1. 引言
硅橡胶是一种兼具无机物和有机物性质的高分子弹性体,具有优异的耐高低温、耐候、耐臭氧、抗电弧、电气绝缘、高透气以及生理惰性等,广泛应用于航空航天、电子、医疗、食品及通讯等领域。虽然普通硅橡胶自身具有一定的阻燃性,但不具有难燃性及自熄性,因而限制了在航空航天、汽车制造、电子电器及对硅橡胶阻燃性要求较高的领域中的应用。因此,研发高阻燃硅橡胶具有重要意义 [1] [2] 。
国内外在硅橡胶阻燃方面虽已做了大量工作 [3] [4] [5] [6] ,但仍存在大量的问题,因此阻燃硅橡胶的研究是一个经久不衰的课题。随着研究的深入,单一阻燃剂的阻燃体系越来越不能满足人们对阻燃硅橡胶性能的要求,协效阻燃体系越来越受到青睐。而随着环保意识的逐渐增强,在新型阻燃剂研究过程中,硅橡胶的阻燃也不例外,无卤化成为其主要的发展趋势 [7] [8] [9] [10] 。
添加型阻燃剂由于工艺简单,效果明显,因此应用很广。其中氢氧化铝在无机添加型阻燃剂中因其价格低廉而应用普遍,但单一使用氢氧化铝阻燃效果较差,所以多与其它阻燃剂复配使用。铂配合物是一种高效阻燃剂,但其价格较贵,使其应用受到限制。因此,本文考虑将氢氧化铝与铂配合物进行协效复配,并和氢氧化铝单一阻燃进行对比,旨在提高硅橡胶阻燃性能的同时,兼顾其成本和阻燃性能。
2. 实验部分
2.1. 实验原料
聚甲基乙烯基硅氧烷:摩尔质量55 × 104~60 × 104 g/mol,乙烯基含量0.18%,扬州晨化新材料股份有限公司;沉淀法白炭黑,氢氧化铝,双二五硫化剂及羟基硅油:皆由扬州晨化新材料股份有限公司提供;铂配合物:自制。
2.2. 主要设备
捏合机,ZH-2,江苏如皋强盛塑料化工机械厂;开炼机,XK-160A,上海第一橡胶机械厂;平板硫化机,QLB-D,上海第一橡胶机械厂;材料拉力机,QJ-210A,上海倾技仪器仪表科技有限公司;硬度计,PHBI-625A,福建泉州试验机厂;厚度计,威海裕福量具有限公司;水平垂直燃烧测定仪,江苏省江宁县分析仪器厂。
2.3. 试样制备
将硅橡胶生胶与白炭黑、氢氧化铝和氯铂酸配合物阻燃剂进行捏合,同时加入羟基硅油、脱模剂等,在真空和加热的条件下进行,然后进行开炼得混炼胶样品。将混炼胶在开炼机包辊,加入硫化机薄通3~5次,出片。接着在平板硫化机上进行硫化成型。一次硫化175℃,5 min;二次硫化200℃,4 h。
2.4. 样品表征
硅橡胶拉伸强度和断裂伸长率:按GB/T5 28-1998测试;撕裂强度:按GB/T 529-1999测试;硬度:按国标邵氏硬度法,GB/T 531-1999测试;燃烧性能:将改性后的硅橡胶切成宽13 mm,厚3 mm的长条状,在静室中将其点燃,记录其从开始燃烧到熄灭的时间,第一次结束后继续进行第二次测试,如此反复测试,每个样品平行测试5个样品取平均值。
3. 结果与讨论
3.1. 氢氧化铝的用量对硅橡胶性能的影响
氢氧化铝的用量对硅橡胶燃烧性能和力学性能的影响见表1。由表可知,随氢氧化铝用量的增大,硅橡胶的燃烧时间明显降低;当氢氧化铝的用量达到60份时,第1次垂直燃烧试验硅橡胶无法点燃,第2次的离焰燃烧时间也仅有1.36秒。但由表1还可见,随氢氧化铝用量的增加,硅橡胶的拉伸强度、断裂伸长率和撕裂强度出现了下降的现象。即单独使用氢氧化铝虽然可明显提高硅橡胶的阻燃性能,但同时会导致硬度增加,力学性能明显下降,性能变差。
3.2. 氢氧化铝/氯铂酸复配对硅橡胶燃烧性能的影响
图1是氢氧化铝不同用量时与氯铂酸复配对硅橡胶燃烧性能的影响。由图1(a)可知,当氢氧化铝用量40%时,添加氯铂酸后,第1次和第2次的燃烧时间明显降低,这说明复配对硅橡胶的阻燃性起到了明显改善作用;由图1(b)可知,氯铂酸添加量10~50 ppm之间时,燃烧时间明显减短,说明氢氧化铝和氯铂酸之间的协同效应明显,继续增大氯铂酸的用量,燃烧时间没有继续降低,反而又出现了增大的现象,这是由于氢氧化铝和氯铂酸的协同效应存在最优配比范围,过多的氯铂酸反而会在硅橡胶燃烧时促进高温氧化反应;由图1(c)可见,氢氧化铝用量60%时,比较空白样品与添加氯铂酸复配样品的第2次燃烧时间可发现,燃烧时间有所减小,但幅度有限,当氯铂酸大于50 ppm后,出现无法点燃的阻燃现象。
3.3. 氢氧化铝/氯铂酸复配对硅橡胶硬度的影响
图2是氢氧化铝/氯铂酸复配对硅橡胶硬度的影响。由图可知,氢氧化铝的添加量越大,硅橡胶的硬度也越高,这是因为氢氧化铝本身作为无机材料对硅橡胶就有增大硬度的作用;此外,对于不同用量氢氧化铝时,氯铂酸用量30 ppm以下,硬度变化不大,超过30 ppm之后,硬度略有增加,这说明阻燃硅橡胶的硬度主要还是受大量添加的氢氧化铝影响。
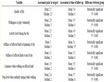
Table 1. Effects of the content of Al(OH)3 on the properties of silicon rubbers
表1. Al(OH)3用量对硅橡胶性能的影响
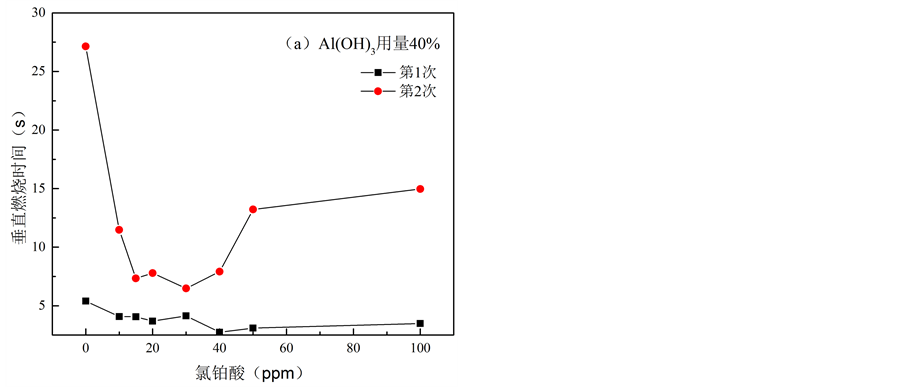
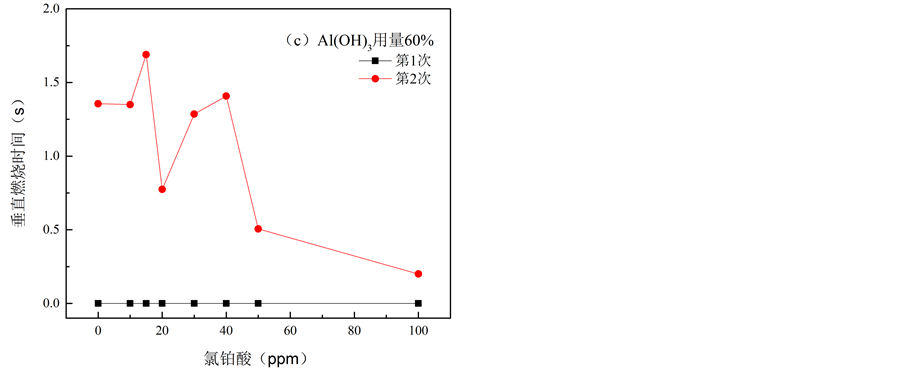
Figure 1. Effects of Al(OH)3/chloroplatinic acid on vertical combustion time
图1. 氢氧化铝/氯铂酸复配对垂直燃烧时间的影响
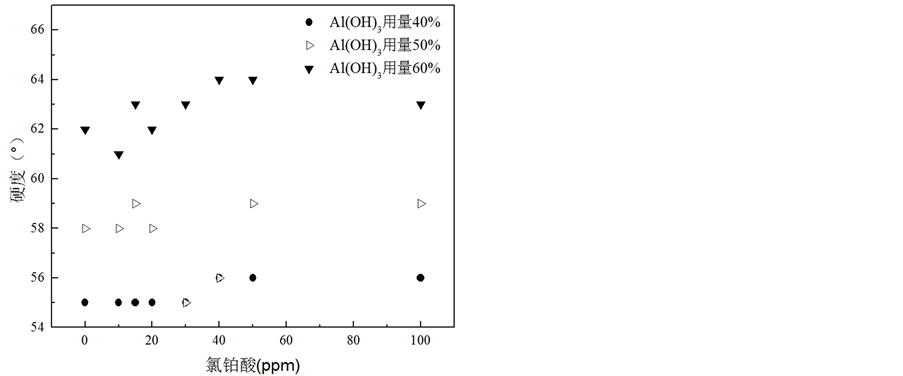
Figure 2. Effects of Al(OH)3/chloroplatinic acid on the hardness of silicone rubber
图2. 氢氧化铝/氯铂酸复配对硅橡胶硬度的影响
3.4. 氢氧化铝/氯铂酸复配对硅橡胶力学性能的影响
图3、图4和图5分别是氢氧化铝和氯铂酸复配对硅橡胶拉伸强度、断裂伸长率和撕裂强度的影响。由图3可知,氢氧化铝用量越大,硅橡胶的拉伸强度反而降低,可见氢氧化铝用量增多反而会对硅橡胶的强度产生不利影响;此外,随氯铂酸用量的增加,氢氧化铝用量50%和60%时,硅橡胶的拉伸强度逐渐增大,说明两者之间的协同效应不仅对阻燃性能有益,对增加硅橡胶的强度也有一定作用。由图4可知,随氢氧化铝和氯铂酸用量的增大,断裂伸长率双向下降,说明这两者之间复配会使硅橡胶的韧性下降。由图5可见,撕裂强度出现了和断裂伸长率一样的变化趋势,这说明在提高硅橡胶阻燃性能的同时,要控制氯铂酸的用量,否则撕裂强度下降过多会影响硅橡胶的使用性能下降。
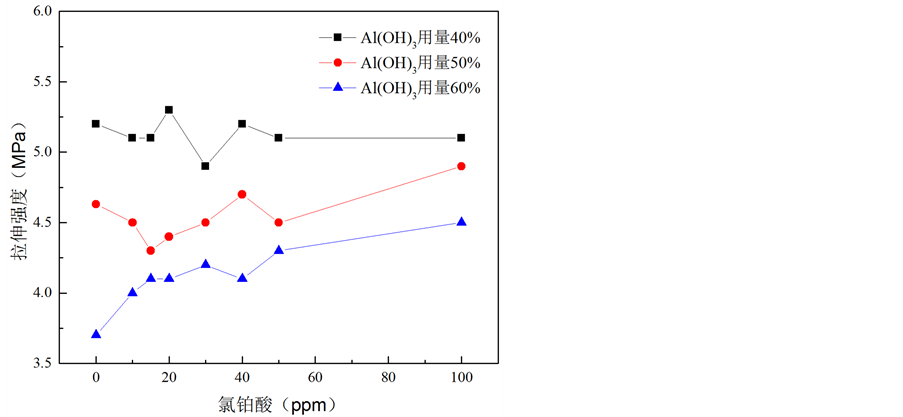
Figure 3. Effects of Al(OH)3/chloroplatinic acid on the tensile strength of silicone rubber
图3. 氢氧化铝/氯铂酸复配对硅橡胶拉伸强度的影响
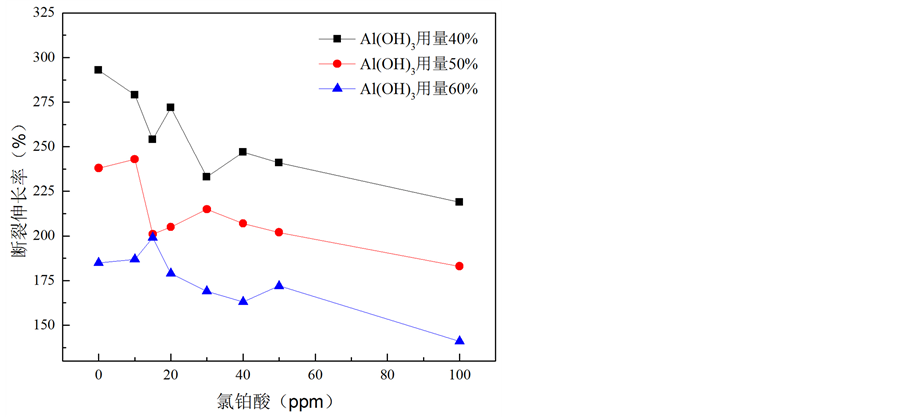
Figure 4. Effects of Al(OH)3/chloroplatinic acid on the elongation at break of silicone rubber
图4. 氢氧化铝/氯铂酸复配对硅橡胶断裂伸长率的影响
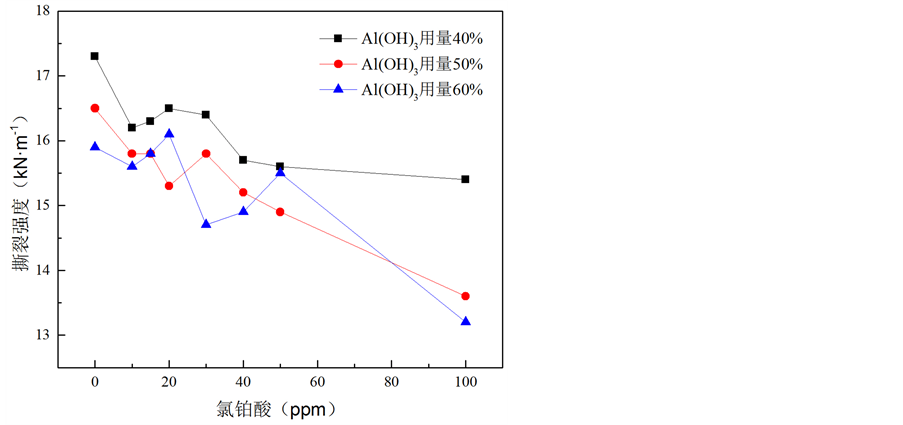
Figure 5. Effects of Al(OH)3/chloroplatinic acid on the tear strength of silicone rubber
图5. 氢氧化铝/氯铂酸复配对硅橡胶撕裂强度的影响
4. 结论
单一使用氢氧化铝可改善硅橡胶的阻燃性能,当氢氧化铝用量为60%时,硅橡胶可实现无法点燃的阻燃等级,但硅橡胶的力学性能明显降低。氢氧化铝和氯铂酸复配协同使用时,氯铂酸添加量不超过50 ppm时可在获得较佳阻燃性能的同时,保持拉伸强度大于4 MPa,而断裂伸长率和撕裂强度分别大于160%和15 kN∙m−1,满足用户的使用需求。
基金项目
本研究得到了江苏省“双创博士”计划和江苏省博士后科研资助计划的支持。
*通讯作者。