1. 引言
7075属于Al-Zn-Mg-Cu系高强高硬铝合金,因具有密度低、强韧性高、易加工、可焊性优良等特点,广泛应用于航空航天、轨道交通和高端民用等领域 [1] [2] [3]。但由于其合金化程度高、变形抗力较大,不仅需要更大吨位的挤压设备,而且为避免挤压过程中出现开裂、尺寸形位超差等缺陷,其挤压速度不能过快,通常只能控制在5~8 mm/s。因此,7075的挤压过程属于慢挤压 [4]。以75 MN挤压机生产截面规格为26 * 310 mm的7075排材为例,挤压铸锭长度为1200 mm,挤出长度为15.4 m的排材耗时约35 min。以此推算,单日产量不足14 t,严重影响生产效率和产能发挥。
本文通过要素分析,利用有限元软件对铝合金排材的挤压过程进行正交模拟试验,研究不同要素组合对挤压出口速度、温度以及挤压内筒比压的影响,为7075排材的生产工艺优化提供理论参考。
2. 要素分析
2.1. 模具要素分析
模具是影响铝材挤压生产的主要因素之一。在挤压过程中,坯料金属先填充导流孔进行一次预成形,然后流入工作带进行二次成形,从而得到成品尺寸规格。在这个过程中,由于挤压力在模具中呈非均匀分布,导致模具出口各部位的金属以不同的速度流出。当速度差异过大时,排材内应力加剧,从而出现开裂、扭拧、波浪、弯曲、尺寸超差等缺陷 [5] [6]。因此,为保证模具出口金属均匀流出,需要合理设计并匹配导流孔深度和工作带厚度这两个参数。模具结构如图1所示。
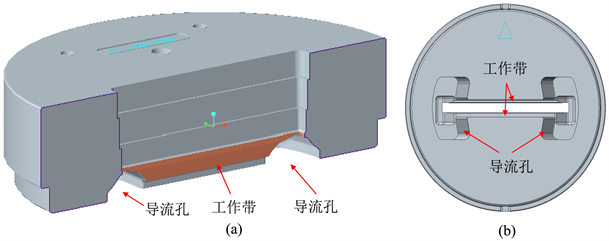
Figure 1. Die structure. (a) Cross section view; (b) Top view
图1. 模具结构示意图。(a) 截面图;(b) 俯视图
导流孔深度直接影响着模具中金属流的体积 [7]。当导流孔过深时,模具内金属的体积随之增加,有利于平衡金属流动,尺寸形位稳定可控,但由于金属与模具之间的接触面积增大,摩擦力显著增加,从而导致排材升温快、挤压载荷过大,这不仅增大了排材开裂的风险,也降低了模具的使用寿命。反之,当导流孔过浅时,尺寸精度和平面的稳定性得不到保证,容易出现塌边现象。
工作带是挤压成形最后环节,其厚度直接影响着排材的形状尺寸和表面质量 [8]。工作带厚度越大,在工作带堆积的金属增多且流速变慢,在一次预成形阶段形成的死区增大,虽对挤出排材的表面和尺寸有利 [7],但金属与模具之间的接触面积增大,摩擦力随之增大,导致排材温度升高,容易开裂。反之,工作带厚度越小,虽然挤压载荷有所降低、排材升温有限,但容易带来排材表面质量不稳定,尾部尺寸不合格等问题。
2.2. 工艺要素分析
挤压过程中的铸锭温度和挤压杆速是对挤压成形过程影响最大的两个工艺参数 [9]。首先,铸锭温度和挤压杆速决定了金属的变形抗力和摩擦力,从而决定了实际挤压力和模具载荷的大小,最终影响挤出件的质量与模具寿命。其次,铸锭温度和挤压杆速也在很大程度上决定了金属的微观组织,这对最终产品的性能与质量尤为关键 [10]。因此,合理设定铸锭温度和挤压杆速,是挤压排材优质高效生产的前提和基础。挤压过程示意图如图2所示。
铸锭温度对挤压过程中金属变形的影响极大。铸锭温度越高,金属的强度越低,这使得挤压力减小,容易挤压;但金属与模具之间的摩擦力增大,金属流动的不均匀性增加,从而导致挤出产品更容易产生裂纹、粗晶环等缺陷 [11]。反之,铸锭温度越低,金属的变形抗力越大,挤压载荷增大,容易造成挤压闷车(满压挤)、模具寿命缩短等问题的出现。
挤压杆速同样也影响着挤压时金属的变形,决定了金属的流出速度(排材的挤压速度 = 挤压杆速 × 挤压比) [12]。挤压杆速越快,生产效率越高,但金属温升迅速,容易超出金属的塑性温度区间,从而产生裂纹;并且变形抗力也会越大,容易造成挤压闷车。反之,挤压杆速越慢,生产效率越低,但金属的温升相对缓慢,有利于避免挤压裂纹的出现;同时变形抗力相对较小,有利于延长模具寿命 [13]。
3. 试验方法
为寻求7075排材挤压过程的最优参数组合,本文对工作带长度、导流孔深度、挤压杆速和铸锭温度等4因素4水平进行试验设计(具体参数见表1),选用L16 (44)正交表确定具体模拟试验方案(详见表2)。
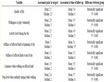
Table 2. Orthogonal simulation test
表2. 正交模拟试验方案
4. 模型建立
将三维建模软件中创建的挤压模具模型导入有限元软件中,并对模型进行几何清理,然后进行网格划分。本模型整体网格总数约为25万,网格划分的大小由变形程度决定,变形程度越大网格越小数目越多,变形程度越小网格越大数目越少。划分网格后的排材挤压有限元模型如图3所示。
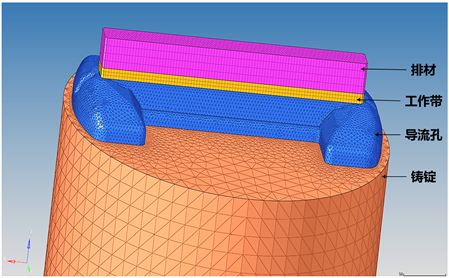
Figure 3. Finite element model for strip extrusion
图3. 排材挤压有限元模型图
4.1. 材料本构模型
挤压排材为7075铝合金,采用反双曲正弦函数模型(Sine Hyperbolic Inverse) [14],即:
(1)
式中:
为流动应力;
为材料参数,与温度有关;
为应变率;Q为活化能;R为气体常数;T为温度;A是应变因子倒数;n是应力指数。
对于选用的7075铝合金,
,
,
,
,
。材料的杨氏模量
,泊松比为
,密度
,比热
,传导率
。通过计算得到7075铝合金的本构关系曲线,如图4所示。
4.2. 模拟参数与边界条件
在模拟挤压成形的过程中,模拟参数和边界条件反映了挤压材料与模具之间的受载与约束情况,参数设置越合理,模拟越接近现实。本文的工艺参数、模具参数与边界条件如表3~5所示。
5. 模拟结果与讨论
5.1. 挤压速度
图5为试验1~试验16的排材挤压速度的模拟结果,显示了排材在挤出模具出口时其横截面上的金属流速分布。可见,排材两端部金属流出速度最快,越往中部金属流出速度越慢。
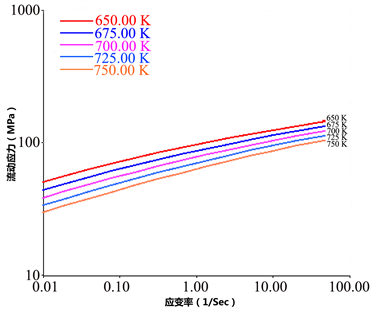
Figure 4. Constitutive relation curves of 7075 aluminium alloy
图4. 7075铝合金的本构关系曲线
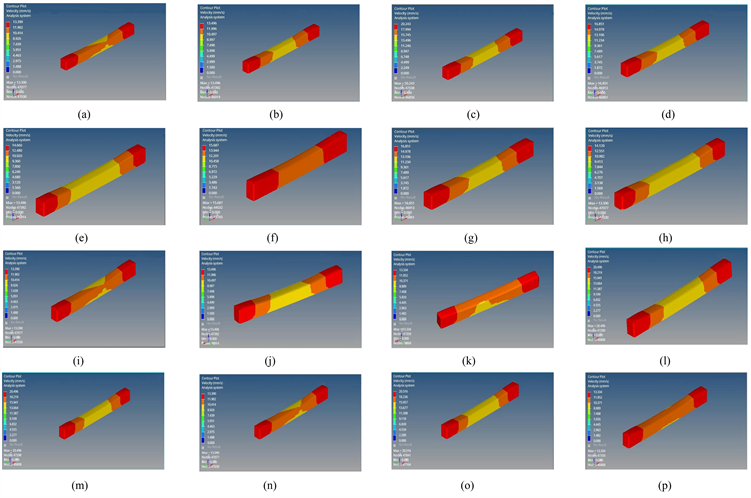
Figure 5. Simulation of extrusion velocity distribution of strip’s cross section. (a) Test 1; (b) Test 2; (c) Test 3; (d) Test 4; (e) Test 5; (f) Test 6; (g) Test 7; (h) Test 8; (i) Test 9; (j) Test 10; (k) Test 11; (l) Test 12; (m) Test 13; (n) Test 14; (o) Test 15; (p) Test 16
图5. 排材截面挤压速度分布模拟结果。(a) 试验1;(b) 试验2;(c) 试验3;(d) 试验4;(e) 试验5;(f) 试验6;(g) 试验7;(h) 试验8;(i) 试验9;(j) 试验10;(k) 试验11;(l) 试验12;(m) 试验13;(n) 试验14;(o) 试验15;(p) 试验16
为准确比较试验的模拟结果,需对金属流出速度的均匀性进行评价,即对排材横截面由外至内的50个测量点的流速进行极差和均方差 [15] 计算,公式如下:
(2)
(3)
式中:
为排材金属流速的极差,
为排材金属流速的最大值,
为排材金属流速的最小值。
为排材金属流速的均方差,
是测量点i处的金属流速,
;n是所选的测量点数量,
是所有测量点的平均流速。
图6为各试验流速范围、极差以及均方差。可见,试验5、试验6、试验8的流速极差相对较小,分别为4.14 mm/s、3.49 mm/s、3.98 mm/s;试验6、试验7、试验8的流速均方差相对较小,分别为2.95 mm/s、3.19 mm/s、3.5 mm/s。其中,试验6的金属流速相对较高,且极差值与均方差值均最小。
(a)
(b)
Figure 6. The range and standard deviation of the strip’s extrusion velocity. (a) Extrusion velocity range; (b) Standard deviation of extrusion velocity
图6. 排材流速范围、极差与均方差图。(a) 排材流速范围与极差;(b) 排材流速均方差
5.2. 挤压温度
对试验5~试验8进行挤压温度模拟,并参照公式(2)和公式(3)对温度进行均方差和极差计算。图7显示了排材在挤出模具出口时其横截面上的温度分布,图8为排材挤压温度范围、极差值与均方差值。可见,试验5~8的排材最高温度在都460℃~470℃的范围内,均低于7075过烧温度。其中,试验5、7、8的排材两端温度明显较低;试验6的排材温度区间为451℃~465℃,其极差值与均方差值均为最小,温度分布更为均匀。
5.3. 挤压内筒比压
比压是作用在挤压内筒横截面上的单位压力,是评价挤压载荷的重要指标,公式如下:
(4)
式中:
为比压;F为挤压机的挤压力;
为挤压内筒的横截面面积。
对试验5~8进行挤压内筒比压模拟,并参照公式(2)和公式(3)对比压进行均方差和极差计算。图9和图10分别为挤压内筒比压分布,比压范围、极差值与均方差值。由图可知,4组试验的最大比压均不超过625 MPa (换算后小于75 MN),且比压范围与极差值均十分接近。其中,试验6的比压均方差最小,其最大比压值为595.62 MPa,比其他3组试验的最大比压值低10~20 MPa。
综合考虑排材挤压速度、温度分布的均匀性,以及挤压内筒比压的情况,通过模拟可知,试验6的参数组合为最优,即工作带长度为8 mm,导流孔深度为38 mm,挤压杆速为1.0 mm/s,铸锭温度为340℃。在此参数组合的模拟下,排材的最大挤压速度可达到15.69 mm/s。
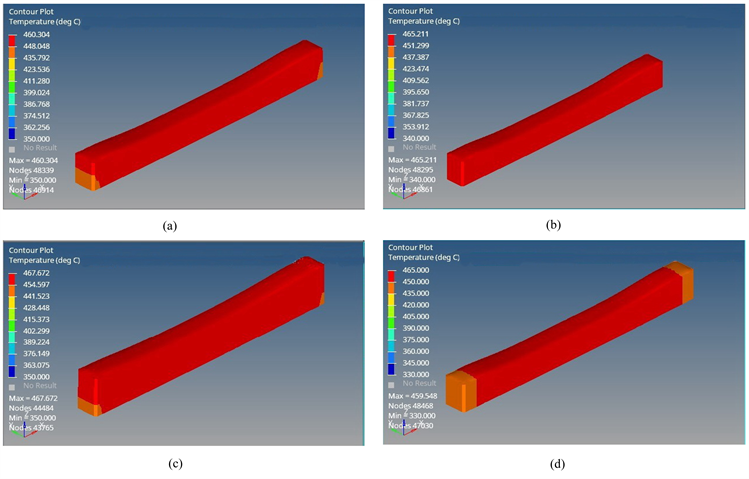
Figure 7. Simulation of extrusion temperature distribution of strip’s cross section. (a) Test 5; (b) Test 6; (c) Test 7; (d) Test 8
图7. 排材截面挤出温度分布模拟结果。(a) 试验5;(b) 试验6;(c) 试验7;(d) 试验8
(a)
(b)
Figure 8. The range and standard deviation of the strip’s extrusion temperature. (a) Extrusion temperature range; (b) Standard deviation of extrusion temperature
图8. 排材温度范围、极差与均方差图。(a) 排材温度范围与极差;(b) 排材温度均方差
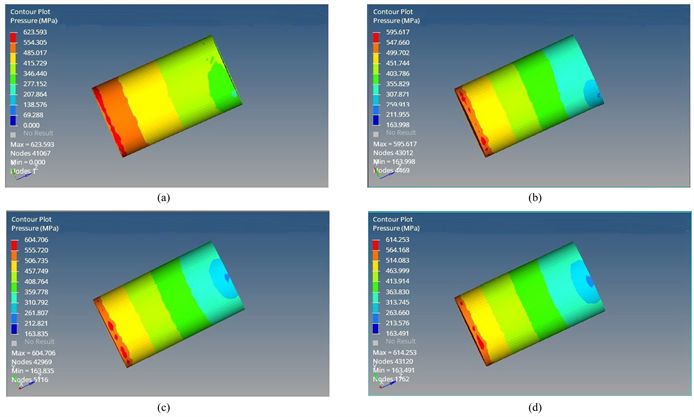
Figure 9. Simulation of specific pressure distribution of extrusion cylinder (side view). (a) Test 5; (b) Test 6; (c) Test 7; (d) Test 8
图9. 挤压内筒比压分布模拟结果(挤压内筒侧视图)。(a) 试验5;(b) 试验6;(c) 试验7;(d) 试验8
(a)
(b)
Figure 10. The range and standard deviation of the extrusion cylinder’s specific pressure. (a) Specific pressure rang; (b) Standard deviation of specific pressure
图10. 挤压内筒比压范围、极差与均方差图。(a) 挤压内筒比压范围与极差;(b) 挤压内筒比压均方差
6. 生产验证
采用模拟得到的最优参数组合,在75 MN挤压机上进行生产试验。挤出的7075排材(截面规格为26 * 310 mm)表面质量良好,力学性能、形位尺寸合格稳定,如图11所示。排材挤压速度从之前的5~8 mm/s提升到了15 mm/s,挤压时间也从之前35 min缩短至20 min,大大提高了生产效率。
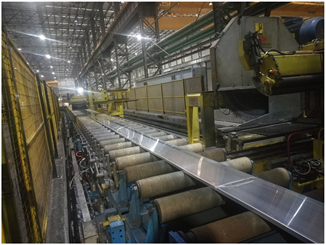
Figure 11. Extrusion of 7075 aluminum alloy strip after parameter optimization
图11. 优化后挤出的7075排材
7. 结论
通过对7075铝合金排材的挤压过程进行仿真模拟研究,得出以下结论:
1) 工作带长度、导流孔深度、挤压杆速和铸锭温度等参数之间的耦合匹配,决定了排材在挤压过程中其横截面金属的流动速度、温度的分布均匀性,以及挤压内筒比压的大小。
2) 7075排材在75 MN挤压机的最优参数组合为:工作带长度为8 mm,导流孔深度为38 mm,挤压杆速为1.0 mm/s,铸锭温度为340℃。
3) 采用正交法和有限元仿真模拟得出的参数进行生产,挤出的排材满足技术标准要求,表明数值模拟能为高强高硬铝合金排材的挤压工艺优化提供有效指导,降低生产试验成本。