1. 引言
济南是著名的泉城,地下岩溶裂隙发育,溶洞众多,水源补给充足,裂隙的存在给地下水提供了储水条件及运输通道,并且灰岩裂隙岩溶水具承压性,盾构掘进过程中极易发生突涌水灾害。岩溶的存在可能会使盾构掘进过程中发生盾构机栽头、陷落 [1],隧道上方溶洞可能引发地表塌陷,运营期车辆振动引发地表坍塌或激发管片下方溶土洞的坍塌,导致列车运行存在风险并且岩溶水的存在引发溶洞继续发育,对地铁长期运营造成威胁。为确保施工及运营安全,必须对岩溶裂隙水、溶洞进行处理。
盾构施工过程中如采用直接降水方案,降水量巨大并且会威胁附近建筑物的运营安全 [2]。为保证施工安全同时达到绿色施工的目标,按照“以堵为主,综合治理”的原则施工 [3] [4] [5],堵是从水源传播路径上阻断岩溶裂隙水向隧道渗透,尽量不影响地下水的原始结构,综合治理包括溶洞的注浆填充和结构的防水措施。
2. 工程概况及穿越灰岩复合地层岩溶裂隙水涌水情况
济南地铁R1号线王府庄站至大杨庄站区间线路主要穿越京沪高铁高架桥、京台高速公路桥、腊山河桥、陡沟桥,区间全长3754 m,采用盾构法施工,区间在右K30 + 411.950 (中心里程)处设一座中间风井,采用明挖法施工。王府庄站~风井区间盾构机均在此处拆机吊出,区间风井~大杨庄站区间左右线盾构机在此处分体始发。区间风井~大杨庄站段隧道长度约2033 m,其中在K30 + 460.3~K31 + 362.2下穿灰岩段,该段区间需穿越两端基岩凸起段,左线隧道穿岩长度约725 m,右线隧道穿岩长度约798 m,该段线路图如图1所示。本文主要论述区间风井到大杨庄站中风化石灰岩段的岩溶裂隙水涌水情况及其安全控制技术。
中风化石灰岩地层单轴饱和抗压强度与土体强度相差悬殊,容易造成掘进机破岩困难、刀具严重偏磨、轴承受损等事故 [6]。富水岩溶地区修建城市地下轨道交通工程有着极大的风险,盾构隧道的施工和运营过程中都有可能使溶洞顶板坍塌、溶洞的突泥、涌水等事故发生已成为当前最严重的地质灾害之一 [7],给地铁隧道的施工和运营都带来了很大的安全隐患。目前,区间风井~大杨庄站左线灰岩段已累计完成426 m,右线灰岩段累计完成429 m,盾构机在中风化石灰岩段掘进过程中,地层岩溶裂隙水补给量大,管片和掌子面涌水严重,螺机喷涌严重(如图2所示),额外消耗大量排水、清渣时间,影响施工进度;若盾尾清理不干净,影响管片拼装质量可能影响施工安全。
(a) 隧道渗水
(b) 掌子面涌水
(c) 螺旋机喷涌漏渣
Figure 2. Water flow in the tunnel
图2. 隧道涌水图
3. 工程地质和水文地质条件
3.1. 工程地质
勘查资料显示,灰岩段地层特点包括岩石强度高,存在溶洞,岩溶、裂隙水丰富。中风化石灰岩单轴饱和抗压强度位于33.5 MPa~83.2 MPa范围内,标准值为64 MPa,在盾构机实际掘进过程中施工单位取岩芯送检发现岩石抗压强度普遍分布在80 MPa以上,且最高达到112 MPa,现场钻孔岩芯完整性统计显示ROQ值在5~50之间,普遍在5~25之间,质量分级为极差。隧道沿线地质钻孔在中风化石灰岩段揭露有溶洞,局部含有灰岩破碎体。王府庄站至大杨庄站区间线路溶洞数量较多,厚度较大,同时揭露有串珠状溶洞,钻探揭露灰岩溶蚀现象较严重,局部灰岩蜂窝状、针孔状溶孔溶隙发育,在长期的地下水作用下,溶洞规模可能进一步扩大,岩溶稳定性较差。根据钻探成果,钻孔揭露的溶洞总数为129个,其中小于1 m的溶洞79个,占溶洞总数的61.2%;≥1 m的溶洞50个,占溶洞总数的38.8%;≥2 m的溶洞29个,占溶洞总数的22.5%;≥3 m的溶洞23个,占溶洞总数的17.8%。钻探揭露无充填型溶洞的钻孔11个,揭露无充填型溶洞个数12个。其中ZK39-2号钻孔揭露1.0 m无充填型溶洞,其余揭露无充填型溶洞均小于1 m。充填物以黏性土及碎石为主,碎石粒径及含量不均匀。
3.2. 水文地质
王大区间灰岩段揭露地下水主要为灰岩裂隙岩溶水,水位标高27.06 m~32.05 m,水位埋深11.2 m~14.6 m。含水层主要为强风化灰岩层、中风化灰岩层及灰岩破碎体。主要接受大气降水入渗补给、河床渗漏集中补给及第四系松散岩类孔隙水渗透补给,以人工开采排泄、补给第四系含水层为主。该层地下水主要赋存于灰岩岩溶裂隙中,灰岩破碎裂隙及溶洞溶隙的存在给该层地下水提供了储水条件及运输通道。该层地下水局部受完整灰岩及上覆粉质黏土层隔挡,具承压性。
中间风井原始位置做试桩施工时,发现灰岩裂隙水量较大,根据现场抽水试验分析,补给水是溶岩裂隙水。抽水试验采用100 m3/h泵抽水时间4小时,水位降低0.4 m后,稳定水位不变,地下水补给量大,无法成桩,中间风井的位置因此南移。
水文地质图中显示,区间穿中风化石灰岩段,为济南中西部片区水量最大的区域,裂隙岩溶水单井出水量基本大于10,000 m3/d,说明该段为富水区,水量补给较大,且地下水具有承压性(见图3)。
4. 穿越溶洞裂隙水的安全控制技术
在中风化灰岩段掘进过程中,由于岩溶裂隙水补给量大,造成螺机喷涌严重,额外消耗大量排水、清渣时间;盾尾漏水,带走同步注浆浆液;若盾尾清理不干净,影响管片拼装质量;严重影响围岩稳定性,严重影响了施工阶段安全和质量,施工进度也得不到保证。经过多方比较,岩溶裂隙水安全控制技术确定为探测和处理相结合的方案。
探测的方法包括超前探测和地质钻探,超前探测有地质雷达、激发极化、CT扫描、电密度法等方法进行了地下水、溶洞、裂隙分布探测,地质钻探是沿隧道中线每隔5米施打一个钻孔,孔深约23米,进行溶洞、裂隙水、完整性探测。这样得到的探测结果较为真实可信,能为后面的处理方案提供很好的参考价值。
处理的技术有地表注浆,井下施工时注浆,盾尾二次环箍注浆。地表双液注浆预处理是通过地面钻探孔进行水泥水玻璃双液注浆;井下注浆采用无害和初凝时间短的惰性浆液,少量多次,这样注浆的扩散范围小,容易控制;盾尾二次环箍灌浆尽可能靠近盾尾,宜距盾尾后部5环左右,阻隔盾尾后部来水,将浆液凝结时间控制在10 s左右,注浆压力应大于当前位置水压2 bar~3 bar。掘进时可采用气压掘进模式,即在开挖仓里注入膨润土等改良剂,通过气压把膨润土压入周围的裂隙里,起到封堵裂隙水的效果;开仓换刀时,采用衡盾泥泥膜护壁带压开仓换刀。这一控制技术方案经过现场监测效果显著,后面将做较为详细的介绍。
4.1. 岩溶水处理试验方案
由于掌子面涌水严重,根据工程地质和水文地质条件,虽然地下裂隙发育溶洞众多,弄清地下水水源补给的来源,从水源传播路径上截断,因此需寻找水源补给方向,水源方向探测通过以下方式进行:
1) 地质钻机钻孔,钻孔位置如图4所示,从地面打孔,钻孔深度为掘进断面向下5米,钻孔顺序为5 → 3 → 7 → 1 → 9 → 2 → 4 → 6 → 8 → 0 → 10,若过程中找到了水源补给方向,2、4、6、8、0、10可不再钻孔,钻孔完成后,注入清水,若清水能够灌满、不向下渗入或者渗水速度慢,则在此孔附近重新钻孔。
2) 注入水泥浆液,观察掌子面是否有浆液流出,若有水泥浆液流出,则可以判定此孔方向为水源补给来源之一,对此孔进行注浆或灌注砂浆处理;
3) 在已探测出的水源补给孔位两侧1.5米处钻孔,进行注浆或灌注砂浆处理。
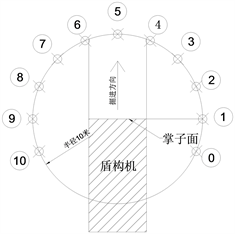
Figure 4. Detection drilling of water source
图4. 水源探测钻孔示意图
4.2. 岩溶裂隙水处理
根据探测结果,对水源补给孔及其两侧孔进行处理,处理方式优先选用注双液浆,当双液浆无法产生有效作用时,采用灌注砂浆。
注双液浆法:依次或同时对相应孔位进行袖阀管注浆,当孔位具备注浆条件后,先注入水泥浆液,同时观察掌子面是否有浆液流出。确认有水泥浆液流出后,调配双液浆凝固时间,分别按照凝固时间120 s、90 s、60 s、30 s、15 s调整配比,按照凝固时间由长到短依次进行注浆,每种配比尝试注浆1 h左右(具体时间根据现场情况调整),若持续流出则更换时间更短的配比,直到掌子面不再流出浆液为止,过程中做好施工记录,特别是最终压力值,作为后续施工的经验值。双液浆中水泥浆与水玻璃体积比C:S = 1:(0.5~1),水玻璃浓度为35波美度,模数m = 2.4~2.8。
灌注砂浆法:当双液浆调整至最短凝固时间仍不能对涌水产生有效作用时,尝试进行灌注砂浆 [8]。
4.3. 溶洞处理
在可溶性岩层中,构造裂隙发育,地下水丰富,由地下水的溶蚀和侵蚀,形成的规模大小不一、形态各异、埋深不等的洞穴。容易造成盾构机卡机、刀盘突水,隧道下方的溶洞塌陷引发地表塌陷等问题。
溶洞处理范围为隧道上部、隧道洞身范围、隧道底板下一倍洞径范围、隧道轮廓线外5 m范围内的溶洞都需要处理,其中硬塑性黏土充填的溶洞可以不处理。
在探测有溶洞的地方加密钻孔,钻孔间距2.5 × 2.5 m,进一步查清和了解溶洞的具体位置、大小、充填物性质及地下水情况,加密钻孔可兼做注浆孔。对于全填充溶洞采用水泥浆进行填充加固;对于岩溶洞穴高度不大于1 m的无填充溶洞和半填充溶洞的直接采用1:1水泥浆液进行压力注浆;对于洞径小于2 m的无填充溶洞和半填充溶洞,可采用水泥砂浆填充;对洞径大于2 m的无填充溶洞和半填充溶洞,先采用吹砂处理,后采用注浆加固的方法;对于洞径大于4 m的特大型无填充溶洞,可考虑先投碎石,后采用注浆加固(如图5)。并且在管片结构上预留岩溶处理专用孔,用于隧道掘进过程中新发现的溶洞,以及隧道后期发生沉降超限或异常的地段,沿线路纵向每10环管片进行洞内补充钻探,钻孔深度为隧道底部一倍洞径,根据钻探结果,对隧道底部进行注浆填充,保证运营安全。
注浆用的水泥浆水灰比为1:1.2,注浆压力控制在0.4 MPa~0.8 MPa,袖阀管和注浆芯管下到洞底或洞底以下 0.2~0.3m,从洞底往上压注水泥浆或水泥砂浆当注浆压力达到1.0 MPa,吸浆量1 L/min~2 L/min稳压10 min可终止注浆。
4.4. 径向注浆和管片防水加强处理
隧道内每环管片是由6只管片连接而成,管片宽1.2 m,每环管片预留四个孔作为堵水注浆孔,浆液为水泥砂浆。隧道整个运营期内最大水头高度为23.5 m。根据管片结构防水图中设计要求,管片接缝允许张开量为6 mm时,弹性密封垫仍可抵抗0.8 MPa的水压,因此,现设计方案满足隧道防水要求。但考虑到该段岩石强度较高,岩溶及破碎带发育,岩溶水水量丰富,盾构施工过程中掘进姿态难以控制,管片拼装质量难以达到理想状态,因此对穿岩段盾构管片满环柔性嵌缝,以提高管片的防水能力,嵌缝采用柔性聚氨酯密封胶(如图6)。
(a) 普通地段防水处理示意图 (b) 穿岩地段防水处理示意图
Figure 6. Segment waterproofing schematic
图6. 管片防水处理示意图
5. 应用效果及结论
地面注浆加固,从水源传播处切断其传播,施工时采用分序孔的注浆方式,并宜采用间隔跳孔、逐步约束、先下后上的注浆施工方法,注浆过程中,随时关注泵压和流量变化,若吸浆量很大或压力突然下降,注浆压力长时间不上升,应查明原因,如工作面漏浆,可采取封堵措施;如跑浆可通过调换浆液、调整浆液配比,缩短浆液凝胶时间,进行大泵量、低压力注浆,必要时采用间歇注浆,及时调整注浆参数,以达到控域注浆的目的。
工程实践证明盾构机掘进到注浆区域后掌子面涌水情况得到明显改善。据统计处理前掌子面涌水量值大约为4 m3/h,控制之后掌子面涌水量在0.3 m3/h以下,管片上的涌水量几乎为零。从盾构机的掘进速度来看,前期由于涌水严重,盾构机时常需要排水而停机2~3天,掘进速度受到严重制约,不停机时掘进速度大约在3 m/d;控制之后平均掘进速度大约达到了6 m/d。由此可见溶洞的处理减少了盾构机卡机、栽头的灾害,确保了施工进度与施工安全,为之后地铁隧道的盾构施工提供了经济可靠的方法。