1. 引言
当前原油输送大多采用长输管道密闭输送 [1] ,杨开玖在其文章中指出,管道输送工艺技术解决了上述问题输油设计中存在外部依托条件差、油源分散、进油点及出油点均较多和进油量不确定等问题 [2] ;而罗塘湖在其文章中结合国情客观地分析了我们在密闭输送、液环输送、优化运行、管道保温技术、原油热处理及常温输送、化学助剂、乳化和磁处理等原油管输工艺技术的研究和进展情况 [3] ,充分展示了长输管道密闭输送的优势。随后学者对其进行安全可靠性及自动化相关的研究,刘鑫在介绍实施原油全密闭输送需要解决的工艺技术和问题的基础上,详细讨论了油气长输管道密闭输送的安全技术 [4] ;董有智对原油全密闭输送工艺进行了简要分析,并对其安全措施做了探讨,为提升原油输送工作安全性研究提供参考意见 [5] ;余光辉在轮–库–鄯原油管道的自动控制中采用以计算机为核心的数据采集和监控系统(SCADA),该系统在乌鲁木齐调度控制中心可对全线进行监控、调度和管理 [6] ;尤立华通过SCADA系统在原油管道实际运行中的运用,实现了对该管道的自动控制与远程监控,提高了管道运行的自动化管理水平 [7] ;针对长输管道密闭输送中存在的问题,学者们也有所研究。张大安等对如油量损耗、压力波动大、腐蚀、结蜡、摩阻增加等问题,分析并得出解决对策 [8] ;刘波等从原油长输管道密闭输送中常见的问题以及解决措施两个方面进行了分析探讨 [9] ;吕根群等分析了长输管道原油密闭输送中存在的问题,指出了原油输送过程中降低油气损耗、消化原油结蜡、缓解压力波动、降低摩阻等问题的解决方法 [10] 。
关于密闭输送原油管道控制原理相关的研究国内外都比较少。目前大多数指导密闭输送管道的控制原理为设计单位编写,设计单位在建立管道建模型时的沿线参数通常是以查询资料的方式获得对应参数,且该模型所得控制原理均为理论所得,缺乏现场实际运行情况验证,故很有必要建立新的模型对控制原理进行验证(上述标红为回答问题1、引言需要增加国内外针对密闭输送原油管道控制原理方面的现状及存在问题的调研)。本文基于某密闭输送原油长输管道,应用仿真软件对其进行建模,并以其近几年的实际运行数据对控制原理进行逐一验证与修订。研究方向为控制原理的可靠性和该密闭输送原油管道的超前保护设置的可靠性。超前保护的原理是在产生水击时,由管道控制中心迅速向上、下游泵站发出指令,上、下游泵站立即采取相应保护动作,产生一个与传来得水击压力波相反的扰动,两波相遇后,抵消部分水击压力波,以避免对管道造成危害 [11] [12] [13] 。
2. 研究介绍
SPS仿真软件能对管道输送的单一流体、单相混合流体或批次流体进行仿真。SPS软件从INPREP文本文件获得管道信息,包括物理元件的所有信息 [14] 。SPS软件不但能仿真大多数管线的正常运行工况,并能仿真控制管道事故工况,诸如管线断裂、设备故障等。SPS软件可计算管道沿线流量、压力、密度、温度等参数,并能以图形或报表的形式输出 [15] 。
SPS软件的仿真功能可以通过两种形式实现,通过控制序列运行或交互式(运行过程中可以改变边界条件)运行,初始状态可以是零流量状态、已储存的稳定状态或者用户自定义稳定状态 [16] 。
某密闭输送原油长输管道有4个泵站(A、B、C、D),1座分输站(E)和1座末站(F),设计输量为1300 × 104 t/a。由于首站有15万方储罐,故该密闭管道为一单独的水利系统,可该原油管道利用SPS仿真软件建模进行定性研究。
该原油管道已经累积约五年的运行数据,可供进行其控制原理的可靠性验证工作。基于该管线清管所得中线成果数据,利用SPS模拟软件建立模型。结合该管道近几年运行数据,逐一对初步设计中的控制原理进行校核,以验证控制原理的可靠性并对存在的缺陷提出相应改进建议。
本文中选择的油品为STQ油,在设计输量下研究控制原理和超前保护设置的可靠性。表1为该原油管线稳态的运行参数。
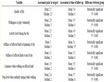
Table 1. Study on steady-state operating parameters of crude oil pipelines (1300 × 104 t/a)
表1. 研究原油管线的稳态运行参数(1300 × 104 t/a)
3. 研究内容
3.1. 控制原理可靠性研究
基于表1,依次模拟初设中的所有故障触发的超前保护程序。模拟故障包括甩泵、进出站ESD阀门故障关断、监控阀室故障关断。现针对上述三种故障,依次选取一个进行控制原理可靠性分析。
例一:D站甩泵故障工况
控制原理如下:
1) 停运C站1台外输主泵;同时将C出站调节阀设定值改为10.9 MPa,将AL末站进站减压阀设定值改为4.22 MPa;
2) 在(1)执行后60 s,将B泵站出站调节阀设定值改为12.7 MPa;
3) 在(2)执行后30 s,停运A泵站1台输油主泵,并将A泵站出站调节阀设定值改为7.45 MP;
4) 程序自动处理完成。
结论:D泵站输油泵停运,60 s内采取以上控制程序后,管道降量输送,输量为1390 m3/h。
将上述控制逻辑编入文本,将表1稳态作为初始状态并设定某一时刻出发D站甩泵故障工况,随后调用控制逻辑。
模拟结果显示:C站的泄压罐会出现满罐的情况。
通过分析原因,在全线降量输送后,C站的进站压力大于该点的水击泄压阀触发值,造成该处泄压阀为常开状态。故该控制原理是存在缺陷的,需要立刻进行修正。
经过多次模拟得出该故障工况下可靠地控制原理如下:
1) 停运A泵站所有给油泵和输油主泵,同时停运B泵站、C泵站和D泵站的所有外输主泵;
2) 在(1)执行后60 s,将F末站进站减压阀设为0开度,并关闭减压阀上下游的截断阀;
3) 将全线所有泵站出站调节阀设为0开度,并关闭调节阀上下游的截断阀;
4) 程序自动处理完成。
需要在故障后30 s内启动上述控制逻辑,可保障该故障工况下,全线不会超压。
例二:C泵站进站ESD阀门事故关断(阀门全关断时间为180 s)
故障工况的控制原理如下:
C泵站进站ESD阀门事故关断,必须在阀门离开全开位置之后的30 s内开始顺序执行以下指令,实现管道停输:
1) 停运A泵站所有给油泵和输油主泵,同时停运B泵站和C泵站的所有外输主泵;
2) 在(1)执行后30 s,停运D泵站的所有输油主泵;
3) 在(2)执行后30 s,将F末站进站减压阀设为0开度,并关闭减压阀上下游的截断阀;
4) 将全线所有泵站出站调节阀设为0开度,并关闭调节阀上下游的截断阀;
程序自动处理完成。
结论:C泵站进(出)站ESD阀门事故关断,30 s内采取以上控制程序后,管道全线不会超压。
将上述控制逻辑编入文本,将表1稳态作为初始状态并设定某一时刻出发D站甩泵故障工况,随后调用控制逻辑。
模拟结果显示:该控制逻辑可保证全线不超压。但保山站泄油量超过60方,需针对该问题进行进一步研究。
例三:E120线路监控截断阀事故关断(阀门全关断时间为180 s)
故障工况的控制原理如下:
E120线路监控截断阀事故关断,必须在阀门离开全开位置之后的120 s内开始顺序执行以下指令,实现管道停输:
1) 停运A泵站所有给油泵和输油主泵,同时停运B泵站、C泵站和D泵站的所有外输主泵;
2) 在(1)执行后60 s,将F末站进站减压阀设为0开度,并关闭减压阀上下游的截断阀;
3) 将全线所有泵站出站调节阀设为0开度,并关闭调节阀上下游的截断阀;
4) 程序自动处理完成。
结论:E120线路监控截断阀事故关断,120 s内采取以上控制程序后,管道全线不会超压。
将上述控制逻辑编入文本,将表1稳态作为初始状态并设定某一时刻出发D站甩泵故障工况,随后调用控制逻辑。
模拟结果显示:该控制逻辑可保证全线不超压。但保山站泄油量超过60方,需针对该问题进行进一步研究。
通过对三种故障工况进行模拟得出:很有必要对保山进站水击压力值进行进一步研究(如下2:超前保护设置的可靠性);
后续按照相同方法对所有故障工况控制逻辑进行验证,经过模拟发现两处不合理(包括上述示例)。
两处不合理包括:一是C站进站水击泄压设定值偏低,在大多数故障工况下,该处的水击泄压阀均会触发动作,部分故障工况下泄油量超过60方。这将造成很大的风险隐患和给现场带来较大的额外工作量。经过与初设方沟通,目前已经完成该点水击泄压设定值的更改(设定值为4.7 MPa改为5.2 MPa);二是上面举例出现的隐患,原因已经分析清楚,建议就是按照修订的控制逻辑进行更正。经过与初设方沟通,目前已经完成该故障工况控制逻辑的修改(由降量输送改为全线停输)。
综上所述,本次研究发现该密闭输送原油长输管道控制原理有两处较大的隐患,后经过与初设方协调进行修改;经过本次修改,进一步加强控制原理在故障工况下的可靠性。
3.2. 超前保护设置的可靠性
基于表1,按照下述方法依次研究该原油管道各站水击泄压阀设定值的极限值。
所采用的方法是:1) 将表1的稳态作为模拟的初始状态;2) 将模型中所有站的进出水击泄压阀关闭;3) 调用一项编辑好控制逻辑的故障工况控制逻辑开始模拟;4) 完成模拟后依次记录各站进出水击泄压处的最高压力;5) 依次模拟控制原理中的所有故障工况触发的控制逻辑,并最终比选出各站进出水击泄压处的极限压力。
由表2可以得出:C站进站的模拟极限压力为6.02 MPa,而实际设定压力为4.7 MPa,该点的设定压力建议值应为6.3 MPa,但由于该处的设计压力为5 MPa,故经过协调,将其泄放压力设定为5.2 MPa。
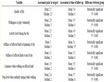
Table 2. Simulated Extreme pressure of water hammer relief valves for entering and exiting stations at each station
表2. 各站进出站水击泄压阀模拟的极限压力
3.3. 控制原理的响应时间研究
基于表1,按照下述方法依次研究不同故障工况下控制原理的相应时间,给出相对较优值。主要设计阀门的关断时间和故障下控制逻辑的相应时间。
1) 该原油管道干线的阀门开关时间为180 s,本部分主要基于不同故障工况研究阀门开关时间取值范围并给出建议设定值。
具体方法是:a) 将表1的稳态作为初始状态;b) 调用一项编辑好的故障工况控制逻辑开始模拟;c) 待模拟完成后,查看各站模拟的泄压罐是否油液位上升,全线是否有压力超压的报警;如没有相关报警更改阀门关断时间(增加1 s),如有相关报警则记录该关断时间,该时间为该故障工况下阀门关断时间的上限值;d) 完成步骤3后,从步骤2开始重新模拟,待模拟完成后,查看各站模拟的泄压罐是否油液位上升,全线是否有压力超压的报警;如没有相关报警更改阀门关断时间(减小1 s),如有相关报警则记录该关断时间,该时间为该故障工况下阀门关断时间的下限值;e) 结合步骤3和步骤4,得出该故障工况下的阀门全关时间区间。
依次模拟出不同工况下的阀门全关时间区间。将所有得出的阀门全关时间区间取交集,得出阀门关断时间的取值范围为175~182 s。在实际中设定值为180 s,建议可将阀门全关断时间设为177 s,这样可在保证故障工况下超前保护程序对管线的保护,又可在故障时尽快关闭阀门,减少损失。
2) 控制原理中明确在故障工况下控制逻辑的响应时间为30 s,本部分主要探讨其是否可靠。
具体方法是:a) 将表1的稳态作为初始状态;b) 调用一项编辑好的故障工况控制逻辑开始模拟;c) 调整控制逻辑的相应时间(增加1 s),如有相关报警则记录该时间,该时间为该故障工况下阀门关断时间的上限值。
经过验证:控制逻辑响应时间为30 s时可以使得故障工况下触发全线不超压,建议可以恰当减少响应时间,避免故障工况下造成的损失(比如油品泄漏)。
4. 结论
1) 该管输原油管道的控制原理存在两处不合理。一是C站进站水击泄压阀设定值偏低;二是D站甩泵故障工况下的超前保护程序错误。以上两缺陷已经完成修订,故本次控制原理的可靠性研究是很有意义的;
2) 该管输原油管道C站进站水击泄压阀设定值明显偏低,建议现场人员结合该管段的设计压力,将该处水击泄压阀设定值更改为6.3 MPa,同时和设定方沟通做好相关的变更;
3) 通过对该管输原油管道控制原理的响应时间进行模拟,得出阀门关断时间的取值范围为175~182 s。在实际中设定值为180 s,建议可将阀门全关断时间设为178 s;控制逻辑响应时间为30 s时可以使得故障工况下触发全线不超压,建议可以恰当减少响应时间,避免故障工况下造成的损失(比如油品泄漏);
4) 该管输原油管道控制原理经过本次可靠性研究,完成了几项控制逻辑的修订,这对提高该管输原油管道控制原理可靠性有着较大的意义;针对国内其它长输原油管道,由于服役时间长短会造成长输原油管道输送能力的变化,故很有必要定期基于其近几年运行数据修正其控制原理。尤其是新投运管道,运行前三年内需尽快完成可靠性校核。
5) 由于模型中的长输原油管道壁厚采用设计数据的壁厚录入,故校核结果仅针对干净的长输原油管道。运行单位需根据原油管道的结蜡情况,合理安排清管作业,以避免由于罐壁结蜡造成长输原油管道控制原理出现失效的情况。