1. 引言
钒是一种重要的战略金属,由于其独特的物理性能,如抗拉强度,硬度,抗疲劳性等,常用于合金。石煤是最重要的含钒资源,其中钒主要以同晶形式存在于云母族矿物的晶格中。钒以元素的形式存在于自然界中。石煤中钒的含量变化很大,一般在0.13%~1.2%左右。在目前的技术经济条件下,只有V2O5品位高于0.80%~0.85%的石煤才有工业开发利用的潜力 [1]。
中国是世界上钒储量最大的国家之一,从石煤中提取钒的研究早在20世纪60年代 [2] 就开始了,近年来已有一定程度的提高。从石煤中提取钒是困难的,石煤中的钒大部分存在于铝硅酸盐矿物的晶格中,并且在含钒云母中同构地取代了Al (III)。云母具有稳定的层状结构,高度耐酸碱侵蚀;因此,为了有效地从石煤中提取钒,必须破坏硅铝酸盐矿物的结构。目前常用的两种提取方法有:1) 焙烧–浸出,包括氯化焙烧–水浸出或酸浸,空白焙烧–碱浸出 [3] [4] [5],钙化焙烧–硫酸浸出或碳酸盐浸出 [6];2) 浓缩直接酸浸ED硫酸或低浓度硫酸 [7];与此同时,在氯化焙烧过程中释放出许多有毒的气体,如HCl或Cl2,以及在随后的水浸出过程中产生超高盐度废水 [8] 等工艺给环境带来严重的污染。相比之下,尽管钙化焙烧更环保,但钙化焙烧存在精确控制各原料矿钙盐添加量、焙烧时间长、能耗高的缺陷 [9]。直接湿法冶金浸出工艺,如硫酸或盐酸浸出,由于严格的环境问题和立法,尽管存在高温、高酸浓度和低钒浸出效率的缺点,但正在进行深入研究 [10]。采用氧压酸浸 [11] 和超声辅助酸浸 [12] [13] 来提高钒的浸出率,但是这些处理对设备提出了很高的要求。用NH4F [14] 、CaF2 [15] [16] 或H2SiF6 [17] 等助剂对浸出进行了研究。虽然氟化物会破坏硅酸盐矿物的晶体结构,但它们对环境和工人的健康构成威胁。
近年来工业上对钒的需求量逐渐增加,但大量的石煤钒矿资源却难以开采利用。因此,研究清洁高效的石煤提钒方法迫在眉睫。在一些金属的回收过程中,长期以来,使用了添加少量氮元素(如硝酸盐或硝酸盐)的硫酸处理方法 [18] [19] [20] [21]。其中的原因是:1) 它们是强氧化剂;2) 从烧瓶中逸出的氮氧化物气体可以被少量的氢氧化钠溶液吸收,形成硝酸钠和硝酸盐,然后进入浸出回路;3) 氧化剂可以自动催化再生。然而,利用硝酸盐作为添加剂对石煤提钒的研究却很少。因此,本文提出了一种以硝酸钠为辅料的硫酸法从石煤中提取钒的方法,并进行了系统的研究。
2. 实验部分
2.1. 试剂与仪器
本研究所用石煤矿取自湖南湘西自治州古丈县。石煤的主要化学成分通过ICP-AES (电感耦合等离子体原子发射光谱法,Thermo.iCAP 6300)测定,如表1所示。矿物相分析由X射线衍射仪(TD-3500,丹东通达科技有限公司),如图1所示为石煤样品的XRD图谱,以石英、白云母为主相,以菱锌矿为次相。数显恒温水浴锅(XMTD-4000,上海比朗仪器有限公司);数显无极调速搅拌器(SXTQ-1,郑州长城科工贸有限公司);集热式恒温磁力加热搅拌器(BF-101,上海上登实验设备有限公司);循环水式多用真空泵(SHB-III,郑州长城科工贸有限公司);实验所有试剂,包括硫酸、硝酸钠、高锰酸钾、氢氧化钠、氟化氢、磷酸二氧化锰(MnO2)、重铬酸钾、次氯酸钠、氯酸钠和硝酸钠,均为分析级。
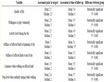
Table 1. Chemical composition of run-of-mine ore
表1. 矿物化学成分含量
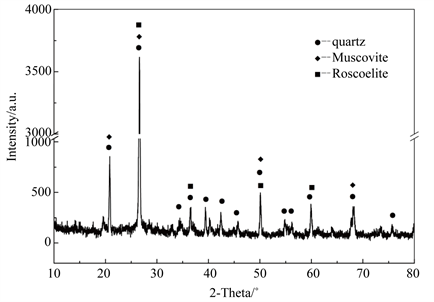
Figure 1. XRD patterns of stone coal
图1. 石煤原矿的XRD图谱
以往的研究表明,钒以V (III)、V (IV)、V (四价钒)和V (V) (五价钒)的形式存在于石煤中,其中V (III)不溶于酸和水。测定石煤中三价钒的方法如下:1) 石煤样品用脱氧蒸馏水制备的氢氧化钠溶液浸出,过滤。滤液载有石煤中全部V (V),其含量以硫酸亚铁铵滴定法测定,以2-(苯氨基)-苯甲酸为指示剂;2)残渣在80℃下预置时间用混合酸HF-H3PO4分解。过滤后,在过滤液中加入一定量的过量V (V)标准溶液,其中V (V)预期通过V (III)减少到V (IV)。结果,用硫酸亚铁铵滴定法,以2-(苯氨基)-苯甲酸为指示剂,测定了未还原的V (V)含量;3) V (IV)含量等于总V减去V (V)和V (III)。表2列出了V (III)、V (IV)和V (V)的含量,石煤中的钒主要以三价钒的形式存在,五价钒种类稀少,说明石煤中的钒很难提取。
2.2. 实验方法
精确称取50 g石煤样品(干燥矿石经筛分,筛分粒度为125~180 μm,占100%)于500 ml三颈烧瓶中,按一定固液比加入不同浓度的硫酸溶液,加入一定比例(质量比)的助浸剂,浸出过程在装有特氟隆磁力搅拌的恒温水浴锅中反应一特定时间。产生的废气用氢氧化钠溶液吸收,其中硝酸盐和硝酸盐的含量可通过化学分析容易地测定,相同浸出条件下进行三组实验。浸出反应完成后,抽滤,滤饼用酸化去离子水洗涤,然后在80℃下干燥,称重。洗涤水与滤液混合。采用ICP-AES法测定了浸出液和残渣中钒的含量,以计算钒的浸出效率。
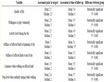
Table 2. The distribution of different valence state of stone coal
表2. 石煤原矿中不同价态钒的含量
3. 结果与讨论
3.1. 助浸剂的比较
对石煤直接酸浸与添加各种氧化剂KMnO4 (高锰酸钾)、MnO2 (二氧化锰)、K2Cr2O7 (重铬酸钾)、NaClO (次氯酸钠)、NaClO3 (氯酸钠)、NaNO3 (硝酸钠)回收钒进行了比较。在硫酸浓度为1.8 mol/L、固液比为1:1 g/ml、浸出温度为95℃、浸出时间为6 h、单独添加氧化剂2% (氧化剂与石煤样品的质量比)的条件下,表3列出了各种氧化剂的钒效应。
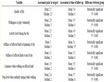
Table 3. The vanadium leaching efficiency with different oxidant
表3. 同助浸剂时钒的浸出率
从表3中可以看出,与不添加氧化剂相比,添加氧化剂使钒的浸出效率提高了10~30%。具体而言,当使用NaNO3时,钒的浸出效率最高,达到68.27%,高于使用其他氧化剂的情况,尽管它们是强氧化剂。当硝酸钠加入到酸性溶液中时,很容易形成亚硝酸。亚硝酸进一步反应生成NO+,
NO+/NO偶联具有极高的氧化还原电位1.450 (V/SHE) [22],远远大于其它氧化剂的氧化还原电位。然后NO+与矿物 [19] 反应,破坏这些铝硅酸盐矿物的晶体结构,并将V (III)氧化成水溶性V (V)。与此同时,亚硝酸降低至NO,与大气氧反应生成NO2。NO2很容易被吸收回溶液中,这允许原位再生亚硝酸。如上所述,亚硝酸作为将氧气输送到固体颗粒表面的快速手段,这允许产生的反应在高的氧化还原电位下进行。总的净反应是矿物质与酸和氧的反应,大气中的氧是无限的,远远超过其他使用的氧化剂。
3.2. 硝酸钠用量对的影响
采用浸出温度、浸出时间、固液比和硫酸浓度分别为80℃、6 h、1:1 g/ml、2 mol/L,研究了硝酸钠用量(NaNO3与石煤样品的质量比)对钒浸出的影响。实验结果如图2所示。
图2表明,随着硝酸钠用量的增加,钒的浸出率逐渐增加。当加入1.5 wt%硝酸钠时,钒的浸出率达到62.24%,之后随着硝酸钠用量的增加,钒的浸出率缓慢上升。与不含硝酸钠的硝酸钠相比,硝酸钠的浸出率提高了30个百分点。因此,取硝酸钠加入量为1.5 wt%。
水溶性五价钒,如钒酸盐,易提取,而石煤中的不溶性三价钒不能直接提取。研究人员发现偶联氧化还原电位:φΘ (VO2+/V3+) = +0.359 (V/SHE)和φΘ (VO2+/V3+) = +0.680 (V/SHE),表明三价钒可以通过氧化还原电位 > 0.680 (V/SHE)的氧化剂氧化成钒酸盐。硝酸钠是酸性溶液中
= +0.957 (V/SHE)的强氧化剂,特别是生成φΘ (NO+/NO) = +1.450 (V/SHE),表明三价钒具有氧化成钒酸盐的潜力。
3.3. 固液比的影响
考察了固液比在0.1 mol硫酸、1.5 wt%硝酸钠、80℃浸出温度和6 h浸出时间条件下对钒浸出的影响。
图3表明,钒的浸出效率随固液比从1:0.5 g/ml降低到1:1 g/ml而增加,在1:1 g/ml时达到最大值,然后随着固液比的进一步降低而降低。降低固液比为1:0.5 g/ml至1:1 g/ml降低了矿浆的粘度。因此,矿石和酸混合得很好,提高了浸出效率。一方面,降低固液比等于降低浸出浆的密度和粘度,从而降低酸–矿界面的传质阻力。因此,钒的提取随着固液比的降低而增加,直到1:0.6 g/ml。另一方面,随着固液比的降低,硫酸的浓度也降低,因为硫酸的初始量是恒定的,所以当固液比小于1:0.8 g/ml时,它应该负责曲线的下降,如图3所示。结果表明,固液比1:1 g/ml对其它浸出参数的测定是合适的。
3.4. 浸出时间的影响
在硫酸浓度2 mol/L、浸出温度80℃、固液比1:1 g/ml、硝酸钠添加量为1.5 wt%的条件下,浸出时间对钒提取的影响如图4所示。图4表明,9 h内钒的浸出率迅速达到78.25%,9 h后钒的浸出率为79.16%,缓慢上升,延长浸出时间没有效果。延长浸出时间将降低设备生产能力,因此9 h是进行以下实验的适宜浸出时间。
3.5. 浸出温度的影响
在硫酸浓度2 mol/L、固液比1:1 g/ml、浸出时间9 h、硝酸钠添加量为1.5 wt%的条件下,研究了不同浸出温度下钒的浸出率。结果如图5所示。
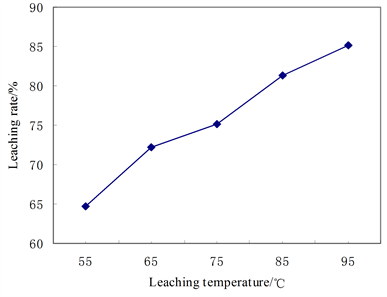
Figure 5. Effect of leaching temperature
图5. 浸出温度的影响
如图5所示,浸出温度对钒浸出率有显著影响。浸出温度越高,钒浸出率越快。这种现象可能是由于浸出剂与矿物之间的离子扩散速率随着温度的升高而增加,从而加速了矿物的溶解 [23]。在95℃时,钒的浸出率最高可达85.22%,当浸出温度超过95℃时,水蒸发速率增加。因此,选择95°C作为最适宜的浸出温度。
3.6. 硫酸浓度的影响
在95℃下,以1:1 g/ml固液比和1.5 wt%硝酸钠为添加剂,研究了1.0 mol/L~3.0 mol/L硫酸浓度对反应9 h的影响,结果如图6所示。
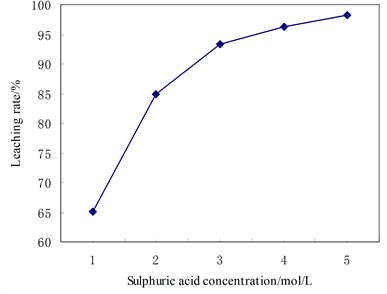
Figure 6. Effect of sulfuric acid concentration
图6. 硫酸浓度的影响
钒的浸出率随酸浓度的增加而增加。这种现象的出现是因为在高酸浓度下,足够的质子(H+)很容易穿透并破坏云母的晶格;此外,高浓度的硫酸具有钒的高溶解度极限 [24]。然而,使用极高的硫酸浓度会增加溶液中杂质的量并给环境带来极大的压力。当酸浓度为3 mol/L时,钒浸出率接近98.16%,石煤中的钒几乎完全浸出。
4. 结论
助浸剂硝酸钠能显著提高石煤中钒的浸出率,其机理可分为两种:
1) 产生氧化还原电位极高的NO+ 1.450 (V/SHE),有利于云母结构的破坏;
2) 把低价钒氧化成高价钒,有利于钒的浸出。实验结果显示,加入1.5 wt%硝酸钠时钒的浸出率比未添加硝酸钠的浸出率高30个百分点左右。
3) 在浸出条件为:硝酸钠1.5 wt%、固液比1:1 g/ml、硫酸浓度3.0 mol/L、浸出温度95℃、浸出时间9 h,石煤中钒的浸出率达到98.16%。
NOTES
*第一作者。
#通讯作者。