1. 引言
航空发动机高压压气机可调静子(Variable Stator Vane, VSV)液压作动系统,是现代先进航空涡轮喷气发动机气流控制系统中非常重要的系统,是防止航空发动机喘振装置之一 [1] [2] [3] [4],一旦VSV作动系统失效,可导致发动机压气机失速、发动机喘振、EGT超温等严重后果,尤其在民用航空发动机应用领域 [5],发动机的可变几何机构液压作动系统的稳定性要求非常高 [6] [7] [8],因而,深入分析液压作动系统的故障机理及故障影响,对于航空发动机控制系统的故障诊断并采取相关措施是非常必要的 [9] [10] [11]。进行故障注入测试试验,是全面评估航空发动机液压作动系统在各种飞行条件下安全性的最有效方式,但是由于检验成本、研发进程、周期及文件指导等局限性,很难进行具有实际意义的航空发动机液压作动系统的故障注入测试试验。文献 [12] [13] [14] 采用了AME Sim对航空发动机液压机械装置和燃油计量装置等各部件进行了仿真模型建立,通过仿真模型的建立可以分析航空发动机液压机械装置和燃油计量装置等设计参数对液压机械装置运行和燃油计量特性的影响。
本文将首次建立以机、电、液多物理场耦合的联合仿真模型,全方面高精度的分析典型电、液伺服故障模式对高压压气机可调静子控制回路的性能影响,并分析了系统的故障特征变化规律,为进一步航空发动机控制系统机载模型建模及故障诊断提供依据。
2. VSV作动机构系统工作原理
在航空发动机上应用高压压气机可调静子作动机构的主要目的是提高发动机的工作稳定性,防止发动机喘振。其工作原理是根据发动机的转速和高压压气机进口气流温度来调节静子叶片的安装角度,以调节叶栅通流流量和栅后气流攻角,保证压气机能稳定正常的工作。VSV包括单级和多级可调,目前多级可调的VSV已经广泛应用于多种航空发动机中。
VSV作动机构系统如图1所示,主要由电子控制器、机械液压作动部件和叶片角度调节机构组成。工作原理如下:航空发动机电子控制器通过收集航空发动机传感器发送的参数和VSV作动筒位置反馈信号,计算并控制VSV力矩马达工作以通过控制供给VSV作动筒内的燃油流量,使VSV作动筒运动,带动连接在其末端的VSV作动环一起运动,此时作动环分别带动安装在其上面的高压压气机叶片运动,从而实现对叶片的角度控制。
VSV叶片角度调节机构如图2所示,一般包括液压作动筒、主连杆、曲柄、联动环、摇臂及角度反馈系统等组件。图2以CFM56-3为例给出了多级VSV调节机构示意图。
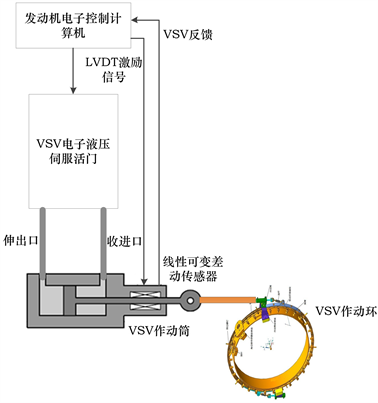
Figure 1. VSV actuating system diagram
图1. VSV作动系统示意图
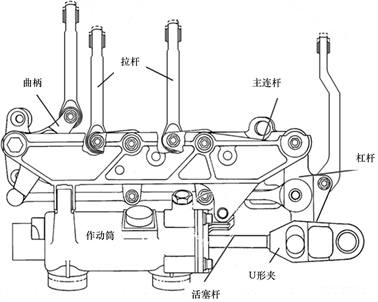
Figure 2. VSV regulating mechanism diagram
图2. VSV调节机构示意图
图3给出了VSV调节机构的闭环伺服调节系统,主要由控制器、电液伺服阀、作动筒和LVDT传感器等构成。
3. 多物理场耦合模型的建立
多物理场耦合模型的建模鱼仿真分析为复杂系统的机理和性能研究具有重要意义 [10],Modelica是一种开放的、面向对象的以方程为基础的语言,包括机械、电子、电力、液压等以及面向过程的子系统模型,可以基于物理方程描述物理行为,无需型,该模型可模拟VSV作动系统的液压作动及负载力驱动部件的正常运转和故障传输及影响。然后将所建的机–液模型基于FMI标准的FMU模型导出,封装的FMU
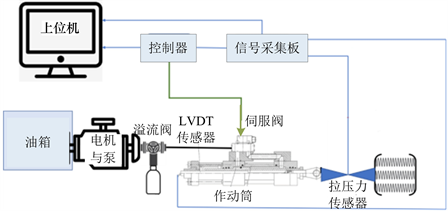
Figure 3. VSV electro-hydraulic servo control system diagram
图3. VSV电液伺服控制系统
包括模型文件、模型描述文件和模型中引用的资源,利用Matlab/Simulink设计高精度闭环控制系统,Simulink利用内嵌的FMI Import模块导入Modelica模型,实现基于Modelica与Matlab的机–电–液联合仿真。本文基于Matlab/APP Designer开发了液压作动系统故障分析软件,将基于联合仿真的VSV作动系统内嵌至分析软件中,使得作动系统的故障注入、故障影响和故障特征分析以及故障数据提取更为方便。
3.1. 液压作动模型
高压压气机VSV液压作动系统主要由电液伺服阀、作动筒和扭力杆式调节机构组成。发动机电子控制器(EEC)通过调节电液伺服阀的输出伺服燃油控制VSV作动筒的位置,VSV作动筒是燃油控制系统的作动部件,每台发动机上安装两台VSV作动筒,用于控制高压压气机可调静子叶片的角度,以提高高压压气机效率。每个作动筒上安装一个单余度的线位移传感器(LVDT),该传感器将VSV作动筒的位置信号反馈至EEC,形成闭环控制。
a) 电液伺服阀
电液伺服阀主要作用是根据电控制信号和液压伺服信号实现对液压油流量和流速的控制,从而控制作动筒的伸出与缩回。VSV电液伺服阀接收控制电流,调节阀芯的位置,计量至作动筒两腔的伺服燃油。
对电液伺服阀原理进行抽象和简化,即不考虑控制线圈、射流管、射流接收管的特性,可以认为阀芯的位置与控制电流成正比。不考虑主阀芯的运动特性和液动力,主阀芯可以抽象为通流面积与阀芯开度成正比的可变面积节流孔模型。节流孔流量计算公式为:
(1)
式中,Q是通过孔的流量,A是流通面积,Cd是流量系数,ρ为流体密度,∆P为节流孔口前后压力差。图4是基于Modelica建立的VSV电液伺服阀,由4个与阀芯相连的面积可调的流量控制孔组成,图5为电液伺服阀不同阀芯位置的开度。
电液伺服阀接收的控制电流用以调节阀芯的位置,从而计量至作动筒两端的伺服燃油量。在该电液伺服阀中设置了漏油参数,可用于模拟电液伺服阀的伺服燃油外漏故障。
b) 作动筒
作动筒为双作用液压缸元件,将液压力转换为机械力通过摇臂组件作动环控制高压压气机可调静子叶片的角度。作动筒两端接收电液伺服阀的输出压力,高压油进入VSV作动筒的收进腔,作动筒在高压油的作用下,活塞杆收进,当电液伺服阀的高压油进入VSV作动筒的伸出腔时,作动筒在高压油的作用下,活塞杆伸出。活塞杆的收进和伸出位移由VSV作动筒内置的线位移传感器传送至EEC。
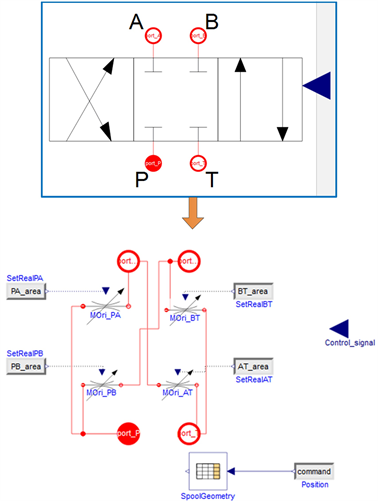
Figure 4. VSV electro-hydraulic servo valve model
图4. 电液伺服阀模型

Figure 5. Relationship of spool position and signal diagram
图5. 阀芯位置与信号关系图
作动筒的简化数学模型可以用流量连续方程和活塞运动方程来描述,在考虑液压缸的内部泄漏的情况下,油腔的流量连续方程为:
(2)
(3)
式中:QL、QR为左右液压缸流量,PL、PR为左右液压缸压强,Gleak为泄漏率,S为液压缸行程,AL、AR为左右液压缸面积,E0为油液体积弹性模量,V0为油腔初始容积,x为活塞位移。
力平衡方程为:
(4)
式中:x为活塞位移,B为阻尼系数,Fw为外力。
图6展示了所用作动筒模型。液压部分处理为两个腔体,压力由流量和活塞位移来决定,内部泄漏用层流液阻Leakage来模拟,用两个弹簧阻尼系统Stop_a和Stop_b分别模拟活塞靠近壳体左端或右端时候的液压减速衬垫,杆模型模拟腔体的长度,活塞和杆的惯量和适当的驱动载荷被集中到一个质量块上,活塞左右两边的杆将力传递到活塞上,使用阻尼模块Friction模拟活塞的卡滞特性。
c) 力综合臂模型
本文将作动筒连接的VSV扭力杆调节的连杆机构简称为力综合臂,VSV扭力杆调节机构的二维布局图如图7所示,运动传递路线为作动筒利用伺服燃油驱动活塞杆,活塞杆通过杠杆带动主连杆,从而带动连接在主连杆的各级曲柄,曲柄通过连杆驱动摇臂从而来调节静子叶片的角度。在实际的三维运动中,曲柄通过连杆带动连动环,连动环带动沿轴向均匀分布的摇臂从而调节高压压气机各级静子叶片的角度以实现压气机进口气流特性。
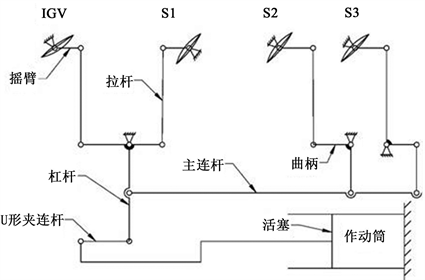
Figure 7. Schematic diagram of two-dimensional layout of regulating mechanism
图7. 调节机构二维布局示意图
Modelica标准库里包含Mechanics机械模型库,主要包括转动、平动和多体三部分。其中多体模型库可以提供三维机械组件搭建机械系统。因此力综合臂模型可以利用多体库里的模型搭建连杆、杠杆、拉杆、摇臂以及连接件等,叶片对摇臂的作用通过作用力进行模拟,利用弹簧阻尼模块模拟拉杆与摇臂间连接处的变形。图8给出了基于调节机构的二维布局建立的一级VSV调节机构模型。
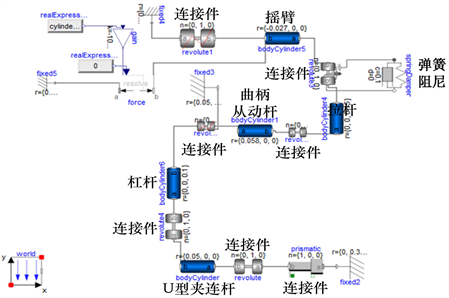
Figure 8. Model of comprehensive force mechanism
图8. 力综合臂模型
d) VSV系统模型
如图9所示,按照VSV作动系统模型架构完成系统模型构建。作动筒利用伺服燃油驱动活塞杆,活塞杆通过杠杆带动主连杆,从而带动联接在主连杆的各级曲柄,曲柄通过连杆驱动摇臂从而来调节静子叶片的角度。模型里利用层流液阻元件模拟外泄漏。
电液伺服阀的控制信号将通过Matlab/Simulink建立基于作动筒位移的闭环系统得到电液伺服阀的电流控制信号,从而实现基于机–电–液的多物理场耦合模型。
3.2. 联合仿真模型
MODELISAR协会基于Modelica技术提出的功能样机可交换接口建立了FMI (Functional Mock-up Interface)规范,遵照FMI规范可以实现Modelica工具和非Modelica工具之间生成和交换模型,基于FMI规范生成的模型为FMU模型(Functional Mock-up Unit),即执行FMI规范的模型单元。本文基于该规范,将上述建立的基于Modelica的液压机械作动导出FMU模型单元,在导出时将注入的故障参数作为输入端口以便于故障分析软件开发,故障参数包括作动筒摩擦阻尼系数、内泄露系数、电液伺服阀等效泄露面积、负载力系数等。
将液压机械作动FMU模型单元通过Simulink/FMU Import模块导入至Matlab中,通过原有交互接口替换原有的VSV功能模型,构建基于PID控制器的VSV液压作动闭环控制系统,在FMU模型输出的作动筒位移反馈处设置传感器注入故障模块,传感器故障类型包括传感器增益故障和传感器偏差故障,如图10所示。
基于联合仿真模型,使用Matlab/APP Designer开发液压作动系统故障分析软件,如图11所示,该软件主要分为参数配置区、故障模式设置区和结果展示区,参数配置区可以设置液压作动系统作动筒、电液伺服阀的物理参数、PID控制器参数等,故障模式设置区可以选择故障模型并设置故障等级大小等,结果展示区可以展示液压作动回路故障响应曲线,包含作动筒期望位移与实际位移,控制信号,电液伺服阀伺服流量、燃油泄漏量、电液伺服阀伺服压力以及负载力。
4. 基于联合仿真的故障模式影响分析
本文在所建立的液压作动系统联合仿真模型中模拟系统的机械结构故障,以作动筒活塞位移阶跃响应的闭环控制为目标,下面分别以系统无故障、作动筒活塞卡阻、电液伺服阀漏油、力综合臂卡滞及传感器漂移故障为例分析液压作动系统各关键信号参数的变化规律。
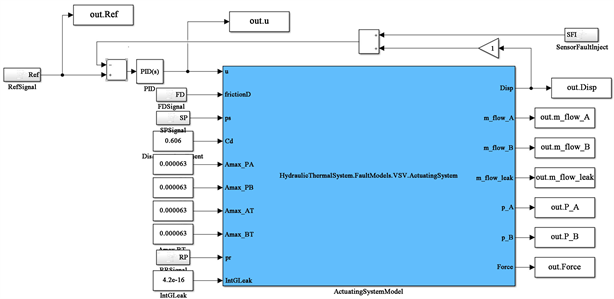
Figure 10. VSV hydraulic actuation closed-loop control system
图10. VSV液压作动闭环控制系统
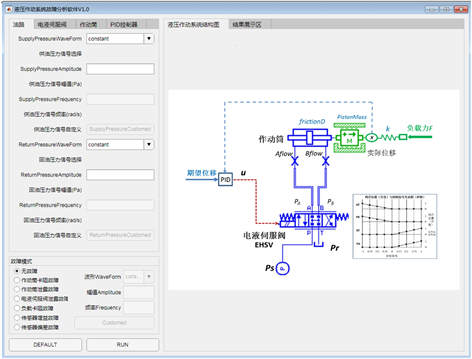
Figure 11. Hydraulic actuator system fault analysis software
图11. 液压作动系统故障分析软件
1) 系统无故障
图12给出了液压作动系统无故障下的作动筒位移响应、控制信号及电液伺服阀伺服流量信号,控制信号为电液伺服阀的驱动电流信号,系统无故障下作动筒伺服位移跟踪响应时间0.5 s,此时电液伺服阀伺服流量较大。
2) 作动筒活塞卡阻
如果作动筒外筒内壁因油液污染等造成内部局部划伤或作动筒局部摩擦力增加,则会导致活塞杆速度不均匀或活塞杆运动迟缓。根据作动筒的力平衡方程即公式(4),本文通过增加作动筒活塞在容腔里的摩擦阻尼系数B来模拟作动筒活塞的卡阻故障,分别将摩擦系数设置为
N/(m/s)和
N/(m/s),以模拟摩擦程度逐渐增大的的卡阻现象,结果如图13所示。由图13可以发现,随着作动筒活塞与容腔间摩擦系数的增加时,作动筒活塞位移响应延迟增加,电液伺服阀的伺服流量随之降低。
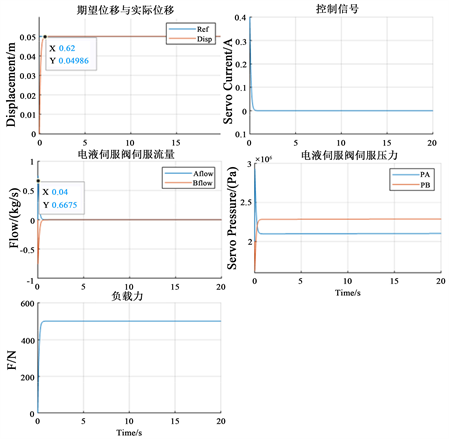
Figure 12. System response of hydraulic actuator without failure
图12. 液压作动系统无故障下的系统响应
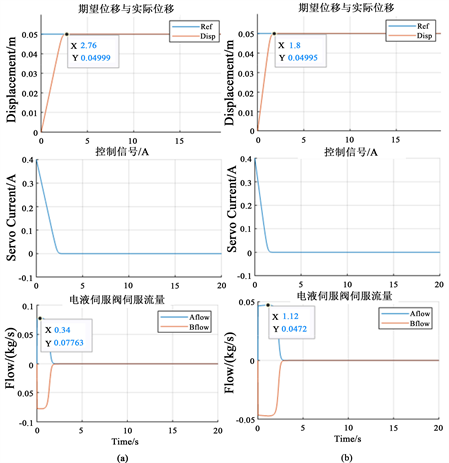
Figure 13. Frictional coefficients are 3 × 105 and 5 × 105 respectively. (a) Friction coefficient: 3 × 105; (b) Friction coefficient: 5 × 105
图13. 摩擦系数分别设置为3 × 105和5 × 105。(a) 摩擦系数 = 3 × 105;(b) 摩擦系数 = 5 × 105
3) 电液伺服阀漏油故障
通过在电液伺服阀组件参数里修改等效泄露面积Aleak的大小来模拟电液伺服阀的内泄露量,本文所设计的模型以Aleak = 0 m2为无泄漏的电液伺服阀,其响应如图12所示。以Aleak =
m2和Aleak =
m2分别表示两种不同泄漏量等级的内泄漏故障,图14给出了作动筒在不同的等效泄漏面积下的执行机构液压作动系统响应特征,由图14可以看出,随着电液伺服阀的等效泄漏面积增加,与无故障相比,随着电液伺服阀内燃油泄漏,作动筒左右腔体的压力,即电液伺服阀压力PA、PB也发生了偏移。
(a) Aleak = 1 × 10−6 m2
(b) Aleak = 5 × 10−6 m2
Figure 14. Electro-hydraulic servo valve oil leakage failure
图14. 电液伺服阀漏油故障
4) 力综合臂卡滞
通过在组件Spring Damper里修改弹性系数的大小来模拟力综合臂不同程度的卡滞,弹性系数分别设置为
N∙m/rad和
N∙m/rad,从图15可以看出,与无故障相比,随着负载系数的增大,负载力逐渐变大,作动筒左右腔体的压力,即电液伺服阀压力PA、PB也随之发生改变,其变化趋势与电液伺服阀漏油故障有所区别,电液伺服阀伺服压力在作动筒位移闭环控制下呈现逐渐变大的趋势。
5) 传感器增益故障
传感器故障通常分为硬故障和软故障,传感器的硬故障通常表现为传感器测量值在正常输出的基础上,出现瞬变或产生较大的阶跃,其特征表现为传感器偏差故障;传感器的软故障通常表现为传感器观测信号在正常输出的基础上出现随时间累加的渐变,其产生的根源通常是由于发动机元器件的老化或零漂等,其特征表现为传感器恒增益故障。本文以传感器恒增益故障为例,通过设置不同大小的传感器增益故障进行故障模拟,增益故障值分别为1.5和2,图16给出了不同增益故障等级下液压作动系统作动筒位移的闭环响应特征,由该图可以看出,由于传感器发生故障,因而传送至PID控制器的作动筒位移发生变化,控制器无法识别出作动筒的实际位移,控制器只能基于传感器供给的数据进行控制,因而随着传感器增益故障等级逐渐增大,作动筒实际位移逐渐偏离期望位移,且故障特征在伺服压力、负载力等均有反映。
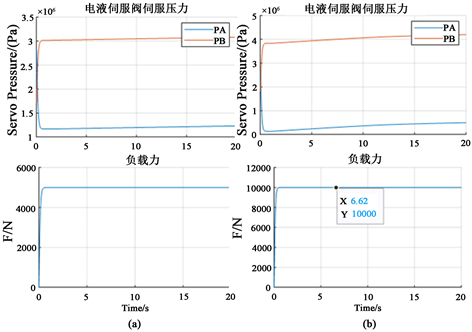
Figure 15. Stuck fault of comprehensive force mechanism. (a) Elastic coefficient: 1 × 105; (b) Elastic coefficient: 2 × 105
图15. 力综合臂卡滞故障。(a) 弹性系数 = 1 × 105;(b) 弹性系数 = 2 × 105
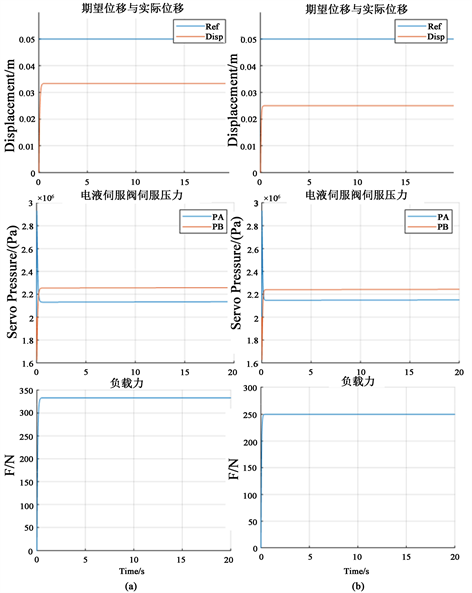
Figure 16. Sensor gain failure. (a) Sensorgain fault: 1.5; (b) Sensor gain fault: 2
图16. 传感器增益故障。(a) 故障增益 = 1.5;(b) 故障增益 = 2
表1总结了本文所提出的VSV液压作动系统故障模式影响分析(FMEA)。
基于VSV液压作动系统FMEA表可以看出,航空发动机VSV调节机构闭环控制系统在不同的故障模式及故障等级下,系统信号具有明显的特征变化规律,系统故障特征信号变化规律可作为基于模型和数据的故障诊断方法研究的模型及数据基础,为航空发动机执行机构回路故障诊断创造条件。
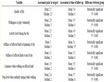
Table 1. FMEA table of VSV hydraulic actuation system
表1. VSV液压作动系统FMEA表
5. 结论
本文基于航空发动机VSV作动系统工作原理建立了基于Modelica的多物理场耦合模型,并开发了VSV作动系统故障注入分析软件,研究了电液伺服阀、作动筒、传感器及负载故障对作动系统响应的影响。通过本文的模型与工具开发,可以直观的分析并观察航空发动机执行机构回路故障的影响机理,降低故障试验测试成本,快速获取故障数据,为进一步航空发动机机载模型建模、执行机构回路控制器设计、基于模型与数据的航空发动机执行机构回路故障诊断提供了较优的设计基础。
基金项目
国家科技重大专项(2017-I-0001-0001),上海青年科技英才扬帆计划资助(20YF14544300)。