1. 引言
激光焊接作为一种新型的焊接技术,具有焊接速度快、焊缝深宽比大、变形小,能量密度高,同时也具有非常高的定位精度,焊接接头性能好等优点 [1] ,已被广泛应用于航空航天、船舶、汽车、铁路、能源等重要的工业生产领域当中 [2] 。在焊接过程中,熔池小孔的瞬态行为对焊接质量有着很大的影响,所以对熔池小孔的演变行为进行数值模拟研究是必不可少的。Yue [3] 等人提出了一种三维数值模拟方法,用于模拟研究小孔的轮廓特征以及小孔的演变对熔池的流动影响,该模型考虑了小孔自由表面、熔池表面和固–液–汽三相转变。Wang [4] 等人建立了小孔、反冲压力、熔池的相互耦合的三维模型,采用旋转激光的方法,模拟研究了小孔和熔池流动的动态行为特征。Zhang [5] 等人将流体体积法与射线追踪法相结合,模拟研究了激光全熔透焊接过程中小孔和熔池的动态耦合,研究结果表明,在全熔透焊接中,小孔熔池的瞬态演化具有周期性特征。邓集权 [6] 采用了Level Set方法追踪气液界面,混合模型处理固液界面,考虑了小孔内部多重的反射吸收、表面张力、反冲压力的影响,研究了小孔和熔池的动态形貌,以及熔池的温度场。冯燕柱 [7] 采用FLOW 3D流体仿真软件,对不同的激光入射角下,模拟研究了激光焊接在不同的熔透状态下小孔熔池的动态耦合行为,结果表明,激光入射角为正时,对熔池小孔的稳定性有很大的提高。吴家洲 [8] 建立了随小孔形状变化的自适应热源模型,考虑了反冲压力、表面张力、浮力对熔池小孔的影响,模拟研究了小孔和熔池的演变过程以及熔池的流动。Aparna [9] 等人建立了三维瞬态传热数值模型,该模型考虑了表面张力、Marangoni驱动力对熔池的影响。
2. 模型建立
激光深熔焊接的物理过程十分复杂,当高能量的激光密度照射在金属材料表面时,材料迅速熔化,熔化后的金属迅速汽化产生金属蒸气,在金属蒸气蒸发的反冲压力作用下,材料表面形成一个向下的小孔。为了便于计算,从而对模型做出以下假设:
1) 该工件材料均匀且各向同性。
2) 固–液相变时材料的密度不发生变化。
3) 熔融流动是层流,液态金属被认为是牛顿流体和不可压缩流体。
4) 激光束的热源呈高斯分布。
5) 不考虑保护气体对熔池小孔的影响。
6) 不考虑熔体与气体间的相互作用。
2.1. 计算域和控制方程
为了简化计算,采用对称模型,工件上方为气相区,厚度为2 mm,计算模型尺寸为40 mm × 5 mm × 6 mm,采用正六面体划分网格,如图1所示,图中,面ABCD、AA1B1B、DD1C1C、BB1C1C设置为壁面,面EFGH设置为压力入口,面A1EFB1、B1FGC1、D1HGC1设置为压力出口。图2所示为观察激光焊接过程的实验装置图。
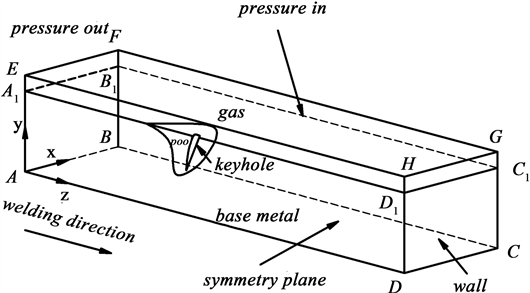
Figure 1. Schematic diagram of calculation model
图1. 计算模型示意图
基于以上假设,列出计算所用的质量方程、动量方程、能量守恒方程来模拟熔池小孔的演变过程。
1) 质量守恒方程如下所示:
(1)
式中:ρ是熔融金属材料的密度,u表示流体的速度矢量。
2) 动量守恒方程如下所示:
(2)
式中:p为流体的压力,μ为金属材料的动力粘度,
为动量源项。
3) 能量守恒方程如下所示:
(3)
式中:k为热导率,H为熔化焓,
为材料的比热容,
为能量源项。
2.2. 反冲压力模型
在激光深熔焊接过程中,激光辐射导致材料蒸发过程中的反冲压力是小孔形成过程中的主要驱动力。因此在本文中,采用Matsunwa [10] 等人提出的反冲压力模型,公式如下所示:
(4)
式中:
为反冲压力,A,
为材料的相关常数:即压力系数、蒸发常数,T表示小孔的壁面温度,K表示斯蒂芬-玻尔兹曼常数,U表示每个原子的蒸发潜热。
2.3. 材料的热物理参数
本文所选用的材料是5083铝合金,物理参数如下表1所示:
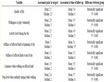
Table 1. The rmophysical parameter value of 5083 aluminum alloy
表1. 5083铝合金热物理参数值
2.4. 热源模型
激光深熔焊接中,热源模型对熔池小孔的演变是非常重要的,基于激光深熔焊接中熔池小孔形成的特点,本文采用随小孔深度方向变化的旋转高斯曲面体热源模型,其表达式如下:
(5)
式中:η为激光的热源效率,本文中取为0.65,Q为激光的总功率,
是随时间变化的小孔深度,
为激光热源作用在材料表面的光斑半径。
2.5. 边界条件
1) 热对流边界:
(6)
式中:
为对流系数,
为环境温度。
2) 热辐射边界:
(7)
式中:
为热辐射率,
为斯蒂芬–玻尔兹曼常数。
3) 小孔自由表面考虑热辐射、热对流、激光吸收以及蒸发的热边界条件:
(8)
式中:
为激光吸收的能量,
为蒸发速率,
为气化潜热。
4) 对于其他表面的热边界条件:
(9)
2.6. 气液界面的追踪与熔化凝固处理
在激光深熔焊接过程中,气液界面的形状是不断变化的,使用VOF方法对于追踪自由界面是非常重要的。VOF方法是基于流体体积占单元格体积的百分比来判断自由界面的,通过求解体积分数F的连续性方程,可以判断出单元所属状态。F的值域为[0, 1],当F = 0时,单元全部状态为气相;当F = 1时,单元全部状态为液相;当F在0和1之间时,表明既有液相也有气相,这些单元所形成的面即为自由表面 [11] 。其VOF方程如下:
(10)
式中:F为体积分数,u为速度,t为时间。
在金属凝固熔化过程中,相变潜热可以通过液相体积分数法来处理,糊状区域的动量损失采用焓–孔隙度法近似。用多孔介质处理相变的控制体,孔隙度等于液相体积分数
,通过计算每个控制体来计算固液界面 [3] 。糊状区域为液相分数在0~1之间的区域,看作孔隙度从0到1递增的多孔介质,动量损失源项
满足:
(11)
式中:ε为取值很小的常数,
为与糊状区枝晶尺寸有关的常数,v为该单元的速度矢量。
3. 计算结果及讨论
3.1. 小孔形成演变过程
图3所示为激光深熔焊接过程中,小孔的形成演变过程,采用的激光功率为3 KW,焊接速度为6 m/min。从图中可以看出,当高能量的激光密度照射在材料表面时,少量的金属材料迅速熔化,从图3中a1图可以看出材料表面有向下凹的趋势;随着焊接时间持续增加,更多的金属材料迅速熔化,被熔化的金属温度逐步升高超过了材料的沸点迅速蒸发,材料蒸发会产生反冲压力,小孔在反冲压力、表面张力的作用下,小孔的深度也逐渐增加,由公式(5)可知,反冲压力是随着温度的升高而加大的,随着时间一直增加,使得材料表面的温度急剧升高,材料蒸发所产生的反冲压力也越来越大,在t = 25 ms的时候,小孔的深度达到了3 mm,小孔达到了稳定阶段。
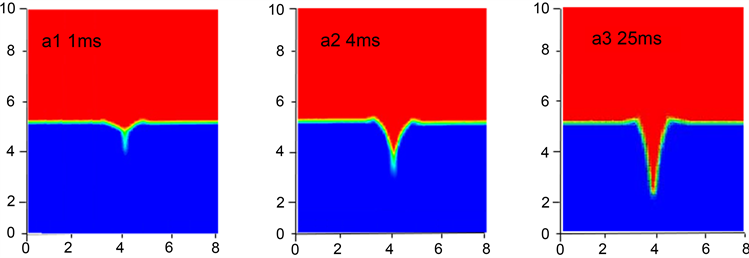
Figure 3. The evolution of a small hole
图3. 小孔的演变过程
3.2. 熔池演变过程
图4则为熔池的演变过程,采用的激光功率为3 KW,焊接速度为6 m/min。熔池的演变过程与小孔的演变过程类似,随小孔是呈正相关性的,小孔形成后,随着焊接的时间增加,小孔深度逐渐加大,此时,传递到小孔壁面的激光能量也越来越多,小孔后方的熔池通过小孔壁面菲涅尔吸收激光束能量,吸收的能量使材料持续熔化,延长了材料凝固的时间。所以熔池的宽度也要比小孔的宽度更宽。
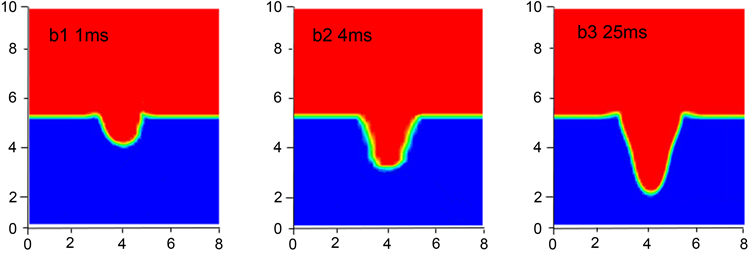
Figure 4. The evolution of a molten pool
图4. 熔池的演变过程
3.3. 焊接速度对小孔形貌的影响
图5则为相同的激光功率3 KW,其焊接速度不同,观察焊接速度对小孔形貌的影响。随着焊接速度的增加,小孔深度略有下降。这是因为焊接速度越高,焊接热输入减少,到达材料表面的激光能量也相应减少,反冲压力的作用也相应减弱,所以小孔的深度也略有下降。但总的来说,焊接速度对熔池小孔的深度影响不大。但在焊接速度为2 m/min时,小孔上部开口较大,这是因为焊接速度越低,激光的线能量越高,辐射在材料表面的能量也越多,熔化的金属材料也相应的增加,反冲压力的作用也越强,且熔化的金属液向小孔后下方流动,导致小孔的后壁面在凝固后变得陡峭。焊接速度对熔池的影响的规律与小孔的影响规律大致一样,此处不再详细介绍。
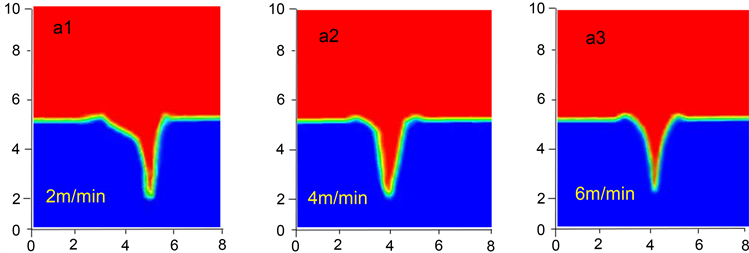
Figure 5. Morphology of small holes at different welding speeds
图5. 不同焊接速度下小孔的形貌
3.4. 焊接功率对小孔形貌的影响
图6为不同的激光功率对小孔形貌的影响,焊接速度取为4 m/min。上述我们分析了焊接速度对小孔形貌的影响,得出了焊接速度对小孔深度影响不大的结论。实际上,对小孔深度影响较大的是激光功率,当功率为5 KW时,小孔的深度有了明显的增加,且小孔上部开口较大。这是因为相同时间内,功率越大,能量密度也越大,激光对材料的熔化作用也越强,作用在材料表面的反冲压力也大,所以小孔的深度也明显增加。
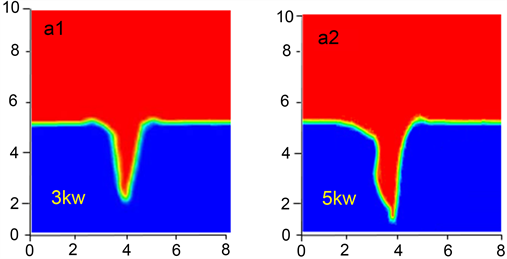
Figure 6. Morphology of small holes at different welding power
图6. 不同焊接功率下小孔的形貌
3.5. 实验验证
为了验证模型的正确性,本文进行了焊接速度为2 m/min和焊接速度为4 m/min激光焊接实验,利用小孔的深度和小孔开口大小来验证模型的准确性,实验结果如图7所示。通过实验结果可知,焊接速度越低,线能量就越高,导致小孔上方开口较大,与仿真结果较吻合,从而验证了模型的准确性。
4. 总结
本文建立了一个考虑表面张力、反冲压力等力的三维数值模型,用VOF方法追踪气液界面,用焓–孔隙度法解决熔化凝固问题,考虑了激光的热辐射、热对流,小孔自由表面对激光的多重吸收,分析了熔池小孔的演变过程,并讨论了焊接速度和焊接功率对熔池小孔的影响。得出结论:小孔的形成是作用在表面上反冲压力的结果,反冲压力越大,小孔的深度越深,熔池深度与小孔的深度呈正相关性;焊接速度对熔池小孔影响的作用不大,焊接速度越低时,小孔的开口较大;激光功率对熔池小孔的影响较大,功率越大,作用在材料表面的能量密度越高,金属液蒸发所形成的反冲压力也越大,熔池小孔的深度相应的增加。