1. 引言
损伤是在材料反复受载情况下,由材料内部的缺陷引起的材料逐渐损坏失效的过程 [1] 。损伤演化方程基于经典热力学,通过损耗功建立损伤驱动力与材料损伤度之间的关系 [2] [3] [4] [5] 。虽然损伤力学发展至今已有半个多世纪的历史,但目前还在处于发展完善阶段 [6] [7] [8] [9] ,对于材料损伤机制的认识尚存在不足,对影响损伤演化的因素尚未完全明晰,因此对损伤演化的研究也仍在继续 [10] [11] [12] [13] 。工程上利用疲劳实验的结果,如标准试件疲劳实验的S-N曲线,拟合损伤演化方程参数 [14] 。上述方法使理论分析较好的贴近实验结果,但建立损伤演化方程的过程中缺少针对特征量的实验结果,对材料损伤演化的物理本质缺乏清晰的反映,因此对材料内部损伤机制和规律的研究不仅十分重要,而且有待深入。
构件/结构的损伤及其后继演化往往是从材质内部存在细观缺陷的部位萌发的,并逐渐累积乃至形成宏观裂纹 [14] [15] [16] 。金属材料的内部缺陷通常是以微孔洞形式存在,缺陷的具体细节,如大小、形状和位置等等,对材料及结构的宏观损伤演化产生重要影响 [17] [18] [19] 。工程中基于S-N曲线来预估结构疲劳寿命,往往需要结合丰富的结构应用经验 [19] 。基于有限元模型的疲劳计算也是以材料内部为均匀介质的前提进行的。要反映细观缺陷对材料宏观损伤演化以及疲劳寿命的影响,就需要在损伤演化的宏观描述中,融合细观损伤演化机制,将细观损伤演化的影响“嵌入”宏观损伤理论中 [3] 。
本文建立带孔/裂纹板有限元模型进行损伤模拟计算,以带孔/裂纹板表征存在细观尺度缺陷的材料,以带孔/裂纹板的损伤演化表征微孔洞/微裂纹材料的损伤演化,将这样的损伤演化影响融合在宏观损伤演化的理论描述中,从而实现细观损伤机制对宏观损伤演化的作用。而后考虑到损伤累积主要是由改变形状的偏斜应力造成的,而体积应力则基本不造成损伤累积,从损伤驱动力中剔除体积应力的成分,得到刨除体积应力影响的损伤演化方程,使用不同应力集中系数的有限元模型进一步对该方程进行仿真验证,并与实验结果进行对比,验证了该方程的适用性及其体现的损伤规律的合理性。
2. 拉压及双向载荷对损伤演化过程的影响
2.1. 损伤演化方程的基本形式
假设损伤度为D,载荷周次为N,考虑到材料的门槛值,微分形式的损伤演化方程如下 [20] :
(1.1)
式中α和p均为损伤演化方程的损伤参数,如上所述,可通过标准试样疲劳试验的S-N曲线拟合确定;Yth为材料损伤驱动力门槛值,YM和Ym为相应于载荷峰值和谷值的损伤驱动力。在单轴加载情况下,损伤驱动力可写为:
(1.2)
(1.3)
(1.4)
考虑通常情况下损伤驱动力门槛值比载荷谷值的损伤驱动力大,即Yth > Ym,则式(1.1)可简化为:
(1.5)
将式(1.2)~(1.4)带入式(1.5)可得:
(1.6)
2.2. 损伤模型的建立
损伤一般发起于材料细观缺陷,包括微裂纹和微孔洞。材料受到拉应力造成并累积损伤,而压应力基本不累积损伤,上述对损伤的传统认识得到工程实践的广泛证实。本文基于上述认识,建立带孔/裂纹大板有限元模型,表征存在细观尺度缺陷的材料,进行损伤模拟计算以揭示含微孔洞/微裂纹材料的损伤演化,将这样的损伤演化特质融合在宏观损伤演化的理论描述中,从而实现细观损伤机制对宏观损伤演化的作用,说明了传统损伤认识的物理合理性。
首先,基于损伤力学方法,在通用有限元软件环境中进行损伤计算程序的二次开发,利用损伤演化方程式(1.6),循环加载并计算模型各个单元的损伤度累积;同时根据损伤度修正单元材料刚度,直至出现单元损伤度达到1并被“杀死”,终得到材料疲劳寿命的模拟结果。需要说明的是,本节损伤累积计算不考虑压应力相应的变形能造成的材料损伤。
本节选取超硬铝合金LC91材料,其刚度E = 75 GPa,泊松比为0.3,使用其疲劳试验结果 [21] 对式(1.6)进行参数拟合,得到σth = 102.017、α = 1.3122 ´ 10−5、p = 0.6994。建立带中心孔方板的有限元模型,板的长/宽为40 mm,厚度1 mm,板的中心孔半径为2 mm,网格划分如图1所示(其中,(a)图为模型整体网格,(b)图为孔边局部放大),加载方式为竖直方向的均布单向拉/压载荷。
(a)
(b)
Figure 1. Model and finite element meshing. (a) Model overall grid; (b) Partial enlargement of the hole edge
图1. 模型及其有限元网格划分。(a) 模型整体网格;(b) 孔边局部放大
2.3. 拉/压加载下孔洞模型损伤演化模拟计算分析
对模型施加脉动循环拉伸载荷,幅值为100 MPa,模型单元(材料)损坏时,损坏区域材料应变能密度分布如图2(a)所示,损伤度分布如图2(b)所示(图中缺口处即为单元被杀死)。显然,由于孔边存在严重应力集中,因此在该区域损伤演化剧烈,相应的,造成材料损伤严重,损伤区明显扩展。
(a)
(b)
Figure 2. Strain energy density and damage distribution of damaged area under pulsating cyclic tensile load. (a) Strain energy density distribution; (b) Damage distribution
图2. 脉动载荷(拉伸)下材料损坏区域的应变能密度和损伤分布。(a) 应变能密度分布;(b) 损伤度分布
与上面情况相对应,当施加脉动循环压缩载荷(载荷幅值相同)时,模型在孔洞的顶部出现单元(材料)损坏,该区域材料应变能密度分布如图3(a)所示,损伤度分布如图3(b)所示。需要说明的是,与拉伸情况不同的是,模型在压缩载荷下,孔洞顶部虽然存在拉应力,但很小,损伤累积很慢。
在模型上下边界施加大小不同的均布拉/压循环载荷,得到疲劳寿命的结果如表1所示,结果表明在载荷幅值相同的条件下,脉动循环拉伸载荷相应的模型疲劳寿命远短于压缩载荷相应的疲劳寿命,二者相差一个数量级以上。当然,无论是拉伸还是压缩,载荷幅值越大,模型疲劳寿命越短。
(a)
(b)
Figure 3. Strain energy density and damage distribution of damaged area under pulsating cyclic compress load. (a) Strain energy density distribution; (b) Damage distribution
图3. 脉动载荷(压缩)下材料损坏区域的拉应变能密度和损伤分布。(a) 应变能密度分布;(b) 损伤度分布
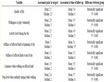
Table 1. Simulation load-fatigue life (´104)
表1. 仿真载荷–疲劳寿命(´104)
参看表1,除上述基本规律外,可以看到模型疲劳寿命对拉应力水平比较敏感,拉应力水平的小幅增加可能造成疲劳寿命显著下降;而在压缩载荷作用下,应力水平提高造成的疲劳寿命减小是比较缓和的。
从材料角度看,拉伸应力会促进晶间变形,加速晶界的破坏,而压缩应力能够阻止或减小晶间变形,随着压应力的增大,晶间变形会愈加困难。工程实践中,拉应力作用下结构损伤演化显著,疲劳寿命短,而在同等水平的压应力作用下,疲劳寿命相比于拉伸情况明显增长,这是得到广泛验证的事实 [22] [23] 。
2.4. 微裂纹模型损伤演化模拟计算分析
通常延性材料中的微缺陷多为孔洞型,而脆性材料的微缺陷以微裂纹为主。材料(疲劳)破坏表现为脆性也是材质微裂纹扩展造成的。因此,本节建立微裂纹缺陷的有限元模型,进一步对脆性材料在脉动循环拉伸和压缩载荷情况下的疲劳性能和机理进行模拟分析。
首先建立正方形板有限元模型,模型板的长宽均为200 mm,裂纹长6 mm,宽度0.1 mm,如图4(a)图所示,局部网格划分如图4(b)图所示,所用材料为铸铁HT250,E = 110 GPa,泊松比为0.156,其标准试件疲劳数据如表2所示 [23] 。
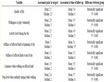
Table 2. Cast iron HT250 fatigue test life
表2. 铸铁HT250疲劳试验寿命
(a)
(b)
Figure 4. Crack model meshing. (a) Finite element crack model; (b) Partial enlargement picture
图4. 裂纹模型网格划分。(a) 有限元裂纹模型;(b) 局部放大图
本节模型中的裂尖用弧段来模拟,对微裂纹损伤进行定性讨论。不同于延性材料,脆性材料没有应力门槛值,因此对应的损伤驱动力谷值为零。通过表2中的疲劳实验结果拟合得到损伤参数为:
,
(2.1)
对模型分别施加垂直裂纹方向(Y方向)拉力以及平行裂纹方向(X方向)压力两种脉动循环拉伸循环载荷,两种不同载荷的应变能密度分布分别如图5(a)和图5(b)所示,计算寿命如表3,表4所示。对比可知,在微裂纹垂直方向上的拉应力所造成的应力“集中”远非微孔洞可比,微裂纹对与其垂直的拉应力几乎不具备承受能力,很小的拉应力就可以导致迅速破坏。与此相对比,平行裂纹的压应力由于泊松效应,在裂纹尖端的Y方向上也会产生拉应力,导致材料疲劳失效,但显而易见,比在垂直裂纹方向的拉应力作用下的疲劳寿命要长很多。
(a)
(b)
Figure 5. Vertical crack direction pull and parallel crack direction compressive strain energy density distribution map. (a)Strain energy density under tensile load; (b) Strain energy density under compressive load
图5. 垂直裂纹方向拉以及平行裂纹方向压应变能密度分布图。(a) 拉伸载荷下的应变能密度;(b) 压缩载荷下的应变能密度
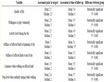
Table 3. Model damage fatigue life under uniaxial tensile stress
表3. 单向拉应力状态下模型损伤疲劳寿命
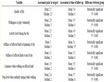
Table 4. Model damage fatigue life under uniaxial compressive stress
表4. 单向压应力状态下模型损伤疲劳寿命
以上结果说明,由于微缺陷的几何属性所决定的物理特质,相比微孔洞主导的微缺陷模型,微裂纹主导模型的抗拉能力显著变差,并与压应力的情况形成很强的对比,从而造成材料破坏的脆性特质。
2.5. 双向加载结果分析
多向加载情况下的损伤演化,即多向应力状态下的损伤累积规律,是损伤力学研究的重要课题。本节沿用上节“拉应力造成损伤累积,压应力不造成损伤累积”这一理论假说,基于2.3节中的材料和模型进行损伤模拟分析,保持模型所受Y向应力为100 MPa不变,在X方向施加不同的载荷,如表5所示,其中正值为拉应力,负值为压应力,计算模型材料疲劳寿命的具体结果如表5的最后一行所示。可知,在双向等拉的情况下,模型疲劳寿命最大,远大于单向拉伸的情况;在双向拉伸的情况中,(Y向应力不变),X向应力越小,疲劳寿命也越短;在Y向为拉应力、X向为压应力的情况中,压应力越大,疲劳寿命越短。
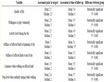
Table 5. Model fatigue life under biaxial stress (´104)
表5. 双向应力状态下模型疲劳寿命(´104)
为了更深入的研究双向载荷对材料损伤的影响,定义双向应力比为
(2.2)
取若干双向应力比r,对每一个双向应力比,取不同应力水平的载荷,通过损伤模拟分析,考察构件模型的疲劳寿命变化,计算结果如图6所示:当双向应力比值r = −1时,即σx = −σy,构件的受力状态为一拉一压,其中压应力显著加大了构件的偏斜应力,相应的模型疲劳寿命也是各应力组合中最短的;当应力比值逐渐增大时,即外加载荷的偏斜应力部分减小,体积应力部分增大,则构件的疲劳寿命相应增长。总之,在同一应力水平下,应力状态越接近双向等拉,即r = 1,模型疲劳寿命越长,反之则越短。
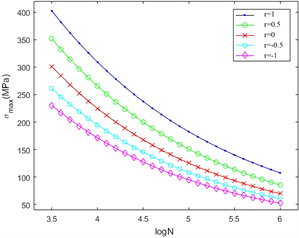
Figure 6. Model fatigue life at different stress ratios
图6. 不同应力比下的模型疲劳寿命
基于对损伤及其演化的认识,毫无疑问,较大应力带来较大损伤。但从上述结果可见,体积应力和偏斜应力对损伤累积的作用有着显著区别,下面对这一问题将做进一步研究分析。
3. 刨除体积应力后的损伤演化研究
3.1. 损伤演化方程参数的非一致性
损伤演化方程是材料损伤的本构,损伤演化方程参数是材料的损伤特质参数,与外在条件无关。而实际应用中,需要通过疲劳实验的S-N曲线确定损伤演化方程参数,这样确定的损伤演化方程虽然符合疲劳试验的基本规律,但其损伤参数难以体现损伤演化的物理特征。对于不同类型的外载荷以及试件(不同的应力集中系数),拟合得到的损伤参数可能不同,进而影响理论预估的疲劳寿命,不利于工程应用。基于上述情况,本节将对损伤演化方程及损伤参数的确定进行分析讨论。
3.2. 偏斜应变能与体积应变能
物体在外力作用下发生变形,既包括体积改变也包括形状改变;外力在相应的位移上做功,亦即应力在相应的应变上做功,在物体内部积蓄能量(即应变能),因此有
(3.1)
其中,γε为总应变能密度,γV为体积应变能密度,γd为偏斜应变能密度,后两者分别表示体积改变的球形应力和形状改变的偏斜应力所对应的应变能密度。一般认为损伤累积主要由改变形状的偏斜应变能γd造成的,而对应体积改变的体积应变能γV不造成损伤累积。上节的有关结果与此认识相一致。从宏观认识上,塑性变形所对应的是偏斜应力,材质的损伤与塑性相类似,所以这里做一个大胆的推断,即认为损伤累积主要是由改变形状的偏斜应变能γd造成的。因此在后面的损伤模拟分析中,将损伤驱动力中对应体积改变的体积应变能γV部分刨除。
3.3. 刨除体积应变能的损伤驱动力
若定义等效应力σe为:
(3.2)
式中σx、σy、σz、τyz、τxz、τxy分别为x、y、z方向的正应力和切应力,μ为材料泊松比,则损伤驱动力Y可进一步表示为:
(3.3)
体积应力σv可表示为
(3.4)
设σxs、σys、σzs分别为式(3.2)中应力对应的偏斜分量σx-σv、σy-σv和σz-σv,则偏斜等效应力σes可表示为
(3.5)
因此,偏斜应力定义的损伤驱动力与损伤演化方程可表示为:
(3.6)
(3.7)
3.4. 单向加载模型结果分析
损伤演化方程参数是根据标准试样疲劳试验的S-N曲线拟合得到的,之前的讨论已经表明体积应力对应的体积应变能不造成损伤累积,损伤是偏斜应变能造成的。因此,将S-N曲线中的应力转化成相应的偏斜应力,进一步以此偏斜应力定义损伤驱动力进行损伤演化分析。特别需要指出的是,本节中损伤演化方程中的损伤参数也是以这样的偏斜应力来拟合确定的。
选取超硬铝合金LC91材料,其损伤演化方程参数为σth = 95.03 MPa,α = 1.685 × 10−5,p = 0.7041,在损伤驱动力中刨除体积应变能,然后进行模拟损伤分析。
由材料力学可知,带孔无限大板的孔边应力集中系数K = 3,而本模型的建立其意在研究宏观模型中细观缺陷对宏观损伤的影响,其形恰好符合带孔无限大板的情况,即在预估模型疲劳寿命时,应对应K = 3的试验件的疲劳寿命。为验证“在损伤累积及疲劳寿命预估时应刨除体积应力所对应的应变能,只考虑偏斜应力对应的应变能造成损伤累积”这一假说,将本文模型的单向拉伸寿命预估计算结果与K = 3的标准试样疲劳试验的S-N曲线进行对比,结果如图7所示。应该说明的是,图7中的曲线是实验曲线,菱形数据点是采用传统方法计算得到的结果,而图中圆形数据点是采用本文新方法计算得到的结果,两类数据点的应力是相同的。由图7可知,取偏斜应力定义损伤驱动力,计算出来的疲劳寿命更为符合K = 3时的材料S-N曲线。
一般而言,材料的疲劳损伤是由其内部的微缺陷诱发的,其损伤演化是跨尺度的,损伤效应具有强烈的局部性,损伤演化过程是非线性的。在工程中使用的S-N曲线是假设材料内部均匀无损,截面上各个位置等速损伤;当萌生宏观裂纹时对应的载荷周次即为疲劳寿命。这样试验得出的疲劳寿命其实也包含了细观缺陷的影响。
与此不同的是,有限元模型中的材料是均匀无损的,计算结果没有真实材料缺陷的影响,这与实际情况不符,本文中的模型,宏观上是一个带孔的无限大板模型,但表征的是细观上带微缺陷(微孔洞)的构件模型。
为了进一步揭示损伤累积中体积应力与偏斜应力的贡献,考虑无限大板带椭圆孔的模型,椭圆缺陷的应力集中系数公式 [24] :
(3.8)
其中a为椭圆孔长轴,b为椭圆孔短轴。考察K = 5,由上式可知a = 2b,建立模型如图8:
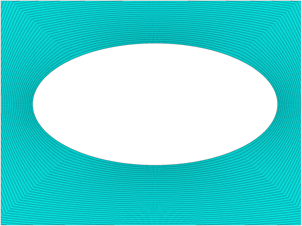
Figure 8. Schematic diagram of finite element meshing with elliptical square plates
图8. 带椭圆孔方板的有限元网格划分示意图
模型仍采用前面模型的材料,板的长/宽为40 mm,厚度1 mm,板的椭圆长轴为2 mm,椭圆短轴为1 mm。在上图模型中施加垂直方向的均布载荷,由于应力集中,损伤在椭圆的长轴端缘累积最快,因此在椭圆周围一圈加大了网格密度,确保计算精度。
以K = 5的材料疲劳试验的S-N曲线为参考,对模型上下两边分别施加短轴方向67 MPa、78 MPa、98 MPa和132 MPa的均匀拉载荷,并设置等效应力(式(3.2))主导以及刨除体积应力的偏斜应力(式(3.5))主导的两种损伤驱动力形式,分别计算其疲劳寿命,其结果与K = 5的标准试样材料疲劳试验的S-N曲线进行对比,如图9所示,与前例相似,取偏斜应力定义损伤驱动力时,计算出来的疲劳寿命更为符合K = 5时的材料S-N曲线。
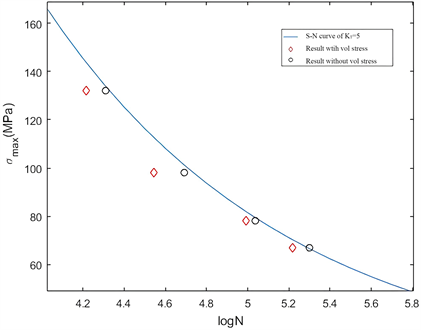
Figure 9. Fatigue life results for different damage driving forces of K = 5
图9. K = 5情况下不同损伤驱动力的疲劳寿命结果
同样,使用文献 [24] 中应力集中系数K = 1时的标准件模型,进行标准件单向拉伸疲劳仿真,设置布载荷分别为270 MPa、221 MPa、196 MPa、156 MPa和130 MPa,使用两种损伤驱动力形式分别计算其疲劳寿命,得到结果如图10所示,仍是使用偏斜应力定义的损伤驱动力得到结果较好。
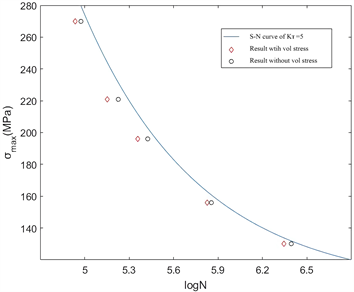
Figure 10. Fatigue life results for different damage driving forces of K = 1
图10. K = 1情况下不同损伤驱动力的疲劳寿命结果
从上面例子可以看出,基于上述损伤驱动力的新定义,通过标准试样疲劳实验的S-N曲线确定了统一性的损伤演化方程参数,有限元模型损伤累积模拟计算的结果与试验结果符合良好,从而证明材料的损伤演化方程参数是材质特性参数,对于不同应力状态有内在一致性。
3.5. 体积应力造成的损伤演化模拟分析
参考“3.4双向加载结果分析”一节表5第一列双向等拉载荷情况,比较表5其他载荷情况下的疲劳寿命可知,前者的疲劳寿命远长于后者。本节仍沿用前述有限元模型以及材料参数,计算上述双向等拉载荷下材料损伤,参看图11,初始阶段的损伤演化大致呈现线性快速增长状况;当损伤演化进程到达一定阶段时,即本例中损伤度达到0.6时,材料损伤基本呈现停滞状态。按照一般情况,此时材料损伤应迅速劣化,材料进入不稳定破坏状态。
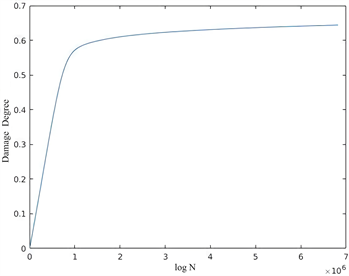
Figure 11. Model material damage accumulation curve under biaxial equal tension
图11. 双向等拉情况下模型材料损伤累积曲线图
应该指出的是,由于本模型表征了含微孔洞的材料,因此上述损伤累积趋势也能体现细观的材料损伤机制。
之所以会在双向等拉情况下产生上述损伤演化停滞的情况,是因为在该状态下微缺陷周边的Mises应力沿孔边呈现均匀分布,该构件的损伤围绕微孔洞出现等演化扩展,参看图12。由于孔边同步损伤,刚度同步下降,其变形同步等变;随着材料损伤演化、变形加大后,原孔周边区域承载力下降,损伤区外缘区域周向均匀的进入新一轮损伤的同步演化,演化状况与前相同,即“周向同步”。因此模型总体的损伤演化反而减缓。
(a)
(b)
(c)
(d)
Figure 12. Damage accumulation process cloud diagram in biaxial isolating state. (a) N = 3 × 104; (b) N = 15 × 104; (c) N = 50 × 104; (d) N = 100 × 104
图12. 双向等拉状态下损伤累积进程云图。(a) N = 3 × 104; (b) N = 15 × 104; (c) N = 50 × 104; (d) N = 100 × 104
上述演化过程和特征表明,由于处于双向等拉状态,材料损伤加大后,损伤演化趋于停滞状态,因而“体积应力不累积损伤”的理论假说,不仅在与试验曲线相符合的角度得到了宏观印证,也与材料细观损伤演化的基本规律相符合。因此,本节研究不仅直接支持了体积应力不造成损伤累积的宏观假说,特别是材料在损伤演化中趋于停滞的细观机制更是该假说的坚实物理基础。
4. 结论
1) 本文通过带孔洞无限大板模型的损伤演化模拟,揭示了带微孔洞(/裂纹)缺陷材料的损伤演化特质。这一模拟研究说明,工程应用中认为“拉应力造成损伤而压应力不造成损伤”,这样的认识源于微孔洞边缘的应力集中。在拉应力作用下,由于孔边拉应力集中严重,因此损伤演化严重,损伤累积严重;与此相应,在压应力作用下,由于拉应力只存在于孔缘在压应力方向上的拉应力区,且该区域的拉应力相比于远场应力较小,因此损伤演化很慢,损伤累积基本可以忽略。
2) 上述研究说明,“拉应力造成损伤,压应力不造成损伤”的工程认识不仅具有实践基础,也具有理论合理性,更重要的是,基于材料细观构型,这样的认识不仅源于宏观唯像,也反映细观机制。
3) 本文基于前述模型对双向应力状态下的损伤演化进行了模拟研究,结果表明,处于等拉状态下模型的疲劳寿命最长;相反,两向应力相差越大,乃至双向应力为一向受拉一向受压的状态,模型的疲劳寿命越短。
4) 双向应力状态的模型损伤研究表明,在一种应力状态下,其体积应力的成分越大,损伤演化越慢,损伤累积越小,也就是说,体积应力不造成损伤累积。这样的工程认识具有良好的理论基础,本文含缺陷棒件的疲劳寿命预估也证明了这点。
5) 本文研究了双向等拉状态下含孔洞模型的损伤演化,结果表明,由于孔洞周边应力分布的均匀性,造成孔洞周边材料损伤演化的等同性,因而损伤累积进程十分缓慢,揭示了“体积应力不造成损伤累积”的细观机制。
6) 含微裂纹模型在双向应力作用下的疲劳寿命预估结果与前述含微孔洞模型在双向应力作用下的疲劳寿命情况相近,再次以宏观模型解释材料细观微裂纹缺陷对损伤累积的作用,从而证明了压应力不造成损伤累积这一认识的应用性。
NOTES
*通讯作者。