1. 引言
铝硅系合金具有低密度、高比强度、良好的铸造性能等优异性能,在航空航天、汽车等领域有着广泛的应用,如发动机缸盖、进气歧管、轮毂、活塞等。在汽车工业中,铝硅系合金可作为钢铁材料的替代,在相同强度下,质量更轻,燃料消耗更少 [1] [2] [3] 。然而,传统铸造、锻造方法成形的制件疏松,生产周期长,成型复杂形状困难,材料利用率低 [4] [5] 。
选区激光熔化技术(Selective laser melting, SLM)是一种新型的增材制造技术,基本原理是根据三维软件制作的零件模型,切片软件切片后通过激光扫描,逐层堆积得到制件 [6] [7] [8] 。SLM可成形出致密度接近100%的制件,易于成形复杂形状制件,具有制件精度高、材料利用率高等优点,使得SLM技术成为铝硅系合金理想的成形工艺 [9] [10] 。
近期,国内外学者对SLM成形AlSi10Mg合金的组织与性能进行了研究。布雷西亚大学的Luca等人发现,SLM成形的AlSi10Mg制件室温抗拉强度、屈服强度和伸长率分别达到452 MPa、264 MPa和8.6%,均显著高于重力铸造AlSi10Mg制件 [11] 。伯明翰大学的Noriko等人发现,随着能量密度的增加,SLM成形的AlSi10Mg制件致密度先上升后下降,在60 J/mm3时达到最高(99.2%) [12] 。山东省科学院的王小军等人发现,粉体颗粒形貌越接近球形,粒径分布越窄,SLM成形的AlSi10Mg制件致密度越高(为98%) [13] 。中北大学的白培康等人发现,合适的热处理(723 K, 1 h)可使SLM成形的AlSi10Mg制件组织、成分更均匀,提高综合力学性能 [14] 。然而,现有的研究中,采用的激光扫描速度通常在2000 mm/s以下 [11] [15] [16] ,成形效率不高,微观组织分析不够充分。为此,本文在极高的扫描速度(3800 mm/s)下SLM制备了AlSi10Mg试样,详细考察了其微观组织与力学性能,为拓宽SLM成形铝合金的应用提供技术支撑。
2. 实验方法
实验采用美国AMA公司生产的AlSi10Mg合金粉末,其名义与实测成分列于表1中。该合金成分靠近共晶成分,热裂纹几率低,铸造和焊接性能优良,且粉末流动性能好,适合SLM成形。该合金粉末呈不规则椭球形,平均粒径为42 μm,90%的粉末粒径集中在20~77 μm之间,呈正态分布(见图1)。粉末粒径分布集中,有利于提高制件致密度。
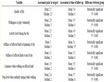
Table 1. Nominal and measured compositions of AlSi10Mg alloy powder (weight percent, wt%)
表1. AlSi10Mg合金粉末的名义和实测成分(质量百分数,wt%)
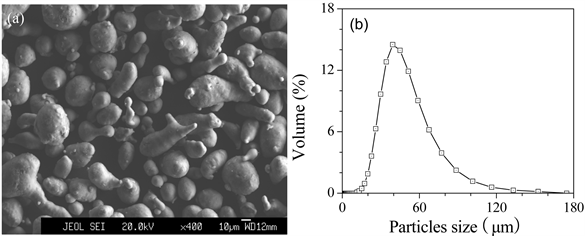
Figure 1. Micro-morphology (a) and particle size distribution (b) of AlSi10Mg alloy powder
图1. AlSi10Mg合金粉末的微观形貌(a)和粒径分布(b)
SLM实验在广东汉邦激光科技有限公司生产的SLM-250型金属SLM设备上进行,其原理如图2所示。打印过程先建立制件三维模型,再用切片软件获得每层平面轮廓模型,铺粉辊将粉末从供粉腔带入
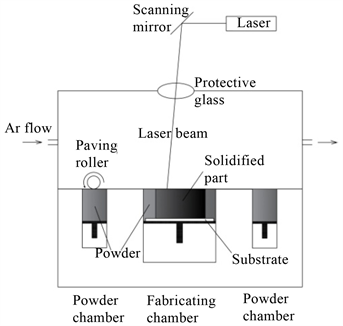
Figure 2. Schematic diagram of SLM equipment
图2. SLM设备的原理示意图
成型腔,激光束根据模型扫描,扫描完成后成型腔下降一个层厚重新铺粉,激光根据下一层模型重新扫描,最终堆积得到制件。为保证打印效果,试验前用酒精擦拭基板、供粉腔、刮板等位置,并充入Ar气保护。
本文采用的SLM工艺参数为:激光功率450 W,扫描速度3800 mm/s,层厚30 mm,扫描间距60 mm,线能量密度65.8 J/mm3。由于扫描速度较快,所以采用较高的激光功率,提高线能量密度,防止粉末热输入量不足熔化不完全造成孔隙、夹渣等缺陷。本文SLM成形了Φ10 mm的金相试样和拉伸试样(见图3)。
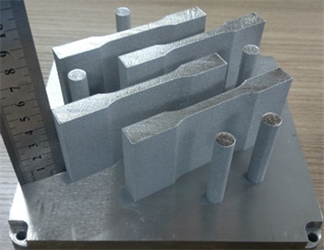
Figure 3. Metallographic and tensile AlSi10Mg sample fabricated by SLM
图3. SLM成形AlSi10Mg金相和拉伸试样
经打磨、抛光后的金相试样用keller试剂(95 mL·H2O + 2.5 mL·HNO3 + 1.5 mL·HCl + 1 mL·HF)浸泡腐蚀15 s后,在Leica DMI 3000M型金相显微镜(OM)和JEOL JXA-8100型扫描电子显微镜(SEM)下观察微观组织。在SmartLab型X射线衍射仪(XRD)上进行物相分析,采用CuKβ靶。在MH-5L型显微硬度测试计上测试硬度,载荷9.8 N,加载15 s。在DNS200型万能材料试验机上进行室温拉伸,拉伸速率为3 mm/s,用SEM观察断口形貌。
3. 结果与讨论
3.1. 微观组织分析
图4为SLM成形的AlSi10Mg制件横截面的OM照片。宏观上,整体由不同方向上平行的条纹构成,尺寸相差不大,宽约100 μm,长约300 μm,条纹间相互搭接,有明显的方向性。这样的条纹是激光扫描粉末熔化后快速凝固形成的,条纹方向和激光扫描方向一致,激光扫描方向改变,则条纹方向改变。
图5为SLM制件横截面的SEM照片。可见,在本文工艺参数下SLM成形的试样无明显空洞或微裂纹等缺陷,说明该工艺参数是合理的。单个条纹中包含了大量细小的晶粒,可以将其分为三个区域:内部细晶区(Inside Fine Grain Zone, FGZ)、热影响区(Heat Affected Zone, HAZ)、边界粗晶区(Boundary Coarse Grain Zone, CGZ)。条纹内部细晶区晶粒大小均匀,晶粒直径集中在300~500 nm,无方向性,呈等轴晶;条纹边界上粗晶区晶粒明显长大,晶粒直径略大于500 nm,宽度较窄,约4~5个晶粒大小,无方向性,呈等轴晶;内部细晶区与边界粗晶区中间有一段过渡热影响区,晶粒被拉长,长度达到2~3 μm,晶粒宽度与内部相当,有向条纹内部生长的趋势,呈柱状晶。由于SLM过程热输入较大,冷却速度较快,晶粒没有足够的时间长大就凝固,导致整体晶粒尺寸较小;边界及热影响区晶粒受到相邻条纹熔化时的热影响,得到的热输入大于内部晶粒,晶粒长大或重熔,所以晶粒尺寸大于内部,晶粒在长大或重熔过程中,向已凝固的金属区域散热比向空气散热快,温度梯度大,所以晶粒有向内生长的趋势。
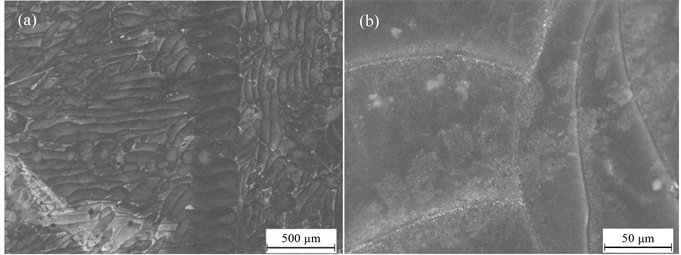
Figure 4. OM graphs of cross section of AlSi10Mg sample fabricated by SLM
图4. SLM成形AlSi10Mg试样横截面的OM照片
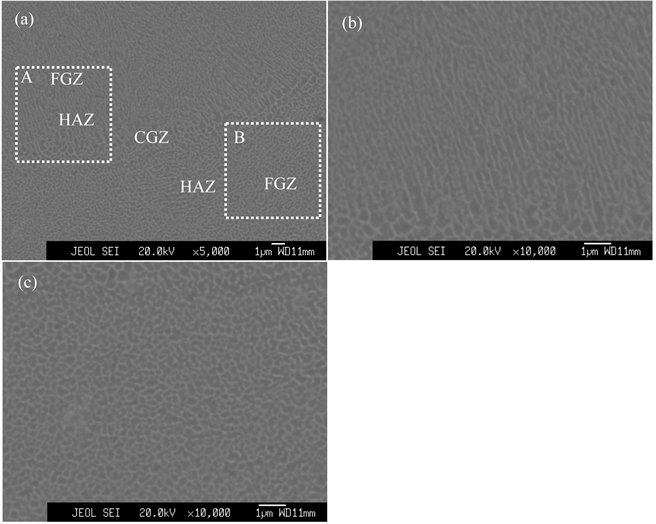
Figure 5. SEM graphs of cross section of AlSi10Mg sample fabricated by SLM: (a) Overall morphology; (b) Magnification of A region; (c) Magnification of B region
图5. SLM成形AlSi10Mg试样横截面的SEM照片:(a) 整体形貌;(b) A区放大;(c) B区放大
图6为SLM制件纵截面的OM照片。可见,纵截面由“U形”条纹构成,大小不均,呈“鱼鳞”状分布,熔池在激光作用下形成,然后快速冷却。熔池呈“U形”是因为U形上部与激光接触,热输入较高,粉末熔化量多,传输到下部能量较上部少,热输入低,粉末融化量少。“U形”条纹之间互相穿插覆盖,呈“鱼鳞状”,说明在激光扫描的过程中,已经凝固的部分又发生过重熔的现象,达到了较好的冶金结合。
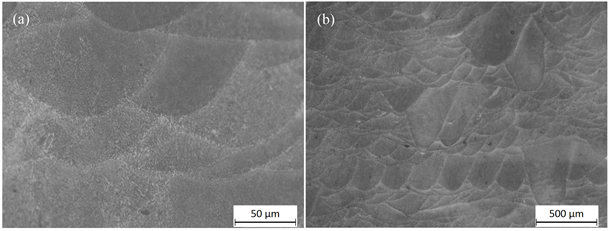
Figure 6. OM graphs of longitudinal section of AlSi10Mg sample fabricated by SLM
图6. SLM成形AlSi10Mg试样纵截面的OM照片
图7为SLM制件纵截面的SEM照片。其显微组织和横截面类似,“U”形条纹也是由无数细小晶粒组成,可以将其分为两个区域:内部等轴晶区(Internal Equiaxed Crystal Zone, ECZ)、边界柱状晶区(Boundary Columnar Crystal Zone, CCZ)。条纹内部等轴区晶粒大小均匀,晶粒直径直径略大于500 nm,与横截面边界粗晶区相当,无明显方向性,呈等轴晶;条纹边界上晶粒变得细长,宽度比条纹内部晶粒略宽,长度分布不均,主要集中在3~4 μm,少数达到10 μm以上,宽度较窄,约10个晶粒大小,有明确的方向性,呈柱状晶。纵截面晶粒形成过程和横截面类似,SLM过程中粉末熔化后快速冷却,导致整体晶粒尺寸不大,条纹边界上受到相邻条纹熔化的影响重熔,冷却时沿散热最快的方向结晶,形成柱状
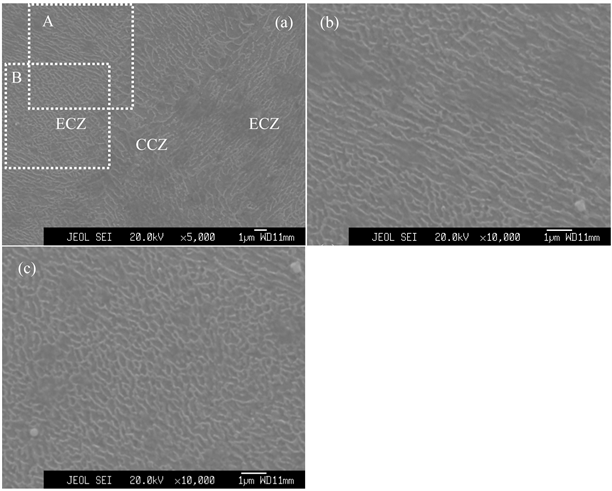
Figure 7. SEM graphs of longitudinal section of AlSi10Mg sample fabricated by SLM: (a) Overall morphology; (b) Magnification of A region; (c) Magnification of B region
图7. SLM成形AlSi10Mg试样纵截面的SEM照片:(a) 整体形貌;(b) A区放大;(c) B区放大
晶。然而,纵截面晶粒整体尺寸大于横截面晶粒,原因是纵截面条纹间搭接率更高,重熔面积大,总的热输入高于于横截面总热输入。
3.2. 物相分析
图8为SLM成形AlSi10Mg试样的XRD谱。可见该试样主要由Al基体和Si相组成,还含有少量的Mg2Si相。谱中得出Al的衍射峰相对于纯Al相产生了向右的偏移,θ值偏大。由布拉格方程:2sinθdhkl = λ(θ为入射角,dhkl为晶面间距,λ为波长),本实验靶材(CuKβ靶)不变,则λ不变,当θ偏大时,dhkl偏小,晶格常数减小,表明Al基体发生了晶格畸变。AlSi10Mg合金主要成分中只有Si原子直径小于Al原子,Si占据了Al基体中原本属于Al原子的位置,导致Al基体的晶格常数减小,形成了固溶置换体。

Figure 8. XRD spectrum of AlSi10Mg sample fabricated by SLM
图8. SLM成形AlSi10Mg试样的XRD谱
3.3. 力学性能分析
SLM成形AlSi10Mg合金横纵截面的显微硬度无明显差异,分别为133 HV和134 HV,远高于传统铸造AlSi10Mg合金(86 HV)。
图9为SLM成形AlSi10Mg试样室温工程应力应变曲线,其拉伸力学性能值列于表2中。可见,在本文工艺参数条件下SLM制备的AlSi10Mg试样呈现优异的综合拉伸力学性能,其抗拉强度、屈服强度和伸长率分别达到470 MPa、327 MPa和8%,远高于铸造AlSi10Mg合金(ISO R2147铸态标准中AlSi10Mg合金最高屈服强度、抗拉强度、伸长率分别为317 MPa、170 MPa和3.5%)。同时也高于部分文献 [12] [15] [16] 提及的SLM成形的AlSi10Mg合金综合拉伸力学性能结果,说明本文采用的工艺参数更佳。此外,SLM扫描速度有明显提升,加工效率更高。
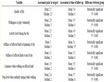
Table 2. Comparison on tensile mechanical properties at ambient temperature of AlSi10Mg samples fabricated by SLM
表2. SLM成形AlSi10Mg试样室温拉伸力学性能对比
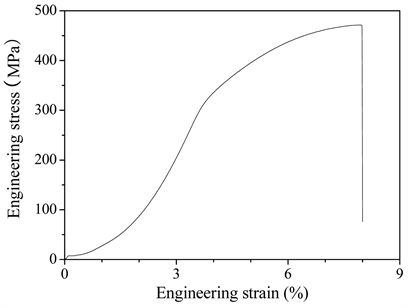
Figure 9. Engineering stress-strain curve at ambient temperature of AlSi10Mg sample fabricated by SLM
图9. SLM成形AlSi10Mg试样室温工程应力应变曲线
综合力学性能的提升主要来源于晶粒细化和固溶强化。SLM成形的AlSi10Mg试样晶粒极细,且组织致密缺陷,大部分晶粒直径在500 nm及以下,远小于铸态晶粒(通常达到100 μm以上),大量的晶界阻碍了位错的运动,加载时可以抵抗更高的应力。横纵截面晶粒尺寸差异不大,所以显微硬度无明显差别。Si原子以置换固溶体的形式存在存在于Al基体中,产生的晶格畸变增加了位错滑移的阻力,从而增强试样强度。
图10为SLM成形的AlSi10Mg试样拉伸断口形貌。拉伸沿着垂直纵截面方向进行。断口几乎观察不到孔洞,呈蜂窝状,具有大量韧窝结构,为韧性断裂。试样致密度较高,缺陷少,几乎观察不到气孔、微裂纹等缺陷,裂纹源少不易启裂。
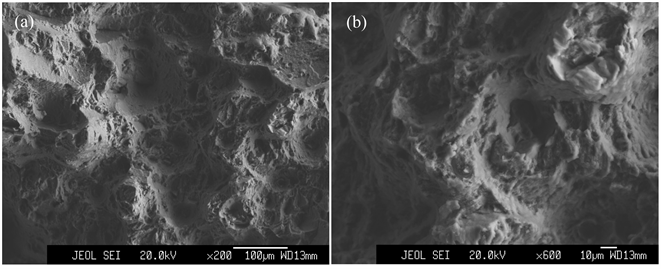
Figure 10. Tensile fracture morphology of AlSi10Mg sample fabricated by SLM
图10. SLM成形的AlSi10Mg试样拉伸断口形貌
4. 主要结论
1) 在激光功率450 W,扫描速度3800 mm/s,扫描间距60 μm,层厚30 μm条件下SLM制备的AlSi10Mg试样观察不到明显孔洞和其他缺陷。
2) AlSi10Mg试样横截面主要由大小均匀“带状”条纹构成,纵截面由大小不均的“U形”条纹构成,条纹间界限明显。横纵截面条纹都由大量细小晶粒组成,横截面“带状”条纹中可分为三个区域:内部细晶区、热影响区、边界粗晶区;纵截面“U形”条纹中分为两个区域:内部等轴晶区、边界柱状晶区。受热输入量不同影响,横纵截面条纹边界晶粒直径大于条纹内部,纵截面晶粒直径整体大于横截面。
3) SLM成形的AlSi10Mg试样具有良好的综合拉伸力学性能,抗拉强度、屈服强度和伸长率分别达到470 MPa、327 MPa和8.0%,较常规铸造的AlSi10Mg合金分别提高了92%、48%和129%,综合力学性能的提升来源于细晶强化和固溶强化。
基金项目
广东省科学院发展专项资金项目(2019GDASYL-0203002);广东省重大科技专项(2014B010131005和2016B090914001);肇庆市科技项目(2018K006)。
NOTES
*通讯作者。