1. 引言
固体浮力材料是各种潜器如AUV (Autonomous Underwater Vehicle)、ROV (Underwater Operated Vehicle)、水下拖体、潜标等水下装备重力平衡配套的关键材料,随着全球范围内海下资源勘探、海洋环境监测等领域的快速发展,固体浮力材料的制备及应用技术的也受到了关注 [1] 。在深海环境下压力较高,对固体浮力材料要求苛刻,所以,解决深海固体浮力材料的制备技术问题成为人们研究的重要方向之一,近年来人们从浮力材料的制备 [2] [3] [4] 、结构 [5] [6] 、性能表征 [7] [8] 等多方面展开了研究,并取得了可喜的成果。随着国家蓝海政策的不断推进,针对近、浅海(小于500 m深)的水体资源、海底资源勘探和开发,海洋环境的监测与评价等工作将进入常态化阶段,与此同时,与之相应的浅海海下装备的制造业必将全面兴起。然而,不容忽视的问题是,目前,在小于500 m深度的下潜装备上所用的固体浮力材料基本上还沿用深海的固体浮力材料,即空心玻璃微珠泡沫材料。虽然这种材料可以很好地提供浮力,但是在实际工程应用中不得不考虑两个问题。第一,空心玻璃微珠泡沫材料针对深海开发,其制造成本高,一般最低使用深度也接近2000 m,该材料用在浅海是极大的浪费;第二,空心玻璃微珠泡沫材料的最小密度也要大于0.45 g/cm3,针对浅海的工作压力,应该有进一步降低材料密度的空间。由此可见,开发一种适用于浅海、成本低、密度低、综合性能优越的新材料必将对近、浅海海下装备的发展和进步起到巨大的促进作用。
EPS (Expanded Polystyrene)泡沫颗粒是一种具有闭气泡结构的轻质材料 [9] ,以其良好的超轻、隔热、降振等特性(一般密度为0.01~0.045 g/cm3)在包装材料 [10] 、建筑保温材料 [11] [12] 、道路桥梁工程减震 [13] 等领域得到了广泛的应用。充分利用EPS泡沫材料超轻和廉价的特性,将其填充到环氧树脂材料中,有望获得一种具有适当强度的低密度、低成本复合材料。本文就是以环氧E44为基体材料,EPS泡沫颗粒为填充物,制备了一种轻质复合材料,探讨了该材料在1 MPa静水压力下的抗变形性能及吸水率,探讨了该材料作为浅海下潜浮力材料应用的可能性,为制备浅海用固体浮力材料提供一种新的制备思路与理论依据。
2. 实验
2.1. 实验原材料
实验采用的原料均为市场上方便购买的商业试剂和工业原料,相关原料详见表1。
其中EPS颗粒直径为0.5~0.7毫米,体积密度为0.045 g/cm3,环氧树脂密度约为1.20 g/cm3,固化剂密度为1.05 g/cm3。
2.2. 试样制备
将环氧树脂、固化剂按照一定的质量比混合,充分搅拌,然后加入EPS颗粒继续搅拌,充分混合均匀,使EPS颗粒表面被环氧树脂充分浸润。将混和好的物料,填入模具(实验室自制)中,在真空环境下进行双向加压,然后在保持某一恒定压力和室温环境下经24小时固化成型,脱模后得到实验样品。
2.3. 性能测试及结构分析
2.3.1. 密度测定
把各组样品用GTQTM5000型精密切割机切成规则的长方体状试样,按照GB/T1033.1-2008“塑料非泡沫塑料密度的测定”的规定测量。
2.3.2. 压缩性能测试
本文所制备的固体浮力材料其压缩性能的测量按照国家标准GB/T 8813-2008“硬质泡沫塑料压缩试验方法”实施。制作5个测试试样,试样尺寸:50 × 50 × 50 mm,采用上海协强仪器制造有限公司型号CTM8050的微机控制电子万能材料试验机进行测试。
2.3.3. 吸水率和耐静水压性能测试
吸水率和耐静水压性能测试参照 MIL-S-24154A的规定实施,采用济南思明特科技有限公司生产的深海静水压模拟装备SUP-HD-12000进行测定。
2.3.4. 材料结构表征
采用光学显微镜对材料试样的切割表面结构进行观察。
3. 结果与讨论
3.1. 成型压力的确定
EPS颗粒是一种具有较大压缩变形率的材料,本实验旨在探索一种应用于一定深度水下的材料,并且在使用环境下,材料应具有很小的变形率和吸水率。在一定的压力下固化成型是达到这一目标的必要手段。EPS颗粒的堆积压缩性能是确定材料成型压力的重要参考。在本试验中,将EPS颗粒堆积于Φ80 × 47 mm的圆筒模具中充分震实,在万能试验机上以5 mm/min的加载速率进行了准静态压缩性能实验,得到了EPS颗粒压缩过程中应力-压缩率(应变)及密度-压缩率的变化规律如图1所示。从图中明显看出,EPS颗粒堆积体在很小的应力作用下产生了很大的变形率,直到压缩率约达到80%时应力才上升到约1.25 MPa。随后,应力随着变形率的增加急速上升,当变形率达到91%时,应力达到了3.2 MPa。可见EPS颗粒的压缩过程明显区分为两个阶段,其一是变形率达到80%以前,在该阶段内主要是颗粒间空隙气体的排除过程,泡沫颗粒由球形变成多面体,属于弹性变形范围,此时泡沫颗粒形态将发生如图1中A到B状态的转变。当EPS颗粒继续被压缩时,泡沫颗粒内部的气体被挤出,泡沫颗粒的体积收缩并致密化,堆积体的形态发生图1中B到C的变化,压缩体密度也急剧上升。这一规律与文献报道的结论相一致 [14] 。
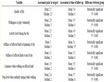
Table 1. Main experimental raw material
表1. 主要实验原料
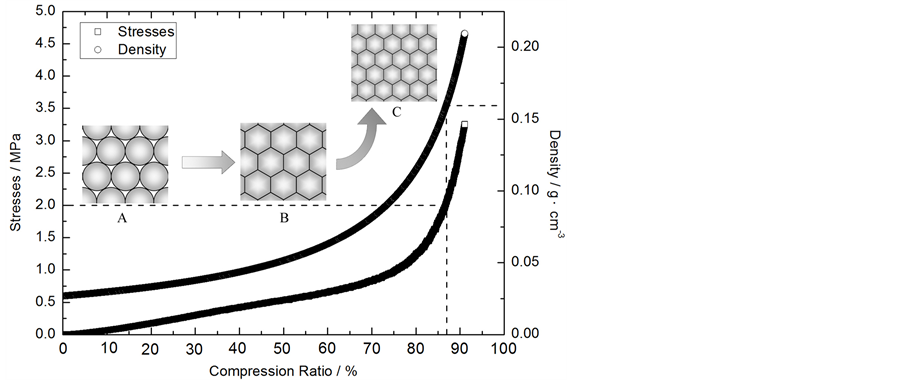
Figure 1. Compression performance of the EPS particles
图1. EPS颗粒堆积压缩性能曲线
另外,EPS颗粒压缩体的密度随着压缩率的增加也发生了类似的变化,在压缩率小于80%以前其密度由自然堆积密度(约0.027 g/cm3)增加到约0.1 g/cm3,压缩率增加到91%时,密度急增至0.21 g/cm3。从以上性能分析中可以看出,当EPS颗粒压缩率从80%~90%之间变化时,应力和密度的变化范围分别为1.25~2.9 MPa和0.115~0.194 g/cm3。通常人们对浅水浮力材料的要求是希望其密度小于0.3 g/cm3,考虑到EPS颗粒与环氧树脂复合后的增重,故实验选取复合材料的固化成型压力为2 MPa,此时EPS颗粒的压实密度约为0.165 g/cm3,与适量的环氧树脂复合后有望将材料的密度控制在0.3 g/cm3以下。
3.2. EPS/环氧树脂复合材料性能
3.2.1. EPS颗粒与环氧树脂复合比与材料密度的关系
复合材料的组成以EPS颗粒与环氧树脂基体的质量比β计,为叙述方便,定义其为复合比。实验分别选择β值0.7、0.75、0.8、0.85和0.9的五个组分,在真空环境下,采用双向加压方法制备复合材料试样,固化成形圧力为2 MPa。根据3.1中的实验结果,在2 MPa下,EPS颗粒的压实密度为0.165 g/cm3,以ρe记。从所用原料参数计算出固化环氧树脂基体的密度ρ为1.17 g/cm3。考虑到液态环氧树脂具有很小的压缩比,在所选用的成形圧力下可认为其体积不发生变化,可推算出不同配比的EPS颗粒/环氧树脂复合材料的预期密度ρ*,即:
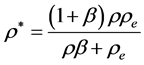
五组试样的实测密度和计算密度与材料组成的关系如图2所示,从图中可以看出,试样的计算密度和实测密度均随着试样中EPS颗粒用量的增加而降低,计算密度高于实测密度,计算密度与实测密度的
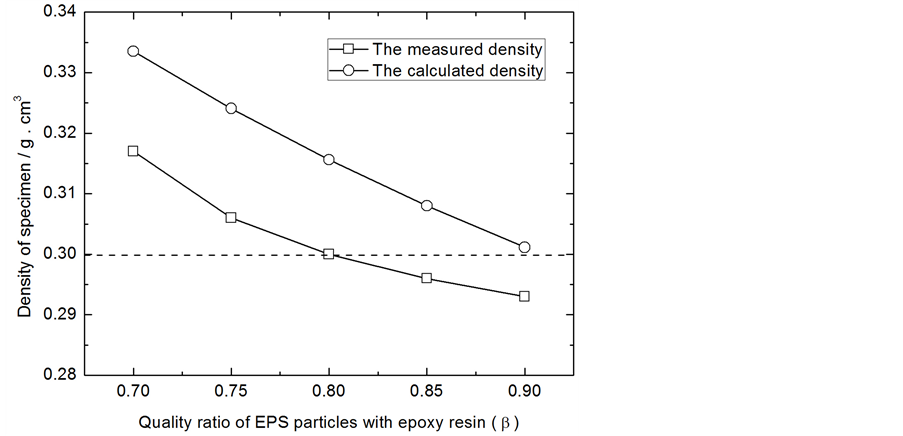
Figure 2. The relationship of the density and composition of specimens
图2. 试样密度与组成的关系
偏差随着EPS颗粒用量的增加而减小。当材料的复合比大于0.8时,所得到的复合材料密度均小于0.3 g/cm3。
3.2.2. 复合材料的压缩性能
对实验所得的β值为0.7、0.75、0.8、0.85和0.9的五组试样按照标准GB/T 8813-2008进行压缩实验的结果如图3所示。从图中可以看出,5组试样均表现出明显的弹塑性变形行为,并且,随着复合比β值增加,其变形率也增大。在应于1 MPa的应力下,5组试样的平均应变值在1.8%~3.2%之间。对上述5组试样分别施加1 MPa的应力后,测量其残余应变的结果表明,其残余应变均小于0.2%,所得到的复合材料在1 MPa以下的应力下基本处于弹性变形范围。
作为水下浮力材料的应用,材料的吸水率是其关键的性能之一 [15] 。对以上五组材料在1MPa的静水压力下,进行了24小时的保压实验,并对其吸水率进行了分析。其结果表明,5组试样经24小时的保压试验后,材料的形状及表面状态完好,其吸水率如图4所示。材料的吸水率随着复合比的增加而增大,但所有材料的吸水率均未超过0.5%,均能够达到固体浮力材料吸水率不超过2%的一般标准要求。
3.3. 影响复合材料性能的结构因素分析
轻型高分子聚合物EPS颗粒具有闭孔结构,这种闭孔结构使水的渗入极其缓慢,吸水性小,有优良的抗水性。环氧树脂固化体系中活性极大的环氧基、羟基以及醚键、酯键等极性基团赋予环氧固化物极高的粘结强度,再加上它有很高的内聚强度等力学性能,使得它的粘结性能特别强,用做浮力材料的基体,可以与EPS颗粒凹凸表面密实粘结。
EPS颗粒具有规则的球形形貌(如图5,A所示),且粒径分布较小。由于EPS颗粒密度很小,在本实验所选用的复合比的情况下,环氧树脂的实际体积含量为4%~4.8%。所以,将EPS颗粒与环氧树脂充分混合后,实际上是在EPS球形颗粒的表面均匀浸润了一层环氧树脂膜层(如图5,E所示)。在真空压制的过程中,经过间隙气体的排除和EPS颗粒的压缩过程,最终形成了以环氧树脂膜层为骨架的EPS多面体相互嵌合的结构(如图5,F所示)。正是这种特殊的结构,导致了所制备材料性能的一些特殊变化规律。
首先,从实验所制备的复合材料密度可以发现,在所有复合比的情况下,试样的实测密度均小于计
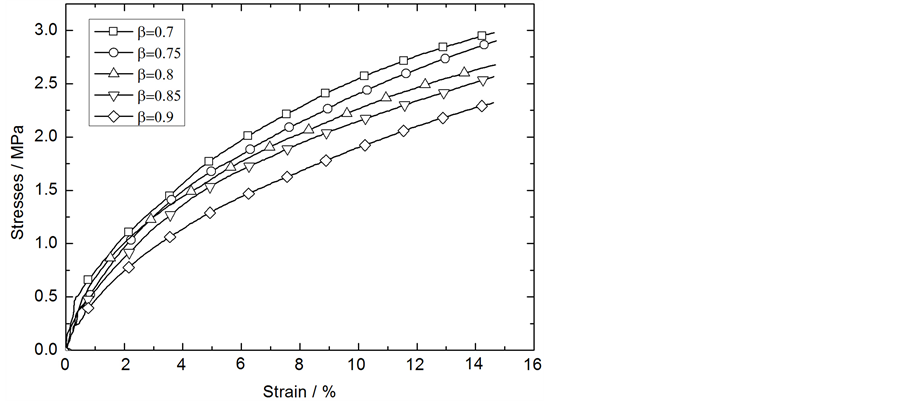
Figure 3. The relationship between the stress and strain of specimens
图3. 材料试样的应力–应变曲线
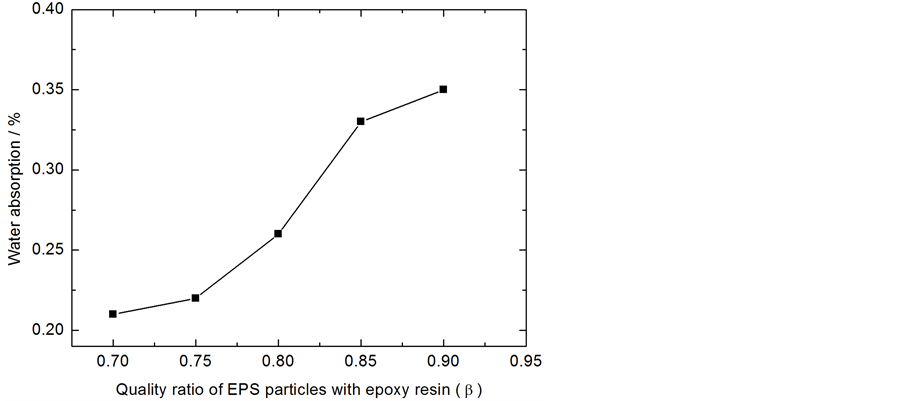
Figure 4. The relationship of the water absorption and composition of specimens
图4. 试样吸水率与组成的关系
算密度(图2)。有研究表明,EPS堆积颗粒在压缩的过程中,包含了堆积间隙气体的排除和SPS颗粒内部气体的排除两部分 [14] 。在本实验材料试样制备过程中,EPS颗粒的表面浸润了一层环氧树脂膜,在加压过程中球形颗粒堆积间隙气体可以正常排除,然而,在压缩后期由于具有较高粘度的环氧树脂膜的封闭作用使EPS颗粒内部气体的排除受阻,部分气体保留在颗粒内部,从而导致了实际试样的密度要低于计算密度。从图2中还可以发现,实测密度与计算密度的差值随着复合比的增加而减小。事实上,复合比的增加,意味着试样中环氧树脂含量的降低。而环氧树脂含量降低就会导致材料中环氧树脂骨架膜层的变薄或不连续。图5中所示的复合比分别为0.7 (图5(B))和0.9 (图5(C))的试样光学显微照片可印证这一点。这一现象降低了环氧树脂膜对EPS颗粒内部气孔的封闭效率,致使EPS颗粒内部的气体部分被挤出,其最终结果就是导致材料的实测密度更接近于计算密度。
其次,从材料的压缩性能(图3)和吸水率(图4)方面不难发现,在相同的应力作用下,材料的变形率
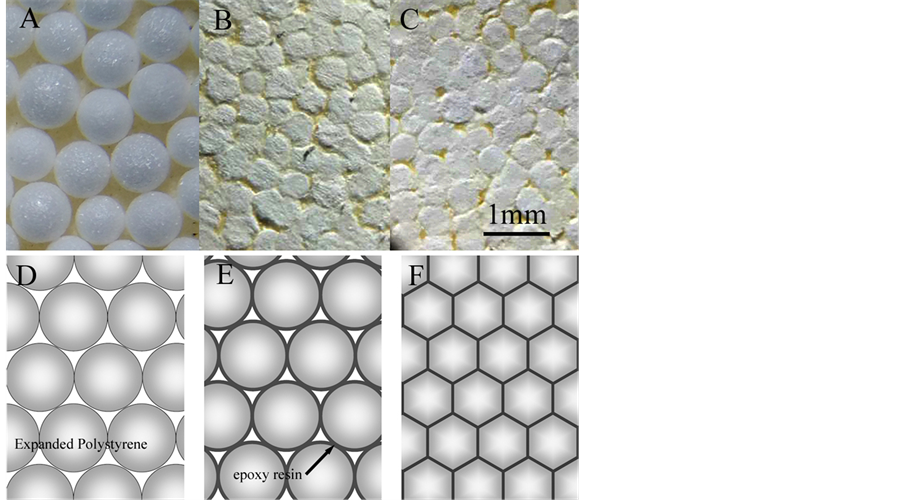
Figure 5. Cutting surface optical micrograph and structure diagram of the specimen
图5. 试样切面的光学显微图片及结构示意图
随着复合比的增加而显著增大,材料在1MPa静水压力下的吸水率也随着复合比的增加而增加。事实上,EPS颗粒是一种多孔聚苯乙烯泡沫材料,其体积密度仅为0.045 g/cm3左右,而聚苯乙烯的真密度为1.05 g/cm3。可以估算,即使将EPS颗粒体积被压缩10倍,其内部的气孔率仍大于50%。所以在本实验的成型压力下,EPS颗粒仍然具有很高的气孔率,其本体仍属于易变形材料。试验所制备的复合材料的强度在很大程度上取决于环氧树脂骨架的强度。随着复合比的增加,材料中环氧树脂骨架膜层变薄,在压应力作用下更易坍塌,从而导致材料的变形率增大。当材料处于静水压下时,也正是由于环氧树脂骨架膜层的变薄,高压水冲破环氧树脂膜层,使易变形的EPS颗粒与环氧树脂膜剥离,并向材料内部渗透。故而,表现出吸水率随着复合比的增加而增大的行为。
营造更多的材料内部气孔,降低材料的密度,从而使材料具有更大的浮力正是浮力材料研究所追求的目标。所以,综合以上分析可以认为,选用高强度的基体材料,适当地增加膜层厚度,充分封闭EPS颗粒的内部气孔应该是进一步改善EPS颗粒/环氧树脂浮力材料性能的有效途径。
4. 结论
1) 采用2 MPa的成形圧力制备了不同复合比的EPS颗粒/环氧树脂复合材料,当复合比在0.75~0.8时,可得到密度为0.3 ± 0.01 g/cm3的复合材料,该材料在1 MPa静水压力下24小时吸水率小于0.3%,变形率小于2%,可作为100 m水深的固体浮力材料使用。
2) EPS颗粒/环氧树脂复合材料的性能与环氧树脂基体材料骨架的结构及性能密切相关,合理选择基体材料,改进骨架结构设计有望得到密度小于0.3 g/cm3,适用于0~300 m水深的固体浮力材料。
致谢
本实验工作得到了国家高技术研究发展计划(863计划)项目(2012AA09A20101)经费的大力支持,在此表示衷心感谢。