1. 引言
完全由碳和氢原子组成的碳氢化合物可以根据其化学性质分为烷烃或链烷烃、烯烃或烯烃或芳香烃。近两个世纪以来,随着工业的快速发展,碳氢化合物已成为必不可少的化学物质和能源,并在我们的日常生活中得到广泛利用。随着新兴产业的发展,此类产品又被广泛应用于集成电路、显示面板、光伏等行业的生产过程中,这类气体被称为“电子特种气体”,而电子级丙烯就是其中的重要组成部分。
电子级丙烯由于含有碳碳双键,容易发生化学反应生成另一种物质,进而在衬底表面沉积,主要用作外延、沉积气体;作为成膜气体,主要作用是非晶硅碳生长,丙烯可以在硅片等半导体器件上形成无定形碳,可以粘合光刻胶,同时辅助保护掩膜下层结构受到刻蚀,是半导体制造用的一种关键气体。丙烯为低压液化气体,在常温常压下为无色、有烃类气味的气体,极易燃,毒性并不大,人吸入后有麻醉作用,相对分子质量为42.09,沸点为−47.7℃,熔点为−185.2℃。
如今,随着半导体技术快速更迭,要求更大的晶圆尺寸、更细微化的制程技术,对电子级丙烯的需求会越来越大,纯度的要求越来越高。此外,在全球化石能源的紧缺和环境污染的背景下,大力发展清洁能源和低碳环保技术的政策已经被多数国家采纳贯彻施行,我国的太阳能电池和半导体发光器件及相关产业得到了迅猛发展,电子级丙烯市场空间非常广阔。
2. 电子级丙烯纯化技术的方法
通过对工业用丙烯的纯化精制,可获得电子级丙烯产品。工业级丙烯纯度为99.5%,其主要杂质有丙烷、乙烯、氧气、二氧化碳和水等,根据原料中各杂质的沸点与丙烯的沸点来比较,可分成轻组分和重组分两类。其中,轻组分即杂质沸点低于丙烯沸点的组分,如乙烯、氧气、二氧化碳等,重组分则为杂质沸点高于丙烯沸点的组分,如丙烷、水等;又因为丙烯沸点(−47.7℃)与丙烷沸点(−42.1℃)十分相近,且两者相对挥发度极为相似,所以丙烯和丙烷的分离尤为重要,对最终产品中杂质含量是否符合标准影响巨大,在很多文献中,丙烯和丙烷的分离已经成为了一大课题。
2.1. 吸附法
李中元 [1] 公开的一种通过化学吸收法除去丙烷杂质的方法逐渐兴起。其原理是,相较于丙烯,丙烷具有很大的化学活泼性,能与硫酸起加成反应,生成异丙基硫酸酯,进而从丙烯原料气中除去。加工后的气体经过两级吸附器除去残余的C4以上的烃类杂质;再把气体通入冷凝器,在−45℃的环境下让丙烯冷凝成液体,在此将不凝的N2、O2、CH4等低沸点杂质除去,制得纯度为5N的高纯丙烯。此法的产品收率高,杂质少,且容易分离,除产品本身外,不带有其他有害、有毒的副产物,操作也较方便,是高纯丙烯制备的理想技术。
丙烯/丙烷的分离传统上是通过高耗能的低温蒸馏过程来进行的,由于丙烯和丙烷的沸点接近,很难将两者高效分离。基于膜的技术已经成为一种更节能的丙烯/丙烷分离的替代品。已被探索的候选膜包括聚合物膜 [2] 、碳分子筛 [3] 、沸石和促进转运膜 [4] 。然而,几乎所有这些膜都受到一些关键缺陷的限制。有人提出,1巴的最小渗透率和35巴的选择性可以使膜分离法完全取代丙烯装置中的精馏装置;然而,目前几乎所有的高分子膜在渗透性和选择性方面都不能满足上述要求。聚合物膜的性能受到渗透性和选择性的上限衡量以及塑化问题的限制。沸石如八面沸石和ETS-10已显示出有希望的单组分分离性能,但对混合物的选择性显著下降。碳分子筛(CMS)和促进传输膜可以满足上述要求;然而,CMS膜很难扩大规模,而促进运输膜存在着长期稳定性问题。
沸石–咪唑酸骨架(ZIFs)作为一类基于沸石拓扑结构的新型纳米多孔材料,由过渡金属离子(锌/钴)和咪唑盐/咪唑盐型连接剂组成,因其具有类似沸石的永久孔隙、均匀的孔径以及优异的热稳定性和化学稳定性,且具有较高的比表面积和孔容的高度有序晶体材料,成为了制备新型分子筛膜的候选材料。该材料分离原理是通过调节有机配体进而可控调节功能基团和孔径大小,其中的无机阴离子位点可选择性的吸附丙烷且容量很高,通过穿插结构可调节孔道立体空间结构,进一步提高吸附选择性和吸附容量。近年来,几种类型的ZIF膜已经成功合成,并在气体分离中显示出很有前景的分子筛性能,在C2/C3分离中表现出优异的分离性能,能够有效地分离丙烯和丙烷混合物。
Cravillon等人 [5] 报道了一种制备ZIF-8晶体的方法:分别将Zn(NO3)2∙6H2O和2-甲基咪唑溶于甲醇中,然后将2-甲基咪唑溶液加入到Zn(NO3)2溶液中,将液体混合物用磁棒搅拌30~40分钟,然后在不搅拌的情况下放置24小时。通过离心收集溶液中形成的白色胶体颗粒,再用甲醇洗涤,将获得的ZIF-8粉末在室温下真空干燥过夜,再分散到甲醇中,最后超声处理30分钟就可获得分散良好、稳定的ZIF-8悬浮液。在120℃的水溶液中,通过二次生长法重复制备薄(2.5 pm)、高质量的ZIF-8膜。此膜对于C3H6/C3H8混合物的渗透性和选择性都随着进料压力的增加而降低。C3H6/C3H8的选择性随着温度的升高而降低。ZIF-8膜在大气条件和C3H6/C3H8流中都是稳定的,这表明其具有巨大的实际应用潜力。
2.2. 精馏法
丙烯主要通过三种途径获得:68%作为乙烯蒸汽裂解厂的副产品,29%作为流态化催化裂解的副产品,3%通过烯烃转化和丙烷脱氢等方法获得;然而,无论来源如何,始终需要对丙烯和丙烷进行分离。对于沸点相似或共沸的混合物,人们研究了不同的精馏方法,其中有共沸精馏、萃取精馏、吸附精馏等操作方法。由于丙烷和丙烯具有相似的分子大小和物理性质,并且在很大的压力范围内,纯组分沸点非常接近,因此很难通过普通蒸馏将它们分离。为了克服这一问题,有人提出了改进,以达到所需的纯度并且降低丙烯–丙烷分离过程的能耗。
2.2.1. 常规精馏
Alcantara-Avila等人 [6] 提出了一种通过热泵蒸馏和高压或低压蒸馏分离丙烯和丙烷的方法。高压精馏由于塔顶温度高于40℃,可以用冷却水冷凝产生回流,塔釜可用低压蒸汽或热水加热,设备简单,但此法的缺点也很明显,即回流比大(10~20),塔板数量多(120~150),压力大(1621~2634 kPa),能耗高,投资成本高。而如果采用低压蒸馏工艺,由于丙烯/丙烷相对挥发性高,级数和回流比会减少,但是塔顶需要低温冷凝而不是水冷却,会大大地增加运行成本。
许少鹏等人 [7] 公布了一种双塔精馏代替单塔精馏的方法,可直接将纯度为99.5%的工业级丙烯纯化为99.999%的电子级高纯丙烯,此法按照工艺流程依次分为三个系统:原料供应系统、丙烯精馏系统(如图1所示)、丙烯充装系统。在工业生产准备阶段,为保证系统的管路无泄漏、无污染,需提前向系统中通入氮气,以置换管路中的空气并检测其气密性,然后对两级精馏塔的分析点取样分析,水分含量达到要求后保持系统压力,此时进入到正式精馏生产阶段;将工业丙烯混合物料经原料供应系统管路通入到一级精馏塔,在塔内进行充分的热质交换,丙烷、丙炔等重组分汇聚在塔釜,含丙烯、一氧化碳等轻组分则汇聚在塔顶,轻组分中部分重组分经冷凝器冷凝液化后作为回流液重返一级精馏塔,其余轻组分和丙烯作为原料进入二级精馏塔,同样在塔内进行充分的热质交换,一氧化碳、乙烯等轻组分汇聚在塔顶并收集至去尾气处理装置,其中部分重组分物质经冷凝液冷凝回流至塔内,在塔釜收集到精馏后的高纯度丙烯,然后分别对二级精馏塔塔釜和丙烯充装系统进行取样点分析,当达到符合产品质量标准的杂质含量要求后,将纯化后的丙烯输出至产品充装系统进行充装。此法中两级精馏塔塔顶安装冷凝器,塔釜安装再沸器,可依靠对塔内温度与压强的调节来灵活进行脱重和脱轻的选择,与传统技术相比,此法结构简单,设计合理,在工业生产中有很大的可行性。
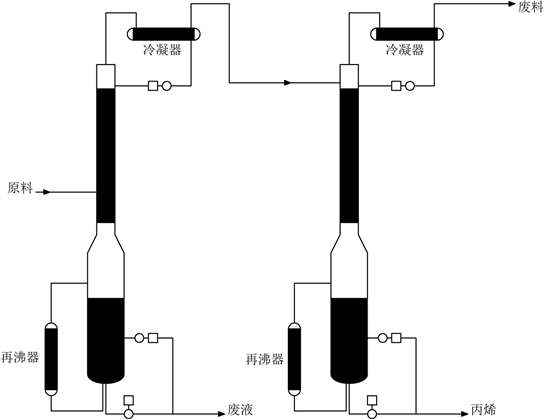
Figure 1. Propylene rectification system
图1. 丙烯精馏系统
2.2.2. 萃取精馏
萃取精馏工艺通过添加一种称为分离剂的溶剂而获得了比高压蒸馏工艺的优势。用常规精馏分离这些混合物很困难,因为它们的挥发性重叠。而在分离剂的作用下,丙烯的相对挥发性与丙烷不相近。这种溶剂的目的是改变丙烷的活性系数,有利于链烷烃–烯烃混合物的分离。这就解释了为什么此法对这类混合物的分离更有吸引力。因此,分离溶剂的选择在萃取精馏过程中起着重要的作用。
Liao等人 [8] 提出了一种使用乙腈水溶液作为分离剂来达到修饰丙烷活度系数,从而增加体系在单体以上的相对挥发性,促进石蜡烯烃混合物分离目的的方法,实现了需要少量塔板、小塔径、低能耗的工艺,并提供了高纯度的丙烯,与高压蒸馏相比,锅炉负荷节省13.2%,冷凝器负荷节省79.1%,理论级数减少25%。
尹华清等人 [9] 提出了一种使用正戊烷(骨架溶剂A)作为分离剂生产出纯度为99.7%的丙烯;降低了能耗,平均分离1吨丙烯的能耗为4.18~5.02 GJ,而现有技术需要7.53~8.37 GJ。
Valdez等人 [10] 提出了一种使用n-甲基-2-吡咯烷酮(NMP)作为分离剂提高混合物分离的方法,因为NMP无毒且符合生态标准且具有良好的分离效果,首先被Chen等人提出。具体工艺流程为:使用两座精馏塔,一级精馏塔为萃取精馏塔,二级精馏塔为回收塔,把一级精馏塔设计成50级,丙烯混合物在311.15 K和2000 kPa的供应压力下送入第15级,NMP溶剂在293.15 K和2000 kPa的供应压力下送入第二级,保持塔内压力为1400 kPa,塔内进行充分反应,丙烷作为馏出产物在塔顶获得,丙烯溶剂混合物作为底部产物被送入二级蒸馏塔,保持此塔中的压力为1400 kPa (如图2所示)。此时,由于丙烯和溶剂之间的沸点温度范围宽,丙烯作为馏分产物获得,而底部产物溶剂被送至储罐处理回收。此法中的分离剂NMP具有沸点高的特点,这有助于减小精馏塔的尺寸和回流比,并降低冷凝器和再沸器的热负荷,而它又可回收循环利用,符合节能减排和经济节约的理念。
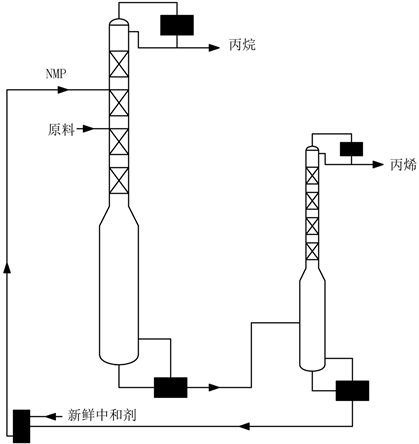
Figure 2. Extractive distillation system
图2. 萃取精馏系统
2.2.3. 吸附精馏
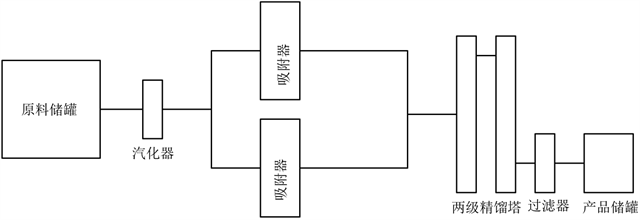
Figure 3. Adsorption distillation process
图3. 吸附精馏流程
为达到电子级丙烯纯化的要求,各种方法参差不齐,优劣各异,但此类中大部分的方法都不适合在实际的工业生产中应用,存在着能耗高、工业条件控制难和原材料更不易获得的问题,还停留在实验室少量制备的过程中,就比如吸附膨胀法和异丙醇催化脱水法等。对此,针对于工业化和产业化难实现的困境,一种采用上文中提到的双塔精馏法和吸附法相结合的方法取得了良好的效果并实现应用,产品纯度达到了电子级丙烯的要求,可直接用于集成电路芯片制造。
赵毅等人 [11] 公布了一种吸附和精馏结合的方法,原料经过加热气化、分子筛吸附脱水后进入一级精馏塔脱除重组分,塔顶的物料进入二级精馏塔进行脱除轻组分处理,过滤后收集进入产品储罐,获得高纯丙烯产品,采用色谱DID检测碳氢杂质总和为85 × 10−6 (如图3所示)。此法为了保证产品的洁净要求,提纯设备材质为不锈钢材质,内表面经过抛光处理,避免内表面沾污带来的污染。
2.3. 催化剂法
考虑到丙烷的分离难点,除了精馏吸附的方法,传统的处理方式是通过丙烷催化转化反应脱氢后转为丙烯这一路径,主要催化剂有铬系催化剂(如ABB Lummus公司的氧化铬/氧化铝催化剂)和铂锡催化剂(如UOP公司的铂锡/氧化铝催化剂),铬系催化剂虽然对原料杂质要求低且价格低廉,但是存在环境污染严重,不符合高效节能导向的问题。铂锡催化剂虽然活性高、选择性好,但是金属铂的价格昂贵,催化剂成本较高,价格居高不下。而且针对痕量ppm级的丙烷杂质需要彻底催化转化,传统的催化剂净化深度根本不够,需要进一步改善。因此,开发性能优良的高纯丙烯中痕量丙烷脱氢催化剂具有现实意义。
马建修等人 [12] 公开了一种高纯丙烯中痕量丙烷转化的催化剂及其制备方法,此法利用铁的催化活性位与丙烷发生脱氢催化反应,为了提高催化剂活性位的分散性,加入磷原子,形成P-Fe网状型结构,使P原子均匀规则的分散在催化剂表面,提高催化活性。通过络合剂、粘合剂、涂覆焙烧等高效制备方法使催化活性中心与载体相结合,并实现造粒。该反应制备简单、原料易得,生成的副产物为氢气和少量的甲烷、乙烷等,这些杂质与丙烯沸点相差较大,很容易通过精馏吸附去除掉,具有能耗低和催化度高的特点。
2.4. 金属有机框架材料
丙烯和丙烷混合物的分离是石化工业中最重要且最具挑战性的过程之一。目前,这种分离主要是通过低温精馏实现的。由于丙烯和丙烷的沸点接近,典型的丙烯和丙烷分馏塔需要200级以上的级数和12~20的高回流比,是石化工业中最耗费资金和能源的工艺之一。因此,希望能开发出能够显著降低碳氢化合物分离的能源成本的替代分离技术。而多孔金属–有机框架(MOFs),也称为多孔配位聚合物,代表了一类新的多孔材料,由于其易于调节、可设计和功能性,为碳氢化合物分离提供了巨大的前景。已经设计和合成了许多MOFs,以在各种烃分离中显示出优异的分离性能。
事实上,基于传统活性炭和沸石材料的碳氢化合物分离的吸附分离是在20世纪90年代中期成功实现的。然而,这些多孔材料在调节孔径、形状和功能化方面非常有限,基本上只能通过控制热活化和金属阳离子的取代来实现,这限制了分离性能。与传统的活性炭和沸石相比,微孔MOFs在气体分离方面具有一些独特的优势:1) 可设计性:MOFs的网状化学使目标材料的前瞻性设计具有很大的结构可预测性,从而准确控制结构/拓扑结构和孔隙率 [13] ;2) 可调谐性:微孔空间/尺寸可以通过金属簇和有机连接体的司法选择进行微调 [14] ;3) 易于功能化:一些功能位点可以简单地固定在MOFs的孔表面,以引入特定的相互作用来识别气体分子,从而显著提高其气体分离能力 [15] 。因此,已经开发了大量MOF材料作为碳氢化合物分离的分离吸附剂。特别是在过去几年中,一些互补技术,如单体/粉末X射线/中子/同步加速器衍射研究,已被广泛用于表征气体加载结构 [16] ,这可以直接确定MOF框架中的气体吸附位点,从而有助于更好地理解吸附和分离机制。通过对孔结构的精确控制,开发的MOFs对C3H6/C3H8的分离表现出理想的分子筛选效果,从而获得有史以来最好的超高选择性。
Cadiau等人 [17] 公布了一种氟化MOF,即NbOFFIVE-1-Ni,它可以在环境条件下完全将C3H8从C3H6排除。NbOFFIVE-1-Ni与SIFSIX-3-Ni等网,由Ni(II)-吡嗪方栅层与(NbOF5)2−柱桥接而成。Nboffvee-1-Ni中的无机柱(NbOF5)2−取代了(SiF6)2−,使金属–氟的距离变长,从而使吡嗪倾斜。因此,NbOFFIVE-1-Ni的孔径比SIXSIX-3-Ni的孔径要小得多。当吸附C3H6分子时,发现吡嗪倾斜角度较大,导致栅极打开,C3H6分子可以通过孔隙。相比之下,当C3H8分子通过时,吡嗪没有发生额外的倾斜。进一步实验证实,从50/50的C3H6/C3H8混合物对C3H8进行完全的分子筛选,C3H6的产率约为0.6 mol/kg。
Wang等人 [18] 提出了一种设计微孔MOF,即Y6(OH)8(abtc)3(H2O)6(DMA)2(Y-abtc),其具有表现出C3H8分子排斥行为的笼状孔。Y-abtc的框架具有ftw拓扑结构,具有适合于分子分离的大笼和小窗口。受限孔径正好介于C3H6和C3H8的动力学直径之间,使得Y-abtc对C3H8完全排斥。此外,作为通道中的电荷平衡阳离子,二甲铵与C3H6分子的具有很强的相互作用,有助于提高C3H6吸收量和同位吸附热。实验表明,Y-abtc可以生产纯度为99.5%的C3H6,且有较长的保留时间。结合C3H8分子的排斥性、高稳定性和可扩展合成,Y-abtc有望成为一种潜在的工业分离材料。
Wang等人 [19] 公开了一种多孔MOF,即[Zn2(btm)(btk)]。通过在氧气流动下加热[Zn2(btm)2] (MAF-23),从而氧化一半的btm2−配体,形成具有C=O键的btk2−。一方面,MAF-23-O中的羰基通过形成氢键为C3H6分子提供了额外的识别位点,而C3H8分子不能与之相互作用,导致了较高的热力学选择性。另一方面,氧化降低了框架的灵活性。由于羰基与芳香环结合,C3H6分子需要更多的能量才能扩散到MAF-23-O中,从而提高了动力学选择性。实验表明,等摩尔C3H6/C3H8混合物对MAF-23-O的吸附选择性在298 K和1 atm下远高于MAF-23。因此,通过同时提高热力学和动力学选择性,可以获得较高的吸附选择性。
3. 小结和评论
丙烯纯化常用的精制方法有吸附、精馏、催化、金属有机框架材料选择性吸附等手段。理论上,吸附和膜技术可以比精馏过程使用更少的能量,可提供更高的资本投资回报,但此过程需开发出具有特定性能的吸附剂或膜材料,并且选择性不高;精馏方法是丙烯纯化的主要技术,工艺路线安全可靠,结构简单,易于大规模工业化生产,但对设备的要求比较高,一般的小塔径、单塔系统无法生产出杂质含量达标的产品,且对塔内的温度和压力必须准确调控,这就导致操作要求高且能源密集;催化剂法能耗低,催化深度高,使用寿命长,但制备难度大,并且有些催化工艺需搭配精馏工艺来进行生产,纯化步骤较多;金属有机框架材料选择性好,但目前报道的MOFs绝大部分是对丙烯有优异的选择性,稳定性差,合成过程中的高成本和困难抑制了其发展潜力,工业化应用难度高。