1. 引言
激光抛光作为一种非接触加工的新型加工技术,有传统抛光技术无法比拟的优点,近年来被广泛的应用于航空、医疗等领域。随着激光技术的发展,很多研究学者对激光复合抛光进行了研究,主要针对不同类型激光器与化学液、电化学、超声等方法的加工进行分析 [1] 。
自20世纪90年代以来国内外许多专家学者已经对金刚石薄膜、高分子聚合、陶瓷、半导体、光学元件等材料进行了大量抛光实验研究 [2] 。Ranoz [3] 等采用Nd:YAG激光和CO2激光将金属表面粗糙度Ra由7.0 μm~9.0 μm降到1.4 μm~2.1 μm。Temmler [4] 等考察了连续激光和脉冲激光扫描速度和功率对粗糙度减少量的影响,使粗糙度降低了60%左右。经国内外实验研究发现,在空气中,采用脉冲宽度较小的激光器抛光金属材料时可得到较低的粗糙度和较好的表面质量,但使用红外激光器抛光对材料的热作用更明显,只能用于粗抛光 [5] 。研究表明,采用静态溶液辅助激光抛光的方法可以减少红外激光器抛光时的热作用,在激光抛光中辅以化学液的化学效应和冷却效应,可以达到更好的抛光效果。因此,本文提出了静态溶液辅助激光抛光医用不锈钢的实验研究,进一步探索不同影响因素对其抛光效果的影响规律,从而对参数进行优化,进一步提高抛光效果。
抛光效果主要以抛光后材料的表面质量作为重要的评判指标,因此,选择抛光的工艺参数非常重要。实验采用日本统计学专家田口玄一(Genichi Taguchi)创立了基于正交实验的“田口方法(Taguchi methods)”,通过较少的实验量进行完整的参数研究,引入信噪比(signal to noise ratio,简写为S/N)降低不可控制因素对实验的影响 [6] [7] 。该方法近年来在航空、环境、矿业、机械工程等领域得到广泛应用 [8] 。
本文利用田口正交实验法设计实验方案,通过对实验结果进行分析,研究影响静态溶液辅助激光抛光抛光效果的主要因素,并对实验结果进行优化。
2. 光纤脉冲激光不锈钢表面作用
静态溶液辅助激光抛光是利用脉冲激光聚焦到溶液中的金属表面,在金属与溶液的交界面产生热–力学效应使材料表面发生变形,同时结合溶液的冷却和热化学作用,使金属表面平整。
2.1. 热效应和力效应分析
当高能量、短脉冲激光透过溶液后聚焦到金属表面时,溶液与金属的交界面上,激光被吸收的功率密度分别造成了金属材料和溶液的升温,应该包括金属和溶液两个方面,即:
(1)
其中:Im为金属材料吸收的激光功率密度部分,Il为溶液吸收的激光功率密度部分 [9] 。
对于激光照射溶液与材料界面温度分布可认为:1) 由于纳秒脉冲激光的热渗透深度很小,激光光斑中心处的热传导遵循一维模型;2) 波长在红外波段的激光在溶液中的传输衰减主要以吸收为主(λ = 1064 nm),在分析纯试剂配置的溶液中溶液浓度对激光衰减影响微弱,衰减特性与纯水相当 [10] 。由于覆盖在材料表面的溶液厚度只有3 mm,可忽略溶液对激光吸收的能量损失。3) 固液交界面处溶液和金属的温度相同 [11] 。
由于激光能量在空间上为高斯分布,时间上为矩形脉冲,因此激光辐照部位的温度为:
(2)
(3)
其中:ton为激光脉冲宽度脉冲;A为材料表面吸收率;λm为金属的热导率 [12] 。
根据上式可得到金属表面温度随时间的变化规律,其温度在激光辐照的纳秒脉冲内急剧升温,当脉冲能量结束后又快速下降,到几百度后下降速度逐渐变慢。由于激光的高能量密度、高升温率的作用特点(其热流密度高达MW/m2量级,温度变化107 K/s以上),导致近金属表面的溶液温度过热,瞬间产生气泡并沸腾,又称快速瞬态核化沸腾 [11] 。
激光透过溶液在聚焦区域内生成等离子体,由于液体的不可压缩性,在溶液与金属界面上膨胀的等离子体受到液体的限制,对金属表现出明显的冲击波力学效应,对金属表面材料进行去除。
2.2. 溶液化学效应分析
试件浸在较低浓度的H2SO4溶液中,当激光透过化学液聚焦到试件表面时,激光照射的光斑区域钝化膜被去除,露出基体部分在光化学和热化学作用下发生反应,而其他没有被激光照射的区域则在钝化膜的作用下不会发生化学反应。
3. 实验条件及实验方法
实验主要从激光器参数对加工后效果进行评估,将抛光后试件表面粗糙度作为实验指标。本文采用型号DSX-510 Olympus显微镜对试件表面形貌进行观察,并测量表面粗糙度,基于Origin、Minitab等软件对数据进行处理,分析影响抛光效果的主要因素及其影响规律。
3.1. 实验条件
实验中采用卡本特公司生产的Custom455不锈钢,该材料为马氏体时效硬化不锈钢,由于其有较高的强度和耐腐蚀性,常被用于医疗、船舶、航天等方面,材料化学成分如表1所示。相较于陶瓷材料,不锈钢导热性好,熔点高,其热物理性能参数如表2所示。
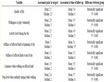
Table 1. Chemical composition of stainless steel custom 455 (wt%)
表1. Custom 455不锈钢化学成分(质量分数,%)
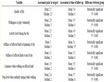
Table 2. Thermal physical parameters of custom 455 stainless steel
表2. Custom 455不锈钢热物理参数
实验中采用的激光设备为IPG光纤激光器,如图1。激光通过扫描振镜、溶液将光斑聚焦到试件表面,利用激光对材料的热作用进行加工。激光器脉宽为100 ns,波长为1064 nm,平均功率200 W,重复频率为200 kHz。相较于传统的Nd:YAG激光器,光纤激光器在功率改变时,无论是平顶模式还是高斯模式,光斑直径始终保持稳定如一。同时,脉冲频率更高,参数的实时调节性能也更强 [13] 。
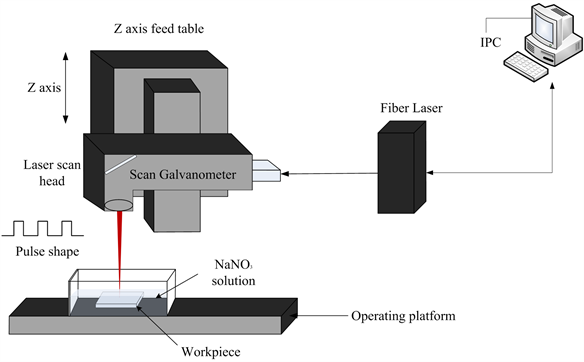
Figure 1. Static solution assisted laser polishing experimental platform
图1. 静态溶液辅助激光抛光实验平台
实验具体参数设定如表3所示,H2SO4溶液浓度为8%,液面到材料表面高度2 mm,加工试件处于焦点位置,抛光尺寸为3.0 mm × 3.0 mm。
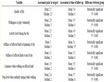
Table 3. Orthogonal experiments plan
表3. 正交实验方案
试件I、试件II实验前表面用抛光机抛光,之后用激光器对试件表面粗加工,之后放入酒精中超声清洗15 min、吹干,除去表面油污等杂质。图2所示激光粗加工后的试件表面形貌,图2(a)为粗糙度Ra为0.513 μm时表面形貌,图2(b)为粗糙度Ra为1.832 μm时表面形貌。
(a) Ra = 0.513 μm
(b) Ra = 1.832 μm
Figure 2. Surface topography of specimen after laser rough machining; (a) Ra = 0.513 μm, (b) Ra = 1.832 μm
图2. 激光粗加工后试件表面形貌;(a) Ra = 0.513 μm,(b) Ra = 1.832 μm
3.2. 实验方法
对于确定的试件表面,影响抛光效果的因素有激光脉冲能量、扫描间隔以及扫描次数,影响脉冲能量的参数是平均功率、扫描速度、离焦量。在激光能量与脉冲宽度不变时,激光扫描速度和重复频率决定了材料表面单位面积单位时间平均吸收的光能,影响抛光效果 [6] 。当激光扫描速度低于5 mm/s时,激光对金属没有抛光作用,反而使金属表面粗糙度升高,表面烧灼作用明显。当扫描速度过高时,几乎没有抛光效果。激光的平均功率过低或过高时,激光和化学对金属材料的作用不明显或过分烧灼。
本实验采用田口正交试验的方法进行实验研究,设计L9(34)四因素三水平正交表,实验结果如表4所示。实验时未考虑各因素的交互作用。
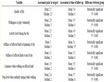
Table 4. L9(34) Orthogonal experimental arrangements and results
表4. L9(34)正交实验安排和实验结果
4. 结果与讨论
4.1. 信噪比与均值分析
信噪比(Signal-to-noise ratio)特征函数可分为望大特性、望小特性和望目特性。在本实验研究中,粗糙度越小,表面点蚀和熔渣越少,抛光效果越好,因此试验中采用望小特性,其信噪比为:
(4)
式中:n为重复次数(n = 3);yi为实验的表面粗糙度。平均响应值的计算公式 [14] 为:
(5)
用Minitab对表4实验结果进行分析处理,抛光后表面粗糙度信噪比(S/N)与平均响应值见图3,当原始表面粗糙度低时(I),扫描间距对表面粗糙度影响最明显;当原始表面粗糙度高时(II),扫描速度对表面粗糙度影响最明显。根据田口正交分析,信噪比越高,输出的性能评价指标越优。
(a) Signal-to-noise ratio of each factor level (I)
(b) Signal-to-noise ratio of each factor level (II)
(c) Mean response of each factor level (I)
(d) Mean response of each factor level (II)
Figure 3. Signal-to-noise ratio and mean response of different original roughness; (a) Signal-to-noise ratio of each factor level (I), (b) Signal-to-noise ratio of each factor level (II), (c) Mean response of each factor level (I), (d) Mean response of each factor level (II)
图3. 不同原始表面的粗糙度与均值响应;(a) 各因素水平信噪比(I),(b) 各因素水平信噪比(II),(c) 各因素水平均值响应(I),(d) 各因素水平均值响应(II)
利用直观分析法,根据表4得出的信噪比和平均响应的分析法见表5、表6。对于试件I,初始表面粗糙度低为0.513 μm,静态溶液辅助激光对试件表面抛光只能降低0.2 μm左右,对实验结果影响的主次顺序为扫描间隔 > 扫描速度 > 平均功率 > 扫描次数,各水平的最佳组合为B1A1C3D2;对于试件II抛光后表面粗糙度最高降低70%左右,对实验结果影响的主次顺序为扫描速度 > 扫描次数 > 平均功率 > 扫描间隔,各水平的最佳组合为A3D3C3B2。
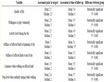
Table 5. Signal-to-noise ratio and mean response (I)
表5. 信噪比与均值响应(I)
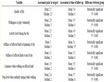
Table 6. Signal-to-noise ratio and mean response (II)
表6. 信噪比与均值响应(II)
4.2. 方差分析
根据直观分析法得出最优加工参数,但是无法分析导致实验结果存在差异的原因。由于实验重复次数低,用Minitab方差分析实验结果时将影响最小的因素作为误差项,试件I、II方差分析结果见表7、表8。在显著性水平为0.1时,P的值小于0.1时,扫描间隔对响应有显著影响,如表7,分析其原因可知,当能量过大;在显著性水平为0.01时,P的值小于0.01时,扫描速度对响应有显著影响,如表8。分析其变化原因可知,当抛光速度较小或扫描间隔过小时,激光扫描线重叠率过高,能量累积严重,对不锈钢表面造成烧蚀严重;而当扫描速度过大或扫描间隔过大时,激光能量累积不足,反而使抛光效果降低。
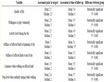
Table 7. Variance analysis table of surface roughness (I)
表7. 表面粗糙度方差分析表(I)
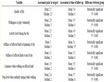
Table 8. Variance analysis table of surface roughness (II)
表8. 表面粗糙度方差分析表(II)
4.3. 最优参数的预测与验证
根据对信噪比和均值响应分析,当原始表面粗糙度低时,抛光只能降低。对于试件II,
(6)
其中,
——最优条件下的信噪比;
——A因素3水平下的信噪比;
——B因素3水平下的信噪比;
——C因素3水平下的信噪比;
——D因素3水平下的信噪比;
——测得的9组信噪比的数据均值 [13] 。
通过计算最终求得:
。
根据望小特性,计算公式(6)预测最优条件下的粗糙度为0.578 μm。通过实验验证,不锈钢原始表面粗糙度为1.832 μm,在A3B2C3D3条件下测得0.510 μm。最优条件下抛光前后表面形貌见图4。
(a) 抛光前表面形貌
(b) 抛光后表面形貌
Figure 4. Surface topography before and after polishing under the optimal conditions
图4. 最优条件下抛光前后表面形貌图
5. 结论
1) 静态溶液辅助激光抛光效果与原始表面形貌有关,当原始表面粗糙度低时,实验参数对抛光效果影响不大;当原始表面粗糙度高时,抛光效果明显;
2) 原始表面粗糙度高时,通过对信噪比响应和方差分析,得出扫描速度对表面粗糙度影响最大,其次是扫描次数、平均功率和扫描间隔;
3) 当扫描速度为11 mm/s,扫描次数为6次,平均功率为12 W,扫描间隔为0.1 mm时,可使表面粗糙度降到0.51 μm,得到更好加工效果。
NOTES
*通讯作者。