1. 引言
近年来,随着自动化技术、网络通讯技术、计算机辅助设计与制造技术(CAD/CAM)等的不断发展,火箭及飞机装配逐渐由传统的人工装配、半自动化装配,发展为数字化装配技术 [1]。以波音、空客为代表的航空制造企业大力推动数字化装配技术的发展和应用 [2],极大提高了运载火箭及飞机的装配质量和装配效率。
本文针对运载火箭大尺寸弱刚性构件特点,开展数字化预装配及自动钻铆技术应用研究。包括数字化工装设计、仿真及制造 [3],还包括精准定位、实时检测与反馈、自动化制孔和连接等装配技术 [4]。该技术将传统基于型架的手工作业装配方式转变为数字量传递的自动化定位和钻铆模式,可为后续的火箭装配流程提供可靠的组件产品及工艺方法借鉴。
2. 弱刚性组件结构特点
运载火箭一级尾段位于火箭底部,需承受巨大的轴向压力和弯曲抗力,对铆接连接的强度及可靠性提出了很高的要求。本文的研究对象为一级尾段1/12弱刚性组件产品,每个组件直径为3350 mm,长度为2400 mm,壁厚1.5 mm,弧度约为30˚,材料为2A12铝合金。该部件由桁条 + 蒙皮铆接构成,铆钉采用直径Φ4 mm,2A10铝合金,如图1所示。
在数字化装配及自动钻铆过程中,该结构存在以下特点:1) 尺寸大,刚性弱,易发生蒙皮中心凹陷,受力偏移,影响制孔及桁条定位精度;2) 铆接孔位数量大,种类繁多;3) 需承受巨大的轴向压力和弯曲抗力,对铆接连接的强度及可靠性提出了很高的要求。需对数字化预装配及自动钻铆接技术应用过程中的相关工艺问题进行研究。
3. 弱刚性构件数字化预装配技术研究
运载火箭一级尾段弱刚性构件装配是利用装配孔或在壁板装配夹具上将桁条与蒙皮进行定位后铆接,组装成12个1/12的筒体,然后将3个弱刚性组件拼装组合为4个1/4壁板组件,最后在壳体型架上拼装组合,最终形成整个尾段筒体壳段。
弱刚性构件的自动化钻铆过程主要包括预装配和自动化钻铆两个阶段。在预装配阶段,蒙皮和长桁在专用型架上通过一定数量的紧固件进行临时连接,以起到确定零件相对位置关系、减小初始装配间隙等作用,同时离散分布的预连接约束还可以增强结构件局部刚度以提高制孔过程中动态性能和加工质量。然而,目前预连接工艺多依赖人工经验确定,由于缺乏理论指导和过于保守,往往存在间隙抑制效果难以预测、局部刚度增强机理不明晰和装配效率低等问题。影响后续的自动化钻铆,导致蒙皮的整体延展甚至翘曲,影响装配协调性,降低了装配质量和效率。综上所述,在弱刚性结构件自动化钻铆过程中仍需要对相关工艺问题进行深入研究,探明弱刚性构件自动钻铆过程影响规律,保障高质、高效装配。
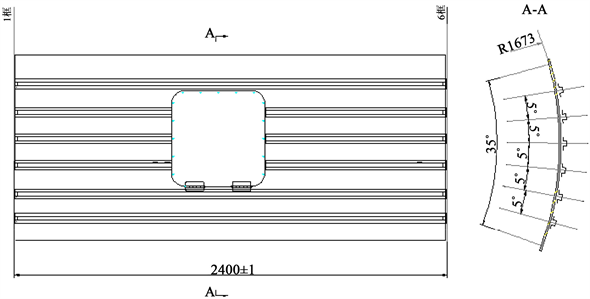
Figure 1. Typical tail weak rigid structure sketch map
图1. 典型尾段弱刚性结构示意图
3.1. 柔性定位工装设计
针对刚性弱的难题,需要在自动钻铆设备托架上设计柔性定位工装以增加自动钻铆过程中结构件的刚性,避免结构件的整体延展甚至翘曲。根据尾段结构件的外形尺寸、桁条角度分布等特点,结合预装配、自动钻铆的装配过程及自动钻铆设备定位平台的特点,设计了一种框架结构柔性定位工装,用于弱刚性构件的定位及预装配。这种定位工装可以使弱刚性组件预装配在自动钻铆设备托架上完成,并直接应用于设备的自动钻铆,避免了二次上架定位装配,提高了弱刚性构件的整体装配效率。
该工装主要由前后支撑框环、支撑桁条及调整垫片三部分组成,如图2所示。工装的主体为框架结构,定位接口可与自动钻铆设备上前后托架相匹配和连接,满足在自动钻铆系统平台上定位装配。
尾段弱刚性结构件在工装上进行定位,工装中心设置垂直定位组件作为产品的定位基准。在工装架体前后两端设置夹紧顶紧装置,用于限位蒙皮并压紧产品。可调整角度的支撑桁条可进行不同型号尾段桁条分布角度进行柔性调整,满足不同角度分布范围的需求,同时调整垫片用于精确调整支撑桁条的高度,使其与托架上表面齐平,确保铆接时与弱刚性构件蒙皮内表面贴合,达到钻铆过程中托起弱刚性构件的支撑功能。实现产品的快速定位及预装配。
3.2. 预连接点位布局优化设计及偏差分析
在弱刚性组件的预连接装配过程中,装配效率和质量是两个相互矛盾的工艺目标。预连接件数目越多越可以有效的减少甚至消除蒙皮长桁之间的间隙,从而提高制孔和后续铆接质量,但是过多的预连接件又会导致后续连接件拆除、扩孔、补铆等工序的工作量增大,降低弱刚性构件自动化装配效率。为此,我们通过研究对应每个预连接数目下对蒙皮长桁间残余间隙抑制效果最好的一组预连接布局,从而根据实际装配过程中对质量和效率的权衡选择最合适的优化布局。
为此,在尾段1/12弱刚性构件上进行了装配孔分布试验,即在壳段的每根桁条上,分布4组不同数量的装配孔,与蒙皮上的装配孔协调,测量每根桁条在蒙皮上的周向、轴向定位尺寸,及贴合间隙,与理论尺寸进行对比。以得出最合适的优化布局。根据试验结果,装配孔数量对桁条周向定位有较大影响,数量过多会出现过定位,数量少会出现欠定位。装配孔应结合桁条长度而定,对于尾段壳体弱刚性构件孔间距在300 mm~400 mm为最佳。
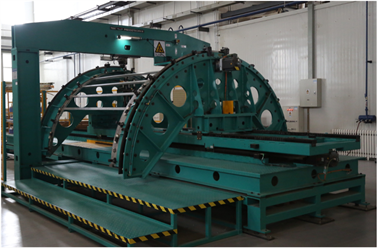
Figure 2. Structural drawing of flexible positioning tooling
图2. 柔性定位工装结构图
3.3. 数字化协调定位及误差补偿技术
传统手工划线定位完成的产品预装配组件在桁条直线度、产品形位等尺寸方面存在较大的数值偏差。采用蒙皮、桁条的数字化协调方法是保证预装配组件具备较高的装配精度的重要技术手段。运用数控钻孔机钻制蒙皮、桁条预连接点位,通过数控精度保证桁条与蒙皮之间的高精度协调关系,以满足桁条在蒙皮上周向分布满足精度要求。
对于数字化协调装配技术的应用过程中,除了确定装配位置及数量以外,还需要考虑桁条数控钻孔机和自动钻铆设备的基准协调统一,避免出现偏差影响自动钻铆。因此,根据装配关系,我们均选取桁条及蒙皮的后端为基准原点,分别在两台设备上进行桁条及蒙皮的装配孔自动钻铆,如图3所示。
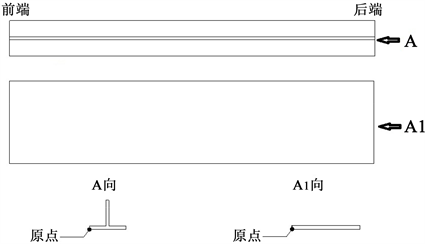
Figure 3. Schematic diagram of skin stringer origin and assembly procedure
图3. 桁条及蒙皮装配孔程序原点示意图
如图4所示,尾段弱刚性组件上除了桁条装配孔,还有后续总装使用的中框装配孔,中框装配孔事先在为保证桁条与中框相互的装配位置精度,需将中框装配孔三维坐标系与自动钻铆三维坐标系进行协调统一:
1) 中框装配孔基准协调找正:蒙皮制装配孔之前,设备上定位蒙皮阶段,首先将蒙皮后端装配在机床坐标系原点一侧,通过测量中框装配孔母线方向四个装配孔的三维坐标角度值,微调蒙皮定位装配位置,确保母线方向四个孔的角度值一致,从而保证后续中框与桁条垂直。
2) 数字化测量及误差补偿:应用自动钻铆设备的测量功能,测量中框装配孔在自动钻铆系统三维坐标值,减去程序编制的理论坐标值,得出误差偏差值输入设备,以实现已制中框装配孔与蒙皮装配孔的协调。
结论:数字化协调方法采用虚拟的数字化标准工装实现蒙皮桁条装配的协调性。装配过程中采用数字化测量手段,保证零组件在坐标系中的正确空间位置。该方法以数字量直接进行尺寸和形状的传递,减少了移形环节的误差积累,提高了制造和协调准确度。大量减少了样板等工装的应用,能够有效地控制成本。
4. 弱刚性构件自动钻铆技术应用研究
4.1. 弱刚性构件自动钻铆工艺流程优化
传统手工铆接装配工艺,一方面,工人手工劳动工作量较大,劳动强度高;另外一方面,铆接工作重复性工作量较大。弱刚性构件产品手工铆接装配工艺流程如图5所示。

Figure 5. Manual assembly flow chart of weak rigid structural parts
图5. 弱刚性构件产品手工装配工艺流程图

Figure 6. Automatic riveting assembly of weak rigid structural parts
图6. 弱刚性构件自动化铆接装配工艺流程图
从手工铆接工艺流程来看,划线、钻孔、去毛刺、铆接等均为手工操作,工作量巨大,且均为重复性操作。根据产品结构特点和弱刚性构件自动化铆接装备,采用人机结合方式,确定了需要手工铆接定位区域、自动铆接装配区域、需下架补铆区域等,同时考虑到钻孔单元、铆接单元和装夹单元在工作过程中可能与产品发生干涉、碰撞等问题,制定了弱刚性结构件自动钻铆工艺流程,如图6所示。后续进行工程化验证。
4.2. 弱刚性构件自动钻铆工艺参数优化
根据产品结构参数,进行力学试验件和金相分析试验件的铆接,通过拉脱试验和剪切试验对比分析手工铆接和压铆试件的连接强度,结合金相分析,形成了如表1和表2所示的压力铆接最佳制孔孔径参数。
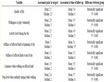
Table 1. Process parameters of hole making
表1. 制孔工艺参数
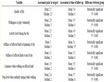
Table 2. Process parameters of riveting
表2. 铆接工艺参数
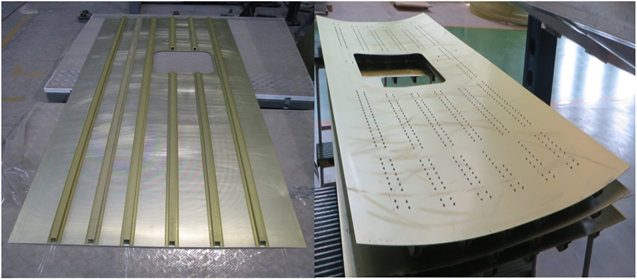
Figure 7. Finished products of tail section 1/12 weak rigid structural parts
图7. 一级尾段1/12弱刚性构件铆接成品
5. 产品工程化应用
该研究内容已成功应用于运载全系列一级尾段弱刚性构件产品生产,产品实物图如图7所示。经检验均符合Q/Y444-2011《铆接通用技术条件》及YS102-88《薄壁加筋结构制造、验收技术条件》的要求。从产品外观来看,铆钉墩头一致性好,产品外表无铆接窝头印等机械损伤。实现了弱刚性结构自动钻铆蒙皮与桁条之间位置关系的精确快速确定。较手工锤击铆接,铆钉间距、边距统一,墩头成型的大小高度一致。效率提高了1.5倍,噪声由之前的120多dB降低到30~50 dB,实现了绿色化制造。
6. 结论
通过开展运载火箭弱刚性组件数字化装配及自动化铆接技术研究,取得了自动钻铆关键工艺参数,实现了弱刚性结构蒙皮与桁条之间位置关系的精确快速确定,不仅能够生产出一致性好,外观质量优异的合格产品,同时数字化协调装配技术的应用还具有灵活性强和精度高等优点,不但可以缩短生产周期、降低制造成本,而且可以提高装配质量、减少工装数量。采用数字化制造技术后,制造成本降低了25%,产品研发周期缩短了5%,出错返工率减少75%,数字化制造技术的大量应用从根本上改变了传统制造方式。提高了运载火箭铆接自动化水平和能力,为完成运载火箭高密度发射任务奠定了基础。