1. 前言
煤泥的主要来源是煤炭生产和洗选加工过程中产生的副产物,由于具有粘湿特性,很难被大规模工业使用,此前长期作为民用能源使用 [1]。大规模工业用途主要是和高热值煤掺混后作为动力煤燃烧使用。但湿煤泥的黏湿特性使其很难被资源化利用,同时也给煤泥的运输和储存带来诸多困难。煤泥堆积形态不稳定,雨天造成大量流失,风干会导致飞扬 [2]。为了解决煤泥黏湿所带来的问题,国内外均采用烘干干燥法处理煤泥,使其失水脆化,方便后续运输和利用。
国内对煤泥的烘干处理研究较多,还未出现对煤泥免烘干处理的研究。近年来低温余热干燥技术贮碱得到推广和应用 [3] [4] [5] ;近年来新兴的微波干燥工艺在国内也开始进行研究 [6] [7] [8] [9] ;中国专利CN106568305A描述了一种高温烟气烘干工艺 [10],这些煤泥处理工艺无一例外地采用了干燥工艺,但这些煤泥的烘干工艺往往伴随着能源消耗以及环境污染问题;随着国内面临的环保形势越来越严峻以及国内环保法规的不断健全,煤泥的烘干受到越来越多的限制,大量的煤泥堆积无法处理,导致国内许多洗煤厂面临限产甚至停产局面,严重影响了洗选煤厂的正常生产。
根据《煤炭清洁高效利用行动计划(2015~2020年)》提出,到2020年原煤入选比例提升至80%以上,届时全国一年将产生2.8亿吨湿煤泥。大量的煤泥若采用传统的热烘干煤泥处理工艺不符合国家的节能减排政策,因此有必要实现一种全新的煤泥免烘干处理工艺,新的免烘干处理工艺,不仅能为国家节省大量能源,还能减少大量的烟尘和废气排放,降低运行成本,具有极佳的社会效益。
通过对煤泥进行了深入的研究,开发了一种全新的煤泥免烘干处理工艺,该工艺采用特殊设计的处理药剂结合配套工艺设备,实现煤泥的免烘干处理。采用本工艺处理后的煤泥状态松散,运输储存不粘,同时不引入重金属和其他有害物质,对煤泥燃烧热值无负面影响,安全环保无污染。
2. 现有处理工艺
2.1. 高温烟气干燥技术
高温烟气煤泥干燥系统主要由燃气热风炉、刮板上料机、滚筒干燥机、传动机构、卸料器、引风机、除尘设备和电控系统构成。
具体干燥工艺过程如下:由压滤装置卸下的湿煤泥经刮板输送机输送到回转圆筒干燥机的筒体内部。与此同时,燃气热风炉内的高温烟气进入筒体内部。煤泥在高温烟气的直接接触下充分传热传质,大量的水分被蒸发,干燥后的煤泥经卸料器排出,完成整个干燥过程,含尘气体经除尘器净化后由引风机排空,干燥成品经输送机输送至成品堆场,其工艺流程见图1。
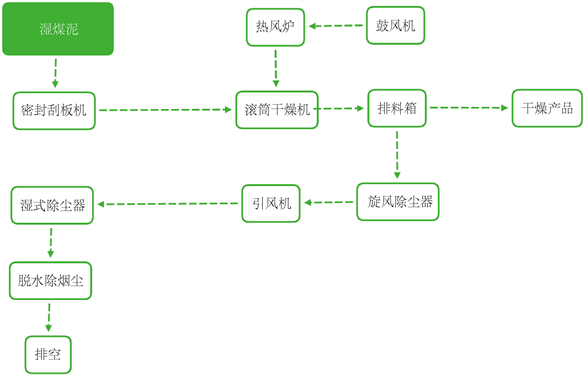
Figure 1. Flow chart of high temperature flue gas drying
图1. 高温烟气烘干流程图
2.2. 低温蒸汽干燥技术
低温蒸汽干燥技术是利用电厂余热蒸汽的汽化潜热加热并干燥煤泥的技术。煤泥蒸发的水分可以通过换热设备进行回收利用。干燥系统主要由打散料仓、皮带上料机、螺旋输送机、蒸汽干燥设备、传动机构、卸料器、引风机、除尘设备和电控系统构成。
具体干燥工艺过程如下:湿煤泥由输送机输送到蒸汽干燥设备内部。与此同时,低压余热蒸汽进入干燥设备。蒸汽与湿煤泥进行间接换热。由于干燥设备与水平线有一定的倾斜夹角,物料进入连续运行的干燥设备后,逐渐由高处向低处移动,最终在低处排料口排出,物料在不断运动的同时与蒸汽进行热交换,蒸发生成的水蒸气由排气口排出,所夹带的细粉料由除尘器回收后经引风机排空。物料在干燥机内的停留时间可由变频调速电机调节,具体工艺流程见图2。
3. 免烘干处理工艺
3.1. 可行性试验
取20%含水率的湿煤泥100 g,按1%的添加比例将自行研发的降粘剂RH101添加至湿煤泥中,使用小型粉碎机粉碎30秒,处理效果见图3。
处理后的煤泥呈松散状态,在施加压力下不团聚,不结块。这证明煤泥免烘干处理在工艺上是可行的,但在实际生产中需要对整个工艺进行设计,同时设备选型要合理,以达到良好的处理效果以及处理效率,同时还要兼顾经济可行性。
3.2. 工业化处理工艺流程
煤泥免烘干处理工艺的本质是煤泥与降粘剂的混合和破碎,但是在工业化生产中,需要考虑设备的稳定、高效运行。因此需要对工业化处理工艺和设备选型进行研究,选择一套合理的流程和设备。
为了便于实现工业化生产以及后期的维护保养,所有的设备均选择市面上常规型号设备。在原有的滚筒烘干设备前端增加双轴剪切破碎设备和螺旋定量输料器,在末端增加锤式破碎设备。其余的设备均使用原工艺现有设备。
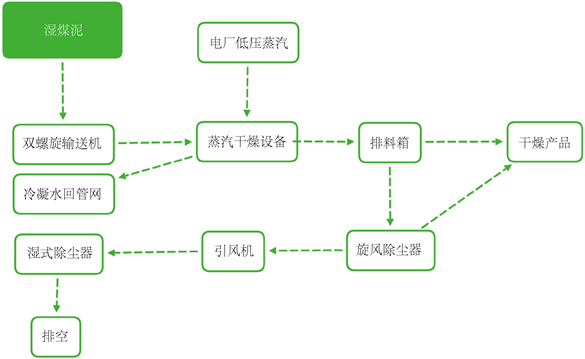
Figure 2. Flow chart of low temperature steam drying
图2. 低温蒸汽烘干流程图
处理前
处理后
Figure 3. Comparison of laboratory slime additions before and after treatment
图3. 实验室煤泥添加药剂处理前后对比
具体工艺流程是湿煤泥经过双轴剪切破碎机破碎成小块煤泥,然后下料至刮板输送机上,位于刮板输送机上方的螺杆定量投料设备将预先按比例混合好的降粘剂和掺混料输送至刮板上的煤泥上面,掺混降粘剂和掺混料的小块煤泥在滚筒烘干机内不断翻滚和混合然后在末端下料至皮带输送机,由皮带输送机输送至锤式破碎机做进一步混合破碎,碎料通过带式输送机输送至滚筒筛分机进行筛分出料。湿煤泥免烘干处理的工艺流程见图4。
首先湿煤泥经过双轴剪切破碎机破碎成小块煤泥,然后通过螺旋定量输料器将煤泥降粘剂添加至小块煤泥中,混合料通过皮带输送机输送至锤式破碎机进行混合破碎,破碎后的成品经过皮带输送机输送至成品堆场。
在宝丰县彭庄货场,七星洗煤厂按此工艺使用中试设备已经处理了3000多t湿煤泥,经过配煤后全部送至平顶山鲁阳电厂使用,产品的储存性、运输性、热值和有害物含量全部符合使用要求。工业化处理后的煤泥见图5。
由图5可以看出,处理后的煤泥呈松散状态,颗粒分明,平均粒径小于或等于50 mm,即便长时间堆积也不会导致煤泥再次团聚,证明煤泥免烘干处理工艺是有效可行的。
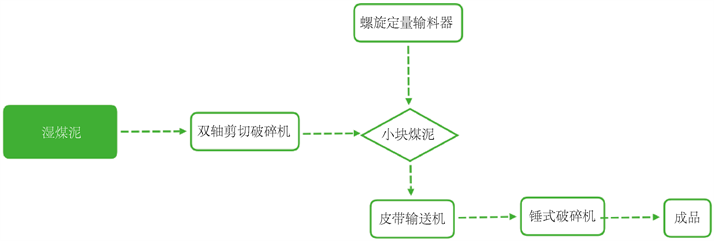
Figure 4. Process flow of drying and drying of wet concrete slime
图4. 湿煤泥免烘干处理的工艺流程
4. 成本分析
4.1. 社会效益
为响应国家号召,国内大多数洗煤厂的煤泥烘干热风炉都完成了“煤改气”改造,在《煤炭清洁高效利用行动计划(2015~2020年)》提到,至2020年,原煤入选比例提升至80%以上,以现在原煤产量计算,届时全国一年将产生2.8亿吨煤泥需要处理,消耗天然气28亿立方。同时我国能源结构最主要的特点就是“富煤、缺油、少气”,目前天然气进口依存度为40%左右,预计到2050年,进口依存度将达到78.5%。国家能源安全问题迫在眉睫。若采用现有的干燥工艺,使用高级能源来制造低级能源,不仅仅是本末倒置造成巨大的能源浪费和环境污染,还会进一步加剧国家天然气紧缺的局面。新的煤泥免烘干处理工艺在全国推广开来,将会对国家的经济、环境保护以及能源安全都产生重大意义。
4.2. 经济效益
采用烘干法处理一吨湿煤泥需要消耗燃气12立方,燃气成本60元/吨,人工成本20元/吨,综合成本为80元/吨;按照醋酸钙市场价4000元/t、101ZX的综合成本5500元/t、降粘剂组分比例为101ZX:醋酸钙= 9:1计算,降粘剂的综合成本为5350元/t;按降粘剂向湿煤泥中的添加比例为8.9‰计算47.6元/t,加上人工等其他成本20元/t,综合成本约为67.6元/t。平煤股份每年需要处理200万吨湿煤泥,综合节省成本:2480万元。
5. 结论
研究表明,吸/固水成分选择101ZX树脂、脱水助剂选择醋酸钙、且二者比例为9:1、降粘剂添加量为湿煤泥质量的8.9‰时,可以达到理想的脆化效果,同时又兼顾了经济性,处理成本约为77.6元/t。
经过工业性试验,此工艺生产过程稳定,处理效率高,处理后的煤泥松散,堆积、运输不粘。
煤泥免烘干处理工艺相对于烘干法,无论在处理成本还是环保方面都具有巨大优势,免烘干处理法,不燃烧化石燃料,无烟尘尾气排放,具有非常好的推广前景。