1. 引言
作为二代半导体材料,单晶砷化镓因其禁带宽度较宽、光电转换效率较高和电子迁移率较高等优异的光学性能,被广泛用作半导体激光器谐振腔面的衬底基片 [1] 。半导体激光器谐振腔面的表面质量影响光源的振荡,直接决定半导体激光器的稳定性。因此,提高其加工工艺技术并制备出无损伤的单晶砷化镓解理基面对于获得理想的谐振腔面和提升半导体激光器的性能尤为重要 [2] [3] 。国际上,WASMER等 [4] 发现划片载荷大小及刀具的形状对解理质量具有影响。PARLINSKA等 [5] 发现滑移和位错是砷化镓划片过程中的两种主要形变方式;国内对于砷化镓的相关解理加工技术仍存在很大的空白,急需相关研究进行填补。尽管已有学者从材料性能和新型工艺等方面对砷化镓纳米加工进行了研究 [6] ,但对于其在此过程中的损伤变形仍缺乏清晰的了解,特别是工艺参数,比如速度和材料各向异性对砷化镓在纳米加工中亚表面损伤形成的影响尚未被充分澄清。因此,为了进一步提高砷化镓基激光器的谐振腔制造技术,探究砷化镓在纳米加工过程中表面和亚表面损伤形成的机制演化是我们解决问题的关键。
2. 分子动力学建模
图1是对GaAs进行划刻过程的分子动力学模型。它由边界层,恒温层,牛顿层以及工件组成,其中边界层和恒温层固定,工件被视为刚体 [7] 。最外层的黄色原子是边界层原子,这层的作用是固定工件使它在加工过程中不移动。边界层里面那层原子是恒温层原子,它的作用是模拟实际加工过程中的温度变化,其温度保持在293 K。恒温层原子的温度由朗格万温控器控制 [8] 。恒温层里面那层原子是牛顿层原子,由GaAs组成。牛顿层原子是自由的,其运动规律符合牛顿第二定律。磨料的初始位置为工件上表面前方2Å。工件尺寸为40 nm * 16 nm * 17 nm。总共包含约八十四万个原子,其中牛顿层约四十八万个,由Atomsk软件进行建模;而其余原子如边界层、恒温层以及工件均由Lammps软件进行建模。
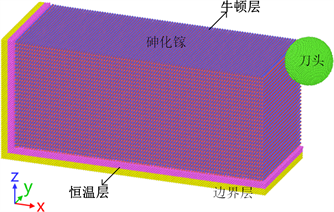
Figure 1. Molecular dynamics simulation model of GaAs
图1. 砷化镓分子动力学仿真模型
为了观察晶体各向异性对加工质量的影响,GaAs单晶的加工方向包括GaAs[010]、GaAs[110]和GaAs[111]晶体取向。如图2所示,灰色的平面即为晶面,与平面垂直的直线即为对应的晶向,如红线所示。对于GaAs[010]取向,取x-[100],y-[010],z-[001]坐标系。对于GaAs[110]取向,坐标系为x-[1-10],y-[110]和z-[001]。对于GaAs[111]取向,坐标系为x-[2-1-1],y-[111],z-[0-11]。加工方向沿x轴方向。为了尽可能地模拟实际情况,x轴方向采用周期边界条件,y轴和z轴方向采用自由边界条件。其余相关参数如表1所示。
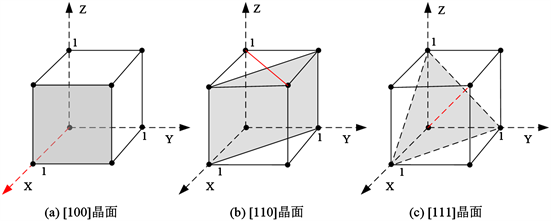
Figure 2. Crystal face and crystal orientation diagram
图2. 晶面与晶向示意图
分子动力学模拟的另一个重要方面是势函数的选择。本文采用Bond-Order势函数对工件内Ga-As原子之间的相互作用进行了模拟。刀头内碳原子之间的相互作用用Tersoff势函数来描述。当工件中的Ga和As原子与刀具中的C原子存在相互作用时,采用Ziegler-Biersack-Littmark (ZBL)势函数来表示这种相互作用 [9] [10] 。这些势函数在模拟砷化镓纳米材料中得到了成功和广泛的应用,使它们成为模拟中准确捕捉原子相互作用的可靠选择。
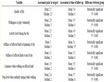
Table 1. The parameters of molecular dynamics model and simulation and values
表1. 关于分子动力学模型和仿真的各参数及其对应值
Bond-Order势函数表达式为:
式中,
为排斥项势能;
和
为sigma和
化学键的积分;
和
为sigma和
的键序。
Tersoff势函数表达式为:
式中,
为截断函数;
为排斥项势能;
为化学键强度;
为吸引项势能。
ZBL势函数表达式为:
式中,e为电子电荷;
为真空介电常数;
和
分别为两个原子的核电荷;
为屏蔽方程;a为屏蔽距离。
在计算磨料与工件之间的相互作用力时,将磨料视为非原子。磨料与工件之间的相互作用力可表示为 [11] :
其中,k为力常数,k = 10 ev/Å3 [12] 。R为磨料半径,r为工件上原子与磨料中心之间的距离。
3. 不同速度下的表面损伤分析
速度是影响纳米加工过程的一个重要因素,不仅仅是因为加工速度的改变会影响砷化镓的表面形貌,同时提高加工速度可以使加工时间变短,从而提高效率。因此,为了研究不同划擦速度对砷化镓纳米划擦过程的影响规律,本节将分析在三种不同的速度(100 m/s、200 m/s、300 m/s)下砷化镓的表面损伤和材料去除的不同,以及不同的速度对不同晶向的影响。
对于表面损伤,本文将采用两个评价指标:
1) 在划片过程中,受到刀头与工件之间的挤压,原子间共价键断裂,晶胞结构被破坏,形成大量非晶原子(Amorphous atoms),非晶原子可被视为材料表面损伤 [13] ,而最大损伤宽度即为工件表面非晶原子层宽度。因此第一个指标就是最大损伤宽度。
2) 表面去除率也是一个用来衡量表面损伤重要的指标,在本文中,我们将采取堆叠高度来量化表面去除率,以此将其作为第二个指标。
3.1. 最大损伤宽度分析
图3分别展示了不同划擦速度下(100 m/s、200 m/s和300 m/s分别对应图中的a、b和c),砷化镓工件表面的原子位移图(左)和最大损伤宽度图(右)。从图中可以看出,原子移动较大的区域主要还是分布在刀头的两侧,只是由于刀头的速度不同而导致了原子位移程度的不同。随着速度的增加,原子受到更强的力,令原子的运动速度提高,从而产生了更大幅度的位移。此外,经过对右图的测量,发现不同速度下的最大损伤宽度分别为121.2、119.8、118.8,随着速度的增加其最大损伤宽度有小幅度的减少,但基本可以忽略不计。但其可能的原因是随着速度的增加,更多的原子有了向前运动的趋势,而不是向两边运动,从而使得最大损伤宽度有了小幅度的减小。
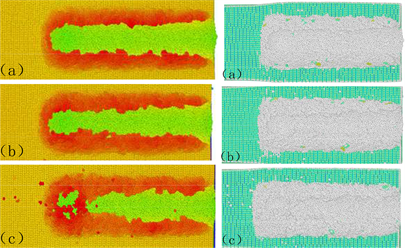
Figure 3. Comparison of scratch damage of GaAs[110] crystal direction at different velocities
图3. 不同速度下GaAs[110]晶向的划痕损伤对比
此外,另外两个晶向的不同速度下的砷化镓划刻过程也被研究了,如下图4和图5所示。GaAs[100]晶向的最大损伤宽度随着速度的增加依次为126.5、125.7和122.3,而GaAs[111]晶向的最大损伤宽度随着速度的增加依次为111.4、10.3和103.3。可以看出,三个晶向的最大损伤宽度都随着速度的增加而减小,这说明随着速度的增加最大损伤宽度会有小幅度的减少这一规律在砷化镓的三个晶向上均适用。这是因为速度的增加使得原子受到了更多向前的力,从而令原子向前运动的趋势增强且向两侧运动的趋势减弱,使得砷化镓的最大损伤宽度小幅减小。此外,速度的增加还会使各晶向上的特性放大,例如GaAs[100]晶向的特性是原子更容易聚集在刀头的前面,而速度的增加使得聚集在刀头前面的原子更多;GaAs[100]晶向的特性是原子更容易聚集在刀头的下面,形成不对称的堆叠,而速度的增加使得这种不对称性更加明显。这些观察结果表明了速度对于砷化镓在不同晶向上的加工特性的影响。
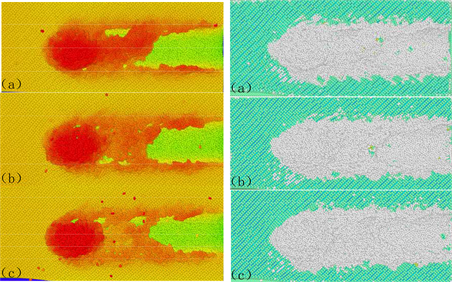
Figure 4. Comparison of scratch damage of GaAs[100] crystal direction at different velocities
图4. 不同速度下GaAs[100]晶向的划痕损伤对比
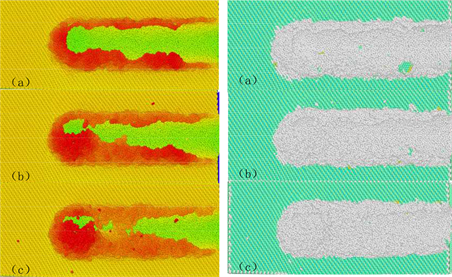
Figure 5. Comparison of scratch damage of GaAs[111] crystal direction at different velocities
图5. 不同速度下GaAs[111]晶向的划痕损伤对比
3.2. 表面去除率分析
观察上图3、图4和图5可以看出,在不同的加工速度下,刀头的两侧以及前方都会有大量的原子堆叠。而随着速度的增加,原子堆叠越加杂乱,这说明,提高加工速度会降低表面质量,但可以提高材料的表面去除率,这一点可以从下图6得出,其堆叠高度随着速度的增加依次为40.2、40.9、46.7。这表明在砷化镓的纳米加工中,适当的增加加工速度可以提高材料的去除率,但同时却也会降低其表面质量。同时,经过对另外两个晶向的研究发现,适当的增加加工速度可以提高材料的去除率,但同时却也会降低其表面质量这一规律同样对三个晶向具有普适性。下图为三个晶向下不同速度的堆叠高度。
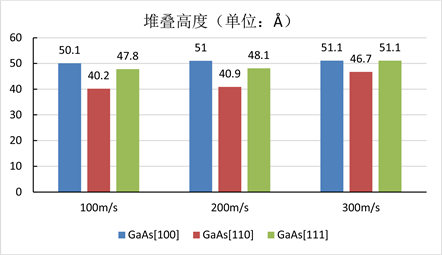
Figure 6. Stack height at different speeds
图6. 不同速度下的堆叠高度
4. 不同速度下的亚表面损伤分析
亚表面损伤层会显著降低砷化镓材料的力学性能,及材料后续的可加工性 [14] 。因此,为了降低砷化镓在加工时亚表面的损伤,了解有哪些要素会影响砷化镓的亚表面损伤层是很有必要的,所以本节将探讨不同划擦速度(100 m/s、200 m/s和300 m/s)下砷化镓亚表面损伤的不同。
对于亚表面损伤,本文同样采用两个评价指标:
1) 随着压头的向前移动,亚表层内会出现大量非晶态原子、位错和闪锌矿相原子等缺陷,进而形成亚表面损伤层。而亚表面损伤会显著影响材料的性能 [15] [16] 。其中,亚表面损伤的厚度是衡量纳米加工后工件损伤程度和加工质量的关键参数。
2) 在加工的过程中,亚表层中会形成了大量间隙原子、空位缺陷、位错和层错等多种缺陷。其中位错是砷化镓在纳米加工中最为显著的一种缺陷,因此加工过程中的位错总长度将是评价亚表面损伤的第二个指标。
4.1. 最大损伤宽度分析
图7(a)~(c)为GaAs[110]晶向不同划擦速度下砷化镓亚表面损伤层示意图,其损伤深度随着速度的增加依次为69.8、68.6、67.6。从数据可以知道,随着划擦速度的增加,砷化镓亚表面损伤层的厚度有减少的趋势,其可能的原因是随着速度的增加,原子向上的运动趋势加剧,使得原子向下的趋势减弱,从而使得亚表面损伤的减小。
同时,另外两个晶向的亚表面损伤深度也被研究了,如下图8所示,可以看出,GaAs[100]晶向的亚表面损伤层深度对速度的变化并不敏感,而GaAs[111]晶向的损伤层深度也随着速度的增加减少。其可能的原因是GaAs[100]晶向的原子堆叠集中在刀头处,而另外两个晶向原子堆叠集中在两边或者单边,集中在刀头处的原子堆叠比另外两个晶向更加密集而使得GaAs[100]晶向的亚表面损伤层深度对速度的变化并不敏感。
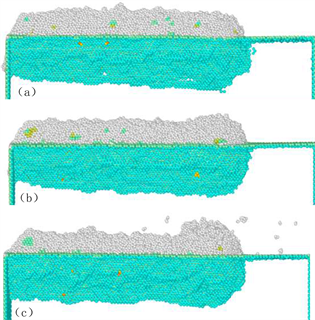
Figure 7. Diagram of subsurface damage depth
图7. 亚表面损伤深度示意图
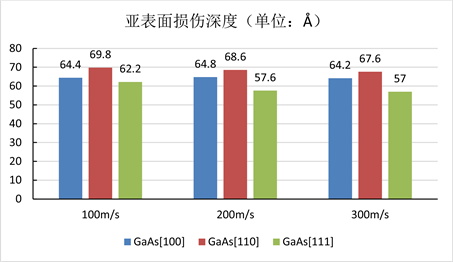
Figure 8. Subsurface damage depth at different velocities
图8. 不同速度下的亚表面损伤深度
4.2. 位错分析
图9展示了纳米划擦后,砷化镓亚表面内缺陷的组成情况。随着划擦的进行,刀头破坏了砷化镓完整的晶格结构,形成了大量的非晶原子。这些原子中的一部分会脱离主体,形成间隙原子,从而产生了空位缺陷(见图9(Ⅱ))。而又因为内力的存在下,部分间隙原子将会往空位处运动,又形成了完整的晶格结构或原子簇,从而令我们观察到部分间隙原子和空位缺陷恢复的情况。而当这种填充运动沿着固定方向扩展时,就会形成各种层错和位错(见图9(Ⅲ)和图9(Ⅳ))。这些缺陷相互作用,共同形成了砷化镓的亚表面损伤层。除了上述缺陷外,工件亚表层还存在一部分与金刚石结构相同的闪锌矿相砷化镓转变为六方纤锌矿相砷化镓(见图9(Ⅰ))。这是因为这两种结构的形成能非常接近,两相之间的能量差约为6.40 ev。因此,随着划擦距离的增加,工件的压力和内部温度逐渐升高,高温降低了能量差;在高压诱导下,砷化镓实现了从闪锌矿相到纤锌矿相的转变。此外,六方闪锌矿相砷化镓和六方纤锌矿相砷化镓会共同存在一段时间。
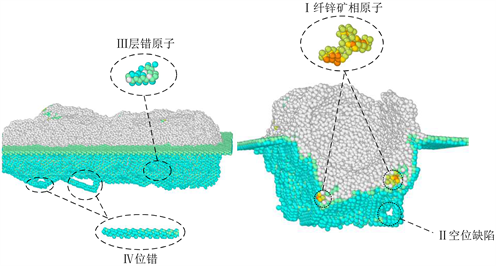
Figure 9. Types of defects in GaAs during scratching
图9. 划擦时砷化镓内缺陷类型
图10(a)-(c)为不同划擦速度下砷化镓亚表面损伤层内位错长度的示意图,图10(d)是速度为300 m/s下的纤锌矿相原子和位错的示意图。如图所示,亚表层内其余位错(除完美位错外的其他位错总和)和纤锌矿相原子数呈正相关关系。同时,由下图11可知,随着速度的增加,位错的长度有着减小的趋势,这是因为亚表层内部分位错由于没有持续的力和能量驱动,也没有足够的时间进行形核及滑移扩展运动,进而导致位错长度有所降低。因此,我们可以得出结论,不同的划擦速度对砷化镓亚表层中的位错类型基本没有影响,但对各类位错的长度影响明显。
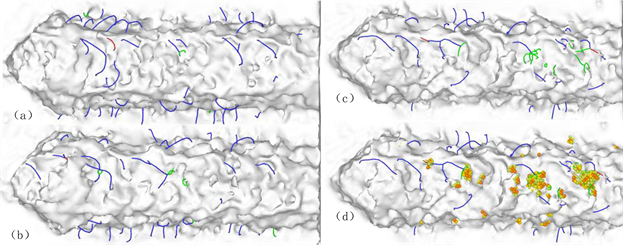
Figure 10. Dislocations of GaAs at different scratch speeds
图10. 不同划擦速度下砷化镓的位错
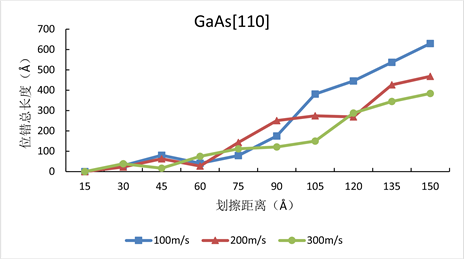
Figure 11. Total length of dislocation of GaAs[110] at different scratching speeds
图11. 不同划擦速度下GaAs[110]的位错总长度
同时,另外两个晶向的位错总长度与速度之间的关系也被研究了,如下图12和图13所示。可以观察到,对GaAs[100]这一晶向而言,随着速度的增加,位错的长度会减小这一规律仅在100 m/s到200 m/s适用,而在200 m/s到300 m/s中国区间位错的总长度会提高,而对GaAs[111]这一晶向同样适用。其原因同样可能是因为GaAs[100]这一晶向的原子容易堆叠到刀头处这一特性,过快的速度会使得向下的原子有着更强大的破坏力,从而造成更多的位错。这意味着在实际加工中,GaAs[100]这一晶向并不能一味地通过适当的提升加工速度来提升砷化镓的亚表层质量,而应该选择合适的加工速度。
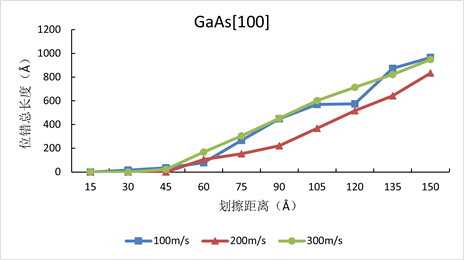
Figure 12. Total length of dislocation of GaAs[100] at different scratching speeds
图12. 不同划擦速度下GaAs[100]的位错总长度
5. 结论
本文从最大损伤宽度、表面去除率、位错种类、位错长度以及亚表面损伤层厚度等多个角度分析了砷化镓纳米划擦过程中表面与亚表面损伤的形成演化机制,并详细对比研究了在不同速度下对砷化镓纳米加工中表面损伤以及亚表层损伤的影响。主要结论如下:
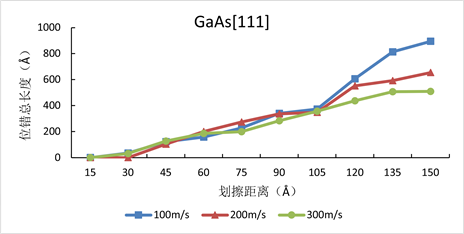
Figure 13. Total length of dislocation of GaAs[111] at different scratching speeds
图13. 不同划擦速度下GaAs[111]的位错总长度
1) 研究发现,增加加工的速度可以减小最大损伤宽度,这一点适用于三个晶向,但对不同的晶向而言,速度的增加同时也意味着其原子堆叠的特性增强;同时,高速加工会使原子的堆叠高度提升,有利于提高材料去除率,但却会使表面质量略微降低,同样适用于三个晶向。
2) 随着划擦速度的增加,砷化镓亚表面损伤层的厚度会减小,这一点仅适用于GaAs[110]和GaAs[111]晶向,GaAs[100]晶向的亚表面损伤层厚度对速度的变化并不敏感;同时,对于位错而言,GaAs[110]和GaAs[111]晶向划擦速度的增加会减小砷化镓亚表层中的完美位错长度和总长度,但对位错类型基本没有影响,而GaAs[100]晶向不能一味地增加速度来减少位错,过快的速度会加大该晶向位错的产生。