1. 引言
随着国内外对石油天然气资源的大量消耗及勘探力度的加大,油气资源的开发区域逐渐向更加复杂的地理环境,很多具有很大潜力的油气田所在地地理环境恶劣,地处丛林、山地、丘陵、沙漠等地形的区块逐渐增多。而且鉴于日益增长的人工费用,各个钻井承包商对钻机的智能化、机械化、快速移运性能提出了更高的要求。常规的自走轻便钻机多采用机械驱动,钻机数字化、自动化程度低;井架为桅杆式井架,须采用地锚固定井架绷绳,占用井场空间大,不能满足特殊地区的油气开发需要;钻机配套部件搬家需要大吨位吊车全程配合,拆装时间长,搬家成本高 [1] 。为解决上述问题,我公司结合以往钻机设计经验,研制了新型1200HP直立井架电动全拖挂钻机 [2] [3] 。该钻机结合了已有直立无绷绳井架技术 [4] 和钻台技术,开发了一种新型直立井架及钻台。车上传动部分采用交流变频电机驱动绞车方式,井架在主机车上随主机车整体运输,外围配套设备全部采用拖挂形式 [5] 。钻机的型式和基本参数符合GB/T 23505-2009标准,各设备设计制造符合API相关规范及HSE要求,满足在特殊地区钻井地域面积有限的使用要求。
2. 技术分析
2.1. 主要技术参数
名义钻探深度:4000 m (f114 mm钻杆);
绞车功率:1000 kW (1200HP)
大钩最大载荷:2250 kN;
井架高度:38 m;
最大抗风能力:110 km/h;
游动系统:6 × 5;
钢丝绳直径:32 mm (11/4 in)
钻台工作高度:6 m;
移运形式:拖挂式;
最高车速:45 km/h;
适应环境温度:−18℃~45℃。
2.2. 工作原理
1200HP直立井架电动拖挂钻机的绞车及转盘分别由独立的交流变频电机和减速箱组合驱动,可实现绞车和转盘的全程无级调速。传动系统采用齿轮传动,具有效率高,噪音低,使用寿命长等优势。钻机传动原理图如图1。
2.3. 结构组成
1200HP直立井架电动拖挂钻机主机主要由半挂车、电机、绞车、传动箱、井架、钻台、转盘驱动装置、控制系统等部分组成。钻机的主机移运状态如图2所示。
2.4. 钻机主要部件
2.4.1. 半挂车
ES9660Q型半挂车是专门为本拖挂钻机设计的半挂车底盘,具有以下主要特点:
① 前轴为空气悬挂,中间四轴采用四联板簧悬挂,后轴为空气悬挂,行驶稳定平顺、操作简便;车辆各轴载荷均匀;结构稳定简单、维护保养方便。
② 制动系统采用了双管路气压制动和放气弹簧制动室,不仅制动可靠、迅速,还具备了停车制动。
③ 支承装置为机械传动式支腿,升降轻便迅速,安全可靠。
2.4.2. 绞车
JC40DB型绞车主要用来为游动系统起下作业提供动力,与驱动机组一起安装于拖车台面上,绞车系统主要由主滚筒、盘式刹车系统、减速箱、自动送钻系统、角传动箱、润滑系统等组成。绞车滚筒轴采用优质合金钢整体锻造而成,两边由调心轴承支承,滚筒体上设置有Lebus绳槽。绞车设计符合API Spec 7 K《钻井和采油提升设备规范》。
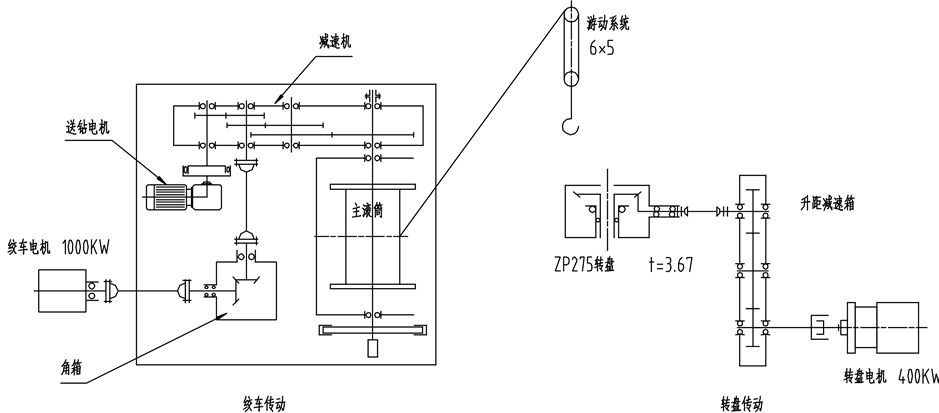
Figure 1. Drilling rig transmission schematic diagram
图1. 钻机传动原理图
1-井架;2-前支架;3-ES9660Q型半挂车;4-液压站;5-立管;6-绞车电机;7-JC40DB绞车;8-井架起升油缸;9-液压小绞车;10-后支架
Figure 2. Main unit transportation of drilling rig
图2. 钻机主机移运状态图
2.4.3. 井架
井架为直立无绷绳、双节套装、伸缩式K形井架。主要由天车、井架上体、井架下体、上下体承载机构、二层工作台、逃生装置、起升液缸、伸缩装置、立管总成、平衡装置及上、下体梯子等部件组成。井架立起和放倒由连接在运载车大梁和井架下体上的两个双作用变辐多级起升液缸来实现,伸出与缩回采用绞车动力实现。井架与运载车后支架之间采用铰支座连接,与钻台之间通过调节丝杠连接,确保井架连接稳固。此种型式的井架结构稳定,对井场的要求不高,无需地锚固定绷绳,满足在钻井地域面积有限的使用要求。井架设计符合API Spec 4F《钻井和修井井架、底座规范》。
(1) 基本参数
井架参数如下:
最大静钩载:2250 kN。
井架高度:38 m (天车底梁下平面至地面)。
二层台高度:16.5 m/17.5 m。
二层台容量:4000 m (4-1/2钻杆、19米立根)。
(2) 环境参数
井架设计风速,如表1。
(3) 设计载荷
根据API Spec 4F第4版规范载荷组成的规定,结构计算以下工况如表2。
(4) 井架模型图示
1) 作业工况
井架作业工况模型如图3所示。
2) 起升工况:
井架起升工况模型如图4所示。
(5) 结论
通过分析表明,该结构在各工况下杆件最大拉应力203 MPa;最大长细比117.36;稳定性判别数UCR值均小于相应工况的名义应力校核系数。最大拉应力处的结构所用材料为屈服强度345 MPa,安全系数:345/203 = 1.70。该结构的强度、刚度、稳定性均满足API规范要求,是安全的。
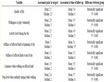
Table 1. Design wind speed for derrick
表1. 井架设计风速
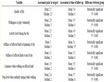
Table 2. Design loading for derrick
表2. 井架设计载荷
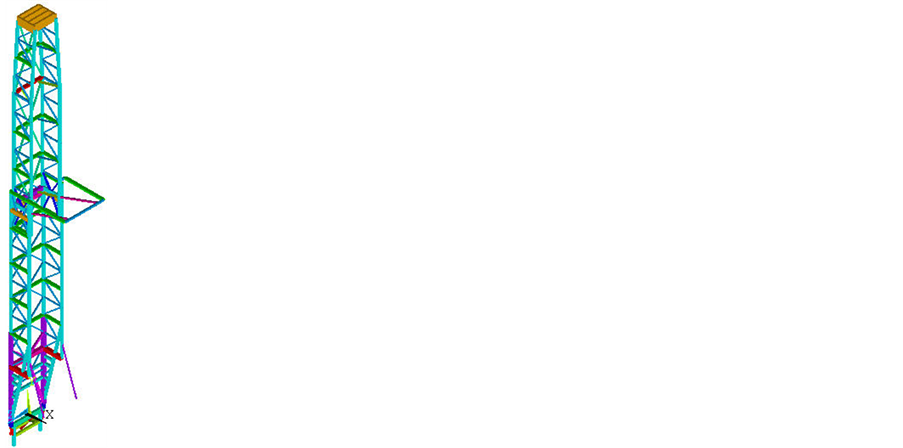
Figure 3. Mast working condition model drawing
图3. 井架作业模型图
2.4.4. 钻台
钻台由船形底座、井架基础、转盘座、立根座、转盘驱动装置、飘台、坡道、防喷器安装装置等组成。船形底座用来支承车装钻机主机、井架基础用来支承井架的重量及大钩载荷,转盘座、立根座用来承受钻井作业时转盘载荷及存放立根,转盘驱动装置用于驱动转盘进行钻进工作,位于台体上的飘台用于存放井口工具,及为司钻和井口操作人员提供作业场所等,台体台面下提供井口装置安装空间,防喷器安装装置用于安装防喷器,坡道用于单根上下钻台及甩钻具作业。钻井作业时钻机载荷通过钻台的上
述不同的部件传递到基础与地面 [6] 。底座设计符合API Spec 4F《钻井和修井井架、底座规范》。
(1) 作业模型
钻台作业工况模型如图5所示。
(2) 载荷模拟
钻台结构的自重载荷在模型中体现,由计算程序自动计算生成。设备的重量按照适当的载荷形式施加。
作业荷载:
转盘最大载荷2250 kN;
额定立根载荷1200 kN。
(3) 吊装模型
钻台吊装工况模型如图6所示。
(4) 结论
分析表明,该钻台结构在各工况下杆件最大拉应力47.433 MPa;最大长细比95.826;稳定性判别数UCR值均小于相应工况的名义应力校核系数。最大拉应力处的杆件的最大拉伸应力小于许用拉应力的
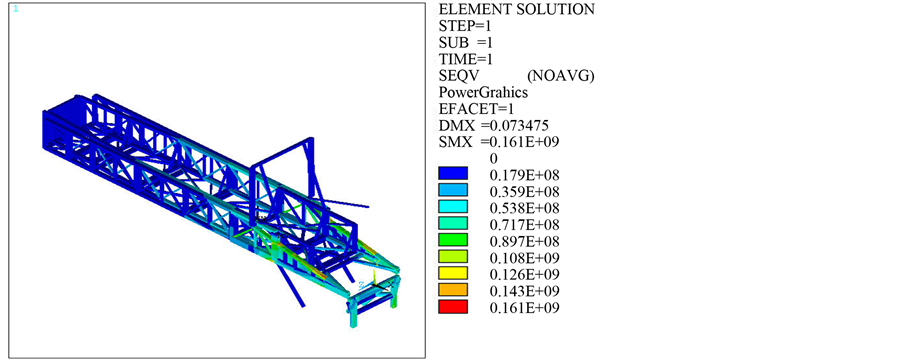
Figure 4. Derrick lifting condition model
图4. 井架起升模型图
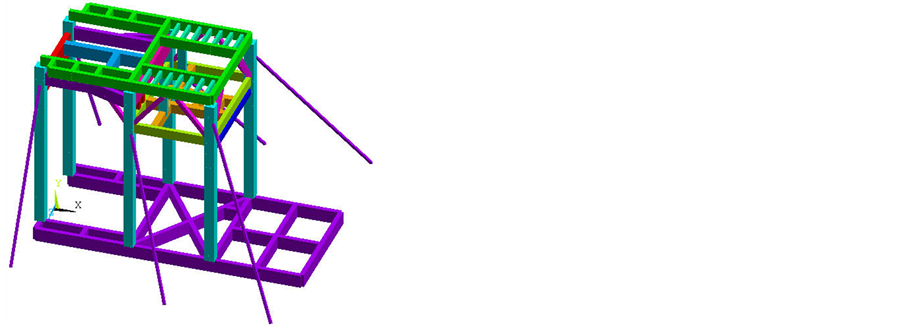
Figure 5. Substructure working condition model
图5. 钻台作业模型图
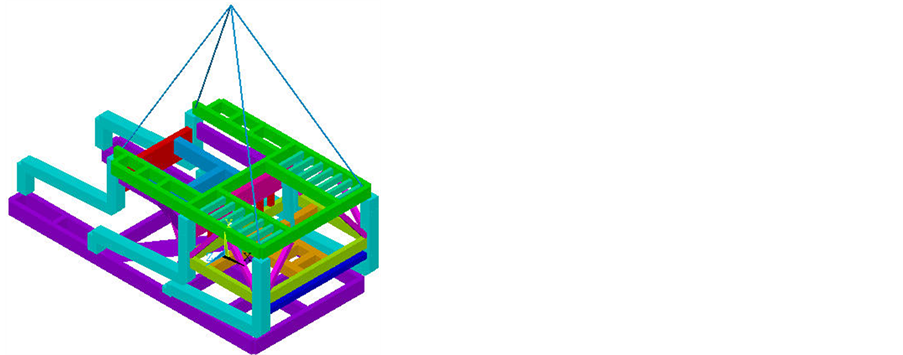
Figure 6. Substructure lifting condition model
图6. 钻台吊装模型图
70%,该结构的强度、刚度、稳定性均满足API规范要求,是安全的。
2.4.5. 转盘驱动装置
转盘驱动装置主要用于为钻具的旋转提供动力,以实现钻井工艺的要求。转盘采用独立驱动方式,主要由交流变频电机、联轴器、升距箱、转盘惯刹、万向轴等部件组成。动力由1台400 kW交流变频电机经联轴器、齿轮升距箱、万向轴驱动转盘,转盘驱动装置整体沉于钻台面下,电机、冷却风机、升距箱及其润滑系统均布置在一个底座上,形成一个整体运输单元。
2.5. 主要性能特点
① 钻机的智能化程度高,能够实现对钻井参数的连续数字化控制;
② 钻机配套直立套装无绷绳井架,井架底部开裆大,稳定性高,不需要打地锚,占用井场空间小,可适应丛林、山地、丘陵、沙漠等特殊地区作业要求。
③ 钻机主机及外围配套部件均采用拖挂结构,搬家过程中不需要大量的运输车辆,仅配套4~5台拖车头及1~2台平板车即可完成搬家运输,钻机移运性能高。
④ 交流变频电驱动单滚筒绞车,绞车可实现无极调速及数字化控制,同时配套全数字自动送钻装置一套,自动送钻速度范围大,适宜于衡钻压钻井及欠平衡钻井,满足现代钻井工艺的要求。
3. 关键技术
3.1. 钻机整体动力学及控制仿真设计
建立钻机仿真设计平台,对钻机的动力性能、结构稳定性、振动区域进行理论系统分析,提高设计的科学性和合理性。包括:三维实体建模、几何建模、模态分析、动力学建模与仿真分析、电机控制与仿真分析、参数化的石油钻机动力学模型等。
3.2. 1200HP交流变频驱动绞车
主电机采用1000 kW单电机经齿轮箱驱动,配37 kW送钻电机,整体结构紧凑,送钻电机还可作为应急动力,传动路线简单可靠;电子刹把液压盘刹:电信号控制,控制灵敏性高,自动控制容易实现,提高钻进效率和安全性;自动送钻系统:采用400 V/37 kW防爆变频小电机反拖,实现“恒钻压”和“恒钻速”钻进,易实现自动化控制,低速和钻压稳定性能高。
3.3. 直立套装井架
采用双节直立套装无绷绳井架,井架工作状态为直立状态,井架底部开裆大,稳定性高,不需要打绷绳,占用井场空间小。井架上体截面为梯形,保证了井架开口尺寸,和机械伸缩所需的绳索空间。顶驱导轨采用双导轨结构,与两侧井架前立柱一体设计。
3.4. 新型旋升式钻台
钻台立柱采用变中心距设计,前后中心距不同,确保了井架的工作位置和井口中心。钻台底部设计液压缸绳索结构,实现防喷器吊装。
3.5. 重载半挂车
半挂车车架主要由两根主纵梁和边梁以及若干根横梁焊接而成,钢材采用优质钢。主纵梁采用绞车后部加高的变截面结构形式,保证车架具有高强度的同时,有效降低整机安装高度。为满足主机车载荷要求采用六桥悬挂配置,一、六桥为空气弹簧平衡悬挂,二、三、四、五桥采用四联板簧悬挂,六桥为随动转向空气悬挂,具有行驶稳定平顺、转弯半径小,操作简便,车辆各轴载荷分布均匀,减少轮胎和刹车的磨损等优点。
4. 试验和应用情况
4.1. 试验情况
严格按照试验规程,对钻机运转性能、行驶性能进行测试。
(1) 对钻机半挂车进行路试。通过200 km不同路况的试验,其悬挂系统工作平稳,具有足够的承载能力,各个部件运行正常,制动灵敏。
(2) 井架起升及载荷试验。因井架采用的是直立无绷绳井架,为了保证井架强度及稳定性,井架开档较桅杆式井架宽且用料增大,所以井架起升系统选用了0#高压(额定压力21 MPa)起升液压缸。试验中井架实际起升压力最大值在17~18 MPa之间,与理论计算误差在允许范围内,表明井架设计的理论分析符合实际工况。
(3) 钻机载荷试验。对井架及钻台分阶段加载,进行载荷测试。通过拉地锚的方式大钩拉力从1200 kN开始,以600 kN的增量增加,最终达到最大钩载2250 kN,井架的应力测试结果的局部最大值与理论计算偏差在允许范围内,井架及底座的性能负荷设计要求。
(4) 钻机配套试验。钻机按照设计要求在厂内进行全配套试验,所有设备在各自单独试运转合格后进行整体12小时不间断试验。试验项目包括钻机主机、泥浆循环系统、高压管汇系统、泥浆泵组、柴油发电机组、VDF/MCC控制系统等。经过12小时不间断试验,钻机各部件运转平稳,各项指标符合试车规程参考值要求。
4.2. 应用情况
该新型1200HP直立井架电动拖挂钻机是我公司与某公司海外项目部合作开发,该型钻机本批共投产3套,在厂内完成组装及试验后即发往现场作业,通过现场跟踪及用户反馈,认为该型号钻机性能稳定,结构紧凑,对井场的面积要求不高,适应能力强,整机移运性好,安装快捷方便,达到预期要求,为用户赢得了更大的利润空间。
5. 结论
① 该钻机在结构设计方面,主机及配套设备对钻井场地要求不高,适合在丛林、山地、丘陵、沙漠等特殊地区进行油气开发,钻机配套设备拆装快捷,移运性能良好。
② 钻机在总体配套方面,配套两台F1300泥浆泵,配套了顶驱、铁钻工、动力猫道等自动化设备,钻机整体自动化程度高。
③ 钻机在动力配置方面,采用AC-DC-AC驱动,实现对钻井参数的连续数字化控制,发电机和网电兼容,系统互补性强,再生能量统一处理,稳定性和控制灵活性好。
④ 钻机在控制方面,司钻系统触摸屏操作,实现了机、电、液、气一体化数字控制,钻机的智能化和集成技术具有国际先进水平。