1. 引言
外圆纵向磨削作为一种获得高精度、低粗糙的加工表面以及对高耐磨金属表面进行精加工的特定工艺方法,在机械加工中的比重越来越大,广泛应用于对轴类等零件的加工 [1] 。在外圆纵向磨削加工过程中,磨削参数是影响加工质量和效率的关键因素。在实际生产中磨削参数往往由工人凭经验确定,这将可能在一定程度上对零件加工精度及效率产生影响。
磨削工艺参数优化是指以获得高质量、高效率、低能耗的零件加工过程为目的,采用各种优化方法对磨削用量或磨削加工工艺过程进行建模优化,对磨削工艺参数优化方法的研究一直受国内外学者的关注。Zhanying Chen等 [2] 以加工误差最小和磨削效率最大为优化目标,建立了磨削加工过程多目标优化模型,并利用改进的粒子群算法对优化模型进行求解,得到了磨削效率与加工误差之间的最优妥协解,最后对优化后的磨削参数进行了实验验证。UlasCaydas等 [3] 探讨了磨削参数对加工零件表面粗糙度的影响,利用响应面法(RSM)建立了磨削参数与零件表面粗糙度之间的数学模型。其次,将建立的RSM模型作为遗传算法的目标函数,对磨削参数进行优化。Ramesh Rudrapati等 [4] 基于理论研究和实验分析,研究了加工参数对不锈钢外圆纵向磨削振动和表面粗糙度的影响,揭示了输出响应随加工参数变化的规律,以此对加工参数进行了优化。Sanjay Shankar Patil等 [5] 利用RSM建立了确定磨削响应的数学模型,进一步利用RSM结果,采用快速非支配排序遗传算法(NSGA-II)获得多目标模型前沿最优解,对外圆切入磨削的修整切削深度、修整横向进给速度和磨削进给速度等工艺参数进行了优化,所得结果为确定最佳磨削参数提供了依据。王泽 [6] 以磨床动力学性能及其相关参数、工件表面质量、砂轮热损伤等作为约束条件,建立了基于碳效益的磨削参数优化模型,采用NSGA-II算法对优化模型进行求解,从而获得了使碳效益达到最佳的磨削参数组合。邓辉等 [7] 为提高TC4钛合金表面加工质量,就磨削深度、纵向进给速度、砂轮与工件转速等磨削参数对TC4钛合金表面加工质量的影响规律进行了理论与实验研究,以此建立了由磨削工艺参数表示的表面粗糙度预测模型,最后采用粒子群算法求解了最佳磨削参数组合并通过磨削实验进行了验证。以上研究均依赖于大量的磨削加工实验样本数据,并且学者大多采用基于人工智能的方法对磨削参数进行优化,少有文献通过磨削机理的角度对磨削参数进行优化。
目前,对磨削工艺参数的优化方法主要以提高零件加工质量和效率、降低加工成本等为最终目的,通过人工智能方法、实验方法或者两者相结合的方法实现对磨削加工过程或磨削参数的优化。本研究以提升外圆纵向磨削加工精度为最终目标,通过磨削实验就磨削参数对加工精度的影响进行分析,并从磨削机理的角度出发对磨削参数进行优化。
2. 外圆纵向磨削原理
如图1所示,磨削加工主要以高速旋转的砂轮等磨具作为加工刀具,磨削时,每一颗磨粒都如同一把切刀,实现对工件表面材料的去除。在进行磨削加工时,砂轮表面大量磨粒不断地去除工件表面材料,外部磨粒磨损达到一定程度时便自动脱落,内部新的磨粒会自动暴露出来继续参与磨削,即砂轮具有自锐性。同时,磨削加工时工件表面材料去除深度一般较小,一般可以达到微米级,正是由于这种特殊的加工机理,使得磨削加工相对于其他机械加工方式具有较高的加工质量。
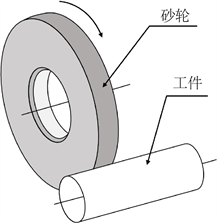
Figure 1. Cylindrical grinding schematic diagram
图1. 外圆磨削加工示意图
如图2所示为采用双顶尖装夹方式时外圆纵向磨削示意图,被左右顶尖装夹的工件为磨削系统的工件系统,砂轮系统由砂轮及砂轮架组成,工件系统与砂轮系统共通组成了外圆纵向磨削的磨削系统。在外圆纵向磨削过程中,砂轮和工件以一定的速度做旋转圆周运动,同时工件沿纵向随工作台以一定的速度做直线往复进给运动,工件在完成一次纵向进给后,砂轮轴做一次横向进给,以实现对工件表面材料的去除。
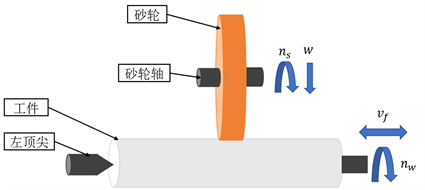
Figure 2. Cylindrical longitudinal grinding schematic diagram
图2. 外圆纵向磨削示意图
其中:
为砂轮转速,
为工件转速,w为指令横向进给量,
为指令纵向进给速度。
3. 外圆纵向磨削加工精度评价指标
机械加工精度是指工件在加工后的实际几何参数与图纸设计要求相符合的程度,而它们之间不相符合的程度,则称为加工误差 [8] 。在外圆纵向磨削加工中,加工精度主要包含尺寸精度、几何形状精度、相互位置精度和表面粗糙度。在本文,涉及到的加工精度包括尺寸精度和几何形状精度,即零件的直径加工误差和圆柱度误差。
外圆磨削加工通过材料去除使回转零件达到指令直径大小,零件的直径加工误差将直接影响其他形位误差,故零件直径的加工误差是判断零件加工是否达标的重要指标。如式(1),直径误差为零件加工后各测点位置真实直径与理想直径差值的平均值。
(1)
式中,
为第i个测点位置的真实直径,
为第i个测点位置的理想直径,n为测点总数目。
如图3所示,零件的圆柱度误差是指零件表面与其理论轴线之间的形状偏差,其数值能够表征零件制造精度的质量水平,圆柱度误差是衡量轴类零件加工质量的重要精度指标。如式(2)所示,圆柱度误差可用形成最小包容区域的两同心圆柱面的半径差来表示 [9] 。
(2)
式中,
分别为圆柱体内外包络圆柱半径。
4. 磨削参数对磨削加工精度影响实验与分析
为确定磨削参数对零件尺寸精度及圆柱度影响情况,本节将通过磨削加工实验就磨削参数对加工精度影响进行分析,从而为后续磨削工艺参数的优化提供参考。通过查阅磨削工艺手册 [10] ,设置加工工艺参数范围如表1所示,其中B代表砂轮宽度。
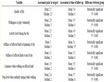
Table 1. Grinding process parameter range
表1. 磨削工艺参数范围
选用型号为MK1320B数控外圆磨床进行磨削加工实验,该磨床的主要技术指标如表2所示。实验过程采用直径为50 mm、长度为500 mm的45钢工件作为磨削加工标准件。
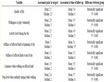
Table 2. Main technical indexes of MK1320B CNC cylindrical grinder
表2. MK1320B数控外圆磨床主要技术指标
4.1. 指令磨削深度对磨削加工精度的影响
控制纵向进给速度、砂轮及工件转速不变,分别对指令磨削深度为0.01 mm、0.015 mm、0.02 mm、0.025 mm、0.03 mm、0.035 mm、0.04 mm时进行7组外圆纵向磨削加工实验,得到零件加工后各位置实际直径去除深度如图4所示。从图中可以观察出,零件实际直径去除量不等于指令磨削深度,并且零件各位置实际去除量也不相同,造成该现象的原因为磨削系统弹性变形及砂轮磨损的存在。
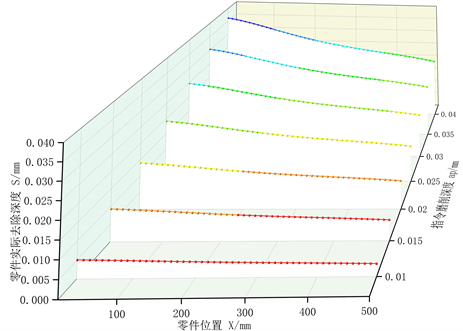
Figure 4. Effect of instruction grinding depth on actual removal depth (vf = 5 mm/s, vs = 35 m/s, vw = 0.2 m/s)
图4. 指令磨削深度对实际去除深度影响(vf = 5 mm/s, vs = 35 m/s, vw = 0.2 m/s)
根据零件加工结果,由式(1) (2)计算得到各指令深度下零件直径加工误差及圆柱度误差如图5、图6所示。从图中可以看出指令磨削深度对零件加工质量影响效果较为明显,增大指令磨削深度,零件直径加工平均误差以及圆柱度误差增大,这是由于增大磨削深度会使实际去除深度与理想去除深度差值增大的缘故。例如,指令磨削深度为0.015 mm时,零件平均直径去除深度与指令去除深度之差为0.015 mm,指令磨削深度为0.03 mm时其差值为0.022 mm。
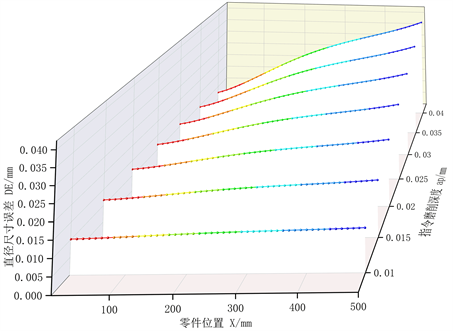
Figure 5. The influence of instruction grinding depth on machining error of part diameter (vf = 5 mm/s, vs = 35 m/s, vw = 0.2 m/s)
图5. 指令磨削深度对零件直径加工误差影响(vf = 5 mm/s, vs = 35 m/s, vw = 0.2 m/s)
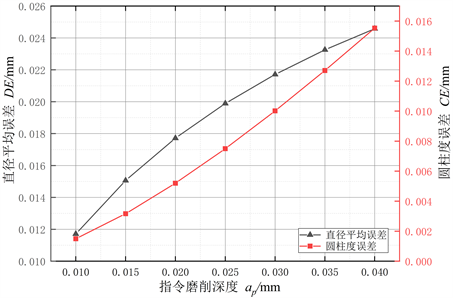
Figure 6. The influence of instruction grinding depth on grinding accuracy (vf = 5 mm/s, vs = 35 m/s, vw = 0.2 m/s)
图6. 指令磨削深度对磨削加工精度影响(vf = 5 mm/s, vs = 35 m/s, vw = 0.2 m/s)
4.2. 纵向进给速度对磨削加工精度的影响
如图7所示为纵向进给速度大小对磨削加工精度的影响曲线。从图中可以分析出:增大纵向进给速度会使零件直径加工误差增大,使圆柱度误差降低。造成该现象的原因为增大纵向进给速度会使工件各位置的实际材料去除率降低,从而导致直径加工结果与理想结果相差较大,而零件圆柱度则不断提高。对比图6及图7可以发现,相对于指令磨削深度,纵向进给速度对磨削加工精度影响较小,其中圆柱度误差最大为7.8 μm,平均直径误差最大为16.4 μm。
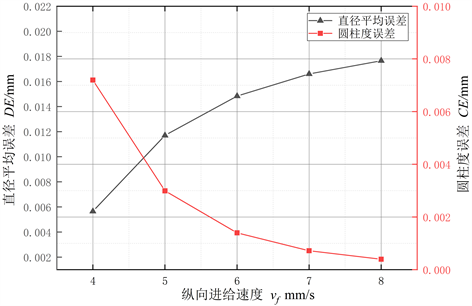
Figure 7. The influence of longitudinal feed speed on grinding accuracy (ap = 0.01 mm/s, vs = 35 m/s, vw = 0.2 m/s)
图7. 纵向进给速度对磨削加工精度影响(ap = 0.01 mm/s, vs = 35 m/s, vw = 0.2 m/s)
4.3. 砂轮转速对磨削加工精度的影响
如图8所示,零件直径平均误差随砂轮线速度的增加呈现出先降低后增加的趋势,当砂轮线速度接近35 m/s时误差最小,为11.6 μm,当砂轮线速度大于35 m/s时,直径平均误差开始呈现出增大的趋势。零件圆柱度误差随砂轮线速度的增加而呈现缓慢上升的趋势,但从图中可以观察出砂轮线速度对零件圆柱度影响程度较小,图中圆柱度最大数值为接近4.2 μm,平均直径误差最大为15.9 μm。
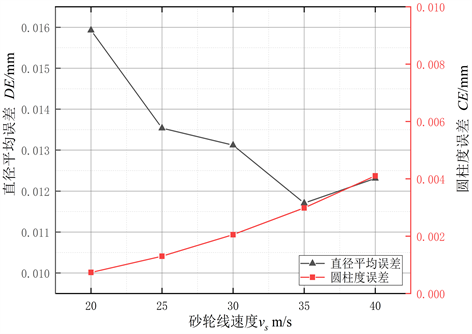
Figure 8. Influence of grinding wheel speed on grinding accuracy (ap = 0.01 mm/s, vf = 5 mm/s, vw = 0.2 m/s)
图8. 砂轮转速对磨削加工精度影响(ap = 0.01 mm/s, vf = 5 mm/s, vw = 0.2 m/s)
5. 基于恒力控制策略的外圆纵向磨削参数优化方法
5.1. 磨削力模型
近三十年来,有关磨削力的研究倍受学者关注 [11] [12] 。图9所示为进行外圆纵向磨削时磨削力分力示意图。其中,
与
分别为磨削力沿法向及切向分力,
为磨削力沿纵向进给方向分力。
决定了磨削时有效功率的消耗,
为砂轮与工件沿纵向进给方向产生的相互作用力,其数值大小远小于
和
。
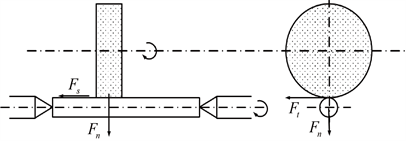
Figure 9. Cylindrical longitudinal grinding force diagram
图9. 外圆纵向磨削力示意图
目前,磨削力求解计算公式主要包括基于磨削实验数据的磨削力经验公式以及基于理论解析法建立的磨削力公式。由于经验公式只能对磨削力进行简单估计,其计算得到的磨削力误差较大,故丁宁等 [13] 从砂轮单一磨粒的切削状态出发,确定了基于磨削机理的外圆纵向磨削力模型。由文献 [13] :
(3)
式中,
为砂轮磨粒圆锥半顶角,
一般取0.2~0.5,
可由下式求出:
(4)
由式(3)可得到:
(5)
(6)
又
(7)
结合式(4)~(6),可得到磨削深度关于磨削力的表达式:
(8)
式中
(9)
(10)
如图10所示为磨削力仿真结果与磨削力实测结果对比曲线,其中红色曲线为零件各位置实际去除深度,黑色和蓝色曲线分别为磨削力实际值拟合曲线及仿真计算结果。从图中可以看出,磨削力仿真结果与实际测量结果数值大小基本保持一致,通过计算,得到磨削力最大相对误差为15.41%,平均相对误差为4.82%,故磨削力仿真模型计算结果满足精度要求。
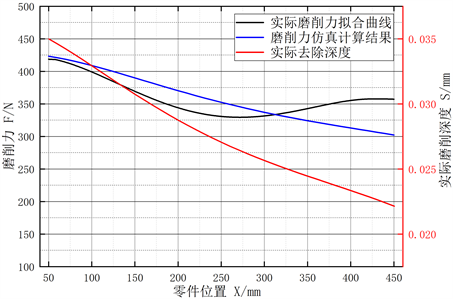
Figure 10. Comparison of simulation results and experimental results of grinding force of parts
图10. 零件磨削力仿真结果及实验测量结果对比
5.2. 磨削力与加工精度相互影响分析
引起零件直径加工误差以及圆柱度误差的本质原因为零件各位置实际磨削深度不等于机器的指令磨削深度,为了降低外圆纵向磨削时零件直径加工误差以及圆柱度误差以提高磨削质量,需要使零件各位置实际去除量恒定并且与指令磨削深度相等。
由式(3)可以分析出,磨削力主要受工件及砂轮规格属性以及磨削参数影响,对于同一磨削系统,当零件材料属性及尺寸规格不变时,磨削力仅受磨削工艺参数影响。如图11所示为磨削力与实际磨削深度相关性散点图,图中黑色圆形代表实际磨削深度及磨削力大小,蓝色实线为磨削力关于磨削深度的拟合曲线,可以发现磨削深度在0.005 mm到0.04 mm时,磨削力与工件表面材料实际去除深度呈线性正相关,拟合曲线相关性系数R为0.97906。故可以得到如下结论:零件各位置的磨削力大小能够从侧面反映出实际磨削深度的大小。
在进行外圆纵向磨削加工时,可根据磨削力大小判断各磨削位置的实际去除深度是否相同。综上,磨削力与磨削加工精度的相互影响关系可总结如图12所示,若零件各位置磨削力恒定,则零件尺寸精度及圆柱度精度相对较高;反之,如果零件各位置磨削力不同并且变化范围较大,则零件加工精度较低。
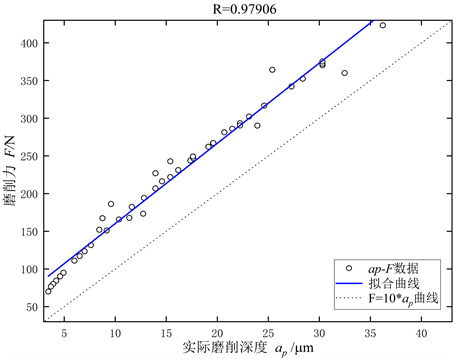
Figure 11. The actual grinding depth and grinding force correlation scatter plot
图11. 实际磨削深度与磨削力相关性散点图
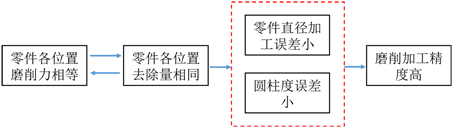
Figure 12. Grinding force and parts machining accuracy influence each other.
图12. 磨削力与零件加工精度相互影响关系
5.3. 基于恒力控制策略的磨削参数优化方法
由上一节磨削力与磨削加工精度的相互影响关系可知,实际磨削深度决定了磨削力大小,反之,磨削力大小又能够反映实际磨削深度。因此,本文提出一种基于恒力控制策略的磨削进给量优化方法,该方法通过对进给深度进行修正以保证磨削力恒定,从而实现对指令进给深度的优化。
综上,得到指令磨削深度优化策略流程图如图13所示,其基本思想及步骤如下:
(1) 对标准件加工结果进行测量,并计算工件各位置的实际去除量,利用磨削力模型对工件各位置的实际磨削力进行计算仿真。数控系统的指令磨削深度为
,理想磨削力为
;
(2) 计算工件第
段实际磨削力
,其中j为工件第i段位置磨削力更新次数,若
满足终止条件则进入下一段
的优化工作并返回步骤(2),否则计算理想磨削力偏差
;
(3) 通过磨削力偏差计算指令磨削深度的修正量或补偿量,其中修正量为
,优化后的
为
;
(4) 返回步骤(2),利用修正后的指令磨削深度
重新计算磨削力
。
6. 实验及结果分析
使用上海机床厂生产的MK1320B数控外圆磨床进行磨削参数的优化实验,该磨床具体技术指标参
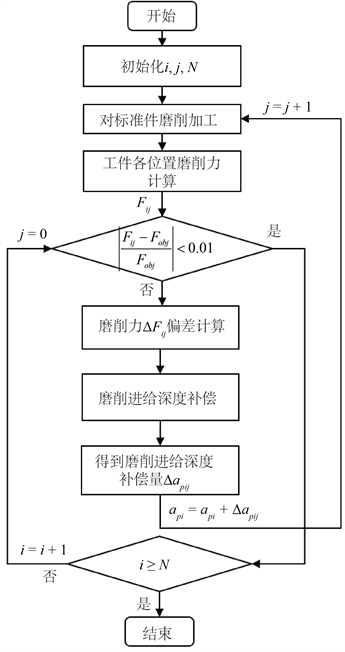
Figure 13. Cylindrical longitudinal grinding depth optimization flow chart
图13. 外圆纵向磨削指令进给深度优化流程图
数已在前文进行了详细介绍。磨削工件信息为:直径为50 mm (49.554 mm),长度为500 mm,工件材料为45号钢。磨削工艺参数信息为:指令磨削深度为0.04 mm,砂轮线速度为35 m/s,工件线速度为0.3 m/s,纵向进给速度为5 m/s,总磨削深度为0.16 mm。
首先将磨削零件沿轴向等距(10 mm)取50个点并对各位置实际去除量进行测量计算,其次按照磨削深度的优化流程并借助Matlab软件进行计算,得到各离散点处原始磨削力和修正后的磨削力如图14所示,以及原始指令进给深度和优化后的指令进给深度如图15所示。
将优化后的磨削深度输入到数控系统进行磨削加工,即按照图15结果:第一段指令磨削深度为0.0438 mm,第二段为0.0440 mm,以此类推,第50段指令磨削深度为0.0593 mm。如图16所示,进行4次纵向磨削后对零件上9个等间距位置的直径进行测量,其中零件理论加工后直径为49.224 mm。
如表3所示为指令磨削深度优化前后对应的零件加工精度计算结果,从表中可以看出,磨削参数优化后的零件加工误差均有明显的降低,其中平均直径误差和圆柱度误差分别降低了37.76%和55.65%,故基于恒定磨削力控制技术的磨削参数优化结果能够有效提升零件的加工精度。
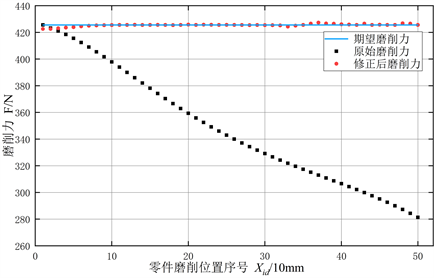
Figure 14. Curve before and after grinding force correction
图14. 磨削力修正前后曲线
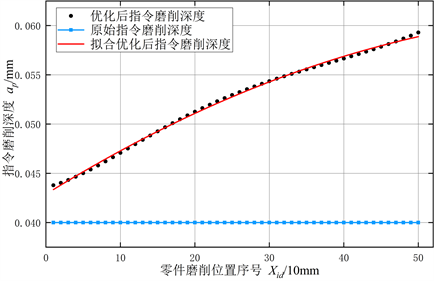
Figure 15. Curve before and after instruction feed depth optimization
图15. 指令进给深度优化前后曲线
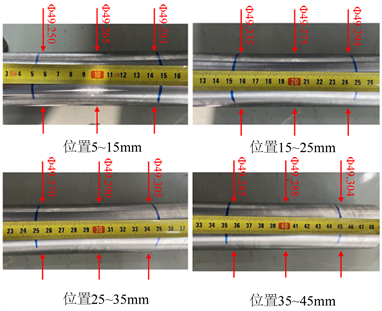
Figure 16. Machining measurement results of parts after instruction feed depth optimization
图16. 指令进给深度优化后零件加工测量结果
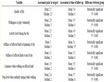
Table 3. Comparison of machining accuracy of parts before and after grinding depth optimization
表3. 磨削深度优化前后零件加工精度对比
7. 结论
为对外圆纵向磨削参数进行优化以提高零件的加工精度,首先就磨削参数对加工精度的影响进行了实验分析,结果表明:磨削加工精度主要受磨削深度的影响。其次,基于磨削力模型对磨削力与加工精度相互影响进行分析,得到磨削力与实际磨削深度呈正相关关系的结论,据此,提出了基于恒力磨削的指令进给深度优化策略。最后,对磨削参数优化结果进行了实验验证,结果表明该优化方法能够有效提升零件精度大幅度提升,其中平均直径误差降低了37.76%,圆柱度误差降低了55.65%。