,对比理论圆心位置和实际位置,确定C轴轴线X和Y方向的位置偏差。同时,根据拟合圆所在平面的法向量与理论圆平面的法向量进行比较,即可得到C轴轴线X和Y方向的倾角误差。
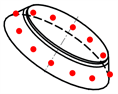
② 圆锥台测点:由于圆锥台沿母线倾斜15˚,切削需要五轴联动。为了避免其他四轴的干扰,本文仅能通过圆锥特征辨识A轴的4项误差。如图8所示,对圆锥台的外圆测点进行圆拟合,确定其圆心在X和Y方向上的偏距,从而辨识A轴轴线在X和Y方向上的位置偏差。另外,根据拟合圆所在平面的法向量与理论圆平面的法向量进行比较,即可得到A轴轴线X和Y方向的倾角误差。
3.3. 误差分离原理
如图9所示,特征工件在加工完成后,通过三坐标测量机上进行测量标定,测量得到的尺寸即为工件的实际尺寸,记为x1。特征工件加工完成后,工件继续装夹在机床夹具上,保证测头测量的基准点和基准平面与切削时一致。在机测量过程中,机床处于低速无载荷的工况,由于机床本身在制造、装配过程存在误差,导轨的运动不能达到预定位置,测头无法准确测量机床的实际尺寸,主要是由机床的准静态误差造成。如图9所示,测头在机测量测得工件的尺寸为x2。工件的理论尺寸记为x0。显然,特征工件加工后经三坐标测量机标定,三坐标测量机标定值与特征工件理论值即切削过程中的总误差
。特征工件经三坐标标定后,可以当作一个标准试件,将其置于机床上,通过测头测量,准静态误差的存在导致测头测得工件尺寸与其实际尺寸存在偏差
。由于测量过程机场处于低速无载荷,而切削过程,存在因切削力改变引起的振动等各种动态因素造成的动态误差。在已知总误差和准静态误差的情况下,可分离将动态误差。
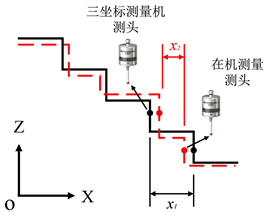
Figure 9. Schematic diagram of error separation
图9. 误差分离示意图
需要解释的是,理论推导过程中,特征工件先三坐标测量机标定后在机测量。而实际实验中,为了保证在机测量过程中的参考点和参考面的一致性,先在机测量后三坐标测量机标定。
基于特征工件的动静态误差分离流程如图10所示。首先切削特征工件,工件在机测量和三坐标测量机标定;然后处理两组数据,三坐标测量机标定值与特征工件理论尺寸值之差即为机床总误差;三坐标测量机标定值与特征工件在机测量值之差即为准静态误差。最后机床动态误差为总误差与准静态误差之间的差值。
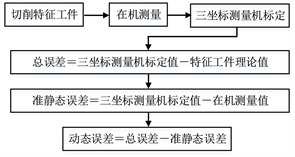
Figure 10. Flowchart of dynamic and static error separation based on characteristic artifact features
图10. 基于特征工件特征的动静态误差分离流程图
3.3.1. 直线度误差分离原理
本节以X轴在Y方向上直线度误差为例阐述直线度误差分离的方法。
如图11所示,工件切削完成后,在不拆卸特征工件的情况下,将机床刀具卸下,在主轴上安装测头并校准,测头测量X轴在Y方向上直线度误差测量分布点。
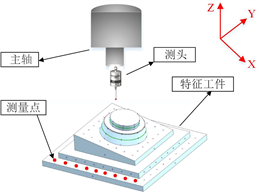
Figure 11. Straightness error measured on-machine
图11. 直线度误差在机测量
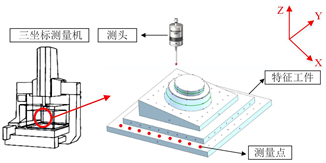
Figure 12. Straightness error CMM calibration
图12. 直线度误差三坐标测量机标定
特征工件在机测量过程中,测头所测数据记为
。以X轴在Y方向上直线度误差待测起始点为基准点,计算后续每个测点数据与基准点数据的差值。
(1)
如图12所示,三坐标测量机测量点与在机测量测量点保持一致,测头所测数据记为
。类似地,以起始测点为基准点,计算后续每个测点与基准点之差。
(2)
理想情况下,直线度误差为0,则加工的工件表面光滑平整。但实际中,工件尺寸起伏不平,则三坐标测量机测量的偏差量为工件的总误差E。
(3)
三轴数控机床平动轴的准静态误差E1,即为:
(4)
因此,切削过程中的动态误差E2,即为:
(5)
3.3.2. 垂直度误差分离原理
通过测量X轴在Y方向上的直线度误差测量点和Y轴在X方向上的误差测量点,可以辨识与分离得到Y轴相对于X轴的垂直度误差。
首先特征工件完成后,特征工件在机测量。测头测量如图13所示测量点(xi yi zi) (
),然后将图中两个不同方向上的点中X坐标、Y坐标分别拟合,最后得到斜率记为
、
。则通过在机测量得到两直线的夹角记为
:
(6)
特征工件取下,通过三坐标测量机进行测量。类似地,测头测量如图14所示测量点(xi yi zi) (
),然后将图中两个不同方向上的点中X坐标、Y坐标分别拟合,最后得到斜率记为
、
。则通过三坐标测量机测量得到两直线的夹角记为
:
(7)
理想状态下,X轴与Y轴的夹角为90˚。在切削过程中,辨识得到Y轴相对于X轴的垂直度误差
:
(8)
则分离得到的静态误差记为:
(9)
则分离得到的动态误差记为
:
(10)
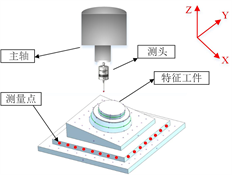
Figure 13. On-machine measurement of verticality error
图13. 垂直度误差在机测量
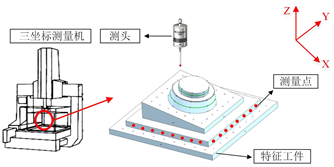
Figure 14. Perpendicularity error CMM calibration
图14. 垂直度误差三坐标测量机标定
3.3.3. 角度误差分离原理
本节以X轴绕Z轴转动的偏摆误差为例进行阐述。
如图15所示,特征工件切削完成后,进行在机测量,测头测量如图所示斜面上的测量点(xi yi zi) (
)。将三维坐标中的Y坐标、X坐标进行直线拟合,得到斜率记为
,则拟合得到的直线夹角即为:
(11)
如图16所示,将特征工件取下,在三坐标机测量机上进行标定,同样地,将三维坐标中的Y坐标、X坐标进行直线拟合,得到斜率记为
,则拟合得到的直线夹角,由于三坐标测量机的测量精度高于三轴数控机床加工精度一个数量级,测得的数据可以认为是特征工件的实际数据,则其实际夹角为;
(12)
理想情况下的
、
均为0,则切削过程中,X轴绕Z轴转动的总偏摆误差
即为三坐标测量机测量点拟合得到的夹角:
(13)
则准静态误差
:
(14)
则分离得到的动态误差
:
(15)
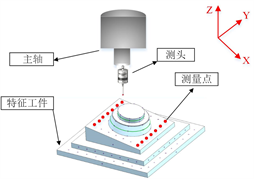
Figure 15. Angular error in machine measurement
图15. 角度误差在机测量
3.3.4. C轴误差分离原理
这里以C轴轴线在X轴方向的位置偏差和倾角误差进行阐述。
如图17所示,特征工件切削完成后,测头测量如图所示圆柱侧面待测点,将圆柱测点进行空间圆拟合,得到圆心O1(x1 y1 z1)以及法向量n1(i1j1k1)。
如图18所示,在机测量完成后,将特征工件放置在三坐标测量机上进行标定,测头测量如图所示点,保证与在机测量时的点一致。将得到的测点数据进行空间圆拟合,得到圆心O2(x2 y2 z2)以及法向量n2(i2j2k2)。
如图18所示,本文将圆柱理论的圆心和圆心所在平面的法向量分别记为O0(x0 y0 z0)和n0(i0j0k0)。
C轴轴线在X轴方向的位置总偏差E:
(16)
C轴轴线在X轴方向的准静态误差E1:
(17)
则分离得到动态误差为E2:
(18)
C轴轴线在X轴方向的倾角总偏差E0:
(19)
C轴轴线在X轴方向的准静态误差
:
(20)
则分离得到动态误差为:
(21)
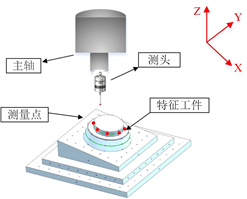
Figure 17. On-machine measurement of a cylindrical measuring point
图17. 圆柱测点在机测量

Figure 18. Cylindrical measuring point CMM calibration
图18. 圆柱测点三坐标测量机标定
3.3.5. A轴误差分离原理
这里以A轴轴线在X轴方向的位置偏差和倾角误差进行阐述。
如图19所示,特征工件切削完成后,测头测量如图所示圆柱侧面待测点,将圆柱测点进行空间圆拟合,得到圆心P1(x1 y1 z1)以及法向量m1(i1j1k1)。
如图19所示,在机测量完成后,将特征工件放置在三坐标测量机上进行标定,测头测量如图所示点,保证与在机测量时的点一致。将得到的测点数据进行空间圆拟合,得到圆心P2(x2 y2 z2)以及法向量m2(i2j2k2)。
如图20所示,本文将圆柱理论的圆心和圆心所在平面的法向量分别记为P0(x0 y0 z0)和m0(i0j0k0)。
A轴轴线在X轴方向的位置总偏差E:
(22)
A轴轴线在X轴方向的准静态误差E1:
(23)
则分离得到动态误差为E2:
(24)
A轴轴线在X轴方向的倾角总偏差E0:
(25)
A轴轴线在X轴方向的准静态误差
:
(26)
则分离得到动态误差为
:
(27)
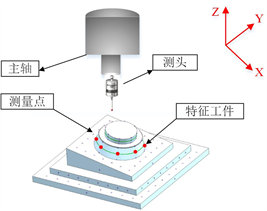
Figure 20. On-machine measurement of conical measuring points
图20. 圆锥测点在机测量
4. 实验内容
4.1. 特征工件加工
准备200.00 mm × 200.00 mm × 80.00 mm铝合金原材料,经去毛刺、打磨、清洗后装夹到机床工作平台。根据特征工件的工艺要求和设计尺寸,将三维模型导入到CAM软件中,生成数控加工NC代码,将NC代码优化并导入到数控系统。如图21所示,首先切除多余的材料(粗加工),最后在JDGR400五轴数控铣床进行半精加工和精加工。
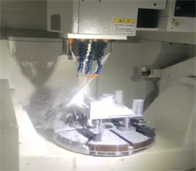
Figure 21. Cutting process of feature workpiece
图21. 特征工件切削过程
4.2. 在机测量
特征工件切削完成后,在不拆卸的情形下进行在机测量。如图22所示,首先完成特征工件待测点测量顺序的规划,然后将雷尼绍OMP600测头安装在主轴上,如图22所示,按照规定的路径,测头依次触碰特征工件待测点,测量得到的数据通过无线信号传送,收集并整理数据。
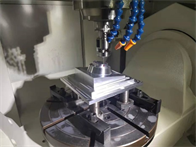
Figure 22. On-machine measurement process of feature workpiece
图22. 特征工件在机测量过程
4.3. 三坐标测量机标定
如图23所示,在机测量完成后,取下特征工件放置在ZEISS三坐标测量机上进行测量。三坐标测量机测头依次测量如图23测量点,保证特征工件在三坐标测量机上测量时的参考系、待测点与在机测量一致。如图23所示,测头依次触碰特征工件待测点,采集得到的数据保存在三坐标测量机专用软件中。
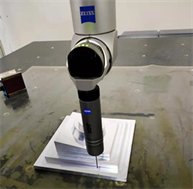
Figure 23. CMM calibration process for feature workpiece
图23. 特征工件三坐标测量机标定过程
4.4. 实验结果
根据上述误差分离与辨识原理,将在机测量数据、三坐标测量机标定数据以及特征工件理论数据代入公式中,辨识得到平动轴、旋转轴的15项误差。同时将误差进行分离,得到15项误差所对应的总误差、准静态误差、动态误差,如图24、表2、表3所示。
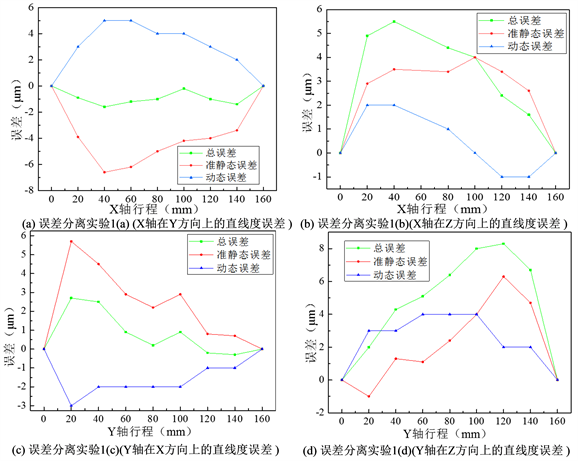
Figure 24. X, Y axis straightness error dynamic and static separation
图24. X、Y轴直线度误差动静态分离
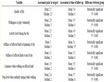
Table 2. 6 position-dependent errors dynamic and static separation
表2. 6项与位置有关误差动静态分离
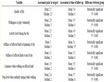
Table 3. 5 terms of position-independent error kinematic separation
表3. 5项与位置无关误差动静态分离
从图24、表2、表3,可以得出:
1) 由实验1(a) (b) (c) (d)可以得到,动态误差与总误差走势基本一致,由此可见,在切削工件表面时,动态误差是影响工件表面精度的主要因素。
2) 由图24和表2、表3,可以看出,相对于X、Y轴方向,Z轴方向加工精度受动态误差变化更大。
3) 由表2可知,X轴的俯仰误差对Y轴运动在Z方向上产生的加工误差普遍小于X轴的偏摆误差对Y轴运动在X轴方向产生的加工误差。
4) 根据加工工艺的过程以及处理的结果综合分析,动态误差的大小与刀具和工件相对位置变化有关,进刀和退刀过程中,刀具受到非均匀切削力,动态误差变化较大;稳定切削过程中,刀具受到均匀切削力,动态误差变化较小。
5) 根据实验4、5数据结果分析,动态误差大小有正有负,方向不固定,说明旋转轴受切削时动态误差的影响更加明显。
5. 实验验证
为了验证辨识和分离测量误差数控机床误差的准确性,本文在同样的AC双转台五轴机床上进行验证实验。将上述辨识与分离得到的误差项导入到空间误差模型中,求解五轴机床在切削过程中的刀具路径下的刀尖相对于工件的位置误差和方向误差,将误差补偿到的新NC代码中,最后通过相同的工艺、补偿后的NC代码加工同样的特征工件。补偿前后的特征工件如图25(a)、图25(b)所示。
(a) 补偿前 (b) 补偿后
Figure 25. Comparison before and after feature workpiece compensation
图25. 特征工件补偿前后对比图
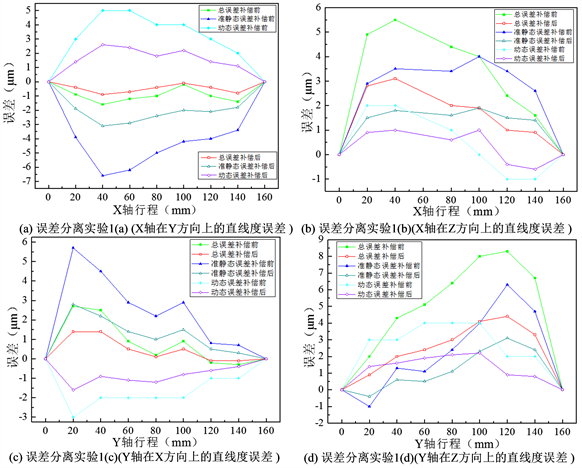
Figure 26. X, Y axis straightness error compensation before and after
图26. X、Y轴直线度误差补偿前后
如图26,X、Y轴直线度误差,补偿前后数据,通过公式计算:
(28)
其中,xi表示补偿后的数据,x表示补偿前的数据,n表示测点的个数。
经计算,如表4、表5所示,计算出基于特征工件分离得到的X轴在Y方向直线度误差总误差的补偿率为50.54%,准静态误差的补偿率为50.96%,动态误差的补偿率为50.23%;X轴在Z方向直线度误差总误差补偿率为49.27%,准静态误差的补偿率为50.72%,动态误差的补偿率为49.00%;Y轴在X方向直线度误差总误差补偿率为49.73%,准静态误差的补偿率为50.16%,动态误差的补偿率为49.52%;Y轴在Z方向直线度误差总误差补偿率为51.58%,准静态误差的补偿率为52.11%,动态误差的补偿率为51.43%。
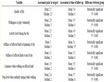
Table 4. Before and after compensation of 6 position-related errors
表4. 6项与位置有关误差补偿前后
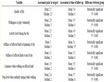
Table 5. Before and after compensation of 5 position-independent errors
表5. 5项与位置无关误差补偿前后
根据以上计算结果,补偿后的特征工件精度提高约50%,证明了本文研究方法的可靠性。此外,在辨识与分离准静态误差的同时,得到能真实反映机床实际切削情况的动态误差,大大提高误差测量效率,保证了本方法测量的高效性。
6. 结论与展望
本文针对目前大多数机床误差直接和间接测量方法是在机床空载无实际加工的情况下完成的,只能反映机床空载下的运动精度而非加工精度,提出一种基于设计和加工特征工件,在机测量和三坐标测量机标定,辨识和分离影响机床加工精度动静态误差的方法。与以往测量数控机床误差方法相比较,误差测量效率进一步提升,为机床误差测量提供了新参考。从特征工件设计的角度出发,设计的特征工件能全部反映出三轴数控机床的21项几何误差、五轴数控机床旋转轴8项PIGEs和12项PDGEs,这将是本文研究方法继续拓展的重要方向。