1. 引言
随着燃料成本和排放标准的不断提高,工程机械的节能减排面临着巨大的压力和挑战。液压挖掘机是一种重要的工程机械,主要应用于桥梁建设、道路施工、房屋建筑等场合。但以传统燃油发动机驱动变量泵作为动力源的方式,不能高效率应对其挖掘工况存在的负载波动大、工作场合复杂多变等情况,当挖掘机低负载工况运行时,发动机往往运行在低效率区间。另外,燃油发动机存在排放大、能耗高等问题。因此,提高挖掘机动力源效率,解决废气污染问题,对工程机械的节能减排有着重要意义。
纯电动挖掘机把发动机换成了电动机,实现了真正意义上的零排放、零污染。电动机有着动态响应快、超载能力强的特点,已成功应用于汽车领域。陈爽等 [1] 提出了一种双电机纯电动汽车实时驱动系统损耗最小的转矩分配策略;胡冰等 [2] 为实现全范围内的转矩电流最优控制,提出了一种电动汽车用感应电机最大转矩电流比控制策略。然而,挖掘机在负载特性、工作转速范围、再生控制等方面和汽车都有本质不同,因此电动汽车的驱动技术和控制技术都无法直接移植到工程机械上 [3] ,我们需要针对工程机械的结构和实际工况,设计出适用于工程机械的电驱动系统控制策略。目前,对电动挖掘机的研究有限,大部分企业或研究团队更关注的是能量管理 [4] 和能量回收 [5] 技术,对电驱动动力传动技术和流量匹配技术研究有限。Lin等 [6] 提出了一种结合发电机和蓄能器优点的新型能源再生系统;Wang等 [7] 提出了一种基于电液复合储能的串联式混合动力液压挖掘机,并采用动态优化算法对其动力传动系统和能量流管理系统参数进行优化。虽然混合动力系统采用了电机,但是发动机仍然是主要的动力装置,因此混合动力挖掘机并不能真正意义上实现零排放。
在电动挖掘机的研究方向上,陈俊屹等 [8] 提出了一种基于分级压差控制的双变动力控制方法,最大限度地避免了流量饱和工况的发生并在一定程度上提高了系统的节能性;刘彪等 [9] 提出了一种基于“排量预值”的转速排量复合控制模式,实现了运行成本的降低;Ge等 [10] 提出了泵转速和排量控制相结合的匹配方法,并设计了一种独立计量系统的动力源和阀门联合控制策略,以同时提高不同工况下的能量效率和动态性能;Guo等 [11] 结合锂离子电池的放电特性和电动机的过载能力,提出了一种分段恒功率控制策略,保证了电动挖掘机在满足大功率输出的前提下,系统在重载时能正常稳定运行;陈俊宇 [12] 研究了电动挖掘机电池的散热系统。
在工程机械电动化的大趋势下,对其电驱动系统控制策略的研究是必然趋势。本文根据现有电动挖掘机存在的控制性能差,能耗大,效率低,低速机动性能差等问题。通过优化算法,匹配系统最优效率时电机的转速,提出了一种基于双变动力源系统效率最优的排量自适应控制策略,充分发挥了电机良好的调速性能和超载能力。搭建了AMESim和MATLAB/Simulink联合仿真模型,在工作装置完成同一工况下,对比分析不同驱动方案液压挖掘机的能耗特性,说明系统和控制策略的节能性。
2. 电动液压挖掘机系统
纯电动液压挖掘机与传统液压挖掘机相比,最显著的变化在于其动力总成系统。纯电动液压挖掘机整体系统原理图如图1所示。系统中用电动机替换了传统挖掘机中的柴油机,通过电缆给电机供电,使用变频器调节电机转速,从而改变负载敏感泵的转速,来实现目标工况。液压部分采用负载敏感系统,控制动臂、斗杆、铲斗和回转马达四个执行器。
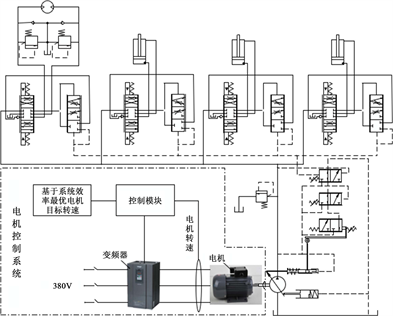
Figure 1. Electric excavator system schematic
图1. 电动挖掘机系统原理图
电动挖掘机将传统的柴油发动机替换为电动机,并通过电池或外接电源与变频器相连。PLC控制模块通过改变变频器的频率来控制电机的转速。这种系统架构的改变一方面实现了真正意义上的绿色零排放,另一方面发挥了电机优良的调速性能。在液压控制系统方面,本文采用了具备抗流量饱和特性的负载敏感系统。该系统通过梭阀,将执行器的最大负载压力作用到压力补偿阀的弹簧腔,与各压力补偿阀进油口的压力平衡,同时将最大负载压力引入到负载敏感泵的控制端,使泵的出口压力始终比最大负载压力高出一个恒定值,使得系统具有良好的操控性。当泵所提供的流量无法满足系统需求流量时,节流口两端的压差仍能保持恒定,使得流向各执行器的流量同比例减少,从而维持挖掘机的正常运作。
3. 基于双变动力源的系统效率最优控制方法
大多数电动挖掘机只是简单地用定速电机代替柴油机,通过改变变量泵排量比来提供系统需求流量。这种方式虽然有效解决了环境污染问题,但是并没有改善系统中存在的动态响应慢,效率低,能耗高等现象。图2为定速电机驱动下,挖掘机模拟一典型工况,泵出口压力减去最大负载压力所得差值的变化曲线。压差设置为1.6 MPa,溢流阀设置为2.8 MPa,模拟挖掘机挖掘、满斗回升、回转、卸载、复位这一经典工况,可以看出出现溢流和流量饱和工况的时间占比很大。
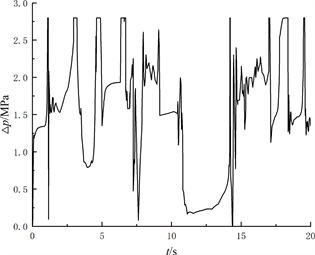
Figure 2. Load-sensitive pressure differential variation chart
图2. 负载敏感压差变化图
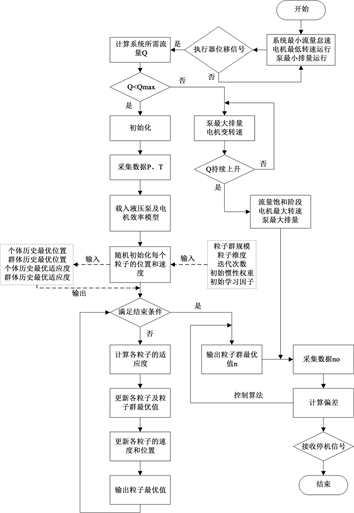
Figure 3. Optimal efficiency-based displacement adaptive control strategy diagram for dual power source system
图3. 基于双变动力源系统效率最优的排量自适应控制策略图
因此,本文提出一种基于双变动力源系统效率最优的排量自适应控制策略,如图3所示,通过控制电机转速,使系统维持最优效率运行。具体控制方式为:根据执行器位移信号计算出系统所需流量,再根据测得的泵出口压力和电机输出扭矩,利用粒子群算法计算出系统效率最优时电机的目标转速。将该目标转速作为输入信号,并将电机的实际转速作为反馈信号,通过PID控制器对偏差进行调整,以实现系统的精确控制和稳定运行;在液压方面,采用具有抗流量饱和的负载敏感系统,根据系统反馈的最大负载压力,液压泵的排量能自适应负载变化。
3.1. 电机效率模型
电机的效率可以通过输出功率与输入功率的比值来计算,而输出功率与电机功率损耗的和为电机输入功率 [13] ,即:
(1)
(2)
其中,
、
、
、
分别指的是电机效率、电机输出功率、电机输入功率和电机损耗功率;
、
、
和
分别指的是电机铜耗、铁耗、摩擦损耗和杂散损耗,杂散损耗一般情况下可以忽略 [14] ,具体计算方法可表示为:
(3)
(4)
(5)
经过进一步推导,可以将电机损耗功率
用输出转矩
和电机角速度
来表示:
(6)
因此电机的效率模型可表示为:
(7)
其中,
代表定子相绕组电阻;
代表电机自感;
代表电机转速;
代表铁损等效电阻;
代表摩擦阻力系数;
代表电机转子永磁体极对数;
代表电机永磁体磁链。
3.2. 泵效率模型
柱塞泵的能量损失主要包括容积损失和机械损失。容积损失是由于液压油流动过程中的泄漏和流阻等因素导致的能量损失,而机械损失则是由于泵内部部件之间的摩擦引起的能量损失。这两种损失分别对应着柱塞泵的容积效率
和机械效率
。泵的容积效率可以表示为 [15] :
(8)
泵的机械效率可以表示为:
(9)
其中,
代表层流泄漏系数;
代表进出口压差;
代表油液动力粘度;
代表泵转速;
代表泵的排量比;
代表层流阻力系数;
机械阻力系数;
代表扭矩损失;
代表泵的最大排量。
因此柱塞泵的效率模型
可以表示为:
(10)
3.3. 电机和柱塞泵整体效率模型
假设系统在理想状态下运行,忽略摩擦损耗、传动装置的效率损耗以及其他能量损耗时,总效率可以近似等于电机效率和泵效率的乘积,即:
(11)
4. AMESim-MATLAB联合仿真模型的建立
为了验证所提出控制策略的可行性并分析其节能效果,在AMESim仿真软件中建立电动液压挖掘机液压系统和机械结构的仿真模型。在此基础上,与Smulink联合仿真来实现系统效率最优控制策略,如图4所示。
挖掘机的液压系统主要组成部分包括:负载敏感斜盘式轴向柱塞泵,LUDV系统,动臂、斗杆、铲斗液压缸和回转马达四个执行器。LUDV系统实现流量的精确控制,使流量匹配只与主阀芯节流口过流面积有关而不受负载影响。整个挖掘机液压系统都在AMESim软件中建立,其参数根据某型号挖掘机设定。
AMESim和Simulink联合仿真通过SimuCosim接口实现,在AMESim模型中,输入变量是系统需求流量Q、泵出口压力P、电机输出转矩
。在Simulink软件环境下建立如图5所示的联合仿真模型。
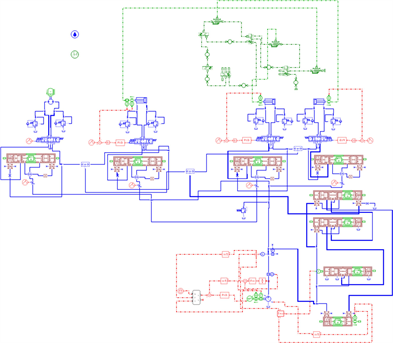
Figure 4. Co-simulation model of electric hydraulic excavator
图4. 电动液压挖掘机联合仿真模型
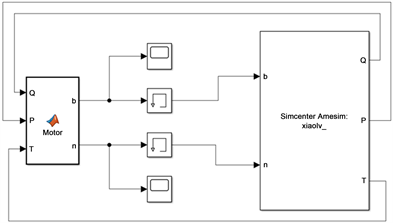
Figure 5. Simulink co-simulation model
图5. Smulink联合仿真模型
5. 仿真及结果分析
5.1. 挖掘机工况及压差分析
本研究以挖掘机挖掘、满斗举升、回转、卸载、空斗回转、动臂下降这一典型循环为工况,研究在柴油机驱动、定速电机驱动以及所提出控制策略驱动下,挖掘机的运动特性以及能耗情况。实现这一工况时动臂液压缸、斗杆液压缸、铲斗液压缸的位移以及马达回转角度曲线如图6所示。
变转速控制时各执行器压力及泵出口压力如图7所示,可以看出泵出口压力与最大负载压力保持一定的压差,证明控制策略的可行性,可以通过变转速变排量来实现系统全范围的流量匹配,在最大程度上避免流量饱和现象发生的前提下提高了系统的操控性。
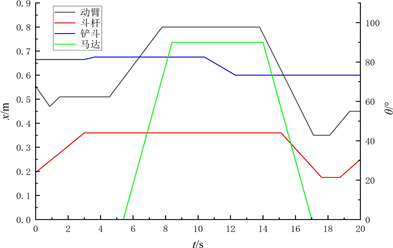
Figure 6. Displacement diagram of typical operating conditions for actuators
图6. 典型工况执行器位移图
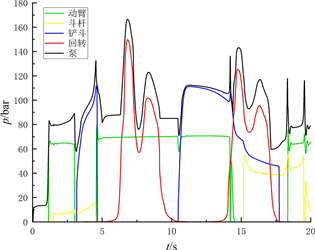
Figure 7. Actuator and pump pressure chart
图7. 执行器及泵压力图
5.2. 运行特性分析
为了验证控制策略的节能性,对其能耗进行分析。图8为实现图6这一典型工况时,不同驱动方案的转速变化图。可以看出发动机的转速有小幅度波动,维持在1800 r/min左右;定速电机维持在1600 r/min;变转速驱动时,在挖掘阶段电机转速保持在750 r/min以上,动臂提升阶段电机最高转速为1700 r/min,回转复位阶段,马达加速,其他执行器几乎没有运动,此刻电机转速最低约为620 r/min。
5.3. 能耗和成本分析
发动机在稳态运行时,其燃油消耗率
可以表示为转速
和扭矩
的函数,并且可以通过二维多项式来表示:
(12)
(13)
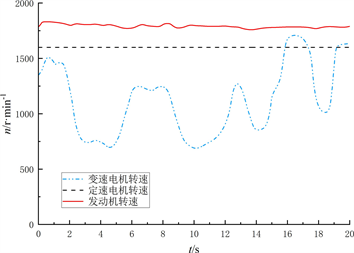
Figure 8. Engine and motor speed curves under typical operating conditions
图8. 典型工况下发动机和电机转速曲线
根据发动机万有曲线图,发动机油耗
可以表示为:
(14)
电机功率
根据仿真模型输出的电机转速和转矩计算,当液压挖掘机的运行时间为
时,电机能耗
为:
(15)
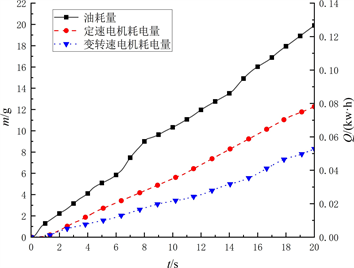
Figure 9. Diesel engine and electric motor energy consumption chart
图9. 柴油机和电机能耗图
在完成同一工况循环,相同工作时间下,根据上述式(16)计算出发动机驱动时的燃油消耗量,根据式(17)计算出电机定速驱动和变转速驱动时的能耗,结果
如图9所示。可以看出在20 s的循环下,发动机驱动燃油消耗19.90 g,定速电机驱动耗能0.0781千瓦时,变转速电机驱动耗能0.0528千瓦时。相比于定速电机,变转速电机在工况循环中的节能量百分比曲线如图10所示。
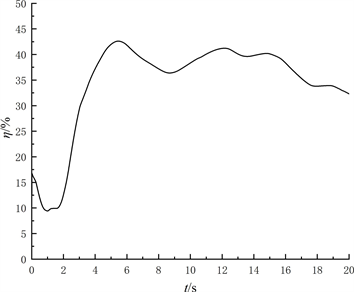
Figure 10. Variable speed motor energy savings percentage curve graph
图10. 变转速电机节能百分比曲线图
为了更加准确地说明控制策略的节能性,本文对三种控制策略的成本进行比较。按照柴油价格7.52元/升,电费1.2元/(kw·h)来计算,挖掘机工作1小时,发动机驱动运行成本为31.68元,定速电机驱动运行成本为16.87元,控制策略控制电机驱动成本为11.40元。
综上,采用基于双变动力源系统效率最优的排量自适应控制策略相比柴油机驱动和定速电机驱动,分别节约成本约64%和33%。
6. 结论
针对简单定速电机代替发动机系统中存在的动态响应慢,效率低,能耗高等现象,提出了一种基于双变动力源系统效率最优的排量自适应控制策略。通过仿真结果分析并验证了其可行性,主要结论如下:
1) 采用转速–排量复合控制模式,与传统液压挖掘机具有相同的运行特性,能够满足作业要求;
2) 控制方法发挥了电机良好的调速性能和过载能力,与传统系统相比,该系统压力和流量的动态响应更好,具有良好的控制性能;
3) 与柴油发动机和定速电机驱动相比,采用复合控制模式,运行成本分别降低约64%和33%。