1. 引言
信息技术的快速发展带动了多种行业的发展,汽车行业也不例外 [1] 。如今,安全性与舒适性成为了评判汽车优劣的重要指标,但是其实人们已经潜移默化地将另一项指标视为基本,那就是耐用性。车辆停驶后,若方向盘不回正,会使得悬架受力不均、车胎受力面不正确 [2] ,长时间下去,对两者的损害会越来越严重,这便会使得悬架与车胎的使用寿命缩短,资源利用率降低。车辆静态下方向盘自主回正系统,就是针对这种情况设计的,该系统能实现轮胎的原地转向,其有利于提高车辆的安全性并能够延长悬架系统及轮胎的使用寿命(图1)。
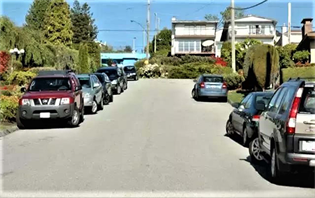
Figure 1. Tires do not return to the right position when the vehicle is parked
图1. 车辆停驶后轮胎不回正
本课题采用SolidWorks对车轮以及电动助力转向系统中(EPS)的(齿轮齿条)转向器进行三维建模分析以及仿真计算,以验证该系统中机械结构部分的可行性。
在此次的研究过程中,我主要做了以下几项工作:
收集汽车轮胎、转向器齿轮齿条的相关参数,并采用SolidWorks对它们进行3D建模。
通过轮胎原地转向阻力矩的经验公式计算了轮胎回正的最大阻力矩,利用SolidWorks Motion对轮胎与地面进行了仿真模拟,模拟了车轮的回正过程,并计算了该情况下车轮回正横拉杆至少要提供的转矩。
通过SolidWorks Simulation对齿轮齿条进行静应力的有限元分析,并得出了该工况下的应力应变情况。
2. 车辆静态下方向盘自主回正系统的工作原理
当车身控制模块(BCM)检测到驾驶员将车辆钥匙由ON转到ACC,电子助力转向系统(EPS)便通过方向盘角度传感器 [3] 检测并收集方向盘的偏转角度,若方向盘处于偏转状态,则车载娱乐系统(ICE)将用文字和语音的方式提示驾驶员,并启动EPS,执行方向盘自主回正动作(图2)。
3. 对车轮、地面的建模与仿真
车辆静态下方向盘自主回正系统 [4] 组成结构很多,在本论文中,只对其执行部件进行研究,即电子助力转向系统(EPS)。因为在该系统启动时,EPS作为执行部件,其内部的电动机提供一定的转矩;而轮胎作为被执行部件,其胎面与地面之间的摩擦会产生一定的力矩,要克服该力矩,电动机所提供的转矩就需大于轮胎与地面产生的阻力矩(图3)。
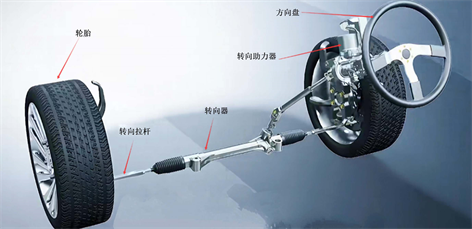
Figure 3. Mechanical structure of the autonomous steering wheel return system
图3. 方向盘自主回正系统机械结构
地面对轮胎的力矩由翻转力矩、滚动阻力矩、回正力矩这三中力矩构成 [5] 。汽车的最大转向阻力矩就是汽车在静态下的原地转向阻力矩 [6] 。
在本次设计中,建模参考的车型为上汽大众途安,该车属于紧凑型MPV。我们要计算在普通路面上,车辆停驶时,要使轮胎回正,轮胎与地面之间会产生多大的力矩,电动机要提供多大的转矩;还要分析在自动回正过程中转向器应力分布情况,在进行分析之前,要对转向器和轮胎进行3D建模,本论文选用SolidWorks软件进行建模,用SolidWorks Motion对轮胎与地面进行摩擦力矩分析,计算出车轮的转向力矩,用SolidWorks Simulation对转向器进行静应力强度分析。
3.1. 车轮和地面建模
本次建模参考的车型为上汽大众途安,该车属于紧凑型MPV,所用轮胎为飞劲Ziex ZE914A,型号是205/60 R16 92V,即该轮胎宽度为205 mm,扁平比为60%,轮辋直径为16寸,载重指数92代表该轮胎的最大载重量为630公斤,V代表其最大行驶速度为240 km/h (图4)。
3.2. 轮胎原地转向阻力矩的计算
原地转向时转向阻力矩主要由三个部分构成:轮胎静态转向力矩、重力回正力矩以及转向系统干摩擦力矩 [7] 。通常情况下,转向系统的摩擦系数为常数,因此这里就以地面与转向轮之间的相互作用作为主要讨论对象。影响汽车转向阻力矩的主要因素有转向轴的负荷、轮胎与地面之间的摩擦系数以及轮胎气压 [8] 。
当前最常用来计算其阻力矩的经验公式 [9] ,如下:
(1)
式中:
为在沥青或混凝土路面上的原地阻力矩;
为轮胎与地面间的摩擦系数,取0.7;
为转向轴负荷;
为轮胎气压,KPa。
该轮胎的型号为205/60 R16 92V,故取摩擦系数
,车胎气压
,前轴载荷取值
。由(1)式得该轮胎的原地转向阻力矩为226.39 Nm。
3.3. 横拉杆作用于车轮的仿真计算
打开车轮与地面的装配体,使用Motion插件功能并建立新的运动算例,为车轮添加材料属性,将轮胎的材料定义为橡胶,将轮辋的材料定义为合金钢。
在算例中给轮胎添加引力和阻力矩,引力方向为Y轴方向,阻力矩大小为226.39 Nm。
对轮胎添加马达力矩,将马达位置安放于轮辋中心,起点位置的马达转动速度设置为0 r/min;将轮胎的转动节点设置在0.5 s位置处,此处节点的时间位置会影响马达力矩,设置的时间越短,马达力矩越大。在该节点处重新定义马达参数,为了使轮胎能够尽快回正,在这里我取马达的转动速度为10 r/min,意思是轮胎从静止的0 r/min到10 r/min要花费0.5 s,且在这0.5 s的时间内车轮会有一个加速的过程,在这个加速过程中,马达会对该车轮产生一个力矩,该力矩的大小就是横拉杆推动车轮产生的转矩。
计算该运动算例,并生成图解。由图5我们可以看到,在这种情况下,推动车轮的转向力矩至少为228.58 Nm。
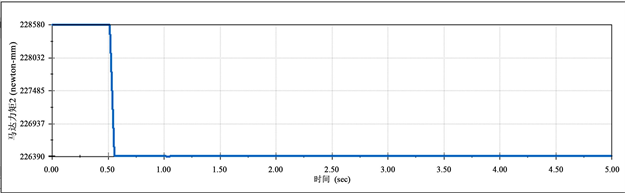
Figure 5. Torque generated by the motor
图5. 马达产生的力矩
4. 对转向器的建模与仿真
斜齿轮在目前的转向器齿轮中应用较广泛 [3] ,齿轮模数的值一般为2至3,压力角为20˚,斜齿轮的齿数通常是5至15之间,螺旋角的取值一般为9˚至15˚,齿条的齿数可以根据斜齿轮齿数进行合理设计。此课题将采用方程式的方法进行建模(图6)。
斜齿轮、斜齿条参数方程式如下表1、表2。
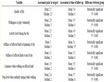
Table 1. Helical gear parameter equation
表1. 斜齿轮参数方程式
渐开线公式:
(2)
(3)
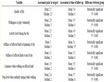
Table 2. Parameter equation for helical rack
表2. 斜齿条参数方程式
4.1. 车轮自主回正工况下齿轮齿条的有限元分析
有限元仿真法则是综合了力学、摩擦学、复合材料力学及有限元算法的一种计算机分析方法,近年来得到了广泛的应用 [10] 。接下来将通过SolidWorks自带的插件Simulation,给予齿轮相应的力矩,对齿轮齿条的静应力强度、位移、应变及安全系数进行分析。
4.1.1. 齿轮齿条扭矩的计算
通过分析车辆的前桥总成和转向节总成,即图7,我们可以发现齿轮的扭矩是通过齿条传递给横拉杆的,再由横拉杆推动车轮旋转。
要找到作用在齿轮条上的推力,可以根据力矩公式:
(4)
其中:
为力矩;
为齿条作用于一个车轮上的推力;
为横拉杆长度。
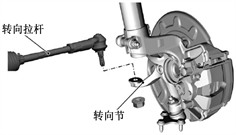
(a) (b)
Figure 7. (a) Front axle assembly; (b) Steering knuckle assembly
图7. (a) 前桥总成;(b) 转向节总成
我们取T为
,R为
。
代入公式(4)得
。由于齿条的推力作用于两个轮胎上,所以齿条作用在齿轮上的推力为
。
(3)再根据力矩公式(4),求出齿轮的扭矩,因转向系统中的传递效率比较稳定,所以取传递效率
[11] 。
由表1,该斜齿轮分度圆直径
,所以齿轮的扭矩为
。
4.1.2. 齿轮齿条有限元分析过程
我们取T为228.58 Nm,R为0.3 m。
在SolidWorks Simulation中建立新算例,选择静应力分析。对斜齿轮应用合金钢的材料属性,对斜齿条应用45号钢的材料属性。设置夹具顾问,对斜齿条的底面应用几何体固定,对斜齿轮的内圆柱面应用固定铰链(表3)。
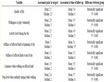
Table 3. Material properties of rack and pinion
表3. 齿轮齿条材料属性
为斜齿轮添加外部载荷,在斜齿轮的内圆柱面内应用力矩,大小为18.10 Nm。
设置相触面组,无穿透类型,选择个零件的相应接触面,摩擦设置为0.1。
生成网格,将网格密度设置为良好。
运行此算例,得到齿轮齿条的应力分布图。
通过图形可以看到,该齿轮齿条在18.10 Nm的扭矩作用下的最大应力值为7.575e+08 Pa,最小应力值为1.200e+01 Pa,最大位移量为3.194e−01 mm,最小位移量为1.000e−30 mm,最大应变量为1.896e−03,最小应变量为2.594e−11,最大安全系数为5.169e+07,最小安全系数为8.191e−01。
从以下图形中我们并未发现灰色区域,这意味着齿轮齿条在该载荷下没有出现变形甚至损坏,材料也没超过应力的极限强度,可看出车辆静态下方向盘自主回正系统中齿轮齿条的应力应变都在可承受范围内,故该设计是合理的(图8~12)。
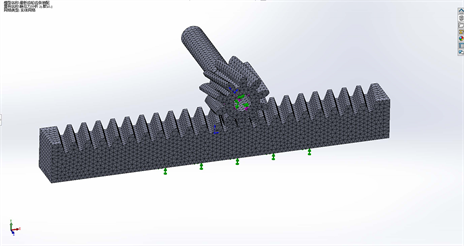
Figure 8. Rack and pinion meshing diagram
图8. 齿轮齿条网格划分图
5. 结论
通过对车辆静态下方向盘自主回正系统的设计与分析,得出以下结论:
齿轮齿条在方向盘自主回正系统工况下的最大应力值为7.575e+08 Pa,最小应力值为1.200e+01 Pa,最大位移量为3.194e−01 mm,最小位移量为1.000e−30 mm,最大应变量为1.896e−03,最小应变量为2.594e−11,最大安全系数为5.169e+07,最小安全系数为8.191e−01。
将电动助力转向系统中的(齿轮齿条)转向器用于方向盘自主回正是完全合理的。
这次实验所得出的数据都在合理范围内,可为以后的相关工作提供参考。