1. 引言
由于飞机使用条件特殊,经常处在高温高湿的环境中,发动机进口环境恶劣复杂,如沙尘、盐雾、粉尘、昆虫、油类等天气,长期使用致使发动机各部件型面如压气机和涡轮叶片积尘、腐蚀、几何变形等 [1] [2] ,各项性能指标将随着部件性能的下降而恶化,进而严重影响发动机整机的性能。上面所述部件失效机理都是有代表性的,任何一种失效形式,在一定程度上都会导致叶片表面粗糙度的变化。随着叶片表面粗糙度的改变,压气机气流通道的流通能力,以及压气机的压比和效率随之改变,从而进一步引起发动机推力下降,耗油率升高以及稳定工作范围进一步减小,从而增加后期维护成本 [3] [4]。
国外对这方面研究的较早,主要是通过实验手段进行研究,取得了一系列有意义的研究成果 [4]。Suder 通过在NASA Stage35高速压气机叶片表面增加粗糙度和叶型厚度的方法,详细研究了污垢沉积下的叶片粗糙度改变和厚度增加对压气机性能与流场分布的影响 [5]。国内学者对压气机叶片粗糙度对其性能影响做了积极的研究。李本威等研究了压气机叶型改变导致其性能下降的情况。采用在易积垢部位增加随机尺寸的方法近似模拟叶片积垢等原因引起的叶型改变,并分析了叶片积垢、叶顶间隙增大等因素对压气机性能的影响,通过仿真得到压气机在各种不同工况下性能衰退程度 [6]。李钊等针对压气机工作过程中叶片表面积垢对压比、效率的影响,将积垢影响换算成压气机叶片粗糙度的变化,分别对积垢分布在叶片前缘、吸力面与压力面以及在不同转速下的压气机性能进行了仿真计算 [7]。郑贇以跨声速风扇Rotor 67转子叶片在气动载荷下的变形为例,分析了叶片变形对风扇气动性能变化的影响 [8]。陈绍文通过对污垢沉积引起的叶片厚度和壁面粗糙度的增加来模拟不同的污垢沉积程度对压气机级性能的影响,两种模拟方法较真实地还原了叶片表面的积垢情况,计算结果具有一定的指导意义 [9]。
本文在上述研究基础上,通过改变叶片粗糙度近似模拟叶片积垢、腐蚀对叶片型面的影响,带入到建立的模型中去,仿真计算压气机气流流场变化,研究叶片表面粗糙度变化后,比较三种粗糙度对应的压气机性能参数、特征截面参数以及总体性能的变化情况。详细描述和分析了不同转速和粗糙度下的叶片表面的激波位置和分离位置变化。
2. 数值方法
在标准大气条件下,仿真计算压气机在稳定工作状态下的性能参数。这是后续研究分析的基础。因此控制方程采用时均湍流模型进行燃气流场计算,其形式如下:
(1)
根据文献 [10] 比较分析,确定湍流模型采用
模型,它是个半经验公式,主要基于考虑湍流动能和扩散率。采用
湍流模型计算流动的湍流效应。k方程表示如下:
(2)
e方程是个由经验公式导出的方程:
(3)
方程中Gk表示由层流速度梯度产生的湍流动能,Gb是由浮力产生的湍流动能,YM由于在可压缩湍流中,过渡扩散产生的波动,C1,C2,C3是常量,
和
是k方程和e方程的湍流Prandtl数。
3. 粗糙度的描述
叶片粗糙度直接影响近壁面区域湍流的产生和发展,从而对附面层厚度变化产生影响,改变气流流场整体粘度,最终引起部件流通能力、做功能力的变化。以叶片粗糙度变化代替积垢、腐蚀、侵蚀等因素的影响,这里引入等价粗糙度这个概念,研究其对叶片光洁度的影响。
叶轮部件长期工作后,由于积垢和腐蚀等原因,叶片表面存在不同形状和大小的凸起或者凹陷,本文使用壁面沙粒粗糙度模型来近似描述叶片粗糙度 [11] ,如图1示。使用的沙粒粗糙度可以被划分为三种类别:
1) 近于光滑壁面:
;
2) 过渡粗糙壁面:
;
3) 完全粗糙壁面:
。
图1所示的沙粒粗糙度模型,模型认为粗糙度具有收缩效应,如果沙粒的大小为hs,此时模型中的粗糙度为
。随着hs的增大,近壁面气流层流底层损失非常快,极大增强壁面附近的湍流粘性。计算过程中,利用改进的壁面函数将壁面嵌入到流场分析中,从而计算叶片粗糙度对其性能的影响。考虑粗糙度影响的近壁面速度修正公式表示如下:
(4)
式(4)中,
表示近壁面速度函数,
表示近壁面的无量纲距离,k表示冯·卡门常数,C是依赖壁面粗糙度的自然对数底参数,又有
(5)
式(5)中,
表示沙粒粗糙度模型中的粗糙度。
4. 模型的建立与求解
4.1. 模型建立
本文以轴流式发动机的压气机为研究对象。根据压气机三维叶型数据,建立实体计算模型,叶片实体模型共分成21个截面,每个截面280余个点,合计6000余个点。叶型的子午视图、三维视图、轮毂面和机匣面视图如图2所示。
在前处理模块中读取模型文件,对模型进行网格划分。叶型及其延伸段模型网格拓扑结构选取设置成HOH型网格 [12] ,其中叶片前、后延伸段为H型网格,叶片型面附近采用O型网格设置,其中沿轴向、径向和周向方向前后延伸段节点设置为33 × 61 × 97,叶片型面附近节点设置为49 × 61 × 99,端壁和叶片表面第一层网格尺度为0.00001 mm,这样做,可以保证壁面第一层网格0< y+ ≤ 10。
压气机模型建立后,仿真计算标准状态下的参数,利用性能参数计算数值与设计数值进行对比验证,检验所建压气机模型的精度。计算发现,在标准状态下的效率和压比最大相对误差为1.59%和1.95%,在允许的误差范围内。因此所建模型有效。
4.2. 仿真计算
在求解器中进行流场计算。由于计算是在稳态情况下进行的,并且各个通道流通情况完全相同,所以本文以单通道进行计算。在计算模型中,选定流动介质类型为理想气体;转速为设计转速;进一步设定边界条件:进口条件为标准大气,给定气流的总压为101,325 Pa、总温为288.15 K,出口条件为给出指定半径处的静压值;同时设置细网格计算和CFL数等相关参数;固壁为绝热、无滑移边界条件,叶片模型进出口延伸段为周期性边界条件。为提高计算效率和准确度,采用多重网格法、当地时间步长和残差光顺等技术加速计算过程的收敛速度。仿真计算时,在设计状态下,通过逐渐增加出口静压值向失速点推进,得到压气机的特性曲线。计算第一个数据点时,指定出口条件为给定出口处静压的估计值,其余计算点取前一工况的计算结果为初场设置值,数值失速前的最后一个收敛解对应着近失速工况。
5. 仿真结果与分析
叶片表面粗糙度变化,将会改变压气机流道壁面边界层的发展趋势。随着压气机叶片粗糙度的降低,流道内流动状况将随之得到改善,带来压气机性能上的提高。本文通过降低压气机叶片表面粗糙度的方法来定量研究叶片表面粗糙度对压气机特性的影响,以获取相关的作用机理和影响规律,从而进一步提高对叶片表面粗糙度影响的认识。
图3、图4和图5给出了100%、90%和80%设计转速下压气机在粗糙度降低前后的特性曲线。由图可知,叶片表面粗糙度的降低将导致压气机的增压比和效率显著提高,并且当效率达到最高点后,压气机的增压比和效率将下降明显。压气机的增压比随着转速的减小而减小,效率随着转速的减小而增大。通过对比可知,压气机的增压比和效率的提高幅度随着转速的降低而减小。
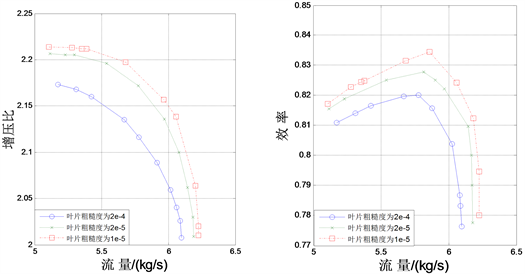
Figure 3. The effect of different roughness on compressor characteristics at 100% rotating speed
图3. 不同粗糙度对转速为100%时压气机特性的影响
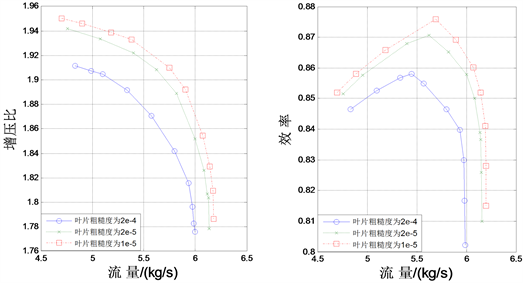
Figure 4. The effect of different roughness on compressor characteristics at 90% rotating speed
图4. 不同粗糙度对转速为90%时压气机特性的影响
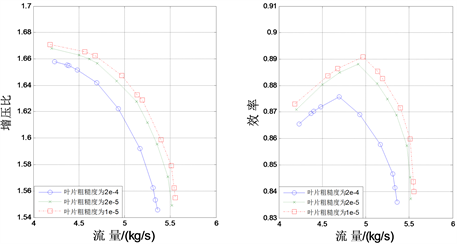
Figure 5. The effect of different roughness on compressor characteristics at 80% rotating speed
图5. 不同粗糙度对转速为80%时压气机特性的影响
叶片表面粗糙度的变化也会影响到各转速工况下压气机稳定工作流量的范围。随着粗糙度的降低,压气机稳定工作流量的范围明显扩大。
超音速气流同亚音速气流相比较,有一个重要的特点,即超音速气流在绕物体流动而被压缩时往往出现跳跃的压缩波,气流通过这种压缩波时,压力、温度、密度均突跃地上升,流速或马赫数则突跃地下降,气流受到突然的压缩,这种突跃的压缩波就叫激波。激波会造成能量的损失。
图6、图7、图8给出了100%、90%、80%设计转速下,50%叶高位置处的S1面马赫数分布云图。由图可见,随着叶片表面粗糙度的减小,吸力面侧激波的位置向叶片出口方向移动,且激波的强度下降,气流密度较之以前有所减小,使得激波作用引起的气流分离推迟发生,进一步使得叶片的尾迹区范围减小,这是压气机性能改善的主要原因。随着转速的下降,激波强度下降明显,尾迹区范围相应减小。
(a) ks = 2e−4
(b) ks = 2e−5
(c) ks = 1e−5
Figure 6. The influence of different roughness on shock wave on blade surface when rotating speed is 100%
图6. 不同粗糙度对转速为100%时叶片表面激波的影响
(a) ks = 2e−4
(b) ks = 2e−5
(c) ks = 1e−5
Figure 7. The influence of different roughness on the shock wave on blade surface when rotating speed is 90%
图7. 不同粗糙度对转速为90%时叶片表面激波的影响
(a) ks = 2e−4
(b) ks = 2e−5
(c) ks = 1e−5
Figure 8. The influence of different roughness on the shock wave on blade surface when rotating speed is 80%
图8. 不同粗糙度对转速为80%时叶片表面激波的影响
随着叶片表面粗糙度的降低,叶片表面摩擦系数
减小 [13] ,摩擦阻力也随之减小,当气流流过叶片表面后,摩擦产生的热能也随之减少,致使叶片表面的总温有不同程度的降低。
图9、图10、图11分别给出了100%、90%、80%设计转速不同粗糙度下流场中叶片表面总温的分布情况。由图可知,叶片顶部的总温比叶片底部大,则叶片顶部承受着更大的热载荷。随着叶片表面粗糙度的降低,压气机入口和出口总温减小,入口变化比较明显,出口总温变化不大,叶片表面平均承受的热载荷有所减小,叶片表面总温的降低幅度从叶片底部到叶片顶部依次减小,随着转速降低依次减小。
(a) ks = 2e−4
(b) ks = 2e−5
(c) ks = 1e−5
Figure 9. The influence of different roughness on the total temperature on blade surface when rotating speed is 100%
图9. 不同粗糙度对转速为100%时叶片表面总温的影响
(a) ks = 2e−4
(b) ks = 2e−5
(c) ks = 1e−5
Figure 10. The influence of different roughness on the total temperature on blade surface when rotating speed is 90%
图10. 不同粗糙度对转速为90%时叶片表面总温的影响
(a) ks = 2e−4
(b) ks = 2e−5
(c) ks = 1e−5
Figure 11. The influence of different roughness on the total temperature on blade surface when rotating speed is 80%
图11. 不同粗糙度对转速为80%时叶片表面总温的影响
6. 结论
本文利用流场仿真技术,将叶片腐蚀和积垢原因导致的叶片型面改变,近似看成叶片粗糙度的变化,通过在模型中修改叶片粗糙度设置的方法研究压气机叶片粗糙度增加对其性能的影响。得到的主要结论如下:
1) 叶片表面粗糙度的降低,这将导致压气机增压比和效率显著提高,扩大了压气机稳定工作范围,改善压气机总体工作特性,提高了压气机自身做功的能力,减少了流动损失。
2) 随着叶片表面粗糙度的降低,吸力面侧激波的位置向叶片出口方向逐渐移动,且强度减小明显,进一步使得叶片的尾迹区范围减小。
3) 随着叶片表面粗糙度的降低,叶片表面总温有不同程度的降低。当叶片粗糙度降低后,叶片表面总温的降低幅度从叶片底部到叶片顶部依次减小,随着转速降低依次减小。