1. 引言
伴随着连续铸钢技术的不断成熟和对钢洁净度要求的提高,连铸中间包已经不仅仅局限于传统的储存钢液、稳流和分流的作用,人们开始重视中间包在钢水净化中的作用 [1] [2] [3] [4]。为了提高中间包去除夹杂物的能力,研究者们在中间包内设置适宜的控流装置来改善中间包内钢液的流动特性和延长钢液在中间包内的停留时间 [5] [6] [7]。本文通过改变八流小方坯连铸中间包的不同内部结构,比较中间包内流体流动状态,优化中间包内部构造,得到合理的中间包流场,提高中间包去除夹杂物的能力。
2. 中间包物理模拟方案
2.1. 中间包物理模拟原理
由相似原理可知,高温热态炼钢过程可用低温冷态进行实验室物理模拟。为保证相似性,建立的水模型需要保证几何相似和动力相似 [8]。本实验确定水模型与原型中间包的几何相似比为λ = 1:2。水模型与原型中间包内的流体均已处于湍流流动状态,因此只需考虑弗鲁德准数Fr相等,既能保证动力相似,因此模型(m)与原型(p)之间的流量Q、流速u和时间t的关系可表示如式(1)、式(2)和式(3)所示。
模型和原型的流速关系:
(1)
模型和原型的流量关系:
(2)
模型和原型的时间关系:
(3)
2.2. 实验设备及RTD曲线分析
2.2.1. 实验设备
本实验的设备主要包括有机玻璃材质的中间包、数据采集系统和数据处理系统。在实验中采用DDS-11D型电导率仪测定中间包流体的电导率,电极采用DJS-1型铂黑电极,记录仪为YEW3056型记录仪,用计算机进行处理电导率与浓度之间的关系,绘制RTD曲线。采用高锰酸钾溶液作为示踪剂来显示流体在中间包内的流动过程,用摄像机对高锰酸钾溶液在中间包内的流动过程进行录像。
2.2.2. RTD曲线分析
由于使用电导率仪所测得的是电导率随时间的变化曲线,要对停留时间分布曲线分析之前需要将电导率随时间变化曲线转化为浓度随时间变化曲线,因此首先对所使用的示踪剂(NaCl溶液)进行电导率的测量,对测得的电导率与浓度之间的关系曲线进行拟合,可以得到本试验电导率与浓度的换算方程:
(4)
式中:x——出口处电导探头所测得的电导率,μs/cm;y——出口处示踪剂浓度,mol/L。
经过换算之后可得浓度随时间的变化关系(C(i)-ti),但是这些物理量都是有单位的,要想得到停留时间分布曲线,必须先进行无量纲处理,转变为停留时间分布函数E(θ)-θ的关系。
1) 计算理论平均停留时间τ
(5)
式中:τ——理论平均停留时间,s;V——中间包(反应器)的体积,m3;Q——中间包(反应器)的流量,m3/h。
2) 时间的无量纲处理
(6)
式中:
——
时刻的无量纲时间;
——实际时间,s;τ——理论平均停留时间,s。
3) 浓度的无量纲处理
(7)
式中:
——
时刻的无量纲浓度;
——
时刻的浓度,mol/L;
——时间间隔,s;τ——理论平均停留时间,s。
4) 实际平均停留时间tf
停留时间的分布在一定程度上反映了液体流动特性。由响应曲线可知液体的最短停留时间、平均时间以及混合流区、活塞区和死区各占的比例。对中间包内的钢液流动,希望停留时间长些,使夹杂物有充分时间上浮。
(8)
式中:
——实际平均停留时间,s;
——实际时间,s;
——
时刻的浓度,mol/L;
——时间间隔,s。
5) 最短停留时间tmin
从加入脉冲信号开始到出口得到相应时的最短时间,最短停留时间延长,活塞区扩大,一般是指浓度达到最大浓度与起始浓度差值的5%的时间定义为最短停留时间,又称响应时间。
6) 峰值时间tmax
获得最大电导率值的时间,峰值时间越长、峰值越小,曲线就越平缓,流场也就越合理。
7) 活塞区体积分数
若同一时刻进入容器的流团均在同一时刻离开容器,它们不会和先或后于它们进入容器的流团相混合,此为活塞区。活塞区有利于夹杂物的上浮。
(9)
式中:
——活塞区体积分数;
——活塞区体积,m3;V——中间包(反应器)体积,m3;tmin——最短停留时间,s;tmax——峰值时间,s;(8)死区体积分数
。
死区内流体无流动和扩散,相当于缩小了中间包的有效容积。死区的存在对大颗粒夹杂的上浮影响不是很大,但对于中小夹杂(<20 μm),由于没有流体的流动,也就使中小夹杂没有机会碰撞聚集长大而较迅速的上浮。我们可以这样认为对于中小夹杂,在有限的停滞时间内没有上浮的机会,因而死区对夹杂的去除效率(尤其是中小夹杂)可认为为零。
(10)
式中:
——死区体积分数;
——死区体积,m3;V——中间包(反应器)体积,m3;τ——理论平均停留时间,s;(9)全混区比例
。
当流团一进入容器立即与其它流团完全混合,分不出哪个流团是先来的和后来的,这种流动模式称为全混区。
(11)
式中:
——全混区体积分数;
——全混区体积,m3;V——中间包(反应器)体积,m3;
——活塞区体积分数;
——死区体积分数。
(10)对于单入口多出口中间包的总体RTD曲线来说,在各流流量相同的前提下,取各时刻4流示踪剂浓度的算术平均值作为总体RTD曲线的浓度。
2.3. 中间包参数及实验方案
由于该八流中间包为分体式对称结构中间包,由两个独立的四流中间包组成。因此,为简化研究的复杂性,本研究仅对其对称结构中的四流开展研究,另外四流流场结构视为与本流场相同。
2.3.1. 中间包原型参数
本研究中间包原结构总体示意图及挡墙结构如图1及图2所示。
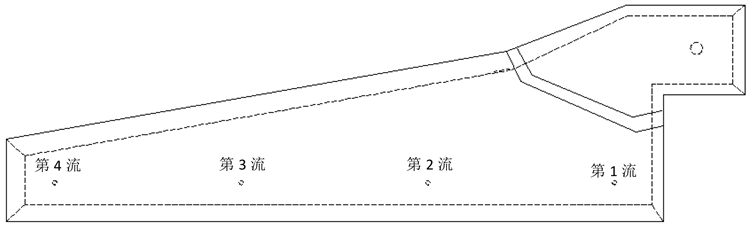
Figure 1. Overall diagram of tundish original structure
图1. 中间包原结构总体示意图
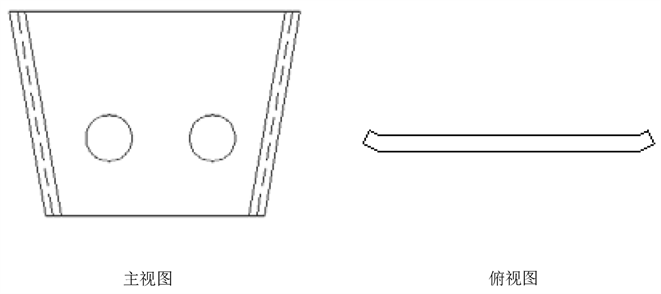
Figure 2. Schematic diagram of original retaining wall structure
图2. 原挡墙结构示意图
2.3.2. 中间包新内部结构参数
在本实验设计新挡墙结构及湍流控制器作为控流装置,中间包新挡墙的内部构造及具体挡墙结构如图3和图4所示,湍流控制器结构如图5所示。
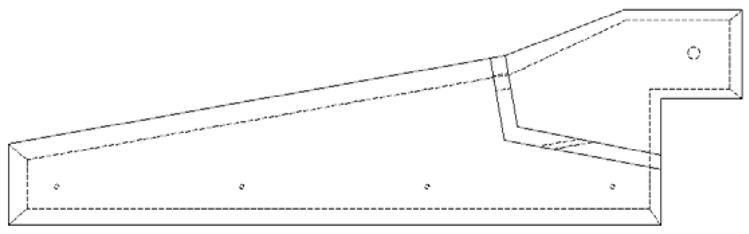
Figure 3. Schematic diagram of internal structure of tundish new retaining wall
图3. 中间包新挡墙内部结构示意图
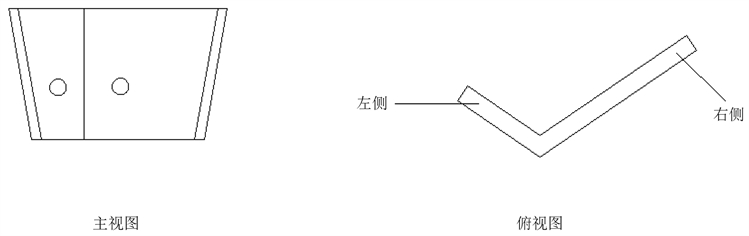
Figure 4. Schematic diagram of new retaining wall structure
图4. 新挡墙结构示意图
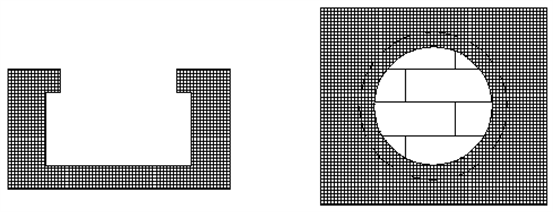
Figure 5. Structure diagram of turbulence controller
图5. 湍流控制器结构示意图
2.3.3. 物理模拟实验方案
中间包流场物理模拟实验方案以不同的挡墙结构及是否加湍流控制器进行设计,具体如表1所示。本实验以工厂常用拉速1.6 m/min为实验拉速。
3. 物理模拟实验结果
3.1. 不同挡墙结构对中间包内流场特征的影响
本实验模拟铸坯拉速为1.6 m/min,按照实验方案,在不加湍流控制器变换挡墙的条件下,不同方案各流及总体RTD曲线 [9] [10] [11] 及RTD曲线特征参数及各区域占比如图6、图7所示。
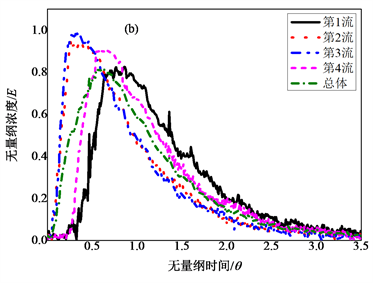
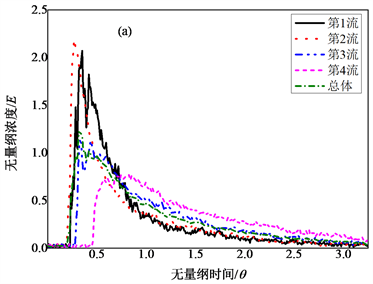
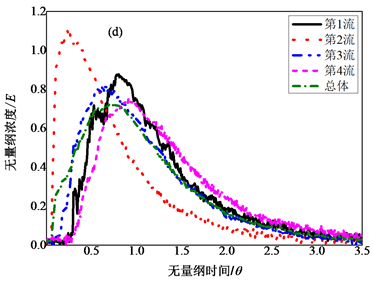
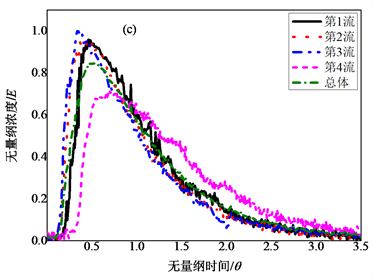
Figure 6. Each flow and overall RTD curve of different schemes
图6. 不同方案各流及总体RTD曲线
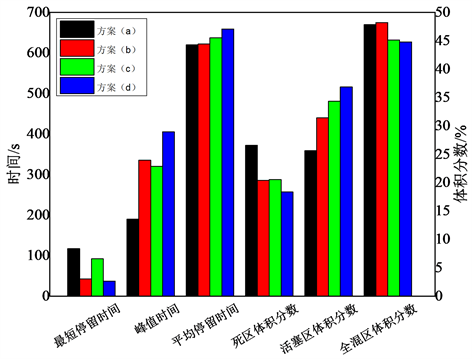
Figure 7. Overall RTD curve characteristic parameters of different schemes and proportion of each region
图7. 不同方案总体RTD曲线特征参数及各区域占比
图6及图7反映了不同挡墙方案下,各流及总体RTD特征曲线、特征参数及死区、活塞区、全混流体积分数的变化情况。从图6中可以看出,方案(c)的各流RTD曲线的变化情况几乎同步表现出良好的一致性,且曲线拖尾现象不是很明显,表明死区较小,活塞区和全混区较大,有利于夹杂物的上浮去除。并由图7可以看出,其中最短停留时间中方案(a)时间最长,次之为方案(c),反应出二者的短路流相对较弱,流体在中间包停留时间长,有利于夹杂物上浮;从峰值时间、平均停留时间上可以看出新挡墙比原挡墙明显的提高,这为夹杂物的聚集长大提供了有利的先决条件。同时,死区体积分数明显降低,活塞区体积分数明显提高,有利于夹杂物的上浮去除。但综合数据分析,在无湍流控制器的条件下,采用方案(c)的挡墙其平均停留时间,死区、活塞区体积分数的变化情况虽不及方案(d),但相差各流一致性保持最佳,且有效减少短路流,有利于各流钢液温度和成分的均匀化,有利于夹杂物的去除,因此方案(c)为最佳方案。图8为实验过程拍摄的以高锰酸钾为示踪剂在不同时刻中间包内的流场图。可以看出在两方案的相同时刻,方案(c)流体流动的更加迅速,扩散更面积更大,体现出各流较好的一致性,与RTD曲线计算结果一致。
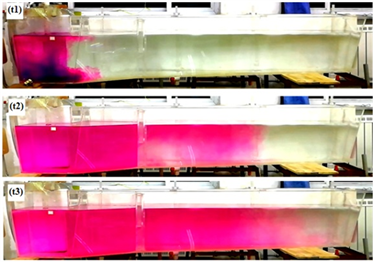
方案(a) 方案(c)
Figure 8. Flow field diagram of tundish experiment process (t1) 3 s, (t2) 50 s, (t3) 120 s
图8. 中包实验过程流场图(t1) 3 s;(t2) 50 s;(t3) 120 s
3.2. 加湍流控制器实验对比
在方案c中加入湍流控制器,模拟有湍流控制器情况下中包流场的变化情况。经模拟实验后得到的结果数据如表2所示。方案(d)与不加湍流控制器的方案(c)的“总体”RTD数据结果相比,除峰值时间有所减少,其最短停留时间延长了6.5%,平均停留时间增加了2.4%,其余数据几乎相同,说明加湍流控制器后,短路流得到更好的抑制,流体的停留时间增加,更有利夹杂物的去除。因此,L型向上开孔的挡墙加湍流控制器是最优内控结构。
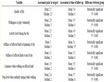
Table 2. Flow field diagram of tundish test process
表2. 加湍流控制器后物理模拟结果
4. 工业试验对比
工业试验在某钢厂在方坯连铸机上进行,试验钢种为45钢和40Cr钢。为对比流场优化效果,分别设置1号中间包使用原挡墙,2号中间包使用最优内控结构,共进行6个浇次试验,共22炉抽取34个样品,并对样品分别进行夹杂物检测分析。将各夹杂物检测数据进行统计整理,统计结果如表3所示。
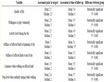
Table 3. Data statistics of slab inclusions
表3. 铸坯夹杂物数据统计表
从表3可以看出,最优内控结构与原挡墙对A类、C类及D类夹杂物出现比例、平均级别的结果相同或相差很小,优化流场并未对这几类夹杂物去除产生更优的效果,分析原因主要是这些夹杂物有些是凝固时产生内生夹杂,如硫化锰大部分在凝固时产生,或此类夹杂在钢中存在较少,如C类夹杂物,或小尺寸球状夹杂物难以去除。但B类及DS类夹杂物在最优内控结构出现比例大幅低于原挡墙,分别降低了62.5%和54.5%,在夹杂物平均级别结果可以看出新挡墙+湍流器比原挡墙降低了74.3%和65.7%,可见夹杂物数量降低效果非常明显,表明B类氧化物夹杂,在延长停留时间、改变流体运动轨迹的优化流场中,可以增加碰撞机会,迅速长大并快速去除,同时也可以看出,大颗粒夹杂Ds类也显示出明显去除效果,因这类夹杂物直径大,在优化内部结构后,停留时间延长及更加合理的流体流动形式,既可将其很好的去除。
综上所示,对于不同类型的夹杂物,最优内控结构对于B类夹杂与Ds类夹杂从出现占比以及平均级别方面相比于原挡墙均具有较好的去除作用。
5. 结论
1) 根据相似原理,建立中间包物理模型。在实验室中对不同结构挡墙进行实验,并将得到RTD曲线进行计算分析,综合各个特征参数可以看出,L型向上开孔的挡墙的流场形式最优;
2) 针对湍流控制器对中间包的影响,进行实验室实验,研究发现加入湍流控制器后中间包流场优于无湍流控制器中间包流场,因此L型向上开孔挡墙加湍流控制器为八流中间包的最优内控结构;
3) 在工业试验中,将最优内控结构与原挡墙进行对比试验,共取样34个,并将样品进行夹杂物检测,经统计分析可知采用最优内控结构铸坯中B类与Ds类夹杂在出现占比以及平均级别两方面相比于原挡墙均有明显的数量下降,达到了优化中间包内部结构净化钢水的目的。
基金项目
辽宁省教育厅高等学校创新人才支持计划(LR2020066);辽宁省本溪低品位非伴生铁矿优化应用重点实验室。
NOTES
*通讯作者。