摘要: 在分析铸件结构特点的基础上,使用传统经验公式对盖板的压铸工艺进行设计,同时使用CAE (Computer Aided Engineering)软件对铸件进行数值模拟。模拟结果表明,初始工艺中铸件的部分位置缩松、缩孔现象严重且存在冷隔现象。生产试模结果与初始工艺数值模拟结果基本一致,初始压铸工艺无法满足生产要求。依据试模和数值模拟结果对初始压铸工艺进行改进,添加并改变了溢流槽的尺寸和位置,改空冷为水冷。对改进后的压铸工艺进行数值分析和生产试模,缩松、缩孔和冷隔现象得到大幅改善,满足生产质量要求。
Abstract:
On the basis of analyzing the structural characteristics of the casting, traditional empirical formulas were used to design the die-casting process of the cover plate, and CAE (Computer Aided Engineer-ing) software was used to numerically simulate the casting. The simulation results show that some parts of the casting designed in the initial plan have serious shrinkage, shrinkage cavities and flow marks. The production trial mold results are basically consistent with the initial process numerical simulation results, and the initial die-casting process cannot meet production requirements. Based on the trial mold and numerical simulation results, the initial die-casting process was improved, the size and position of the overflow groove were added and changed, and air cooling was changed to water cooling. Numerical analysis and production test molds were conducted on the improved die-casting process. The phenomena of shrinkage porosity, shrinkage holes and flow marks were greatly improved, meeting production quality requirements.
1. 引言
当前制造业的发展方向为低排放和轻量化,传统的制造工艺和材料已经不能够满足其发展要求。高压压铸作为特种铸造,具有表面光洁度高与尺寸精度优良的特点,在现代生产制造中得到了快速发展 [1] 。压铸铝合金具有比强度高、良好的耐腐蚀、导电导热等性能,被广泛应用于汽车、通讯电子和航天航空领域 [2] 。陈苏坚 [3] 通过使用SPSS软件对材料性能参数进行分析,逆向分析出材料各元素占比,获得力学性能优异的压铸铝合金。传统压铸工艺改进主要为试错法,成本高,周期长且效率低。引入计算机模拟技术,可以根据数值模拟结果进行缺陷预测并进行工艺改进,降低生产成本,缩短生产周期,提高生产效率 [4] [5] 。Zhang [6] 通过使用ProCAST对铸件充型和凝固进行了模拟研究,开发出一种具有较高学术价值的优化算法。因此,本文主要对盖板压铸工艺进行设计,采用CAE软件进行数值模拟,通过改善冷却系统,添加和改变溢流槽的尺寸和位置进行压铸工艺优化。
2. 铸件结构和材料
本文以盖板为研究对象,三维模型如图1所示,外形尺寸为296 mm × 121 mm × 85 mm,平均壁厚4.19 mm,最大壁厚为12.61 mm,其结构对称分布。盖板材料为ADC12,各化学元素所占质量百分数如表1所示,通过DTA测得试验用ADC12铝合金的液相线温度及固相线温度为592℃和539℃。
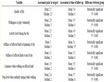
Table 1. Chemical composition of ADC12 aluminum alloy w (%)
表1. ADC12铝合金的化学成分w (%)
3. 压铸工艺设计
3.1. 确定分型面
铸件主体为壳形,底部为梯形,但局部存在镂空,上方壳形难以开模。考虑铸件结构特点和最大投影面原则,同时为了简化模具,将分型面设置在最大投影面上,分型面如图2所示 [7] 。
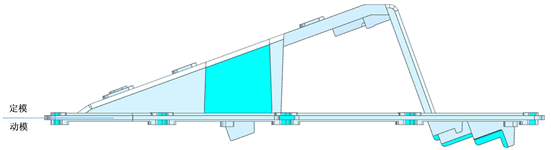
Figure 2. Schematic diagram of the location of the parting surface
图2. 分型面位置示意图
3.2. 浇注系统和排溢系统的设计
浇注系统采用两段流道进料,将内浇口设置于铸件短边位置,减少铝液填充时间,避免生产时出现卷气、冷隔、熔接痕等缺陷。铝液填充铸件行程较长且铸件壁厚不均匀,为防止液流的前锋冷料浇入铸件型腔,在横浇道两侧安置冷料穴容纳冷料。该铸件内浇口截面积90 mm2,取直径为Φ70 mm的活塞。采用集渣效果明显的梯形溢流槽对前端冷污金属、金属液回流和涡流进行收集,减少因浇注系统设计不足带来的压铸缺陷。浇排系统见图3,表2为浇排系统工艺参数。
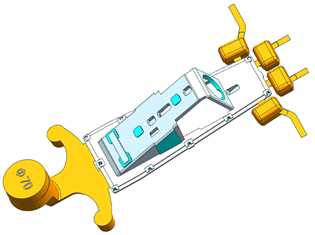
Figure 3. 3D drawing of die casting with gating system
图3. 带有浇排系统的压铸件三维图
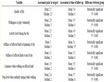
Table 2. Pouring and overflow system parameters
表2. 浇排系统参数
4. 数值模拟结果与分析
在压铸工艺数值模拟中,模具材料选择H13模具钢;设置压铸工艺参数为:浇注温度680℃,模具预热温度200℃,充填速度为45 m/s。冷却介质设置为空气。
4.1. 充型过程模拟
使用CAE软件对铸件压铸工艺进行模拟,充型结果如图4所示。从模拟结果可以看出,金属液首先进入直浇道,在t = 0.1424 s时,金属液从直浇道进入横浇道;在t = 0.1783 s时,金属液进入横浇道后,液流前锋冷料流入两侧冷料穴,后续金属液通过内浇口进入铸件型腔;在t = 0.3123 s时,前端金属液对铸件充填超过一半,并通过两侧筋条和上方筋板对铸件后端进行充填;在t = 0.3156 s时,两侧筋条的金属液到达前端并开始回流,上方筋板的金属液分成两股金属液对铸件前端进行充填;在t = 0.3176 s,金属液在铸件前端完成汇流;在t = 0.3287 s时,金属液充填完毕,型腔被全部充填,无充填空缺。从整个充型过程来看,金属液充型过程不平稳,存在一定程度的飞溅;金属液汇流在铸件内部,可能会出现冷隔,缩松缩孔等缺陷;溢流槽数量和位置存在不合理的地方,在汇流金属液充型处未设置溢流槽。
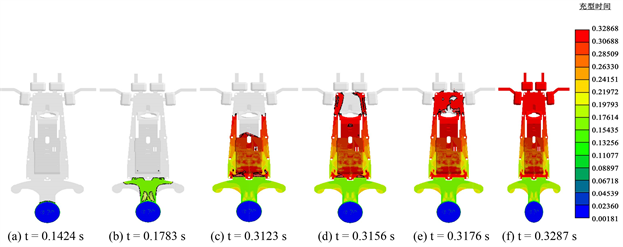
Figure 4. Simulation results of casting filling process
图4. 铸件充型过程模拟结果
4.2. 凝固过程分析
通过模拟软件可以查看并分析铸件凝固顺序和凝固过程中是否存在孤立液相区,有助于我们对缩松、缩孔等缺陷的预测,铸件凝固过程如图5所示。从图5(a)可以看出,金属液最先在铸件边缘开始凝固。在图5(b)中,随着温度进一步降低,铸件型腔内部开始凝固。在图5(c)中,铸件主体大部分已经凝固,铸件前端及铸件顶部出现孤立液相区,且该位置的金属液补缩通道已关闭,无法得到有效的补缩,可能会出现缩松缩孔等缺陷。图5(d)中,铸件顶部和前端的孤立液相区特征进一步明显。
4.3. 缺陷预测
根据凝固过程分析,认为在铸件顶部会出现缩松、缩孔缺陷。图6为模拟软件对铸件出现缩松、缩孔缺陷的预测图,a和b为具体缺陷位置分布,缺陷主要出现在铸件顶端和铸件前端,该位置容易产生热节,为铸件最后凝固区域,导致该部分孤立液相区无法得到有效补缩产生缩松、缩孔缺陷。根据充型过程分析,充型金属液在铸件前端汇流,该处未设置溢流槽,易出现冷隔缺陷。采用初始铸造工艺进行生产试铸实验,对铸件进行检测,实际缺陷位置与模拟结果的缺陷位置基本一样,证实了初始铸造工艺模拟结果的可靠性。
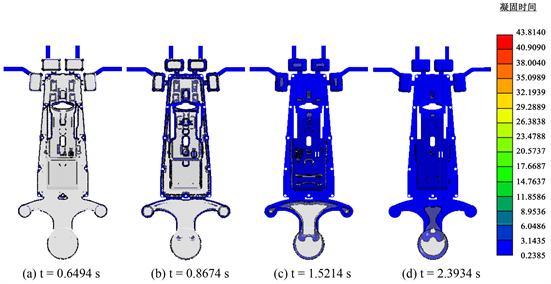
Figure 5. Simulation results of casting solidification process
图5. 铸件凝固过程模拟结果
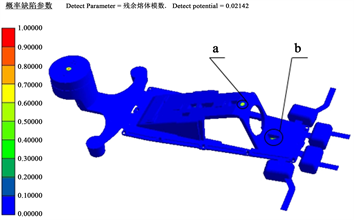
Figure 6. Initial scheme defect distribution
图6. 初始方案缺陷分布
5. 铸造工艺方案优化
5.1. 工艺优化措施
针对铸件顶端和前端易产生热节,出现孤立液相区的现象,优化压铸的冷却系统,使用水冷代替空冷,控制进口水温为25℃。针对铸件前端产生的缩松、缩孔及冷隔问题,在铸件圆环处添加一个溢流槽,使金属液最后汇流在溢流槽内,加强浇排系统的集渣能力。优化方案见图7。
5.2. 工艺优化验证
对初始工艺优化后再次采用CAE软件进行模拟,结果见图8。调整冷却方式后,铸件前端和顶端热节情况得到改善,金属液均匀凝固,未产生孤立液相区,缩松、缩孔等现象得到大幅改善;圆环处增加溢流槽,避免出现因金属液在铸件内部汇流而导致的冷隔现象。图9为试模零件,经检验符合生产质量要求。
1. 内浇口冷却水路;2. 铸件底部水路;3. 溢流槽;4. 铸件顶端水路
Figure 7. Process solution optimization diagram
图7. 工艺优化方案图

Figure 8. Defect distribution of optimization plan
图8. 优化方案缺陷分布
6. 结语
本文利用数值模拟软件对压铸件进行了一定的改进优化,通过充型、凝固顺序以及概率缺陷参数判断设计工艺可能存在的问题。结合模流分析增设溢流槽及冷却系统的再设计进行工艺优化,重新进行模拟得到最终的优化工艺。通过试生产验证了优化的合理性和准确性,表明具有实际的应用价值,但由于时间和条件的限制仍然存在许多不足。主要有以下两个方面:
1) 本文只对铸件充型和凝固顺序进行了探究,后续可以对铸件金属结晶和模具热应力进行分析,探究其对铸件质量的影响。
2) 本文主要针对铸件结构以及冷却进行研究,对于压铸工艺参数并没有深入探究,后续可以对压铸工艺参数进行一定的研究。