1. 引言
5083铝合金板材具有质轻、中等强度、易成型等众多优点,可应用于汽车零部件、运煤货车、船舶等交通运输工具制造[1] -[3] 。但5083铝合金中Mg含量较高,在室温下长期放置易在晶界处析出β相(Mg2Al3),β相的析出将使材料发生时效软化,此外,若β相在晶界处呈网状连续分布,将恶化材料耐蚀性能 [4] - [6] 。为减少β相析出带来的不利影响,工业上开发了H321工艺状态,对冷变形后的5083铝合金板材进行稳定化退火,使部分Mg能够以β相的形式在合金内均匀析出,确保时效软化后的材质依旧满足性能要求,同时避免β相沿晶界连续析出降低耐蚀性能 [4] - [6] 。在5083-H321态板材的工业生产过程中,再结晶退火后的冷变形量与冷变形后的稳定化退火温度、时间是影响材料最终性能的三个关键工艺参数,三工艺参数需要进行合理搭配才能生产出性能良好的板材。国内部分学者在对H321工艺研究中,通常是逐步改变单个工艺参数,再测量材料性能,以建立5083-H321生产工艺 [7] [8] ,但很少有人去研究冷变形程度、稳定化退火温度、稳定化退火时间对材料力学性能的影响主次关系,国内现有研究方式往往工作量大、试验繁琐。本文以3 mm厚5083-H321铝合金板材为研究目标,通过正交试验与极差分析研究了冷变形程度、稳定化退火温度、稳定化退火时间对材料力学性能的影响主次关系,并根据试验结果确定优选的5083-H321生产工艺范围,对所确定范围内试样进行综合性能检测,最终确定最优的生产工艺。
2. 试验材料和试验方法
本文试验用5083铝合金板材化学成分如表1所示。
本文以实际生产流程为基础,分3步对5083-H321铝合金板材生产工艺进行研究。
第1步:采用表2所示的三因素四水平正交表(L1634)来安排试验节点,对试验后的试样进行力学性能检测,通过极差分析方法研究冷变形量、稳定化退火温度、稳定化退火时间对5083铝合金板材力学性能的影响主次关系。具体工艺安排如表3所示。
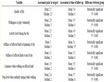
Table 1. Chemical composition table (wt%)
表1. 化学成分表(wt%)
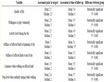
Table 2. Orthogonal experiment collocation table of factors and levels
表2. 正交试验因素与水平搭配表
表3. 工艺安排表
第2步:根据正交试验结果确定优选的5083-H321工艺范围。
第3步:对优选范围内试样进行力学性能、耐蚀性能检测,并进行金相组织与拉伸断口形貌观察,确定最优的工艺制度。
3. 试验结果与分析
3.1. 正交试验结果
将各板材按照表3所示的工艺进行处理,并截取拉伸试样进行室温拉伸,所得试验结果如表4所示。
表4. 力学性能
采取极差分析方法来确定各因素对5083-H321板材力学性能的影响主次关系。分别求出在每个因素每个水平下板材的力学性能总和K1、K2、K3、K4和其平均值k1、k2、k3、k4,进而求出极差R (k1~k4中最大值与最小值之差)。根据R的大小,来确定因素的主次关系,R越大,说明该因素对板材性能的影响越显著,反之则影响较小。分析表3中的数据,可以得到抗拉强度、屈服强度、延伸率的极差分别如表5~7所示。
表8为各因素对力学性能影响的极差,根据数值大小可知,对于抗拉强度、屈服强度、延伸率三个力学性能指标,冷变形量、稳定化退火温度及退火保温时间等三个因素的影响主次顺序为:冷变形量 > 退火保温时间 > 稳定化退火温度。
3.2. 优选工艺范围
从表5~7可以看出:随着变形程度的增加强度有所上升,而随着退火温度的增大、稳定化退火保温时间的延长,抗拉强度和屈服强度随之降低,但随着退火保温时间的延长,5083-H321板材的力学性能数值虽然减少,但其力学性能数值的变化率越来越小(见表5,表6中Ck1~Ck4),因此出于生产成本的角度考虑,在保证力学性能的同时,保温时间不宜过长,从表5~7得出的结果来看,以选择保温2 h为宜。
GB/T3880.2-2006标准中对3 mm厚5083-H321态板材的力学性能要求为:抗拉强度为305~380 Mpa、屈服强度大于215 Mpa、延伸率大于7%,而实际应用中客户希望产品性能要优于国家标准。从上述实验可以看出,较高强度、和较高延伸率(即k值较大)的因素和水平组合为A3B2C3、A3B3C3、A4B2C3、A4B3C3,(Ak3、Ak4、Bk2、Bk3为相应因素的各水平中的较大值),即冷变形量20%~25%、稳定化退火制度160℃~180℃/2h。
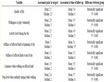
Table 5. Range analysis table of tensile strength (MPa)
表5. 抗拉强度极差分析表(MPa)
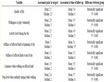
Table 6. Range analysis table of yield strength (MPa)
表6. 屈服强度极差分析表(MPa)
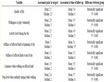
Table 7. Range analysis table of elongation (%)
表7. 延伸率极差分析表(%)
表8. 极差
3.3. 最优工艺制度
上述实验已确定优选的工艺范围为:冷变形量20%~25%、稳定化退火制度160℃~180℃/2h。为进一步的确定最优的生产工艺,对A3B2C3、A3B3C3、A4B2C3、A4B3C3四组试样的力学性能、耐蚀性能进行检测,对金相组织、拉伸断口形貌进行观察。为方便后续试验说明,对试样及具体工艺参数进行如下编号,如表9所示。
3.3.1. 力学性能
4种试样的力学性能值如表10所示,从数据中可以看出四组试样都满足GB/T3880.2-2006中3 mm厚5083-H321板材力学性能要求。相比之下,2#试样抗拉强度、屈服强度、延伸率的综合力学性能更好。
3.3.2. 耐蚀性能
按照GB/T 26491-2011标准采用质量损失法对四种试样进行晶间腐蚀测试,测试结果如表11所示,2#试样质量损失最少,为18.7 mg/cm2,说明其具有最好的耐晶间腐蚀性能。
对腐蚀后的试样横截面进行机械打磨,进行金相观测以了解腐蚀形态,检测结果如图1所示。1#试样腐蚀深度为53 um,2#试样腐蚀深度为48 um,3#试样腐蚀深度为73 um,4#试样腐蚀深度为67 um。四组试样腐蚀深度范围都在30~100 um范围内,腐蚀等级均为3级。通过对质量损失量与腐蚀形貌的观测可以判定试样2#的耐蚀性能相对最好。
3.3.3. 金相组织
图2分别为冷变形量20%、25%下稳定化退火制度160℃/2h、180℃/2h的光学金相组织,从图中可以看出金相沿轧制方向拉长,呈纤维状,虽然经过了160℃~180℃ 2 h稳定化退火,但因为退火温度较低,未发生再结晶,这与正交试验中退火温度需要2 h是相符合的。从1~4#的金相照片也可以看出,3#、4#的纤维状程度要稍大于1#、2#,这是因为3#、4#的变形程度相对较大。
3.3.4. 断口形貌
采用型号为FEI Quanta-200的背散射扫描电镜对四组试样的拉伸实验断口进行形貌检测,断口形貌检测结果如图3所示,从图中可以看出试样的断裂类型均为延性韧断,断口上韧窝数量较多,在韧窝的中心处存在颗粒状质点,这是冷轧过程中合金元素与Fe、Si等形成的粗大硬脆的杂质相破碎所致。这些硬而脆的杂质难溶或不溶于Al基体,当试样受到拉应力而发生塑性变形时,产生位错塞积的杂质相就容易产生应力集中,产生空洞、孔隙,形成裂纹源,变形量进一步增加后,裂纹尖端处应力同样增加,当应力超过材料断裂强度后,基体局部产生断裂,形成下图所示的韧窝。通过比较发现2#试样断口处韧窝数量较多,断裂面上大韧窝尺寸约为20 um,由此也进一步证实了2#试样的断裂韧性较其它3个试样好。
综合上述力学性能、耐蚀性能极其组织检测结果,4个试样都满足GB/T3880.2-2006对5083-H321
表9. 试样编号
表10. 力学性能
表11. 质量损失
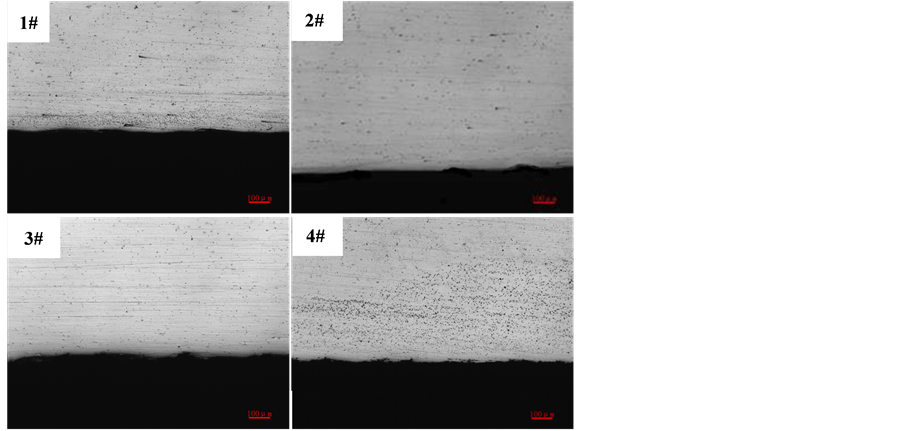
Figure 1. Intergranular corrosion morphology
图1. 晶间腐蚀形貌
力学性能的要求,而客户希望产品的综合性能要优于国家标准,2#试样强度虽然稍低于1#、3#试样,但其韧性和耐晶间腐蚀性能优于其他3个试样,且在20%的加工率下,经180℃/2h稳定化退火处理的2#试样其强度和韧性匹配较好。因此制备3 mm厚5083-H321铝合金板材最有的工艺为冷变形20%后进行280℃/2h退火。
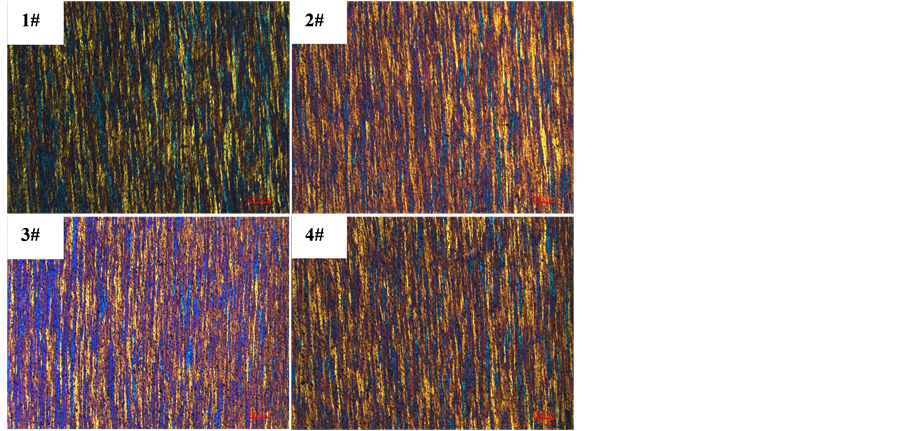
Figure 2. Metallographic structure (×50)
图2. 金相组织 (×50)
4. 讨论
Al-Mg合金在经冷变形后,晶界和滑移带处容易析出成网状分布的β相,从而严重影响其抗腐蚀性能。稳定化退火可以减少Mg在α (Al)固溶体的过饱和度,促使β相在晶界处析出,随着稳定化退火时间的延长Mg原子不断向晶界处传输使得β相长大,从而减少了β相的网状分布,使得晶内和晶界的电位差相对降低,因此提高了5083-H321的耐晶间腐蚀性能[4] -[8] 。但β相的析出将降低Mg元素在Al基体中的固溶强化效果,因而引起合金的力学性能下降。因此制备良好性能的板型需要对冷变形量、稳定化退火温度、稳定化退火时间进行精准控制,保证成品板材稳定化退火后力学性能满足要求,同时β相均匀析出,以使板材日后力学性能稳定、耐蚀性能良好。
冷变形过程中,随着冷变形量的增加,板材晶格畸变、晶粒破碎程度将加大,大晶粒沿轧制方向被拉长,形成纤维或带状组织,晶粒内部产生大量位错及点缺陷,位错间交互作用增强,因此,合金的强度随之增大 [9] ;而随着退火温度的增大、稳定化退火保温时间的延长,抗拉强度和屈服强度随之降低,这是由于板材在冷加工后积累了较大的形变储能,退火时导致回复,回复软化消除了部分加工硬化,因此强度降低而延伸率提高。但是本文中的稳定化退火温度较低,在200℃以下,远未达到5083铝合金再结晶温度,退火只起到低温回复效果,以点缺陷运动位置。这也是冷变形量对材料力学性能的影响明显大于其它量因素的原因,而稳定化退火温度与退火时间对力学性能的影响差别不大,时间影响稍大于退火温度,这可能是随着时间的延长低温回复更加充分 [10] - [13] 。
根据正交实验结果与极差分析,可确定优选的变形程度为20%~25%,退火温度问160℃~180℃,随着退火时间的增长力学性能虽稍有变化,但是时间越长,变化率越低,这与退火温度范围较低有关,综合生产成本,可将退火时间定为2 h。
优选范围内的四组试样结果表明:随着变形量的增大5083-H321板材的耐晶间腐蚀性能降低,而在变形量和稳定化退火时间相同时,在研究的稳定化退火温度下(160℃~180℃,板材未发生再结晶),板材的耐晶间腐蚀性能取决于稳定化退火的温度,温度越高板材回复软化程度越大,板材晶界处析出的β相尺寸越大,并且成不连续分布,降低了晶内和晶界的电位差,因此耐晶间腐蚀性能提高 [4] - [6] ,这就解释了2#试样耐晶间腐蚀性能较其他3个试样好。综合板材力学性能与耐蚀性能,冷变形量为20%、稳定化退火制度为180℃/2h是最佳的3 mm厚5083-H321生产工艺。
5. 结论
1) 正交试验与极差分析表明:在冷变形量为10%~25%、退火温度140℃~200℃、保温时间0.5~3 h范围内,冷变形量、退火温度、保温时间均会对板材力学性能的影响大小顺序为:冷变形量 > 稳定化退火时间 > 稳定化退火温度。
2) 3 mm厚5083-H321态板材优选的生产工艺范围为:冷轧变形量为20%~25%、退火制度为160℃~180℃/2h。
3) 当冷变形量为20%、退火制度为180℃/2h时试样可获得最优的综合性能:抗拉强度328 MPa、屈服强度256 MPa、延伸率16.4%晶间腐蚀质量损失量为18.7 mg/cm2,腐蚀深度为48 um。
项目基金
广西科技计划项目(编号:桂科重14122001-5)。