1. 引言
滚珠丝杠是精密机床进给系统中常用的直线进给传动装置,具有高精度和高效率的特性 [1] 。该系统由丝杠轴、螺母工作台和滚珠组成,使用伺服电机带动丝杠轴旋转,从而带动工作台产生直线运动 [2] 。滚珠丝杠通常采用半闭环控制系统,因此热变形产生的位置误差无法被纳入位置控制回路中 [3] 。随着工作速度和精度的提高,热误差对加工精度的影响越来越大,而非均匀热场是产生热误差的主要原因之一,在精密机床总加工误差中,热误差占据40%~70% [4] 。因此,降低热误差一直是机床加工工程的研究重点。
滚珠丝杠热误差的降低方法包括消除和补偿。消除热误差需要进行设计优化、预拉伸等措施,成本高且许多设备无法改造 [5] 。补偿热误差则是通过计算得到误差位移,然后增减位移来补偿误差。热误差模型有理论模型和经验模型两种。理论模型基于产热机理和热传导原理,通常用于仿真分析 [6] 。例如,Xu [7] 等人使用有限元分析和集总热容法建立了应用于滚珠丝杠空气冷却系统的热行为模型。经验模型基于机械学习理论,建立的模型无需考虑传热学过程,直接寻找信息与热误差之间的对应关系。
理论上,在滚珠丝杠系统中,丝杠轴的温度场信息与热变形信息存在直接映射关系。因此,基于经验模型的热误差补偿方法因实时性与准确性而广泛应用于生产中 [8] 。Jin [9] 等人用神经网络模型研究了滚珠丝杠进给系统的温度和热变形,使用热阻及其调节器和红外辐射温度计测量滚珠丝杠轴承、丝杠轴敏感点温度和工作条件作为输入,得到了工作台的动态热位移,实现了不同工况下热误差的补偿。然而,由于该模型输入测温点较少,无法解决非均匀热场产生的热变形 [10] 。且由于滚珠丝杠结构特性,使用接触式测温设备测量丝杠轴温度困难,因此需要使用红外热像仪记录温度场信息 [11] 。王全宝 [12] 等人使用红外热像仪记录温度场信息用于验证所提出的有限元分析模型的准确性。然而,由于滚珠丝杠光滑表面和复杂几何结构导致其易受外界干扰,因此红外热像仪测得的温度场精度有限 [13] 。实际生产车间中存在各类干扰,导致红外热像仪记录到的温度场信息含有许多干扰和无效信息。因此,大多数动态热误差补偿模型在实际应用中,使用仿真模型计算得到温度场信息,红外热像仅用于检验模型有效性。
近年来,人工神经网络发展迅速,其中卷积神经网络(Convolutional Neural Networks, CNN)在计算机视觉和分类问题中大有作为 [14] 。Helbing [15] 等人使用深度学习有监督学习方法检测风力涡轮机故障。Li [16] 等人提出了基于深度学习的核反应堆瞬时运行状态聚类方法。Al-Antari [17] 等人建立了深度学习检测与分类的CAD系统,用于判断乳腺病变情况。随后,部分学者开始将注意力从可见光图像转移到不可见光图像,使用卷积神经网络识别红外热像仪记录的温度场图像。Ornek [18] 等人使用红外热像仪记录婴儿体温热像图并使用卷积神经网络模型判断健康情况。Akram [19] 等人使用红外热像仪读取光伏模块工作温度并开发深度学习模型识别热像图自动检测损坏元件。
随着卷积神经网络与计算机技术的普及,本文利用红外成像与CNN模型开发一种滚珠丝杠进给系统非线性热误差动态补偿方法,并建立基于卷积神经网络的热误差分段补偿模型。通过挖掘红外热像图中的有效信息建立实时红外热像图与当前热变形的映射模型,在工程环境下,训练神经网络模型并验证其有效性与准确率。研究旨在开发实时的热误差分段补偿模型,并将位移误差补偿表发送给控制器完成补偿。
2. 滚珠丝杠进给系统热误差动态补偿方法
2.1. 滚珠丝杠的动态补偿原理
对于一般的丝杠轴,其轴向长度远大于径向长度,因此在本文中研究其热变形产生的位移误差时仅考虑其轴向误差。Mayr等人 [20] 提出在均匀的温度场下,滚珠丝杠热变形可以视为一维线性膨胀。然而,在机床中的滚珠丝杠轴行程较长,通常轴向热变形是由于不均匀的温度场产生的。因此,在较长行程的滚珠丝杠轴中,直接使用一维线性膨胀模型作为预测模型,可能会使得中间点的位置误差过大。如果将整体的滚珠丝杠轴沿轴向均匀地切分成足够小的n等分,那么可以将每段的热变形视为线性膨胀,工作台每个位置的热误差可以通过相邻两个分段点线性插值得到。如公式(1) (2)。
(1)
(2)
其中,x为滚珠丝杠工作台的位置,单位为mm;D为其补偿值,单位为μm;l0为最小分段长度,单位为mm;
,
为补偿模型的各段补偿模型参数,该参数通过基于深度学习的分段热误差预测模型
获得;
为温度场变化矩阵,即红外成像所获得的信息。
本文所述滚珠丝杠的热误差补偿方法,通过红外成像原理,根据设定的更新频率不断地读取滚珠丝杠温度场,将其输入基于卷积神经网络的热误差预测模型
中,计算并制作为位置补偿表。使伺服电机在伺服循环时不断地读取补偿表,以此实现实时动态补偿热误差。其中,热误差补偿模块与滚珠丝杠系统工作模块相互独立运行。
2.2. 热误差预测模型的建立
2.2.1. 分段预测模型的建立
本文所述的热误差预测模型
是由n个已训练好的卷积神经网络模型CNN_1~CNN_N组成,n为上述滚珠丝杠补偿模型的分段数,该模型分别将温度变化矩阵
分别输入相应的分类模型中,即可得到每个分段点的误差预测值。其工作原理如图1所示。
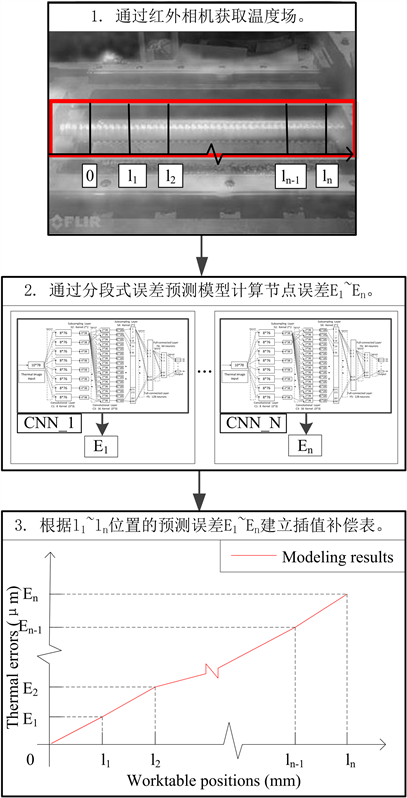
Figure 1. Principle of segmented thermal error prediction model construction
图1. 分段式热误差预测模型建立原理
如上图所示,通过红外相机获取的温度变化矩阵输入CNN_1~CNN_N中,得到每个工作点的热变形E1~En,即可建立误差补偿表。
2.2.2. 卷积神经网络模型
CNN是一种经典的用于图像处理的深度学习模型,其核心在于构建多个滤波器提取图片的敏感信息,通过卷积与池化的方式逐级挖掘并抽象有效信息。并且,卷积神经网络中卷积层的滤波器每次仅与局部的数个输入连接,而非所有输入,因此,与传统BP神经网络相比具有更高的效率。
本文使用的CNN_N模型为改进的LeNet-5网络,该网络具有以下特征层:
1) 卷积层:卷积层是卷积神经网络的核心层,该层的每个神经元与输入层的相应位置周围区域进行局部连接。卷积层的输入以二维矩阵表述
,输出表述为
。其公式表述为:
(3)
其中,
为位置为(i, j)的神经元输出;K为输入层的层数;f为卷积核尺寸;
为第k层输入层;s0为步长;wk为第k层的权重矩阵;bk为第k个卷积核的偏差。
2) 池化层:池化层是用于保持信息不线性的同时降低信息冗余,减少卷积层中包含重复信息的神经元。本文使用的池化方式为均值池化,其公式表达为:
(4)
其中,
为位置为(i, j)的神经元输出;
为输入矩阵;f为池化尺寸。
3) 激活函数:激活函数的主要作用的引入非线性元素。激活函数使神经网络在输入与输出之间能够建立非线性模型,并使输出归一化。本文使用的激活函数为sigmoid函数,其公式表达为:
(5)
4) 全连接层:全连接层是将输出层的神经元与输入层的每一个神经元进行全连接,能够在卷积池化后整合所有的局部信息。全连接层的输入输出均为一维矩阵,表述为
,
,其公式表述为:
(6)
其中,
为输出层的第i个神经元;wij为输出层的第i个神经元对应输入层第j个神经元的权重值;f为输出层的神经元数量;bi为输出层第i个神经元的偏差。
依据上述四类神经元构建改进Lenet-5模型。其模型结构如表1:
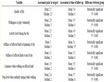
Table 1. Improvement of Lenet-5 layer attribute
表1. 改进Lenet-5层级属性表
3. 实验与分析
3.1. 实验环境
实验装置为一端固定一端支撑式滚珠丝杠台。为避免反向间隙误差,测量时,工作台均沿同一方向运动。滚珠丝杠台由POWER PMAC运动控制卡控制,设定编码器最小单位为0.0001 mm。工作台位置由激光干涉仪MCV-5004测量,精度设定为0.0001 mm。滚珠丝杠台的丝杠轴温度场使用FLIR C3红外热像仪测量,设定测量精度为0.1℃。
实验测试行程设定为300 mm,每50 mm设置一个分段点,共6个分段,即设置6个卷积网络模型。进给速度、运动时间、环境温度等因素均会使滚珠丝杠产生热变形,以及温度场的变化,因此,为保证所收集的数据集拥有尽可能丰富的信息量,实验设定运动速度、运动时间、运动轨迹均为给定范围内随机选取,参数范围见表2。考虑到实际使用时,环境温度将会不断变化,故不对环境温度作约束,而将环境温度包含的信息纳入深度学习网络中,由CNN网络学习其特征。
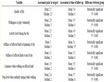
Table 2. Range of motion parameters
表2. 运动参数范围
3.2. 卷积神经网络模型训练及分析
根据以上实验条件,共收集200组实验数据,即获得了200组温度矩阵及其相应的位置数据。任意两组温度矩阵与位移数据的差即为温度变化及其对应的位移变化。通过计算得到39,800组温度变化矩阵及其位移变化矩阵,作为本次模型训练的数据集。为了方便检测精度将数据集按照9:1的比例分为训练集与测试集进行训练。
为了能够直观地表达出训练效果,在每次训练迭代中插入检测机制。500代训练后,如图2所示。
(a) CNN_1
(b) CNN_6
Figure 2. Training accuracy of CNN_1 and CNN_6 model
图2. CNN_1与CNN_6模型训练精确度
如图2所示,(a) CNN_1,(b) CNN_6分别为位置50 mm,300 mm的预测误差。经过500代训练后,训练集与测试集的准确度曲线逐渐分离,即过产生过拟合,需要在过拟合之前及时停止学习。
在经过500代的训练后,测试误差为±0.5 μm以内时,六个模型的精确度分别为86.31%,77.23%,76.99%,68.69%,68.81%,64.25%;测试误差为±1.5 μm以内时,准确度分别为100%,99.7%,99.3%,98.3%,98.05%,96.3%。
3.3. 动态补偿实验与分析
本文将上述模型注入补偿器内,验证模型补偿精度。并将其与无补偿、特征点BP神经网络补偿模型以及全图层BP神经网络补偿模型作对比。设定每5分钟进行一次补偿,每10分钟进行一次采样。结果如图3,图4所示。
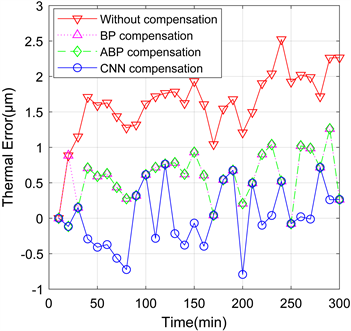
Figure 3. Compensation errors of various models at positions 50 mm and 300 mm
图3. 50 mm与300 mm位置各个模型补偿误差
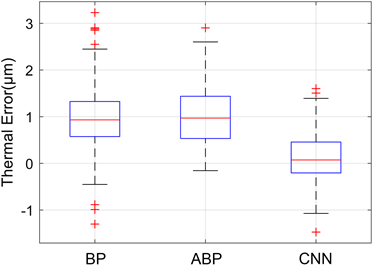
Figure 4. Box plots of error for BP model, ABP model, and CNN model
图4. BP模型、ABP模型与CNN模型误差箱型图
图3所示,为50 mm与300 mm位置时的无补偿、BP模型补偿、ABP模型补偿以及CNN模型补偿随时间变化的位置误差。将各个模型的补偿误差绘制箱型图如图4所示。分别计算三个模型误差的平均绝对误差(Mean Absolute Error, MAE),均方误差(Mean Squared Error, MSE)以及均方根误差(Root Mean Squared Error, RMSE),如表3。由表可得,本文所述方法,其均方根误差比较无补偿、BP模型与ABP模型补偿误差减小了90.3%、53.4%、55.3%。
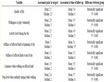
Table 3. Prediction accuracy of BP model, ABP model, and CNN model
表3. BP模型、ABP模型与CNN模型预测精确度
4. 结论
本研究提出了一种使用红外热像仪和深度学习方法相结合的滚珠丝杠进给系统热误差动态补偿模型。该模型通过卷积神经网络识别红外热像仪获取的温度场信息,建立热误差分段补偿模型,并实现实时补偿,能够有效降低滚珠丝杠进给系统的热误差。实验结果表明,该模型的均方根误差比无补偿、BP模型和ABP模型补偿误差减小了90.3%、53.4%和55.3%,验证了该方法的有效性。
本研究所提出的滚珠丝杠进给系统热误差动态补偿模型,不仅能够提高滚珠丝杠进给系统的精度和稳定性,还能够为相关领域的研究提供参考和借鉴。此外,该模型的实时性和抗干扰性也有望为滚珠丝杠进给系统的应用提供更加可靠的支持。未来的研究可以进一步优化该模型,提高其性能和精度,同时将其应用于更多的工业领域和实际场景中,以推动滚珠丝杠进给系统技术的发展和进步。