1. 引言
釜式反应器作为搅拌反应器的一种常见类型,在生物、医药、冶金、环保和化工等领域被广泛使用 [1] [2] [3] [4] [5] 。为了提高反应器内气液两相流体间的混合效果,一些学者做了一些研究,如韩晨 [6] 等通过气含率分布图、液相流线图分析了转速对气液两相流动特性的影响。白锦军 [7] 等通过数值模拟发现流体介质的黏度越大,反应器内混合效果越差。程亮等 [8] 通过数值模拟发现在高粘度的搅拌介质中,桨叶的循环能力弱,槽内容易出现死区、分层等现象,不利于流体间的快速混合。
由于高粘度液体黏度较大,停留时间长,流体流动性差,所以一般要通过一些手段来加快气液两相流的混合进程。合理地选用和设计搅拌布气装置,对提高装置内混合效果和反应效率具有十分重要的意义。叶立 [9] [10] 等通过在釜式搅拌反应器底部加装气体分布器,构建泰勒涡釜式搅拌反应器,发现经过气体分布器的诱导作用,能够在反应器内产生泰勒涡流,在临界旋转雷诺数工况下可使反应器气相均布性提升28%,溶氧速率提升5倍左右,有效地改善了反应器内流动状况,强化了气液间的传质效率,但是叶立等在进行气液两相研究的过程中,多以低粘度介质水为流体介质,并未涉及到高粘度介质的研究。
本文在此基础上,用甘油作为高粘度介质流体,以水作为低粘度介质流体作为对比,采用数值模拟和实验相结合的方法,探究不同介质下,反应器内流动及气液相间混合的影响,为高粘度介质在泰勒涡釜式搅拌反应器内的工业应用提供了理论基础。
2. 数值模拟
2.1. 几何模型
如图1所示,为简化后的泰勒涡釜式搅拌反应器三维模型,通过Solidworks软件进行三维建模,模型的尺寸参数与实验装置一致,具体参数如表1所示。本文研究的泰勒涡釜式搅拌反应器装有五直叶搅拌桨,底部装有气体分布器,气体分布器由一个半球形的集气盒、三个倾斜程度为30˚的喷嘴和三个静态混合器组成,气体经集气盒进入,经喷嘴进入静态混合器,通过混合器的旋转作用,气体被打碎成小泡成旋流进入反应器中。

Figure 1. Three-dimensional model of Taylor vortex stirring reactor
图1. 泰勒涡釜式搅拌反应器三维模型
2.2. 网格划分及无关性验证
利用Fluent Meshing对反应器进行网格划分,由于反应器中搅拌桨及气体分布器等结构相对复杂,采用结构化网格无法达到离散化的需求,因此对流体区域进行离散化处理时采用非结构化六面体网格。对桨叶和气体分布器区域进行加密,边界层生成方式选择uniform,层数设置为10,第一层网格的厚度设为0.01 mm,增长速率为1.2。选取325,346、693,835和914,523,1,593,471四种网格尺寸对比研究网格数量对数值模拟的影响。
选取一条X = 0.06 m,Y = 0 m,Z = 0.6~1.15 m的轴向线,记录该直线上轴向速度随高度增加的变化,来分析网格数量对流速的影响。如图2所示为不同网格数量下轴向速度随轴向高度的变化,由图2可以看出在网格数达到914,523时,网格数量增大,速度变化的趋势趋于一致,差异性较小,可见此时网格数量适中。因此,结合模拟的耗时与精确性,选择网格总数为914,523进行数值模拟,网格细节如图3所示。

Figure 2. The axial velocity varies with the axial height for different mesh numbers
图2. 不同网格数量下轴向速度随轴向高度的变化
2.3. 模型设置及求解
研究对象为多相流,求解器设置为压力修正算法(Pressure-Based),本文为气液两相流,具有较高的复杂性,使用SIMPLE算法进行求解。操作压强设为101,325 Pa,考虑到重力作用,在Z轴负方向设定重力加速度为9.81 m/s2。
物理模型选择Multiphase多相流模型中的Eulerian模型,离散格式选择隐式,湍流模型选择标准k-ɛ模型,壁面函数选择标准表面函数。其连续性方程及动量方程如下式:
连续性方程:
(1)
动量方程:
(2)
式中:
-速度矢量在
三个方向的速度分量,
-
三个方向受到的粘性应力;
为密度,t为时间,p为压力,
-x轴方向、y轴方向、z轴方向的体积力。
分别选取甘油和水作为主相液相物料,以空气为次相气相物料,具体参数设置如表2所示。设定平均气泡直径为1.5 mm,气液相间的曳力模型选择grace模型,表面张力系数设置为0.073 N/m。气液相间物质传递原理采用双膜理论。在泰勒涡釜式搅拌反应器中加入示踪剂来求得停留时间分布密度函数。示踪剂在搅拌过程中浓度变化的组分质量守恒方程:
(3)
式中:
是为示踪剂的浓度,mg/L,
是示踪剂的密度,kg/m3,
是示踪剂在反应器中的扩散系数。
采用多重参考系法(MRF) [11] ,将整个计算域分为两个部分,采用两套坐标系,搅拌桨及三个静态分布器扫过的动区域采用旋转坐标系,其余区域采用静止坐标系,动静区域相互分离,通过坐标系的旋转代替桨和静态分布器的旋转。
将泰勒涡釜式搅拌反应器底部气体分布器进料口设置为质量流量入口,入口仅为气相进入,参数设置为0.00102 kg/s,反应器顶部设置为出气边界,只允许气体溢出。叶片旋转域、静态分布器旋转域与其余流体域交界面设置为接触面(interface),将反应器釜壁设置为普通壁面条件(wall),无滑移边界,搅拌轴设置为普通壁面(wall),且为旋转壁面(moving wall)。泰勒涡釜式搅拌反应器的边界条件具体设定如图4所示。
设置初始条件为反应器内布满液体,以连续性残差曲线收敛标准低于10−4、浓度残差曲线低于10−5时,认定此时计算收敛。当稳态工况收敛后,改成瞬态计算,以稳态计算的结果作为瞬态计算的初始条件,注入2%质量浓度的硫酸铜水溶液,通入量为2 ml,同时在出口处每隔10 s取样一次,取样量不变,从示踪剂通入开始,到250 s停止取样。
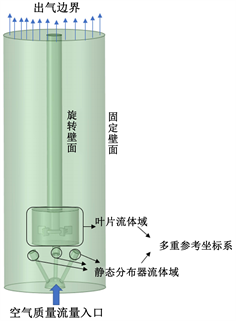
Figure 4. Taylor vortex stirred reactor
图4. 泰勒涡釜式搅拌反应器
3. 模拟结果与分析
3.1. 不同介质下泰勒涡流对流场的影响
选取反应器y = 0截面右侧进行流场研究,图5和图6分别是以水和甘油为流体介质,不同搅拌转速下泰勒涡流的流态演变图,当搅拌转速为150 rpm时,水和甘油流场率先在上方形成小型涡核,这是因为流场顶部是自由液面,反应器内的气液流体在该面上产生了速度梯度,触发了端壁效应,相较于搅拌轴旋转对流体粒子施加的离心力给予的线速度而言,端壁效应占据粒子速度内的主导作用。其中水为介质的情况下,在搅拌桨上方流线是从中部径向分裂成两股不同旋转方向的涡流,并且率先在250 rpm的搅拌转速下形成满涡结构的泰勒涡,而以甘油为介质的情况下,反应器搅拌桨上方流体流线呈现出轴向分布,并在550 rpm的搅拌转速下形成了满涡结构的泰勒涡,对比二者形成的满涡泰勒涡可知,水流场内只形成一个完整的且规整的泰勒涡胞,其结构具有不稳定性,而甘油流场内形成的多对泰勒涡胞,数量多、分布均匀,且大小相似、形状规则,满涡结构具有较强的稳定性。继续增加搅拌转速,水和甘油流场内的涡胞逐渐破裂、合并,流动状态向着波状流发展,如在搅拌转速为750 rpm时,水流场内主流区域的大型涡线扩展至整个区域,而甘油流场上方还留有少量的不规则涡胞,这是由于甘油的黏度远大于水,对流体粒子而言,不同于水介质,甘油介质下粘滞力相比惯性力对粒子的影响占据主导作用,所以反应器上部分流体主要仍受制于粘性力。
3.2. 不同介质下泰勒涡流对气含率的影响
气含率是用来评判气液两相混合效果的一个重要指标 [12] 。图7和图8分别是以水和甘油为介质,不同搅拌转速下流场内的气含率云图。如图7,在搅拌转速为250 rpm时,水流场上方满涡结构对应的气含率在3%~6%,气相分布占比达到70%左右,气含率分布梯度小,随着搅拌转速的增加,水流场顶部泰勒涡发生变化,向着波状泰勒涡发展,这时水流场顶部所对应的气含率在3%~6%占比减小至7%左右,气含率分布梯度大,且主要集中在搅拌轴附近,说明在生成泰勒涡胞的前提下,满涡规则的泰勒涡能够
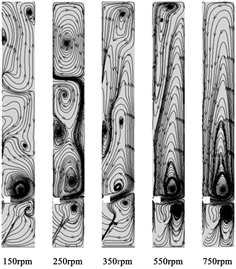
Figure 5. Water as the medium, the right section of y = 0 in the reactor at different stirring speeds
图5. 水为介质,不同搅拌转速下反应器内y = 0右侧截面流线图
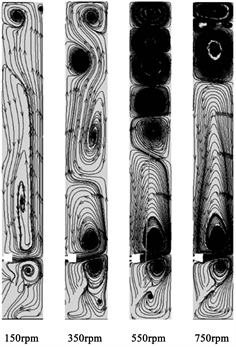
Figure 6. Streamline diagram of the right section of y = 0 in the reactor with glycerol as the medium and different stirring speeds
图6. 甘油为介质,不同搅拌转速下反应器内y = 0右侧截面流线图
促进气相分布和气相的均匀性,增强气液相间的传质。如图8,在搅拌转速为550 rpm时,甘油流场此时为满涡泰勒涡结构,相比较于其它搅拌转速,此时满涡泰勒涡所对应的流场虽然具有较强的气相均匀性,但98%区域内的气含率却低于3%,接近为0,由此得出泰勒涡抑制气相的分布,减弱气液相间传质。
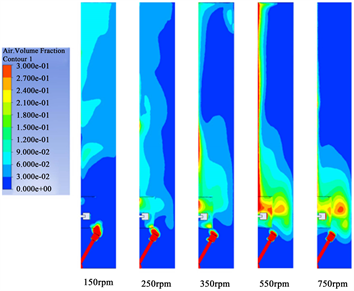
Figure 7. Contour diagram of gas saplance in the right section of y = 0 in the reactor with water as the medium and different stirring speeds
图7. 水为介质,不同搅拌转速下反应器内y = 0右侧截面气含率云图
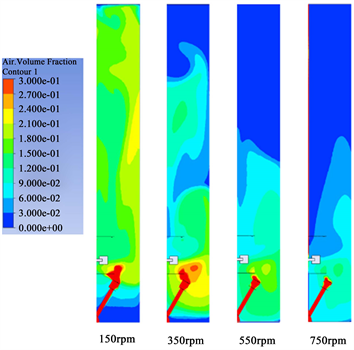
Figure 8. Glycerol is the medium, and the gas content contour of the right section of y = 0 in the reactor at different stirring speeds
图8. 甘油为介质,不同搅拌转速下反应器内y = 0右侧截面气含率云图
3.3. 甘油介质下泰勒涡流对速度分布的影响
在反应器y = 0右侧截面上选择三条轴向线,分别为r1 = 45 mm,r2 = 107.5 mm,r3 = 170 mm,进行轴向上甘油速度的研究,在反应器y = 0截面上选取三条径向线,分别为h1 = 500 mm,h2 = 800 mm,h3 = 1100 mm,进行径向上甘油速度的研究。图9和图10为不同搅拌转速下,不同轴向距离和不同径向距离下三条线上甘油速度曲线图。
如图9(a)所示,在搅拌转速为150 rpm时,此时流场内未形成泰勒涡,在轴向高度大于0.3 m时,三条轴向线上的甘油速度呈现出速度交叉分布的趋势,随着搅拌转速的提升,泰勒涡逐渐生成、满涡至破裂、合并为波状泰勒涡,如图9(b)~(d)所示,在轴向高度大于0.3 m时,三条轴向线上的速度分布出现分层分级现象,甘油速度曲线并无交叉,特别是在搅拌转速为550 rpm时,如图9(c),此时轴向高度大于0.6 m的部分为满涡泰勒涡胞,此时三条轴向线上的甘油速度呈现出类似于正弦周期曲线的变化规律。
如图10(a)所示,在搅拌转速为150 rpm时,此时流场内未形成泰勒涡,不同高度的三条径向线上的甘油速度相互交叉,随着搅拌转速的提升,泰勒涡逐渐形成、满涡至破裂、合并为波状泰勒涡,如图10(b)~(d)所示,由搅拌轴至壁面附近,甘油速度整体呈现减小趋势,且搅拌轴附近甘油速度减小速率远大于壁面附近。由图10(c)可知,在搅拌转速为550 rpm时,轴向高度大于0.6 m的部分为满涡泰勒涡胞,h1 = 500 mm的径向线区域没有形成泰勒涡胞,受到搅拌桨的影响,甘油速度相对较高,此时平均甘油速度为0.49 m/s,而h2 = 800 mm和h3 = 1100 mm的径向线都属于满涡泰勒涡的区域中,所对应的平均甘油速度分别为0.39 m/s和0.37 m/s,速度均匀性提高了20.5%,这说明同样形成泰勒涡的区域内,流体粒子的整体速度很少再受到高度的影响,泰勒涡之间速度基本一致,所以泰勒涡能促进不同高度处的速度均布,提高反应器的反应稳定性。

Figure 9. Glycerol velocity on three axial lines at different axial distances of y = 0 cross-section at different stirring speeds
图9. 不同搅拌转速下,y = 0截面不同轴向距离下三条轴向线上的甘油速度
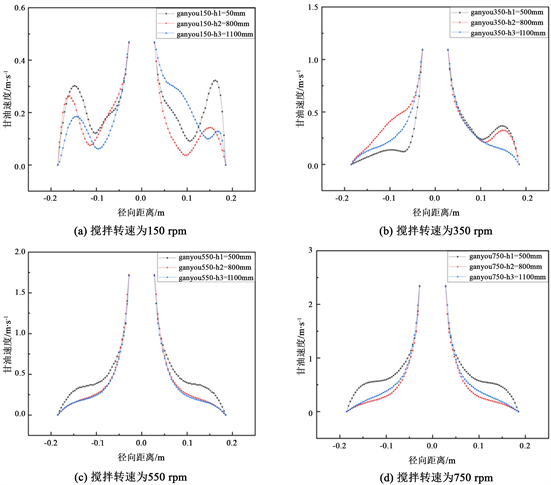
Figure 10. Glycerol velocity on three radial lines with different radial distances of y = 0 section at different stirring speeds
图10. 不同搅拌转速下,y = 0截面不同径向距离下三条径向线上的甘油速度
4. 实验装置与步骤
4.1. 实验装置
图11为实验装置的示意图,主要是由搅拌装置、釜式反应器、布气系统组成。搅拌装置的主要部件为三相异步电机,搅拌桨与转轴在联轴器的带动下进行旋转,选用圆盘涡轮式五平直叶搅拌桨,不锈钢圆筒与不锈钢封头相互连接构成了反应器的主体部分,不锈钢圆筒的尺寸为Φ370×1150 mm,布气系统由通气管、集气盒、喷嘴以及肯尼斯静态混合器组成。
4.2. 实验步骤
打开总电源开关,打开阀门,将100 L甘油加入泰勒涡釜式搅拌反应器中,启动电机,调节搅拌仪器的转速至实验设计值550 rpm。开启涡流泵,将空气的通入量设置为0.00102 kg/s,待反应器中流动稳定后,在入口处注射2%浓度的硫酸铜水溶液,通入量为2 ml,同时在出口处每隔10 s取样一次,取样量不变,从示踪剂通入开始,到250 s停止取样。甘油在强碱环境下会二价铜会发生络合,采用浓度比色分析法对取出的样品进行比色分析,确定样品的吸光度值(波长为630 nm),当样品的吸光率趋于0时认定为测试结束。根据式(4)可计算停留时间分布密度。
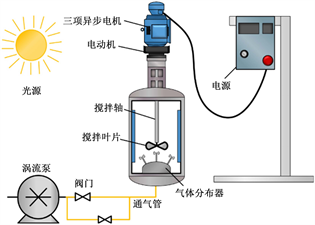
Figure 11. Schematic diagram of the experimental setup
图11. 实验装置示意图
(4)
式中:
是取样浓度,mg/L,t是取样时间,s。
4.3. 实验结果与模拟结果对比分析
图12为模拟和实验得出的停留时间分布密度曲线对比。
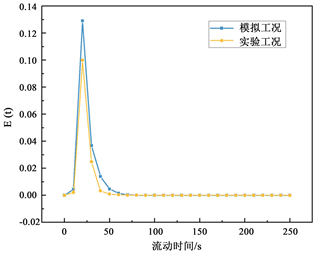
Figure 12. Comparison of dwell time distribution density curves
图12. 停留时间分布密度曲线对比图
由图可知,模拟工况和实验工况的停留时间分布密度曲线变化趋势差距不大,均在20 s左右出现峰值,此时的误差最大为7.6%,模拟工况的峰值略大于实验工况的,原因是由于少量示踪剂在随流体运动时吸附在反应器的内壁面上。随着实验的推进,模拟工况和实验工况的停留时间分布密度曲线差距逐渐变小,误差降低至2.8%以内,模拟工况和实验工况的停留时间分布密度数据值接近,验证了数值模型的正确性。
5. 结论
以泰勒涡釜式搅拌反应器为模型,采用数值模拟与实验相结合的方法,对比分析了不同介质分别在不同搅拌转速下,反应器内泰勒涡流对流场及气含率的影响,并探究了高粘度介质在不同搅拌转速下,反应器内生成的泰勒涡流对速度分布的影响,由此得出以下结论:
1) 在低粘度介质的流场内,能在250 rpm的转速下,快速地形成满涡泰勒涡,但只能形成数量极少、完整且规整的泰勒涡胞,且容易失稳,满涡结构仅能在较窄的转速范围内维持稳定。在高粘度介质的流场内,在550 rpm形成的满涡泰勒涡胞具有数量多、分布均匀、大小相似、形状规则等特点,满涡结构能够在较宽的转速范围内维持稳定。
2) 在低粘度介质的流场内,泰勒涡能增强气液相间传质,同时促进气相均布性。在高粘度介质的流场内泰勒涡能够抑制气液相间传质。
3) 泰勒涡能够使得轴向上的甘油速度分布出现分层分级现象,且满涡泰勒涡对应的轴向甘油速度具有类似正弦的周期变化规律。通过分析不同高度径向上的甘油速度分布,得出泰勒涡能使速度均匀性提高20.5%,增强反应器内的反应稳定性。
4) 模拟工况和实验工况得到的停留时间分布曲线变化趋势一致,模拟数据和实验数据之间的最大误差不超过7.6%,验证了数值模型的正确性。
基金项目
国家自然科学基金重点资助项目(51736007),国家自然科学基金资助项目(51306122)。
NOTES
*通讯作者。