1. 引言
航空发动机是在高温、高压、高速旋转条件下长期反复工作的复杂热力机械。它是飞机的“心脏”,在实际工作过程中,各零部件接触表面会相互摩擦,产生很大的摩擦力,造成发动机的内损耗。同时,由于摩擦而产生的大量热会使零件过热,导致发动机不能正常工作甚至零件的损坏。这时,这就需要滑油在相互接触的零件表面形成一层油膜,使摩擦大大降低。
自上世纪70年代以来,金属基、陶瓷基复合材料、工程陶瓷基材料等具有高比强度和耐高温性能的新型材料被研究开发和应用于现代航空发动机。在不断追求高性能的同时,发动机面临的可靠性、经济性以及维修保障等问题也日益突出。20世纪90年代以后,美国国防部在新的国防采办中将“经济可承受性”作为一项重要指标,即由以安全为主要目标向“保障安全性、兼顾经济性”理念转变,在确保安全与装备性能的前提下,降低寿命周期成本。在此背景下,故障预测与健康管理(Prognostics and Health Management, PHM)概念在美国等发达国家得到了长足的发展,在提高复杂系统的安全性和经济可承受性方面具有巨大的应用潜力。在国内,PHM也是当前可靠性领域中极其重要的研究热点 [1] ,特别是航空PHM的各种磨损趋势预测方法的研究,而准确获取系统状态信息是实施PHM的前提条件和基础。某型发动机10年使用情况统计分析表明,发动机空中停车故障的37.5%及导致发动机提前更换的60%以上的原因是由发动机轴承等零部件的磨损类故障引起。磨粒是零部件磨损的直接产物而不是其二次效应,对其进行监测可以反映摩擦副表面磨损状态的严重程度。因此,滑油磨粒监测技术对有效控制发动机磨损类故障风险,保障飞机安全、可靠运行具有重要意义。
本研究通过对航空发动机滑油系统全流量在线磨粒静电监测方法,荷电机理之一摩擦荷电、全流量静电模拟实验等方面的研究现状的综述与分析,指出摩擦荷电、全流量静电监测模拟实验的关键性问题。针对航空发动机实际磨损情况,对航空发动机全流量静电监测模拟实验方法给出合理性的建议,以供后续的研究者参考与借鉴。
2. 研究现状综述
2.1. 国内外现状
基于静电传感技术的航空发动机润滑油路磨粒在线监测始于1997年。英国南安普顿大学Wood教授带领的研究团队进行了一系列的研究,包括润滑条件下静电监测的可行性 [2] 、静电产生机理 [3] [4] 和磨损机理与静电关系等 [3] [5] 的基础性研究,以及在轴承试验台上开展的滚动轴承磨损与静电感应信号对应关系研究 [6] [7] 。而Smiths Aerospace Information Systems公司(其前身为英国Stewart Hughes Ltd.公司,现已被美国GE公司收购)在20世纪末已经将该技术应用于美国联合式战斗机F35 [8] [9] ,增强了航空发动机的故障预测与健康管理能力。目前,此项技术已被美国列为限制出口的军事技术。航空发动机润滑油路磨粒监测静电传感技术主要是基于静电感应的原理对润滑油路带电磨粒进行监测,实现对润滑部件的实时监控。数据表明 [3] [6] ,由于静电监测的对象是润滑部件发生摩擦磨损现象的直接产物,相对于传统的部件振动监测等方法,能够在故障发生的初期就监测到故障信息,可以实时地对润滑部件故障在线监测。同时,润滑油路磨粒监测静电传感技术克服了其他磨粒在线监测方法对微细颗粒不敏感和不能监测非金属颗粒的不足 [9] 。
目前,国内相关技术的研究刚刚起步。关于在线监测的传感器方面,我国科研人员开展一系列研究:西安交通大学谢友柏等设计图像可视在线铁谱传感器,安装用于润滑系统旁路的磨粒在线监测,通过图像处理技术实现对磨粒识别和分析,有效监测齿轮箱磨损故障 [10] ;武汉理工大学严新平等研制了兼有电感传感器检测大金属磨粒与光纤传感器可测量固体颗粒污染物作用的组合测量传感器,在船舶舵浆装置在线监测中取得一定效果 [11] ;军械工程学院张英堂等研制电感式磨粒传感器在循环油路中监测到大于100 μm铁磨粒和大于500 μm的铜磨粒 [12] ;国防科技大学杨拥民等设计电容传感器用于检测柴油发动机油液老化或被污染时引起介电常数变化 [13] ;中国矿业大学孟国营等采用光学法设计油液污染度传感器用于煤矿井下重载齿轮油在线监测 [14] 。同时,冒慧杰等也研究了静电传感器对滑油系统磨粒电量测量方法的研究,提出了通过信号脉冲宽度来获得磨粒的径向位置,再根据径向灵敏度分布来准确获得磨粒电荷量大小的测量方法 [15] ;殷逸冰等研究了被测物带电量、被测物运动速度、被测物在空间模型中所处径向坐标位置是3个影响传感器输出信号的主要因素 [16] 。根据磨损区域静电感应原理,刘若晨等设计了齿轮和轴承磨区域静电传感器,并搭载160 Km∙h−1城际列车齿轮箱,进行了齿轮箱跑合、负荷疲劳和噪音试验 [17] 。李鑫等搭建了可用于齿轮箱地面试车磨损状态监控的滑油静电监测系统,通过连续加载试验和加速寿命试验,证明了静电监测方法用于齿轮箱磨损状态监测的可行性和有效性 [18] 。
在国外,应用最广泛的是加拿大GasTOPS [19] 公司生产的MetalSCAN在线油液监测传感器,它能够全流量在线监测铁磁颗粒,提供被监测颗粒的尺寸范围,颗粒的总质量,超过限度报警等功能,并且已在管道天然气压缩机组、发电厂、海洋推进发动机行列等工业得到了应用。
关于静电信号的去噪处理方面:噪声主要来自测试系统内部与测试系统外部两个方面,系统内部噪声包括检测电路、测试系统以及信号传输过程中引入的噪声,系统外部噪声包括各种外界因素带来的噪声,例如工频干扰,电磁感应耦合,以及接地不当引入的干扰等等。如何从噪声中检测出最微弱的颗粒信号以便及时地对部件的早期故障采取措施;如何消除由于传感器安装位置的振动而引起的虚假信号以便作出正确的维修决策,是静电监测的重要研究内容之一 [20] 。静电监测传感器所能识别的磨粒的大小很大程度上受背景噪声的制约,而消除虚假信号的难点在于该信号与磨粒产生的静电感应信号具有相似性。所以由于静电感应噪声干扰类型多样,很难采取单一方法有效抑制噪声。张营提出一种基于谱插值和奇异值差分谱的联合去噪方法 [21] ,实验验证结果表明,该方法相比独立分量等方法更适用于在线学习,相比小波去噪和 EMD 去除获得更好的去噪效果,能够有效提高静电监测技术的早期故障识别能力。文振华研究了中值滤波与基于Birge-Massart策略的小波分层阈值滤波方法相结合的滤波方法,取得了较好的效果。此外,文振华研究了基于独立分量分析的静电监测信号降噪方法,提出了采用经验模态分解的方法构造与原始信号中噪声总体相近的参考噪声信号,解决了基于ICA降噪过程中出现的欠定问题。最终,表明了研究的两种降噪方法均能有效地提高监测信号的信噪比 [22] 。黄文杰针对采集信号中含有的工频及
其谐波干扰与振动伪信号,采用梳状滤波器去除工频及其谐波干扰,并提出了基于静态离散小波变换与峭度相结合的方法去除振动伪信号,提高分辨磨粒静电感应信号的能力 [23] 。为了消除信号中的工频噪声干扰,李耀华研究了基于陷波器法、自适应滤波法和独立分量分析法进行去工频干扰的方法,最终通过对比分析发现基于独立成份分析的工频干扰消除方法最为有效,并且能够很好的保留其他频谱分量 [20] 。陈志雄采用基于EMD的小波阈值降噪方法对静电信号进行处理 [24] 。刘天一将小波去噪方法及HHT谱的去噪方法相结合,设计了小波-HHT谱联合去噪方法,并在处理实际测得的磨损区域静电信号时取得理想的效果 [25] 。唐欣提出了基于小波分解的缺省软阈值降噪方法 [26] 。钱颖雪提出了小波分解与傅里叶变换耦合的滤波法,能够对静电监测信号中的噪声进行有效处理 [27] 。刘鹏鹏提出利用小波-Hilbert变换,对信号进行处理,揭示了各信号在频率分布方面情况,发现在不同工况下信号的能量大小以及能量分布都有较大的变化,其中巡航工况时静电信号的能量有大幅度的下降 [28] 。卞利提出基于Stein无偏似然估计(SURE)的小波软阈值自适应去噪方法,对静电信号进行了滤波处理 [29] 。
目前国内的研究还未见报导能满足用于航空发动机滑油系统机载化要求的监测方法。南京航空航天大学航空安全与保障技术研究所从2007年率先开展了基于静电监测的发动机气路监测技术研究 [30] [31] ,并搭建了发动机气路模拟试验台,初步进行了试车台架试验台 [32] ,随后又试探性地开展了滑油系统磨粒全流量在线静电监测研究 [33] [34] ,在国内外的这些相关研究中有些提到了静电感应机理,少数的研究建立了简单的模型 [35] 。然而,一直缺乏与实际的物理模型相一致的数学模型以及进一步深入研究分析。对于国外研究者而言,可能由于静电监测技术已被列为军事保密技术,所以在学术期刊上没有发表。对于国内研究者,由于缺乏精确的数学模型与具体分析,使得该项技术在国内的研究发展比较慢,严重阻碍了基于静电监测技术的航空发动机状态监测的发展及其在实际中的应用 [19] 。
2.2.全流量在线磨粒静电监测方法
2.2.1. 磨粒荷电机理
油液静电监测与气路静电监测、磨损区域里的静电监测虽同属静电监测,但油液里静电监测显然要比其它两种难一些。原因是油液里的静电颗粒混在浓稠的油液里,而这些油液都是绝缘,使得油液里颗粒的静电信号一般较微弱。而气路静电监测的对象和磨损区域静电监测的对象与静电传感器之间除开空气没别的东西,静电信号强度要强很多 [36] 。同样,润滑条件下摩擦接触的荷电机理也比较复杂,它不像空气介质中的荷电机理,不受油介质影响。在油介质中的荷电机理受润滑剂和接触材料的化学、物理性质,也有接触材料间的摩擦化学改变影响。因此,油介质中的荷电机理是颗粒带电和油介质带电耦合的综合结果。润滑条件下磨粒荷电机理主要是:润滑剂摩擦荷电、摩擦副接触荷电、磨粒形成荷电 [37] 。文献 [38] 阐述了润滑条件下轴承钢-黄铜摩擦副荷电磨粒的产生机理,如图1所示。
颗粒带电量的大小因荷电方法的不同而有很大的差异,在具体实验操作当中,为使不带电的摩擦颗粒人工荷电,并且期望在尽量短的时间内赋予磨粒尽量大的电荷,荷电方法就显得极其重要。文献 [39] 采用了直流电晕荷电方式,如图2所示,通过电晕放电形成离子,这些离子被电场加速而与颗粒碰撞,从而使不带电的颗粒在进入外电场的空间后被荷电。但此方法容易受到高压电极产生的电场的影响,同时颗粒荷电需要在开放空间中进行,还会受到环境的干扰,所以该装置还有待改进。
文献 [40] 和 [41] 阐述了润滑条件下GCr15球试件对旋转GCr15盘试件向上施加载荷形成滑动摩擦副荷电磨粒的产生机理。由于磨粒在强烈的塑性变形过程中形成,同时伴有大量原子键的断裂,引起了基体材料表面与磨粒产生静电荷,磨粒同基体材料分离的越快,磨粒荷电量越多。如图3所示,基体材料表面电荷的重新分配取决于摩擦副材料的物理特性。并且,磨粒在形成过程中,因为表面氧化层具有绝
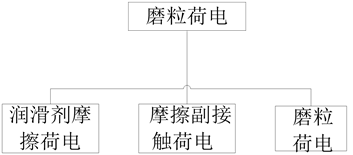
Figure 1. Wear debris charging sources [38]
图1. 磨粒荷电源 [38]
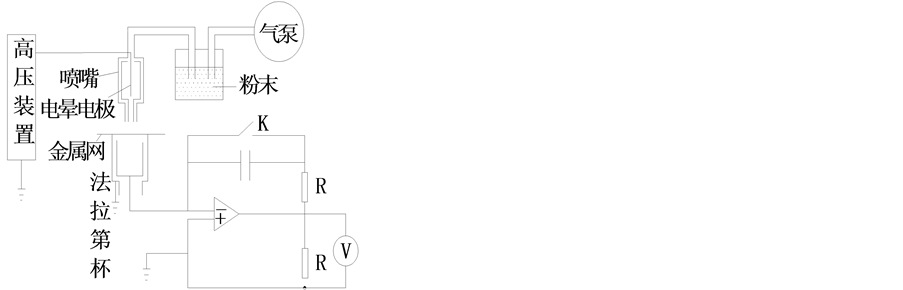
Figure 2. The device for measuring artificial charge of powder particle [39]
图2. 粉状颗料人工荷电测量装置 [39]
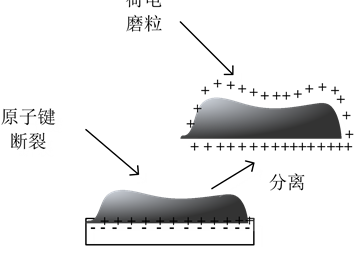
Figure 3. Principle of charged wear debris formed [41]
图3. 荷电磨粒形成原理图 [41]
缘性质,所以磨粒电荷分布取决于润滑油介质的特性。
2.2.2. 荷电磨粒和传感器相互作用的机理
静电传感器的输出信号是荷电磨粒和传感器相互作用的结果。润滑条件下的油路静电监测信号与油路带电以及油液中荷电微粒有关 [40] 。随着油路中的电荷变化,传感器探级表面产生的感应电荷也会发生变化,通过信号调理电路将电荷的变化转为电压信号,通过信号采集卡输入到数据采集以及存储设备。信号调理电路在监测系统中具有重要作用,由于摩擦磨损条件下的荷电量是很微小的,所以用传感器感应的电荷量也是很微小的,因此,需要电荷放大器,文献 [41] 采用了SINOCERA牌电荷放大器YE5854A进行了实验;全流量在线磨粒静电监测系统如图4所示。由于润滑油中所含荷电磨粒在传感器探极表面能够产生感应电荷,并且感应电荷量变化可以形成感应电流信号,故荷电磨粒可以由传感器两个探极感应到,然后通过计算机使用NI Labview编译的信号采集程序可以进行信号的连续采集,再经过信号采集
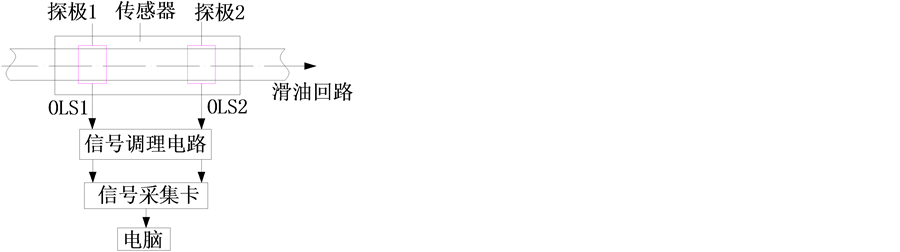
Figure 4. System of oil-line wear debris electrostatic monitoring [41]
图4. 全流量在线磨粒静电监测系统 [41]
卡把感应电流转换为感应电压,同时由于磨粒荷电量极其微小,所以要经过串联的电荷放大器进行电荷放大。故此磨粒的电荷量就可以被成功采集。
文献 [21] 介绍了静电感应信号的特征参数。即全流量静电感应信号RMS值可表示为:

式中:
为取值为1与2,分别代表第一个、第二个静电传感器探极;OLSi(t)是经带通滤波的静电感应电压信号;T是所取时间长度,一般取0.1 s,即每0.1秒长度计算一个RMS值;N为OLSi(t)经离散采样后在T内的采样点数;OLSi(t)为经带通滤波并离散采样后OLS1和OLS2的感应电压信号。
3. 研究现状分析
滑油系统全流量在线磨粒静电监测方法最大的优点在于能够实时、在线监测航空发动机主轴承、直升机齿轮箱的零部件衰退的早期征兆预警。虽然近些年关于滑油系统全流量在线磨粒监测技术方法开展了大量研究,主要的技术有基于磁感应原理Metal-SCAN检测器已在F119发动机上安装使用;基于感应式的定量磨粒监测器(Quantitative Debris Monitor, QDM),已安装用于GE90和GP7200发动机;基于静电油路传感器(Oli-line Sensor, OLS)能监测的最小磨粒尺寸达20 μm,但是,到目前为止,对聚合物材料的磨粒在线监测研究还未见报导。油路磨粒静电监测技术克服了其他磨粒在线监测方法的两个不足:对微细颗粒不敏感;不能对非金属颗粒进行监测。全流量在线磨粒静电监测技术是一种新型的监测技术,该技术基于静电感应原理,对滑油系统主油路中的荷电颗粒经过感应探极所引起感应信号的变化进行监测,从而实现对润滑条件下摩擦副磨损状态的实时监控。由于油路静电监测技术已纳入联合攻击战斗机F-35资助计划,该技术已被美国列为军方保密技术,因此,国内需要开展大量的静电监测研究实验来改善和提高油路静电监测技术以达到世界先进水平。
3.1. 液固两相流荷电装置
目前,滑油系统全流量磨粒在线静电监测模拟实验的关键在于如何使颗粒带电和传感器的优化设计,本文只考虑荷电机理之一摩擦荷电,即当荷电磨粒悬浮在液压油中,油液流动携带荷电磨粒经过传感器探极过程中,荷电磨粒与液压油相界面间自然形成双电层,它们间相对运动发生双电层剪切,由于液压油中基础油是惰性介质,其中添加剂、磨损产生磨粒、氧化物等杂质组成的荷电物种的存在,液压油流过固体表面时,由于流动油液对双电层的剪切作用产生带电现象,使磨粒荷电量发生变化,同时磨粒在流动过程中,磨粒之间、磨粒与管壁之间的碰撞、摩擦、分离引起电荷的转移,导致磨粒累积静电荷。因为在空气中的荷电机理比较单一,当前针对气固两相流系统,颗粒会通过相互摩擦碰撞而荷电的研究已有许多,然而在油液介质中的液固两相流系统的荷电机理因受油介质的影响,它的荷电机理是比较复杂的,影响因素较多而研究也有所限制。D.A.Bograchev分析了管道油流的电化过程,提出管道油流电荷密度的稳态分布 [42] 。Dariusz定量给出了管道油流稳态电荷密度分布规律,李学文研究了有限长管道油流空间电荷密度的暂态过程 [43] ,得出无限长管道油流和有限长管道油流的电荷和电势的分布情况。然而,这仅仅是油液在流动过程中自身与管道的荷电过程,至于油液与管道中各种磨损颗粒之间的荷电规律目前还有待进一步深究。
在具体的实验操作中摩擦荷电方法是目前颗粒注入模拟实验中常用的一种简单可行的荷电方法,人工也可以完成操作,如人工搅拌。但是,人工操作的摩擦荷电的误差性较大,如搅拌的过程中,搅拌速度并不容易控制,因此它是摩擦荷电机理中的关键问题,对于荷电量与搅拌速度之间的关系也是值得研究和探讨的方向。目前,一种对磨损颗粒进行全自动荷电的装置亟待开发,杜学华等人已申请了一项一种荷电装置及荷电发电方法 [44] 的专利,此荷电装置是将外部起电设备所产生的电荷在导体壳体的外表面形成电场,从而驱动电荷在导线中运动以产生电流。但该装置并不能使磨粒直接荷电,后期还需模拟滑油系统油路管道的正常运作环境,对滑油中各种带电磨粒的电荷情况进行归纳总结。
3.2. 润滑条件下销盘滑动摩擦磨损实验装置以及颗粒注入装置
文献 [41] 中的实验装置如图5所示,装置基于MMW-1A型万能摩擦磨损实验机的销盘摩擦副进行设计和改装而成盘试件(1)通过螺栓安装在旋转盘(10)底部实现旋转运动,球试件(2)通过支撑杆固定在下油槽(5)内由底部弹簧装置向上施加垂直载荷,旋转盘试件(1)和固定球试件(2)构成滑动摩擦副,整个摩擦副由上油槽(4)和下油槽(5)封闭,外接便捷式滑油系统(9),全流量在线磨粒静电传感器(6)安装在紧靠摩擦副下游的主回路上,摩擦力矩传感器(7)、力传感器(8)分别用于测量摩擦副的摩擦力矩和载荷。润滑油(3)采用航空用液压油L-HM46。
润滑条件下销盘滑动摩擦磨损实验旨在研究航空用轴承材料在航空液压油润滑条件下摩擦磨损监测,采用自制的全流量在线磨粒静电传感器安装在销盘摩擦副下游的便捷式滑油系统主油路上以监测磨粒通过传感器信号,同时监测摩擦力矩信号,该实验比较接近发动机磨损的实际过程,能够监测到磨损状态。但是,在润滑状态下的颗粒流速并不能很好的控制。另外,在滑动摩擦副的模拟实验过程中,颗粒的形状是多种多样的,如扁平状、方形、菱形、也有不规则形状等,因此,建议针对同种材料的相同形状不同颗粒大小混合、同种材料的不同形状等情况分别进行单独颗粒注入实验模拟研究分析,滑动摩擦副的模拟实验是多种单一因素耦合的结果。因此,分别将同种材料不同大小混合、同种材料不同形状等情况分别单独进行颗粒注入实验模拟研究是一个值得探讨研究的方向。
文献 [38] 介绍的装置实现了颗粒注入实验,如图6,它结构简单、能够监测到颗粒信号,但是该装置注入实验只进行了黄铜、轴承钢球状颗粒注入实验,没有进一步进行其他形状、多种形状混合注入实验。另外,对于颗粒流速没有很好的控制。因此,在颗粒通过传感器监测时,颗粒数量是随机的,这对于监测航空发动机前期磨损状态存在偏差,因为在航空发动机实际磨损过程中,颗粒的状态多种多样,大小、形状也不同。因此,一种微米级荷电颗粒自动控制装置设计及多种类、形状、大小颗粒注入试验研究的必要性显得尤为重要,如何自动控制颗粒数量、流速也是实验模拟继续深入的关键问题。
以上两种装置均为左洪福教授课题组的研究成果,其建立了磨粒形态学分析方法,从理论角度深入定量地揭示出了机械零件的损伤模式、磨损机理与磨粒形态三者之间的内在关系,开辟了发动机磨损状态监测诊断技术,为航空发动机滑油系统的故障预测打开了一个新的通道。
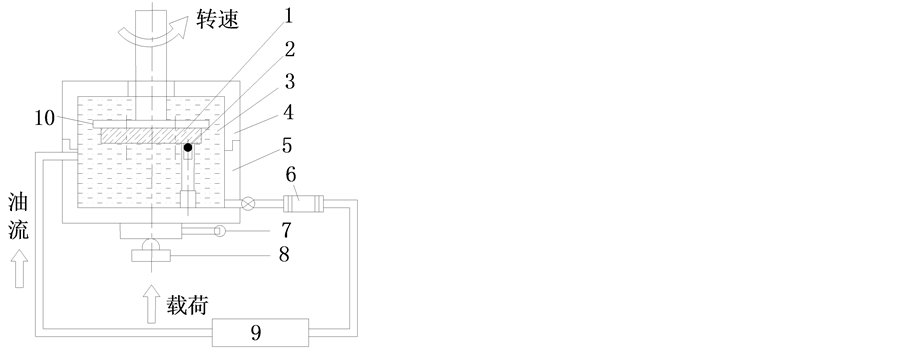
Figure 5. The experimental device for sliding friction and wear of pin plate under lubrication condition [41]
图5. 润滑条件下销盘滑动摩擦磨损实验装置 [41]
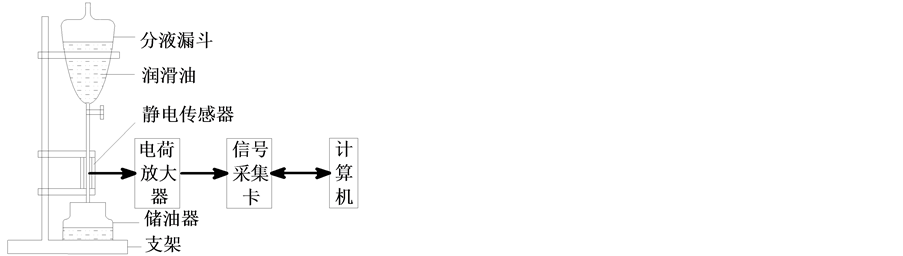
Figure 6. The experimental device for particle injection [38]
图6. 颗粒注入实验装置 [38]
4. 结论与建议
近年来,国内航空发动机滑油系统在线磨粒静电监测技术研究取得了很大进展,进行了不同材料的模拟实验,初步掌握了航空发动机滑油系统全流量磨粒在线静电监测的过程。但是与国外相比,仍然存在很大差距。对在线静电监测模拟实验得到的结论以及提供的建议:
1) 润滑条件下销盘滑动摩擦磨损实验比较接近发动机的实际磨损过程。
2) 滑油系统全流量在线磨粒静电监测方法的关键在于如何使颗粒带电和传感器优化设计。
3) 设计一种自动控制颗粒数量、流速装置是未来研究及探讨方向,它能更好的观察颗粒对应的电荷量,从而更好的判断航空发动机前期磨损状态。
4) 根据航空发动机的实际磨损过程,同种材料的相同形状不同大小混合、同种材料的不同形状颗粒模拟实验研究也是值得深入以及探讨的方向,以便获得更接近于航空发动机实际磨损状态下的前期预兆。
基金项目
国家自然科学基金(51465047);航空科学基金(2014ZD56009);江西省研究生创新专项基金(YC2015- S327)。