1. 引言
当前,汽车是人们生活的重要组成部分,车内空气质量对司机及乘员的健康带来很大影响 [1]。医学研究表明,车内恶劣的空气质量会导致司乘人员头晕、困倦、恶心、咳嗽、脱发失眠等症状,长时间乘坐甚至会引起皮肤、呼吸道及神经系统疾病,甚至提高癌症的发病率 [2] [3]。因此,控制车内空气污染,对于规范和引导汽车及相关产业可持续性发展,促进汽车产业加快结构调整和技术升级,保护消费者的身体健康具有重要意义 [4]。
国家法规和行业标准促使汽车向健康环保方向发展。我国于2007年底发布了《HJ/T 400-2007:车内挥发性有机物和醛酮类物质采样测定方法》,并于2008年3月开始实施 [5];2011年10月发布了《GB/T 27630-2011乘用车内空气质量评价指南》,作为管控车内空气质量的指导性文件 [6]。同时,各大主机厂对汽车散发特性和VOC的要求越来越高,例如一汽轿车于2014年发布了《Q/FC-CD05-011-2014车内非金属零件材料苯系物及醛类物质限值要求》标准,一汽大众2016年发布了《Q/FAWVW 0001-2016汽车内饰零部件挥发性有机物散发标准》。
在PP原料方面,许多企业开展了低气味PP树脂的生产研究 [7] [8]。某材料公司开发了一款环保材料,该材料利用5%无机多孔矿物质页岩蛋白石粉替换5%滑石粉对聚丙烯(PP)进行改性,该页岩蛋白石粉可有效吸附聚合物加工过程中逸出的小分子,从而降低产品的气味。我公司将此研发成果在一款轿车门板上进行产品验证,进一步研究此健康环保型低VOC聚丙烯材料的系列性能。
2. 实验部分
2.1. 样品选取
本文基于汽车内饰常用的改性聚丙烯PP/PE-TD20材料,将5%的页岩蛋白石粉替换5%的滑石粉,并对这两种材料进行对比研究,如表1所示,样品由台湾震雄1500吨注塑机制备。
2.2. 检测项目
5%页岩蛋白石粉替换5%滑石粉后,需要在保证材料基本物理和外观性能的基础上,降低散发四项和VOC的数值,表2为主要检测项。
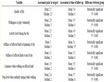
Table 2. Test items and standard
表2. 试验项目及检测标准
2.3. 原理分析
在聚丙烯(PP)改性过程中,通常会加入一些辅助材料和添加剂,如矿物填料、玻璃纤维、相容剂、弹性体及抗氧剂等,这些组分的加入会由于本身的气味或者加工过程中的高温、高剪切而产生气味 [9]。物理吸附从理论上来讲,可以吸附所有挥发出来的小分子化合物。随着物理吸附剂的不断发展,出现了很多的物理吸附体系,包括活性炭体系、硅胶体系、金属氧化物等矿物土体系以及分子筛体系等,当上述系列吸附剂体系以一定形式分布于树脂基体时,它们均能对树脂材料中产生的气味或是挥发性小分子进行吸附 [8]。同样,页岩蛋白石粉的作用原理为物理吸附原理,对改性聚丙烯中挥发的有机小分子进行吸附和捕捉,如图1所示。
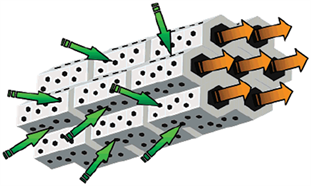
Figure 1. The schematic diagram of sorption
图1. 吸附原理图
3. 结果与讨论
3.1. 添加页岩蛋白石粉后对制件力学性能和熔体流动性能(MFR)的影响
表3为两种材料制件的力学性能和MFR的测试结果,从表中可以看出,由5%页岩蛋白质粉代替5%滑石粉后,材料的密度无变化,拉伸强度、缺口冲击强度、弯曲模量和MFR有所下降,断裂伸长率有所增加,但检测值都在标准范围以内。这说明用页岩蛋白石粉替换部分滑石粉后,力学性能和加工性能是有下降趋势的,所以要保证材料满足标准要求,页岩蛋白石粉的含量要控制在5%以内。
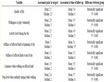
Table 3. Two samples physical properties test results comparison
表3. 两种材料制件物理性能检测结果
3.2. 添加页岩蛋白粉后对制件外观评价的影响
表4和图2为5%页岩蛋白石粉代替5%滑石粉后材料在耐刮擦、耐光照、耐发粘和耐热老化试验后的表面变化。塑料件的耐刮擦性定义为材料本身具有的对机械压力(例如尖锐物体或圆头物体的耐刮擦动作)的抵抗性,采用比色法测量,制件在进行耐刮擦试验后测量值是1.27,满足试验标准要求。耐光照试验是按照PV1303标准对光照后(5个周期)的制件表面进行评价,该评价通过五个等级的灰度尺来判断受光照后制件表面的褪色程度,从5级到1级(灰度)代表受光照后样件的颜色变得越来越浅,也就是褪色程度越来越大。如表4及图2(b)所示,经过5个周期的照射后,制件目视外观质量都满足标准要求,表面无亮斑或发花现象,无可见或可以感觉到的析出物等异常现象,灰度等级为4级,满足要求。耐发粘试验是按照PV1306标准对制件进行5个周期的照射,然后评价制件表面的发粘程度,共分为8个等级。如表4及图2(b)所示,经过5个周期的照射后,样件表面无任何异常变化,不发粘,满足标准要求。耐热老化是在150℃ 400小时的条件下,评价制件是否有表面结构的变化,PP是否有典型的分解。从表中描述和图2(c),图2(d)可看出,耐老化试验后表面无明显变化,由5%页岩蛋白质粉代替5%滑石粉后的改性聚丙烯制件,可以满足系列外观类试验检测要求。
3.3. 添加页岩蛋白粉后对制件散发四项的影响
散发四项是对气味、总碳、雾度、甲醛进行检测。根据PV3900汽车内饰件气味检测标准,气味评价标准可分6级,从表5中数据读出,由5%页岩蛋白石粉代替5%滑石粉后,气味由5级降低到4级。总碳测试的是材料中总的有机小分子挥发物;甲醛的限制主要考虑甲醛的挥发对人体的伤害;冷凝是用来检测温度100℃左右材料中挥发出来的小分子的量,用来模拟车内高温环境下,仪表板等零件中挥发出来的小分子凝结在风挡上对车内环境造成的污染以及对视线造成影响等问题。表5数据表明,制件1#和2#的总碳、甲醛和冷凝测试结果均满足标准要求,但2#件的数值更低。综合来看,5%页岩蛋白石粉代替5%滑石粉,对PP材料的气味等降低起到很大作用。
3.4. 添加页岩蛋白石粉后对制件VOC的影响
VOCs (volatile organic compounds),是指车辆驾驶舱/行李舱内零件或材料散发的挥发性有机化合物,主要包括苯系物、醛酮类物质以及十一烷、乙酸丁酯、邻笨二甲酸酯类等。按照一汽轿车Q/FC-CD05-011标准,用10L袋子评价方法的规定对2种样品进行VOC检测,散发到空气中的苯、甲苯、二甲苯、乙苯、苯乙烯、甲醛、乙醛、丙烯醛的检测结果见表6。从表中数据可看出,由5%页岩蛋白石粉代替5%滑石粉后,除了甲苯的检测值略有升高、苯的检测值保持不变外均大幅度下降。同时,1#样品二甲苯、乙苯和乙醛的检测结果不合格,2#样品测试结果均在标准要求范围内。从VOC测试结果上看,2# 样品是一种低VOC环保型聚丙烯材料。
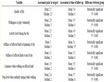
Table 4. 2# Samples appearance properties test results
表4. 2#制品外观性能测试结果
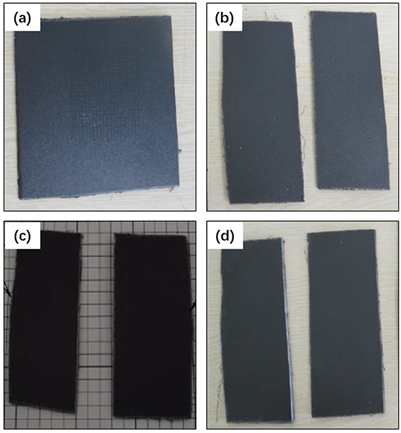
Figure 2. 2# Samples before and after test appearance comparison. (a) Scratch resistant, (b) Light resistant, (c) Sticky resistant, (d) Heat aging resistant
图2. 2#制品外观试验前后对比。(a) 耐刮擦,(b) 耐光照,(c) 耐发粘,(d) 耐热老化
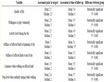
Table 5. Two samples four emission test results comparison
表5. 两种制品散发四项测试结果对比
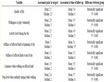
Table 6. Two samples VOC test results comparison
表6. 两种制品VOC测试结果对比
4. 结论
本文基于汽车内饰常用的改性聚丙烯PP/PE-TD20材料,将5%的页岩蛋白石粉替换5%的滑石粉,并对这两种材料进行对比研究。研究表明新材料的物理性能和外观试验检测均满足客户试验标准要求,同时散发四项和VOC检测数值明显降低,说明PP/EP-MD20是一种健康环保低VOC改性聚丙烯汽车内饰材料,可进一步推广应用。