1. 引言
连续退火炉是钢铁企业连续退火生产线上的核心设备,包括预热段、加热段、均热段、缓冷段、快冷段、过时效段和终冷段,炉内各段温度相差较大,而炉温不仅影响带钢表面氧化铁皮的还原,也影响钢基的力学性能,由于带钢在加热过程中自身热应力的变化及炉辊产生正负凸度的影响,很容易造成带钢在炉内的瓢曲,而直接影响产线的产量释放以及产品质量的提升。因此针对退火炉温度控制和带钢瓢曲一直成为人们研究的重点 [1],如何实现炉内温度的自动控制,避免带钢瓢曲成为技术人员亟待解决的问题 [2]。在退火炉二级控制系统投用前,所有退火炉工况控制及温度、速度等控制参数均通过操作工手动设定,导致生产过程存在诸多不稳定因素 [3],对产品质量控制带来一定程度的影响,退火炉二级系统的投入,提高了退火炉温度控制的精度和稳定性,同时也增强了不同规格带钢在退火炉内过渡过程的控制 [4]。深入研究和优化其各项功能,可以提高温度控制的稳定性,有效监控炉内设备性能,对进一步提高生产效率,改善产品质量有着举足轻重的意义。
2. 系统架构
退火炉二级控制系统按照功能可划分为四大类:与外部的通讯进程、内部功能进程、与HMI通讯进程和其他辅助进程,系统架构如图1所示。
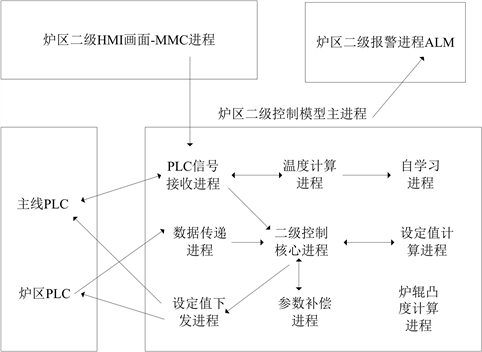
Figure 1. Level 2 control system architecture of annealing furnace
图1. 退火炉二级控制系统架构
退火炉二级控制系统与外部的通讯进程主要包括与主产线PLC和退火炉PLC之间的通讯进程,主要用于主产线钢卷信息的接收和炉区设定值的下发。与HMI的通讯进程用于二级系统与HMI画面之间的数据通讯,进行炉区数据和运行状态显示。其他辅助进程主要包括报警功能和日志功能,用于监控系统运行状态,查看日志信息及反查故障信息。内部功能进程是二级控制系统的核心部分,构成比较复杂,主要分为以下几个进程:
1) PLC信号接收进程:检查主线PLC进程收到的数据并将其传送给其他进程,包括上卷信息、焊接信息、焊缝跟踪、紧急降速信号等。
2) 数据传递进程:检查从炉区PLC收到的钢卷数据并将其传送给二级系统其他进程,包括带钢实际温度,辐射管实际温度,辐射管功率,炉内设备工作状态等;
3) 设定值下发进程:检查二级控制系统计算的设定值,并分别下发至炉区PLC和主线PLC进行设备动作,对于异常的设定值会根据情况进行限制或使用默认值;
4) 温度计算进程:通过数学模型进行温度预估计算,并判断自学习是否启动,当辐射管实际温度与模型计算温度不同,但带钢温度与设定值相同并稳定生产一段时间后,二级系统将启动自学习功能;
5) 自学习进程:用于二级模型计算参数的自学习优化,通过循环计算调整模型参数,使得带钢温度模型计算值接近带钢温度实际值;
6) 二级控制核心进程:用于带钢运行状态的管理和设定值的应用,例如稳定状态,升速状态,降速状态,紧急降速状态,过渡状态和异常状态等;
7) 设定值计算进程:用于二级模型设定值的计算,主要包括炉区预热段,加热段,缓冷段,快冷段的目标温度,辐射管功率和带钢运行速度等。
8) 参数补偿进程:用于对二级模型计算值进行PID参数调节,以补偿实际情况与模型计算的偏差,使带钢温度迅速、稳定地达到设定值;
9) 炉辊凸度计算进程:用于在线炉辊凸度模型计算,计算炉辊温度曲线、炉辊凸度曲线,以及瓢曲风险因数。
3. 通讯接口
炉区二级控制系统的通讯接口主要包括同炉区PLC和主产线PLC之间的通讯,上述接口均采用TCP/IP通讯协议,分别配置不同的端口号进行通讯,该种通讯方式配置简单,通讯速率快 [5]。
3.1. 同退火炉L1通讯
同退火炉L1通讯的报文有接收电文和发送电文,接收电文的电文号为1001,通讯内容为炉内设备的现场实际测量值,主要数据包括每个辐射管的燃烧功率,预热区,加热区,缓冷区和快冷区的区温,每个区烧嘴的燃烧数量,缓冷区和快冷区的风机功率,带钢温度,加热炉辊的温度等。炉区二级接收到上述数据后,会参与到加热模型和炉辊凸度模型的计算过程中,以进一步优化炉内温度控制。
炉区二级系统发送电文的电文号为1002,主要数据包括带钢在加热段出口,缓冷段出口和快冷段出口的温度设定值,加热段各段的功率设定值,带钢规格过渡时的二级使用方式等。炉区L1接收到上述数据后,将上述数据作为目标值,炉内设备进行实时控制。因此二级控制模型直接关系到炉内温度控值的稳定性。
3.2. 同主产线L1通讯
主产线L1系统中的PLC模块采用SIMATIC S7-1500系列,其中的MTR模块负责同炉区二级通讯,该模块型号采用CPU1518-4。该型号模块信号处理速度更快,系统响应时间更短,且可扩展性强,为通讯提供了极大的时效性和准确性。通讯内容包括上卷信息、焊接信息、焊缝跟踪、紧急降速等主产线信号。该功能实现了炉区钢卷信息和主产线钢卷信息的同步功能,并将钢卷实时位置在炉区的HMI画面上显示,方便操作工分析和查看。
4. 模型计算
4.1. 加热模型计算
对于刚上线的带钢,退火炉二级根据钢卷信息、当前速度、温度设定值,以及炉内热传递模型计算出稳态时的辐射管温度设定曲线,然后根据设定曲线在稳态时的状态计算各辐射管的设定功率,该过程由温度计算进程完成。计算过程如图2所示 [6]。同时,在上述稳态计算结果的基础上,根据实际炉况运行状态,如升降速,过渡,板温差值等,对计算结果进行调节,该过程由参数补偿进程完成 [7]。最终得到二级设定值并下发给退火炉PLC执行。
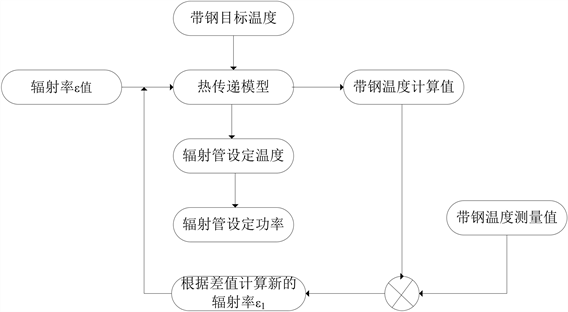
Figure 2. Radiation tube power calculation process
图2. 辐射管功率计算流程
当辐射管实际温度与模型计算温度不同,但带钢温度与设定值相同并稳定生产一段时间后,退火炉二级将启动自学习功能,调整模型参数,使模型计算结果与实际情况一致 [8]。自学习进程会循环计算需要调整的模型参数,最后计算出的εend使得带钢温度计算值≈带钢温度测量值,算出εend后炉区二级会根据εend计算这一卷的二级设定值,同时判断自学习是否持续生效(是否修改模型参数,以对下一卷起效),如果需要修改模型参数,该进程将逐步修改模型参数 [9]。
4.2. 炉辊凸度模型计算
退火炉的稳定运行技术是一项综合性的控制技术,集中了炉辊制造、机械安装、张力控制、跑偏控制、加热控制、冷却控制、速度控制等核心技术 [10],其中,跑偏和瓢曲是影响带钢炉内稳定运行的主要因素,这会导致机组不能稳定运行,直接制约了产能的发挥。炉辊凸度模型的引入旨在分析不同炉况下炉辊的热凸度,根据带钢规格和炉况计算炉辊温度曲线、炉辊凸度曲线,以及瓢曲风险因数,用于分析和预防带钢的跑偏、瓢曲 [11]。
炉辊凸度模型计算流程见图3,其中利用圣维南原理计算带钢与炉辊的实际接触长度,利用Stefan-Boltzmann公式计算热辐射。
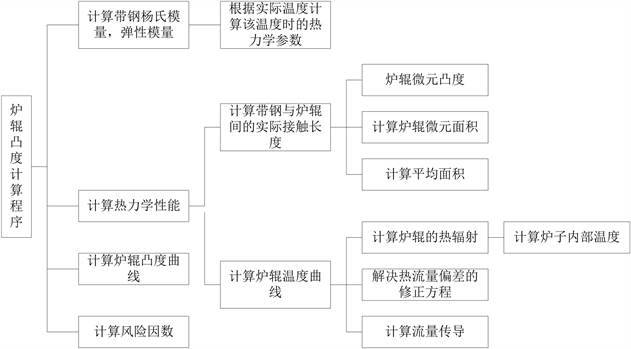
Figure 3. Calculation flow of furnace roll crown
图3. 炉辊凸度计算流程
由于炉辊和带钢的温差较大,导致炉辊辊身沿径向热膨胀不均匀,造成炉辊凸度值发生变化,其效果如图4所示,计算如下式所示:
式1
式中:
——炉辊产生热凸度后的总凸度值;
——炉辊初始凸度;
——热膨胀系数;
——炉辊半径;
——炉辊轴向温差。
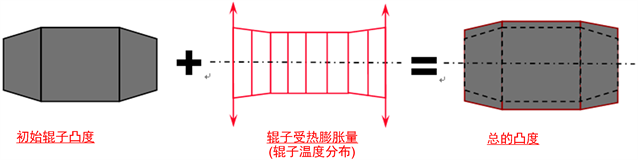
Figure 4. Schematic diagram of crown change of furnace roll
图4. 炉辊凸度变化示意图
从式(1)中可以看出,炉辊热膨胀系数越大,炉辊热膨胀后其总凸度值变化越大。在加热段,炉辊温度高于带温,炉辊热膨胀后产生热凸度为负凸度,炉辊总凸度减小。此时,当炉辊温差控制在一定范围之内时,炉辊总凸度值虽然减小,但仍然保持在正凸度的状态,炉辊防瓢曲的能力增强,但防跑偏的能力减弱;而当温差超过一定值时,炉辊负凸度过大,导致炉辊变成负凸度辊,此时炉辊防瓢曲和跑偏的能力都会变差 [12]。
瓢曲风险通过瓢曲风险因子
进行评估,如
,带钢理论上将会出现屈曲变形。
:瓢曲风险因子,无量纲
:单位张力,单位MPa
:计算临界张力,单位MPa
r:炉辊外径
L:顶辊与底辊间的距离
K:HBR因素,3.9e4
:摩擦系数,0.3
:带钢厚度
Y:带钢杨氏模量
E:带钢弹性模量
:炉辊中心凸度
:带钢边缘炉辊凸度
5. 工艺控制
炉区二级的控制模型的应用主要包括稳态控制,升降速控制,温度过渡和带钢规格过渡四个方面,我们以稳态控制为例,比较二级控制模型和一级控制的应用效果。
在带钢规格、钢种、速度以及退火温度相同的条件下,抽取一级板温控制与二级功率控制下的加热段实际温度数据,并利用minitab软件进行稳定性分析。结果如图5所示。在加热段温度波动允许范围内一级温度控制加热段板温CPK为1.01,二级功率控制加热段板温CPK为1.54,数据表明炉区二级功率控制在温度稳定性方面强于一级温度控制。
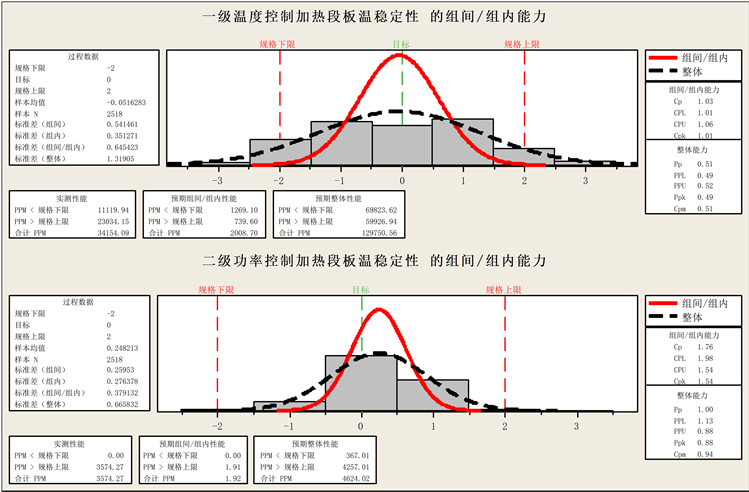
Figure 5. Comparison between level 2 model control and level 1 control in furnace
图5. 炉区二级模型控制和一级控制比较效果
6. 结论
本文研究了连续退火炉二级控制系统的主要功能,针对其系统架构、数据通讯、加热模型计算、炉辊凸度模型计算和稳定性控制等方面进行了研究,加热模型和炉辊凸度模型作为二级系统的核心功能,融入了热传递模型和自适应算法,分析了炉辊凸度与瓢曲风险质检的关系。并在带钢规格、钢种、速度以及退火温度相同的条件下,比较了一级板温控制与二级功率控制下的加热段实际温度数据,结果表明二级控制温度稳定性要优于一级控制。二级控制提高了带钢在炉内加热温度变化的稳定性,有效减少了温度控制的人工干预,提高了炉区控制的智能化水平,并为进一步优化炉区控制提供了数据支撑。