1. 引言
随着汽车保有量不断地提升,截止2019年民用汽车拥有量25376.38万辆,据国家统计局统计2018年用于交通运输、仓储和邮政业汽油消费总量达到2.2739亿吨,与2017年相比增加了3% [1] 。如今汽车已不仅是一项交通工具,它的制造水平被看成衡量一个国家的现代化水平的标志之一 [2] 。据统计,到2016年全世界重载汽车产量突破9000万辆,相应的轮毂的生产量也十分巨大,在汽车整个产业中占相当大的比重。
汽车车轮对汽车车体有承载作用,可以将发动机的动力转化为驱动汽车前进的力。在汽车前进的过程中,车轮不但起着传递动力的作用,还能兼顾降低路面冲击的减震作用,同时还要受到驾驶人对汽车的转向、制动等工况带来的冲击,因此,车轮的设计性能将直接影响着汽车的舒适性、安全性及耐用性 [3] 。
轮毂是汽车车轮总成的重要组成部件,作为车轮的“骨架”,其同样要承受车辆重力的作用以及车辆行驶过程中各种工况下带来的作用力 [4] 。由于轮毂受力较为苛刻以及结构比较复杂,给轮毂的设计开发带来较大难度。本文将从静态、模态、谐波响应三态对汽车轮毂进行仿真从而分析轮毂的合理性。
2. 研究内容
此次研究对象选取汽车轮毂,下方是用ug对汽车轮毂进行的三维建模,见图1:
3. 静态分析
对轮毂施加约束和力之后进行静态分析可以得到它所受到的最大应力和应变程度,其分析步骤和结果如下所示:
使用mesh进行网格划分,见图2,采用四面体网格,网格密度为默认10 mm网格:
网格划分完之后,点击Static Structural模块中的Insert,添加一个固定约束Fixed Support,将约束添加在四个用于固定轮毂的螺栓处,再添加一个远程力Remote Force,将力添加在轮毂最内侧部位,力的大小设置为400 N,再添加一个外部压力Force,将力添加在轮毂外侧,方向设置在外圈任意一面,大小设置为800 N,然后点击添加Total Deformation和Equivalent Stress,最后点击Solve求解,求解结果如下图所示(应力图见图3,总应变见图4):
4. 模态分析
模态是机械结构的固有振动特性之一,结构的每一个模态都有其特定的固有频率、阻尼比以及振型。这些参数对于分析以及评价机床结构的动态性能,指导机械结构优化设计都具有重要的指导意义;此外共振有时会造成结构的振动或疲劳,从而破坏结构,所以了解结构本身所具有的刚独特性(结构的固有频率、振型),就可避免该结构在使用过程中因共振因素造成的不必要的损失。本章将采用有限元法对本论文所设计的机床进行模态分析,为机床的可靠性研究提供重要的理论依据 [4] [5] [6] [7] 。
本节所分析的模型是简化后的汽车轮毂模型,首先利用ug进行三维建模,然后将其以xt文件格式导入workbench,对其进行静态、模态以及谐波响应分析。ANSYS提供了7种模态计算方法:子空间法,分块法,缩减法,动态功率法,非对称法,阻尼法,QR阻尼法。对于大多数分析来说,选用的都是子空间法,分块法和缩减法 [8] [9] [10] 。
4.1. 轮毂的自由模态分析
首先使用通过Geometry导入轮毂三维模型图,然后用Modol模块对轮毂进行自由模态分析,分析过程及结果如下所示:
用mesh进行网格划分,见图5,采用四面体网格:
网格划分完成之后在analysis settling里选择6阶模态,然后进行求解。求解得到机床的前6阶频率与如图6所示:
如下图为汽车轮毂的前六阶振型的总体位移云图(见图7~12):
汽车轮毂前六阶自由模态频率与最大位移表
由以上六阶振频移云图可以看出,前六阶自由模态中,振动频率最大与位移最大皆发生在第六阶,由此可见,第六阶振动频率状态下对轮毂的影响是最大的。
4.2. 轮毂的预应力模态分析
与自由模态一样,首先使用通过Geometry导入轮毂三维模型图,然后用Modol模块对轮毂进行自由模态分析,先对轮毂进行网格划分,见图13:
在静态分析模块,选择轮毂的四个螺栓处施加固定约束,如图14所示:
施加完约束以及载荷后,同样取前6阶预应力模态,进行求解,结果如图15所示:
与自由模态频率对比可以发现,施加载荷后的预应力模态的频率要大得多,然后求解轮毂预应力模态的总体位移,结果如下图所示(图16~21):
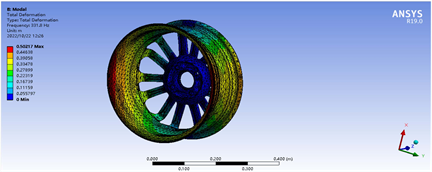
Figure 16. First order vibration mode of prestressed mode
图16. 预应力模态一阶振型
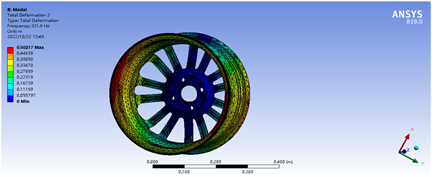
Figure 17. Second order vibration mode of prestressed mode
图17. 预应力模态二阶振型
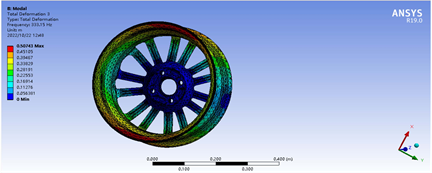
Figure 18. Third order vibration mode of prestressed mode
图18. 预应力模态三阶振型
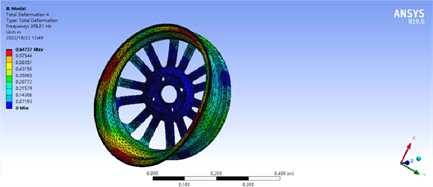
Figure 19. Fourth order vibration mode of prestressed mode
图19. 预应力模态四阶振型
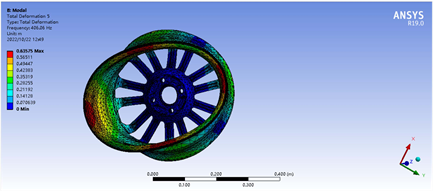
Figure 20. Fifth order vibration mode of prestressed mode
图20. 预应力模态五阶振型
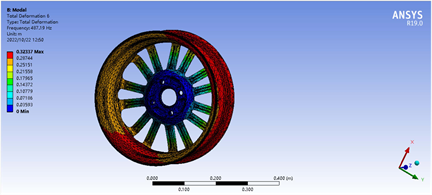
Figure 21. Sixth order vibration mode of prestressed mode
图21. 预应力模态六阶振型
轮毂前6阶预应力模态频率与最大位移表
预应力模态下最大位移发为0.64737,发生在四阶振动频率下,与自由模态相比,预应力模态分析下的位移明显增大,并且最大位移发生的阶数也发生了改变。
5. 轮毂的谐波响应模态分析
谐波响应分析模块也需要在模态分析的基础上进行分析,因此在进行谐波响应分析之前需要先对轮毂进行模态分析施加约束,而约束的施加也需要有一定前提,此处选择将约束施加在螺栓连接处。
选择轮毂上的螺栓连接处,点击Fixed Support施加约束,然后点击apply,便可以成功施加约束,然后点击Hamonic Response,在施加一个力,力的大小设置为400 N,方向延轮毂向里,点击apply,添加位移相关的frequency response,将maximum frequency设置为100,添加位移相关的相位相应phase response,点击frequency设置为100,然后点击求解,求解结果如图22~25所示:
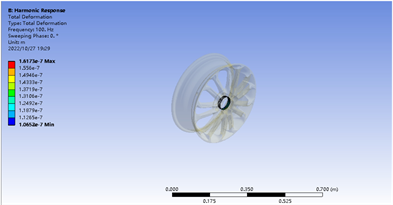
Figure 23. Wheel hub vibration mode at 100 Hz
图23. 100 Hz时轮毂振型
6. 结论
运用ANSYS Workbench对汽车车轮轮毂进行三态的分析,可以得到以下结论:
1) 通过有限元静态分析可以得到车轮轮毂受到800 N的外侧纵向应力时,总应变为8.04e−6。再将轮毂假设以中心固定进行模态分析,得到前6阶固有频率及其振型云图。轮毂的自由模态分析中,前六阶自由模态中,振动频率最大与位移最大皆发生在第六阶,由此可见,第六阶振动频率状态下对轮毂的影响是最大的,在轮毂设计时常用的激励频率应该避开这些频率,以免发生共振。
2) 轮毂的谐波响应分析下,在100 Hz频率下的峰值位移响应发生在100 Hz处,最小位移响应发生在10 Hz处,结合云图分析可知,轮毂的最大位移和振型特征通常随着阶数及频率的增大而增大,且主要集中在轮毂侧面滚筒处,故在轮毂设计时应当加强其刚度和强度,以免在使用过程中发生大幅度形变从而影响使用。