1. 引言
纤维增强树脂基复合材料(Fiber reinforced polymers, FRP)以其优异的比强度、比模量、耐疲劳和耐腐蚀等性能在航空航天以及工业领域有着广泛的应用,如飞机机身和机翼、轨道交通、新能源汽车、风电叶片等。复合材料在生产过程中由于制造工艺和人为因素会在其内部不可避免的形成孔隙、夹杂、分层等缺陷。其中,孔隙是复合材料中最常见的缺陷。这些孔隙的存在对复合材料的力学性能产生不利影响,尤其对像机翼和风电叶片等大型结构件影响更为显著。因此,对复合材料的孔隙及其孔隙对力学性能的影响进行综合评价是非常必要的,对保证复合材料结构的可靠性、防止事故发生以及节约复合材料加工成本具有重大意义。本文简要的介绍了孔隙的形成机理、孔隙的表征评价方法以及孔隙对力学性能的影响。
2. 纤维增强树脂基复合材料孔隙形成机理
孔隙是复合材料制造过程中形成的空洞,普遍存在于增强纤维束内、树脂基体中以及层间区域。当孔隙尺寸较小时,一般多为小圆球形,分散性较大,主要集中在分布在树脂基体内;当孔隙尺寸较大时,多为细长的椭球形,主要分布在纤维束内以及纤维与树脂的层间界面区域内。孔隙的产生的原因主要有以下几方面因素:1) 纤维和/或树脂基体中裹入空气,在固化过程中包夹的气泡不能完全被排除;2) 树脂基体和有机溶剂在固化反应中产生低分子量挥发物而存留在复合材料内部;3) 树脂基体粘度高、纤维束质地紧密,深层纤维没有被树脂基体完全浸润;4) 成型过程中真空系统泄露,外部空气进行材料内部。
Springer和Kardos [1] [2] 从物理包夹现象形成气泡和经典成核理论对复合材料中的孔隙形成进行了研究分析,并建立了扩散控制的气泡生长和消融理论模型。Springer认为机械夹杂形成气泡,它们留存在复合材料内部不能排除而形成孔隙。Kardos认为树脂基体中溶解的水分是形成孔隙的主要原因,当气泡的蒸汽压力小于树脂压力时,溶解在树脂基体中的水分在压力差的作用下通过扩散进入气泡使其变大,当树脂粘度骤增发生凝胶时,气泡被封堵在复合材料内部形成孔隙。张佐光等人 [3] 详细研究了复合材料成型温度、固化压力和操作工艺等因素对孔隙的影响,并对上述机理进行修正及理论分析,提出吸湿水扩散生长和夹杂空气是复合材料孔隙的主要来源。
3. 纤维增强树脂基复合材料孔隙的表征方法
纤维增强树脂基复合材料孔隙的表征一般分为定性指标和定量指标。定性指标是指孔隙的大小、尺寸和分布等信息。定量指标是指孔隙的含量,用孔隙率来表征,孔隙率又分为体积孔隙率和面积孔隙率,即单位体积内所含孔隙的体积百分数和单位面积内所含孔隙的面积百分数;复合材料孔隙检测方法分为有损检测和无损检测。其中有损检测方法有密度法 [4] ,水吸收法,显微照相法等 [5] [6] ;无损检测方法有超声扫描法 [7] [8] ,超声衰减法 [9] ,射线检测法 [10] ,热红外成像法 [11] 等。
3.1. 密度法
复合材料的孔隙含量与增强纤维、树脂基体和复合材料的密度以及纤维和树脂的百分比有关,用式(1)计算体积孔隙率
为:
(1)
式中
——纤维所占体积百分比;
——树脂所占体积百分比;
——纤维所占重量百分比;
——树脂所占重量百分比;
——树脂密度;
——纤维密度。
纤维和树脂含量的测量采用化学或热学方法,在去除树脂过程中纤维自身氧化失重而造成测量误差。在计算纤维和树脂密度及含量时若有0.01%的误差,就会导致孔隙率2.5%的误差。所以密度法具有局限性,测得的孔隙率数值偏差不大于±0.5%。由该法得到的是基于小样品的总的孔隙体积分数,孔隙尺寸、形状和分布无法测定。该方法的优点是比较容易实现,不需要精密仪器。
3.2. 显微照相法
把样品进行剖切,经抛光后在配有格栅的显微镜下观察。计算孔隙率
时(式2),只计算落入格栅交线处的那些孔隙。
(2)
式中
——孔隙上格点数;
——格点总数;
该方法是一种破坏测试法,检测时样品必须进行切割,测完孔隙率后不能进行力学性能测试。若先进行力学性能测试,测量的孔隙率很难将试验过程产生的微裂纹与原有孔隙分开。显微照相法也能测定孔隙的形状、大小及分布等一些较为具体的信息,比密度测定法准确,是目前孔隙率检测方法中精度较高的,但因小试样不能代表整体,所以总的精度只能比±0.5%稍高一点。
3.3. 超声检测法
超声检测方法方便、快捷,是目前复合材料中尤为重要和有效的孔隙率测试手段,它是利用超声波在不同介质中传播速度的差异以及在传播方向上有能量损失和信号衰减来确定材料内孔隙缺陷的存在,实现对整个测试样品的孔隙率进行评价,但是该方法只能给出孔隙分布的定性评价,不能给出孔隙含量、孔隙的大小、尺寸和形状等信息。
Stone和Clarke [12] 较早开展超声衰减法来进行孔隙的测定试验。分析试验结果,发现衰减α和孔隙率P近似成平方关系,得到经验公式:α = kP2。给定频率下,k为常数;当频率变化时,可以将k近似表示成指数形式,因而α与P的关系可以表示成:α = 0.0794f1.27 kP2。通过对用预浸料制备的复合板进行试验发现,当孔隙率P ≤ 1.5%时,孔隙率是由挥发物导致的,直径在5~20 µm之间,孔隙呈球形,孔隙率越大,孔隙直径也就越大;当孔隙率P ≥ 1.5%时,孔隙是由空气引起的,孔隙被压平和拉长。Stone和Clarke采用双线性函数表示了衰减与孔隙率之间的关系:
当P < 1.5%时,α = a1(f) + b1(f)
当P ≥ 1.5%时,α = a2(f) + b2(f)
式中,a1、b1、a2、b2在给定频率下是常数。图1为双线模式的计算结果与试验结果的对比图,从图中可以看出,试验结果很好的印证了计算结果。Stone和Clarke的经验公式和总结的结论至今仍被复合材料孔隙的研究人员进行参考和引用,被当成经典。
Hsu和Nair [13] 在试验中发现,孔隙率P不但与衰减系数随频率变化率dα/df有很好的线性关系,而且随着孔隙率的增加,中心频率单调降低。中心频率的下降量与孔隙率也存在良好的线性关系。高频率导致高衰减,低频率导致低衰减。Hsu [14] 用试验结果并与理论结果进行了对比,如图2所示。从图中可以看出,当孔隙率<10时,理论结果与试验结果符合的非常好。
3.4. 射线检测法
将感光胶片置于被检测样品后面,接收透过试样不同强度的射线,胶片经过暗室处理后得到透射影像,根据影像的形状和黑度确定被测样品中孔隙的大小、形状和位置。
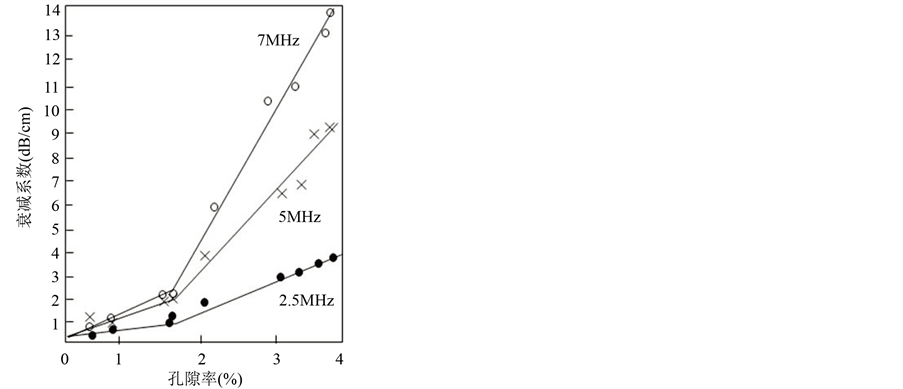
Figure 1. The comparison curves of bilinear pattern theoretical and experimental results [12]
图1. 双线性模式的理论与试验结果对比图 [12]
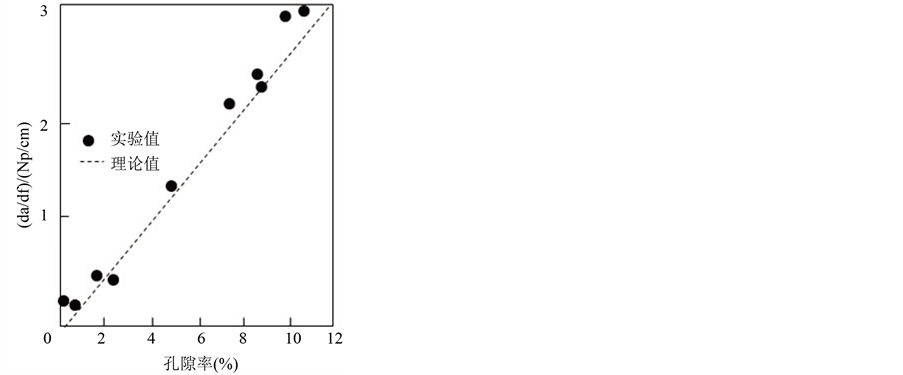
Figure 2. The curve of porosity and frequency change rate [14]
图2. 孔隙率与频率变化率的关系曲线 [14]
3.5. 热红外成像法
采用某种加热的方式激励被测样品的内部缺陷,使被检测样品表面形成反映这些缺陷的温度差,探测器将强度不等的辐射信号转换成相应的电信号,然后经过放大和视频处理,形成人眼可见的视频图像,实现对物品缺陷的检测。
4. 孔隙对纤维增强树脂基复合材料力学性能的影响
复合材料中孔隙的存在降低其力学性能,如层间剪切强度,纵向和横向弯曲强度和模量,纵向和横向拉伸强度和模量,压缩强度和模量等。而且,不同的孔隙含量、尺寸和分布等因素对不同组分复合材料材料的力学性能影响程度差别较大,离散程度较高。因此,从理论上预测孔隙率对复合材料力学性能的影响比较困难。所以,国内外复合材料研究者对孔隙对于复合材料力学性能的影响做了大量的理论分析和试验研究。
Judd和Wright [15] 通过研究后指出,当复合材料的孔隙率在0%~4%范围内时,孔隙率每增加1%,层间剪切强度大约降低7%。当孔隙率大于5%时,材料强度损失过大,层间剪切强度随孔隙率变化变缓甚至趋于稳定。
Olivier等人 [16] 研究了两种不同碳纤维/环氧树脂预浸料在不同固化压力下产生的孔隙率对复合材料力学性能的影响。研究结果表明,复合材料纵向拉伸模量和泊松比几乎不受孔隙率的影响,这主要是因为复合材料固化后纤维体积含量很高。从图中可以看出,当孔隙率从0.3%增加到10.3%时,纵向拉伸强度下降约为12%,这可能是由于较大的孔隙主要是位于层间,并且大部分孔隙表面与纤维接触,使得纤维局部变形所致。从图3(a)和图3(b)中可知,,横向拉伸强度和模量对孔隙率很敏感,两种材料的横向拉伸强度均下降30%左右,横向拉伸模量下降10%左右。图3(c)表明,对于复合材料A,当孔隙率从0.3%增加到6.8%时,弯曲模量下降约4%;而对于复合材料B,当孔隙率从1.4%增加到8.4%时,弯曲模量下降约15%。从图3(d)中可以看出,复合材料A的孔隙率从0.3%增加到6.8%时,层间剪切强度下降约为15%;复合材料B的孔隙率从1.4%增加到8.4%时,层间剪切强度下降约为35%。这表明孔隙率对层间剪切强度的影响是非常大的。从图中还可以看出,两种材料的性能受孔隙率的影响程度是不同的,Olivier等认为这是由孔隙的形状、尺寸和分布等差异而造成的。因此,孔隙的形状、尺寸和分布等因素对复合材料力学性能的影响是十分必要的。
Almeida等人 [17] 研究指出:当孔隙率低于某个临界值时,复合材料的拉伸强度、弯曲强度和层间剪切强度受孔隙率影响较小。有些研究表明,引起材料力学性能下降的临界孔隙率是1%~4%。
Hagstrand等人 [18] 研究了单向玻璃纤维聚丙烯复合材料的孔隙率对结构抗弯性能的影响。研究结果表明:当孔隙率小于4%时,孔隙率每增加1%,层间剪切强度降低约7%。随着孔隙含量的增加,拉伸、剪切、抗弯和抗压强度也降低,其中弯曲模量和强度分别下降20%和28%。
Bowles等人 [19] 以碳纤维/环氧树脂层合板和碳纤维/双马来亚胺树脂层合板为研究对象,研究孔隙率对其力学性能的影响。研究结果表明:常温下,当孔隙率小于0.9%时,复合材料的力学性能受孔隙率的影响非常小,几乎可以忽略;当孔隙率大于0.9%时,复合材料的弯曲强度和剪切强度开始显著下降。Almeida等人通过大量试验研究不同孔隙率对复合材料静力学特性和耐疲劳性能的影响,研究结果指出,复合材料的静态力学性能受孔隙率的影响程度要比疲劳寿命所受到的影响小的多。
国内也对孔隙率对纤维增强树脂基复合材料力学性能的影响进行了大量的试验研究。刘志真等人 [20] 研究表明:复合材料的弯曲强度随孔隙率的增加逐渐下降,如图4(a)所示,当孔隙率大于3%时,弯曲强度的下降趋于平缓,弯曲强度保持率约75%。孔隙率对复合材料的弯曲模量影响不大。图4(b)为剪切强
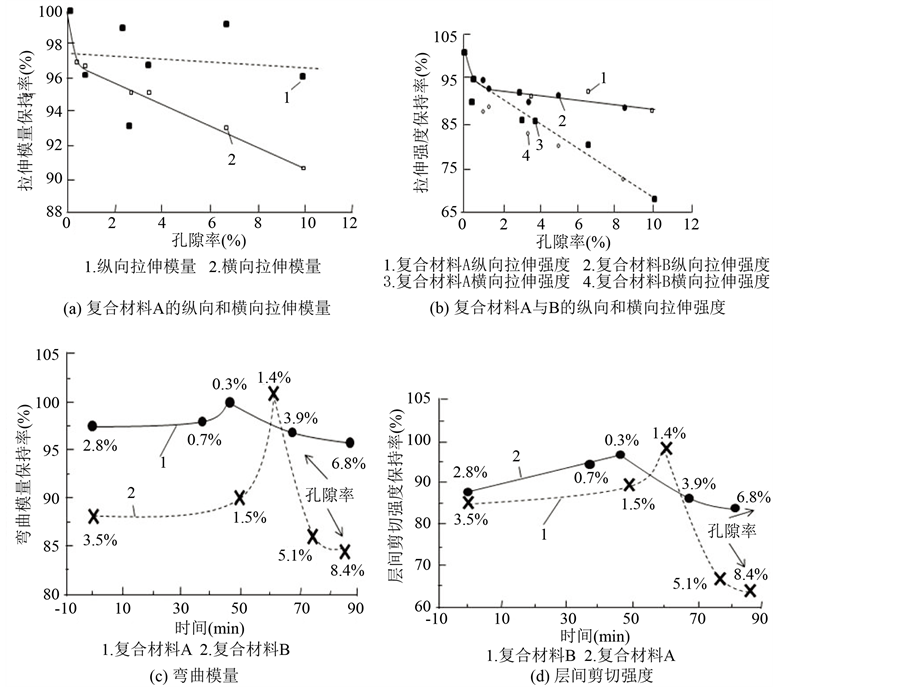
Figure 3. The curves of tensile modulus (a) and strength (b), flexural modulus (c) and interlaminar shear strength (d) with porosity changes [16]
图3. 拉伸模量和强度(a)、(b)、弯曲模量(c)和层间剪切强度(d)随孔隙的变化图谱 [16]
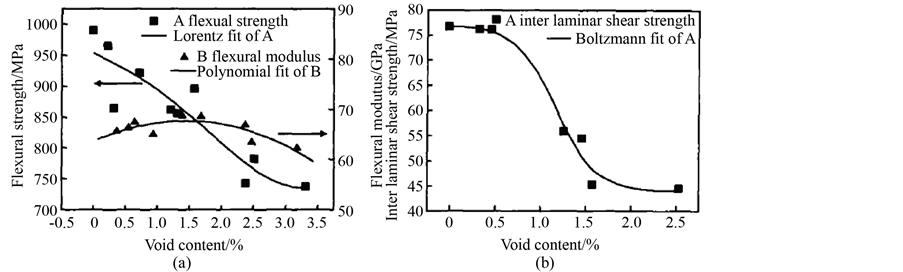
Figure 4. The relationship between porosity and the flexural property (a) and the interlaminar shear strength (b) [20]
图4. 孔隙率和弯曲性能(a)及剪切强度(b)之间的关系 [20]
度和孔隙率之间的关系曲线,从图中可以看出,随着孔隙率的增加,剪切强度逐渐下降。当孔隙率小于0.75%时,孔隙率对剪切强度的影响不大;当孔隙率大于1.5%时,剪切强度迅速下降约40%。
5. 结论
理论和试验都表明,孔隙的存在降低复合材料层间剪切强度、纵向和横向强度和模量和耐疲劳性等力学性能。在4%以内每含有1%的孔隙,复合材料的层间剪切强度减少约7%,在4%以上降低较为缓慢。其它力学性能也受到不同程度的影响。由于孔隙的形状、尺寸、分布以及纤维、基体和界面的力学性能等可变因素,孔隙对复合材料层力学性能的影响是个非常复杂的问题。能正确测量孔隙含量、弄清孔隙的形成机理和评价孔隙对复合材料性能的影响,对纤维增强树脂基复合材料的应用和制备有重要的意义。