1. 引言
艉锚绞车是为特种船舶配套的重要甲板设备,除具有一般的锚泊功能之外,在特定工况下,还须与螺旋桨协调配合,实现船舶牵引后退功能,现大量使用在挖泥船、拖网渔船、登陆艇等船型上。
2. 艉锚绞车工况特点分析
以登陆艇退滩作业为例,需主机倒车与艉锚绞车起锚协调配合,为船舶提供一定的反向作业力方可实现退滩。为了保证船舶能够安全准确后退,艉锚绞车一般设置低、中、高三档速度,低速工况收锚时要求艉锚机具有相当吨位的拉力,随着船舶后退速度的加快,为了防止锚缆与螺旋桨、艉轴、舵叶、人字架绞绕在一起 [1] ,又要求艉锚绞车能够以较高的绳速快速收锚,即:需同时满足拉力和绳速要求。
3. 研究方案
3.1. 艉锚机技术现状分析
目前,小型船舶上艉锚绞车多为液压驱动和电力驱动 [2] 。电动锚机多为交流电电制,并配有减速传动装置,以实现若干档速度,具有体积小、重量轻、传动效率高、维护保养简便的特点,但结构相对复杂、扭矩小。液压锚机主要依靠装置来执行和控制动作,其液压能源来自电动机驱动的油泵装置,具有扭矩大、调速性能好的特点,但占有空间大、对管路要求高,维护难度大且能源消耗较高,能源转换由电动机驱动油泵,再由液压油驱动液压马达,经两次能源转换有效利用率低于80% [3] 。
3.2. 总体思路
为解决艉锚绞车使用易“缠摆”现象,结合船舶功能实现需要,笔者通过研究分析电动锚机和液压锚机各自优缺点,论证选用电力驱动方式开展自动艉锚绞车研制。借鉴汽车自动变速齿轮箱基本原理,开展自动调速研究,以发挥电动锚机体积小、重量轻、维护保养简便、能源消耗低的优势。
主要思路如下:在满足高中低三个工况拉力与速度指标的同时,将每一工况速度细分为2档,以形成6个速度区间。利用力矩传感器测量艉缆受力情况,继而通过程序控制使艉锚机按照预先编好的程序自动选择速度区间,实现艉缆收放的自动控制。动力传递顺序为:三速电动机→联轴器→双速齿轮箱→卷筒、较缆筒→起抛锚、收放缆绳。选用船用三速电机和双速齿轮箱配合使用,齿轮输入轴上设置两个不同齿数的小齿轮和双向离合器,由双速离合器带动小齿轮与大齿轮啮合,以实现6速输出。
4. 关键技术
4.1. 减速比的优化选取
由于艉锚绞车研制结合实船需要开展,主要技术指标已定(如表1所示),其计算设计从分析技术指标
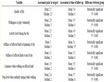
Table 1. List of main technical indexes of stern anchor winch
表1. 艉锚绞车主要技术指标一览表
入手,重点对电动机造型、齿轮箱减速比先取、卷筒设计3方面进行综合考虑 [4] ,权衡利弊。
由于卷筒设计参照标准规范并符合艉锚机总体布置需要即可 [5] ,因此电动机选型与齿轮箱减速比的匹配是实现指标的关键。收放绳速度由3 m/min到80 m/min有近26倍的速度梯增,标准船用三速
4/8/16
极电机速度梯增仅有4倍,单独使用达不到指标要求,需设计2个传动比的齿轮箱,使其速度梯增保持在6倍左右。
按照常规齿轮传动转速转速逐级递减的设计思路,电机需选用2/8/16非标准电极电机(功率:16/11/11 KW,转速:2850/669/307 r/min)与齿轮箱减速比i1 = 172.9、i2 = 63.35进行匹配以实现指标要求,但高速工况转速高、工作电流偏大、齿轮噪音明显,性能不稳定。为达到项目预期,经多角度权衡利弊,将原逐级减速的减速比设计方向调整为先增速后减速的设计思路,电机转速由原2850/669/307 r/min下调为1420/715/320 r/min,电机级数由2/8/16变更为4/8/16,齿轮箱减速比变更为i1 = 172.89、i2 = 32.09。经一系列试验验证,艉锚绞车各功能正常,设备运行平稳,电动机的通用性、稳定性以及与齿轮箱的匹配性较好,实现了艉锚机收放绳速度由3 m/min到80 m/min近26倍的速度梯增。
4.2. 双速齿轮箱研发
双速齿轮箱既要考虑到布局合理和结构紧凑,又要实现2个减速比的自动转换。因此,创新性地将齿轮箱和液压离合器泵站油箱合二为一,将减速箱的输入轴与液压离合器合二为一,以满足功能和总布置所需。将液压离合器嵌入到输入轴内,通过液压离合器选择啮合齿轮,以获得两个传动比。根据齿轮箱布置实际,将狭长的液压离合器液压泵站油箱设置在齿轮箱输出轴右侧,既保证了液压油循环,又带动了减速箱内的散热,有利用齿轮使用寿命和齿轮箱内的轴承使用效果 [6] 。
齿轮箱设计为三级传动,输入轴上设置两个齿轮,传动轴上设置三个齿轮,输出轴设置一个大齿轮,其中:传动轴上两个齿轮与输入轴上两齿轮啮合,另一个齿轮仅与输出轴上大齿轮啮合。充分发挥滑动轴承承载能力大、滚动轴承承传效果好的特点,在高速输入轴上设置滚珠球轴承,在传动轴上设置圆柱滚子轴承,在低速输出轴上设置滑动轴承。
为了实现自动变速功能,参照汽车自动变速箱原理研发了新型多片液压磨擦式离合器,如图1所示。
摩擦片相互挤压带动齿轮组工作,以实现动态离合,结构小巧、布置紧凑、可大扭矩传递,具体如下:液压摩擦式离合器主要由主轴、摩擦片、活塞组成,换向由三位四通电磁阀完成。摩擦片分为2组,每组为6对,每对摩擦片由动摩擦片和静摩擦片组成。动摩擦片套装在主轴上,通过花键与主轴链接并与其共转,与齿轮不直接接触。静摩擦片直接套装在齿轮上并与其保持共转。借鉴双面柱塞式油缸工作原理,输入轴为活塞,轴向不可移动,缸套可左右移动 [7] ,动摩擦片与静摩擦片间通过缸套的轴向移动来完成压紧和脱开动作。输入端的前端镶入液压“端盘”轴承内,后端镶入液压“尾盘”轴承内。压力的传递及切换通过液压“尾盘”上的液压工作口“A”“B”来完成。当A口进油,油腔轴向上移动,挤压摩擦片从而带动齿轮1运转,实现一种传动比。当需转换传动时,A口泄油,B口进油,油腔轴向向
下移动,挤压摩擦片从而带动齿轮2运转,实现另一种传动比。由于力矩传动由油腔内液压油充、泄以 带动动摩擦片挤压静摩擦片来完成,有效解决了齿轮直接接触导致的换档冲击问题,为自动变速奠定了 基础。同时,液压油进入油腔后,其压力逐步增大到额定值,实现了离合器的稳定啮合。
4.3. 自动控制系统研发
双速齿轮箱的设计实现了机械上的自动变速,但如何将机械的自动变速与实际工况紧密相连,还需配置自动控制系统。控制系统研发采用现有成熟的信号采集、PLC微电脑控制、电液一体化三大核心技术来完成。如图2所示,信号采集系统通过安装在导缆轮上的压力传感器将缆绳的力矩信号转变成标准的工业模拟量信号,传递给PLC。PLC将更具预先编好的程序,进行逻辑判断,输出控制信号。电液一体化控制将PLC发出的电信号通过电磁阀控制油路切换,进而控制液压离合器动作,实现动态离合。同时,PLC直接将电信号传递给控制回路,控制电机极数切换,进而改变电机速度,并通过与双速齿轮箱匹配,实现6个速度的自动切换 [8] ,从而达到自动控制。艉锚绞车具体运行流程如图3所示。
为保证控制系统稳定,一方面要考虑电机运行时的惯性,在电机运转速度转换时设置延时过渡,避免了电机在换速瞬间失电现象的发生。另一方面要充分考虑档位转换的工作特性,即力矩信号往返波动,为传感器在各段速临界点附近预留充分的叠加空间,使艉锚绞车在叠加空间范围内不进行档位转换,避免在临界状态频繁换档,对设备造成危害。
5. 结论
自动变速艉锚绞车是将汽车行业摩擦式离合器原理应用于船舶甲板机械设备的一种新尝试,该装备构思新颖、技术成熟、自动化程度高,具有体积小、重量轻、维护保养简便的特点,可大量应用于挖泥船、拖网渔船、登陆艇等特种船型上。同时,定速电机与双减速比齿轮箱匹配设计方案拓展了设备速度
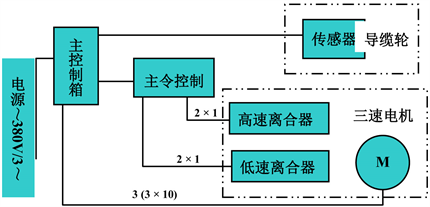
Figure 2. Electrical system diagram of stern anchor winch
图2. 艉锚绞车电气系统图
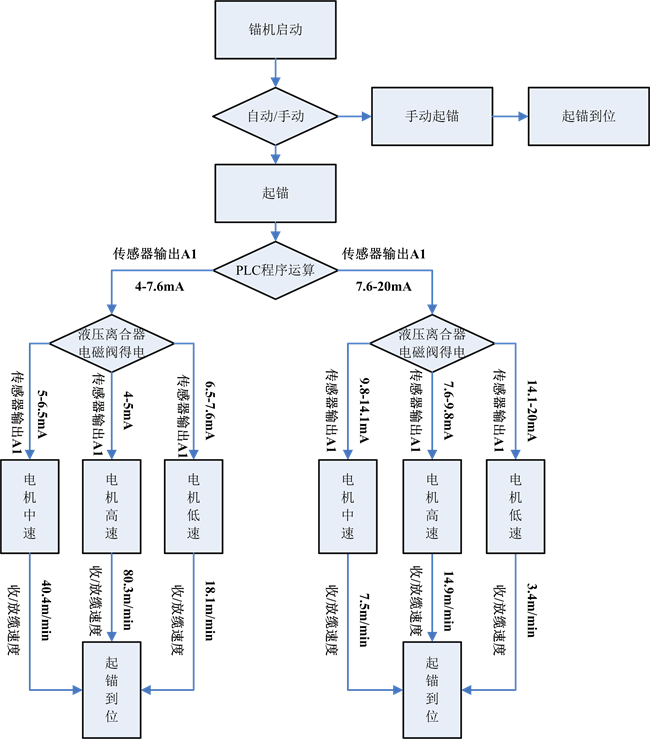
Figure 3. Working flow chart of stern anchor winch
图3. 艉锚绞车运行流程图
调节范围,扩大了定速电机应用领域,可为船舶行业相关甲板设备研制生产提供参考和借鉴。