1. 引言
激光核聚变、光刻设备等高精尖领域的迅速发展对高精度光学元件的加工质量和加工效率提出了严格的要求 [1] [2] ,对此国内外学者研发了如磨料水射流抛光 [3] 、磁流变抛光 [4] 、气囊抛光 [5] 等高性能加工技术。
由于传统机床占地面积大、使用成本高,因此具有高效率、高精度、低成本优点的工业机器人气囊抛光技术,在需求日益增长的高精度光学元件加工领域展现出极大的应用潜力。浙江工业大学的计时鸣 [6] [7] 、黄智 [8] 、厦门大学林泽文 [9] 等人搭建了工业机器人气囊抛光平台,对多种光学元件进行工艺和运动轨迹规划等方面的研究,验证了工业机器人气囊抛光的可行性。但是目前工业机器人气囊抛光技术还处于探索阶段,而且由于机器人低刚度特性产生振动而影响加工质量是现阶段主要存在的问题 [10] 。Pan等人 [11] 针对机器人铣削加工系统,研究机器人加工系统的振动问题,通过建立机器人铣削力模型,分析得出机器人系统固有的低刚度特性是机器人加工系统产生自激振动的主要原因。Hazel等 [12] 通过高速相机观察发现在机器人磨削加工中刀具和工件之间存在的振动冲击严重影响磨削质量。Guo等 [13] 根据机器人镗孔系统的加工特性,分析机器人镗孔系统的振动机理,得出在机器人镗孔过程中机器人本体容易发生自激振动,同时机器人镗孔系统的振动类型是具有位移反馈的强迫振动。Li等 [14] 对机器人铣削系统进行模态实验,得到机器人铣削加工不同状态下的模态参数,并根据振动测试数据得到机器人铣削系统振动稳定性叶瓣图,提出了可降低铣削振动的措施。
目前研究机器人系统振动对磨削、铣削和镗孔的影响较多,而对于机器人气囊抛光技术的研究主要集中在工艺和轨迹规划等方面,尚未有明确的结论阐述机器人系统振动对气囊抛光质量的影响。因此本文通过建立机器人气囊抛光系统的动力学模型,分析机器人气囊抛光系统的振动机理;进行振动响应测量实验和抛光实验,研究抛光过程中不同工艺参数的系统振动对工件表面粗糙度、材料去除率和表面形貌的变化规律。
2. 振动机理分析
六自由度关节型串联机器人的末端动力学特性与其关节姿态角有关,当机器人进行加工时,机器人通常保持固定姿态,因此通过建立质量-弹簧-阻尼系统分别分析机器人在x、y、z各个方向上的振动机理。
在三维空间中,机器人末端各方向上的力–线位移的刚度性能可用椭球体来描述,称为“刚度椭球” [15] 。如图1所示,该椭球体半轴的长度分别表示机器人末端在各个方向上的刚度大小,在气囊抛光过程中,动态的抛光力可以分解为法向的下压力和切向的摩擦力,作用在机器人末端各方向上的力即为抛光反力fn和摩擦力ft 。根据机器人的静力学理论,当取刚度椭球体的半轴x、y、z向为坐标轴时,机器人对应的刚度矩阵为对角阵,可以消除耦合性,便于分析计算。因此以机器人刚度椭球半轴为坐标轴建立主刚度坐标系,建立机器人气囊抛光系统动力学模型,如图2所示。
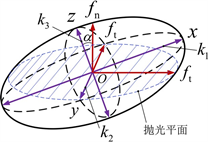
Figure 1. Equivalent model of robot stiffness
图1. 机器人刚度等效模型
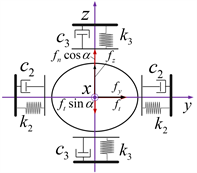
(a) XZ方向 (b) YZ方向
Figure 2. Dynamic model of the robotic bonnet polishing system in all directions
图2. 机器人气囊抛光系统各方向动力学模型
当系统受到抛光反力fn和摩擦力ft作用时,机器人将在x、y、z三个相互垂直的方向上产生受迫振动,设机器人末端在各个方向上受到的作用分力分别为fx、fy、fz,建立机器人气囊抛光系统动力学方程:
(1)
其中m为系统等效质量,x1、x2、x3分别为系统沿主刚度坐标系x、y、z方向上的振动位移,c1、c2、c3分别为系统沿主刚度坐标系x、y、z方向上的阻尼系数,k1、k2、k3分别为系统沿主刚度坐标系x、y、z方向上的刚度值,fx、fy、fz分别为系统在主刚度坐标系x、y、z方向上的所受作用分力。
考虑到系统振动对气囊抛光下压量的影响,对抛光反力引入一固定幅值的正弦波动,并代入正弦力fnsinωt进行分析,其中ω为主轴转动频率,根据文献 [16] ,则此时切向的摩擦力大小为ft = μfnsinωt。根据图2的动力学模型,若机器人当前位姿下所受到的抛光反力fn与刚度椭球z轴之间的夹角为α,则根据图中的几何关系可以得到机器人主刚度坐标系上的作用分力:
(2)
令
分别为系统在x、y、z方向上的固有频率分量;
分别为系统x、y、z方向上的阻尼比分量,则机器人气囊抛光系统的动力学方程为:
(3)
求解式(3)的稳态响应:
(4)
且:
(5)
其中X1、X2、X3分别为系统沿主刚度坐标系x、y、z方向上的稳态响应振幅,φ1、φ2、φ3为稳态响应的相位差,
分别系统沿主刚度坐标系x、y、z方向上的频率比。
分析式(5)可得机器人系统的稳态振幅Xi与刚度ki、阻尼比ξi、抛光反力fn、系统固有频率ωi和主轴转动频率ω等参数密切相关。当机器人在固定的姿态下抛光时,机器人的刚度ki、阻尼比ξi和系统的固有频率ωi已经固定,其振幅主要受抛光主轴转动频率ω (取决于转速)和抛光反力fn (取决于下压量)的影响。机器人在抛光反力fn的作用下将产生较大的振幅,当气囊主轴转动频率ω接近于系统的固有频率ωi时,频率比λ = 1,机器人发生共振。因此,在抛光反力和共振的共同作用下系统的振幅会急剧增大,直接影响机器人末端法兰中心的空间位置,最终导致气囊球心偏离理想位置,产生一定的空间误差,严重影响加工精度。
3. 实验
3.1. 实验设备
图3为基于工业六轴机器人ABB-IRB2600搭建的气囊抛光系统及振动测量装置。机器人气囊抛光系统包括机器人本体、控制柜、气囊抛光工具、抛光液循环装置等;振动测量装置包括加速度传感器、NI数据采集卡、测力锤、采集软件。机器人抛光系统及振动测量装置关键参数如表1所示。
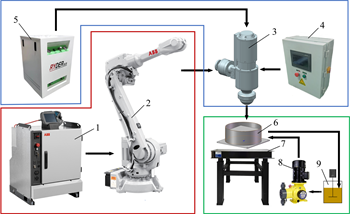
1. 机器人控制柜 2. 机器人本体 3. 气囊抛光机 4. PLC控制柜 5. 空压机 6. 回收槽平台 7. 光学平台 8. 隔膜泵 9. 搅拌装置
(a) 机器人气囊抛光系统
1. 测力锤 2. 抛光机器人 3. 采集软件 4. NI采集卡 5. 加速度传感器(b) 机器人振动特性测量示意图
Figure 3. Robot bonnet polishing system and vibration measurement device
图3. 机器人气囊抛光系统及振动特性测量装置
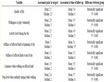
Table 1. Key parameters of robot bonnet polishing system and vibration measurement device
表1. 机器人气囊抛光系统及振动测量装置关键参数
3.2. 实验过程
为研究系统不同工艺参数(下压量、主轴转频)下的振动特性对加工质量影响,设计实验方案如下:采用锤击激励法进行模态实验,将机器人调节到加工姿态并将传感器固定在机器人joint 6处,用力锤给予机器人x、y、z三向激励,分别激励其余布置测点,利用ModelView软件采集模态测试中的加速度信号。进行振动加速度响应测量实验和抛光实验,振动加速度响应测量实验将加速度传感器放置在机器人joint 6处,设置采样频率为10 kHz,利用NI SignalExpress软件实时采集和存储机器人抛光过程中不同工艺参数下的振动加速度数据。抛光实验采用质量分数10%、粒径10 μm的氧化铈磨粒水基抛光液,抛光工件为30 mm × 30 mm × 10 mm的石英玻璃,抛光时间10 min,其余实验参数如表2所示。采用Taylor轮廓仪测量工件表面粗糙度,精密电子秤测量工件抛光前后质量并计算材料去除率,Keyence VHX-2000显微镜观察工件表面形貌。
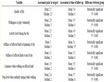
Table 2. Experimental parameters of fixed-point polishing
表2. 气囊定点抛光实验参数
4. 实验结果分析
4.1. 系统振动特性
分析机器人0~30 Hz工况频带,对模态实验采集到的加速度信号进行频域分析和归一化处理,得到在各测试点激励下机器人振动响应加速度频域变化曲线,并通过峰值拾取法得到机器人在加工姿态下的实际固有频率,如图4所示,加工姿态下机器人系统实际固有频率大小分别约为11.35 Hz、13.05 Hz、17.74 Hz、19.89 Hz、27.36 Hz。可以得出,机器人在实际工作姿态下的固有频率整体偏小,刚度偏低,在抛光力的作用下易产生较大的振幅,且在机器人工作频率范围内存在5阶模态,每一阶模态都可能在机器人抛光过程中引起系统的共振使振幅急剧增大。
振动加速度均方根值RMS可较好地反应系统的振幅和振动能量强度,对抛光过程中采集到的各方向加速度数据求取均方根,得到机器人末端各方向振动加速度响应曲线,如图5所示。在相同转动频率下,随着下压量的增加,抛光反力增大,机器人因抛光反力产生的受迫振动增加,机器人末端振幅增大;在相同下压量下,机器人末端在工况频带11~13 Hz、17~21 Hz、27~28 Hz之间的振幅较大,根据模态分析可知这三个频带处于机器人本体固有频率附近,与机器人本体发生共振,振幅较大,而工况频带14~16 Hz、22~26 Hz为机器人气囊抛光系统的非共振区,振幅较小。由此可以确定,机器人可用加工频段严重受限,机器人气囊抛光系统动态特性较差,在实际抛光过程中,由于受迫振动和共振的作用,机器人末端振动更加显著,将严重影响工件的抛光质量。
(a) X方向激励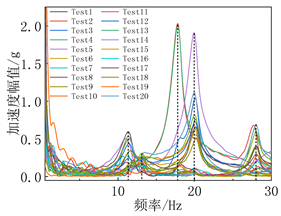
(b) Y方向激励 (c) Z方向激励
Figure 4. Acceleration response spectrum of each measurement point in the modal experiment
图4. 模态实验各测点加速度响应频谱
(a) X方向振动响应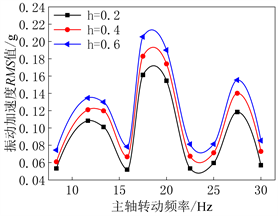
(b) Y方向振动响应 (c) Z方向振动响应
Figure 5. Vibration acceleration response in all directions at the end of the robot during the polishing
图5. 抛光过程中机器人末端各方向振动加速度响应
4.2. 振动对表面粗糙度影响
图6为不同下压量下工件表面粗糙度Ra随主轴转动频率变化曲线。Ra变化曲线和实际抛光过程中测量的机器人末端振动加速度RMS曲线具有相同的变化趋势。在相同转动频率下,随着下压量的增加,机器人因抛光反力产生的受迫振动增加,Ra增大;在相同下压量下,工件在机器人共振频带11~13 Hz、17~21 Hz、27~28 Hz的Ra较大,非共振频带14~16 Hz、22~26 Hz的Ra较小。这是由于系统振动直接影响机器人末端法兰中心的空间位置,使气囊抛光头自身橡胶部分与工件表面接触时会产生持续的“回弹”现象,导致气囊球心偏离理想位置,产生一定的空间误差 [17] ,在实际抛光中将导致气囊抛光头与工件表面接触不稳定,液膜稳定性较差,最终影响工件表面粗糙度。
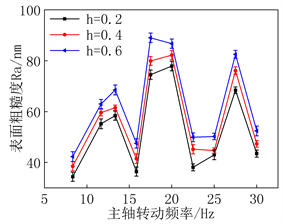
Figure 6. The surface roughness of different pressure amounts varies with the rotation frequency
图6. 不同下压量表面粗糙度随转动频率变化曲线
图7为工件表面粗糙度Ra随机器人末端振动总加速度RMS值变化曲线,当振幅为0.091 g时,对应的工件表面粗糙度最小Ra = 34.4 nm,随着振幅的增大,Ra增大,当振幅达到0.322 g时,对应的工件表面粗糙度最大Ra = 89 nm。表明系统振动严重影响工件表面粗糙度,表面粗糙度随系统振动强度的增加而增大。
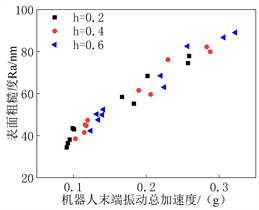
Figure 7. The influence of system vibration on surface roughness
图7. 系统振动对表面粗糙度影响规律
4.3. 振动对材料去除率影响
图8为不同下压量下工件材料去除率MRR随主轴转动频率变化曲线,MRR变化曲线和实际抛光过程中测量的振动加速度RMS曲线具有相同的变化趋势。在相同转动频率下,随着对工件下压量的增大,机器人因抛光反力而产生的受迫振动增加,MRR增大;在相同下压量下,工件在机器人共振频带11~13 Hz、17~21 Hz、27~28 Hz的MRR较高,非共振频带14~16 Hz、22~26 Hz的MRR较低。这是因为系统的振动加速度越大,对应的激振力越大,此时激振力增大了气囊抛光压力,所以具有较高的材料去除率。
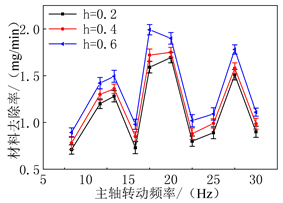
Figure 8. Variation curves of material removal rate with rotation frequency under different pressure
图8. 不同下压量材料去除率随转动频率变化曲线
图9为材料去除率MRR随机器人末端振动总加速度RMS值变化曲线,当振幅为0.091 g时,对应的材料去除率最低MRR = 0. 719 mg/min,随着振幅的增加,MRR也不断增加,当振幅达到0.322 g时,对应的材料去除率最高MRR = 1.991 mg/min。表明系统振动影响工件材料去除率,材料去除率随系统振动强度的增加而增大。
4.4. 工件表面形貌
图10为气囊下压量为h = 0.4 mm,工件在共振频率f = 17.5 Hz和非共振频率f = 15.83 Hz下抛光得到的表面形貌。在其他工艺参数相同的条件下,振动强度较大的共振区抛光得到的工件表面出现较多明显的划痕,材料去除不均匀,抛光表面不平整,光洁度很差,这是由于在实际抛光中系统的振动导致气囊抛光头与工件表面接触不稳定,液膜稳定性较差,主要表现为机械式的材料去除,因此工件表面存在较多划痕和斑点。而非共振区系统振动较小,磨粒和工件之间的接触比较稳定,液膜稳定性较好,因此工件表面凹坑和划痕明显减少,变得更加均匀。
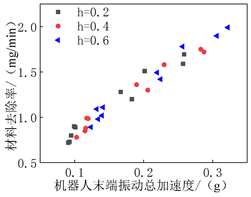
Figure 9. The influence of system vibration on the material removal rate
图9. 系统振动对材料去除率影响规律
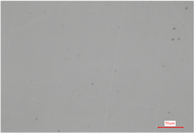
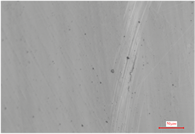
(a) 抛光前表面形貌 (b) 共振频率抛光表面形貌 (c) 非共振频率抛光表面形貌
Figure 10. Effect of system vibration on surface topography
图10. 系统振动对表面形貌的影响
5. 结论
本文针对气囊抛光机器人在加工时易产生振动的问题,开展气囊抛光机器人振动特性对工件加工质量影响的研究。通过建立机器人气囊抛光系统的动力学模型,分析机器人气囊抛光系统的振动机理,并进行振动响应测量实验和气囊抛光实验。主要结论如下:
1) 机器人气囊抛光系统的动态特性较差。在实际抛光过程中,易受到抛光力的作用而产生受迫振动,且在加工姿态下存在多阶工况频带11~13 Hz、17~21 Hz、27~28 Hz与机器人本体发生共振。
2) 系统振动严重影响气囊抛光质量,优化工艺参数可以减小系统振动从而提高工件表面质量。MRR和Ra随系统振动强度的增加而增大,下压量h = 0.2 mm、主轴转动频率在14~16 Hz、22~26 Hz内的系统振动强度较小,MRR较低,Ra较小,适用于精抛阶段可以获得平整和光洁的工件表面。