1. 引言
钢渣和赤泥都是排放量大且难以利用的冶金固废。钢渣是在钢铁生产过程中不可避免产生的副产品,每年的产量约为粗钢产量的10%~15%。钢渣含有的大量的CaO和Fe2O3使其难以高比例地添加到陶瓷配方中,堆积存放也会造成土地的占用和污染 [1] [2]。赤泥是制铝工业提取氧化铝时排出的污染性废渣,根据其生产方式不同,可分为烧结法赤泥和拜耳法赤泥。平均每生产1吨氧化铝,附带产生1.0~2.0吨赤泥 [3] [4]。中国作为世界第四大氧化铝生产国,每年排放的赤泥高达数百万吨。赤泥同样具有很高的碱性,露天堆积会对水和土壤造成极大的污染。因此钢渣和赤泥的循环再利用是一个值得研究的课题。
钢渣和赤泥均有制备陶瓷的基础。赵立华 [5] 等研究了CaO-MgO-SiO2体系的钢渣陶瓷材料,钢渣的掺量达到40 wt.%时,在1210℃制备了最大抗折强度可达143 MPa的样品。Gorokhovsky A.V. [6] 等向合成陶瓷中添加了33~50 wt.%的钢渣,制备了抗折强度最高为203 MPa的陶瓷。Emilia Karamanova [7] 等在1200℃~1220℃的温度下研究了钢渣含量为30 wt.%,50 wt.%和70 wt.%的陶瓷的不同性能,提高了结晶度并形成了钙长石固溶体和辉石。徐晓虹 [8] 等以烧结法赤泥、拜耳法赤泥两种固体废弃物为主要原料,制备出高性能的赤泥质陶瓷内墙砖,抗折强度可达20~35 MPa。李大伟 [9] 等采用黏土20 wt.%、赤泥80 wt.%的配比生产出了符合国家标准的烧结砖,其抗压强度在20 MPa以上,吸水率在18%以下。吕常胜 [10] 等研究了赤泥添加量30~60 wt.%时对烧结砖机械性能的影响,认为赤泥的产物中钙铝黄长石有助于提高烧结砖的抗压强度。在这些利用钢渣和赤泥制备烧结砖的基础上制备发泡陶瓷是一种可行的方法。
发泡陶瓷是一种良好的隔热保温材料,广泛应用于建筑墙体的隔热保温,其内部大量的封闭气孔可以有效地减少壁的两侧的热交换来达到保温隔热的效果。同时,发泡陶瓷作为无机绝热材料,不仅具有普通陶瓷的耐腐蚀、耐高温的优点,还具有强度高、防火和耐候性好的优点。在建筑外墙保温、防火隔离、隔音等高防火要求领域具有重要的应用价值 [11] [12] [13]。
制备发泡陶瓷主要的方法是添加发泡剂法,即在已有的陶瓷基体材料的基础上,加入合适的发泡剂,高温下发泡剂发生化学反应产生气体,同时基体材料产生具有一定粘度的共熔体,两者同时作用,气体引起基体膨胀,基体将气体包裹在内部无法逸出,最后形成具有封闭气孔的发泡陶瓷 [14]。
发泡陶瓷制备的关键在于发泡剂的化学反应,因此基体材料的化学成分和烧成温度对发泡剂有很大的影响。钢渣和赤泥中都含有铁,但是钢渣中的铁大多数为二价铁,而赤泥中的铁是三价铁。周明凯 [15] 等研究表明氧化铁掺量在小于6 wt.%的情况下可以获得孔径均匀、性能较好的发泡陶瓷,密度可以达到170~270 kg/m3。杨赞中 [16] 等研究了炭黑、碳酸钙、氧化铁、碳化硅四种发泡剂的复合作用对发泡陶瓷性能的影响,其中氧化铁对发泡陶瓷体积密度影响大于对吸水率的影响,即氧化铁对孔的形成有显著影响。池跃章 [17] 等在抛光砖废渣中加入不同的发泡剂,研究表明Fe2O3可以同时作为发泡剂和熔剂组分在陶瓷坯体中起作用,当Fe2O3添加量不超过3 wt.%时,可以制备气泡均匀的发泡陶瓷。可见三价铁对发泡陶瓷的制备有积极作用,但二价铁的作用几乎没有被讨论。本文将钢渣和赤泥作为二价铁和三价铁的来源,选取了SiC作为高温发泡剂,通过热重与XRD分析比较两者对发泡陶瓷的影响。
2. 实验原料与方法
2.1. 实验原料及配方设计
本研究中使用的原料及其成分见表1,钢渣来源于山东钢铁集团,赤泥来源于山东铝业公司,其它陶瓷原料来自于山东义科节能公司。钢渣配方S0由30 wt.%钢渣、5 wt.%滑石和65 wt.%粘土1配制而成,赤泥配方R0由5 wt.%长石、37 wt.%粘土2、40 wt.%赤泥和18 wt.%滑石配制而成。从表1可以看出,钢渣和赤泥成分的主要特点是含有大量的钙和铁,硅和铝偏少,粘土1、粘土2和长石则作为硅和铝的补充加入配方,滑石主要为陶瓷配方提供镁。在S0和R0的基础上,分别添加0.1 wt.%的SiC作为发泡剂,其中50%粒径小于6.923 μm。两种样品记为S1和R1。
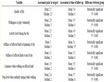
Table 1. The chemistry composition of raw materials, S0 and R0
表1. 原料、S0和R0的化学成分表(wt.%)
2.2. 实验方法
将原料按比例配好后在行星球磨机中分别破碎磨细后通过200目筛,在105℃的烘干箱中烘干24 h,加入6~8 wt.%水均匀混合后过20目筛,在15~20 MPa的压力下压制成50 mm × 10 mm × 5 mm的陶瓷坯体,再次置于105℃烘干箱中烘干24 h,取出后用梯度析晶炉进行烧结,以5℃/min的升温速率升至烧结温度,保温1 h,后随炉冷却。
通过热重–差式扫描量热仪(TG-DSC; SDT-Q600, TA Instruments, USA)分析原料在升温过程中进行的反应,X射线衍射仪(XRD; M21X, MAC Science Co., Ltd., Japan)分析烧结前后的物相变化,光学显微镜(Leica Microsystems CMS GmbH, Germany)观察样品的微观形貌。
3. 结果与分析
3.1. 原料的热分析结果
SiC、钢渣和赤泥的TG-DSC曲线结果见图1。从图1中可以看出,钢渣和赤泥始终在一个失重的状态,700℃后质量变化不大。SiC在约1000℃时才开始反应,主要为反应式(1)的氧化反应,且随着温度的升高,反应一直持续进行。这一反应将导致固相增重,SiC转变为SiO2,理论上导致生成物重量相对反应物SiC增加50 wt.%。由图1可知,碳化硅在1016℃开始增重,但增加缓慢,一直到1300℃时,其增重才为2.2 wt.%,也就是仅4.4%的SiC发生了氧化反应。已有研究表明,SiC氧化形成的SiO2会在SiC表面形成致密的氧化层,阻断了氧气的扩散。因此,碳化硅作为加热元件时,可以长期使用;但是作为发泡剂,通常采用物理细碎的方法增加表面积,使得碳化硅被粉磨至500目甚至1000目。本实验所用的碳化硅为200目,颗粒较粗,因此容易形成致密的二氧化硅保护层。在制备陶瓷过程中,碳化硅粉与其它陶瓷原料混磨,进一步增加其细度,促进更多的SiC氧化。
(1)
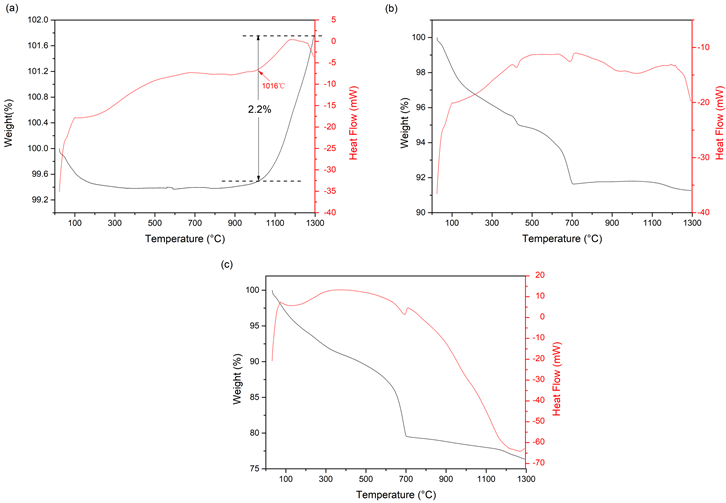
Figure 1. The TG-DSC result of (a) SiC, (b) steel slag and (c) red mud
图1. (a) SiC,(b) 钢渣,(c) 赤泥的热分析曲线
3.2. 样品的机械性能与微观形貌
将烧结后的样品进行抗折强度、吸水率和密度的测试,检测不同温度下的矿相变化,同时在光学显微镜下观察样品的微观形貌。从图2可以看出,样品S1在1120℃抗折强度达到最高且吸水率最低,从1130℃开始强度和密度都迅速降低,吸水率开始有所升高,到1160℃时吸水率迅速升高,密度可降低至0.5 g/cm3。从图3的微观形貌可以看出,1130℃时样品内还没有形成明显的气孔,抗折强度还保持在较高的水平;样品在1140℃开始出现明显区分的孔和孔壁,孔的边缘不规则;1150℃时开始出现规则的圆形的孔,孔的边缘光滑,且孔壁上存在一些较小的孔;当烧结温度达到1160℃时孔的直径明显变大,孔壁上也出现了明显变大的孔,且有向主要的孔合并的趋势。图4分析了样品S1在不同烧结温度下的矿相转变。样品在1140℃时还存在大量的石英和硅灰石,随着温度升高两者均有所降低,而辉石和钙长石显著增加,烧结温度达到1160℃时主晶相为辉石和钙长石,还有少量硅灰石剩余,几乎没有石英。
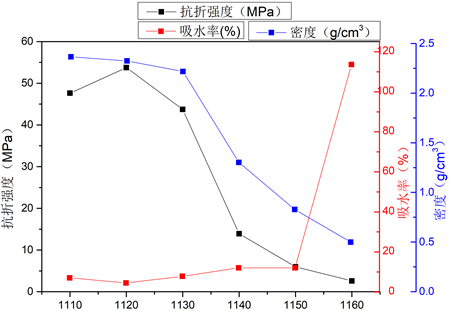
Figure 2. Flexural strength, water absorption and density of S1 sintered at different temperatures
图2. 不同温度下S1的抗折强度、吸水率和密度
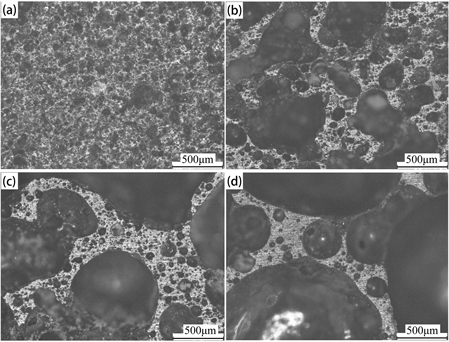
Figure 3. The microstructure of S1 sintered at (a) 1130˚C, (b) 1140˚C, (c) 1150˚C and (d) 1160˚C
图3. S1在(a) 1130℃,(b) 1140℃,(c) 1150℃和(d) 1160℃下烧结样品的微观形貌
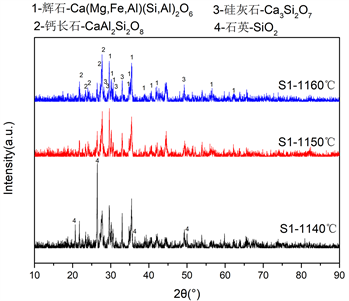
Figure 4. The XRD results of S1 sintered at 1140˚C, 1150˚C, 1160˚C
图4. S1在1140℃,1150℃,1160℃下烧结样品的XRD结果
结合以上结果分析可知,样品S1在1130℃时尚未形成孔,坯体内部还保持致密,当样品在1140℃开始形成明显的孔时,烧结样品仅由孔壁提供骨架的支撑,因此抗折强度迅速减小。同时在烧结过程中产生的气体被包裹在坯体内部形成封闭气孔,坯体膨胀导致体积增加,密度随之降低。当温度进一步升高的时候,坯体表面开始有气体逸出留下的微孔,使陶瓷吸入的水充满内部的空间,导致吸水率极大地升高。在S1样品中,铁的去向主要为与钙硅等离子结合形成辉石,检测结果中没有铁的氧化物的特征峰。
从图5中可以看出,R1样品呈现出与S1样品相似的曲线。在1080℃~1120℃之间陶瓷样品处于致密化阶段,抗折强度和密度都呈现出上升的趋势。1120℃之后开始出现液相,同时气体的产生使坯体变得疏松多孔,在曲线上表现为抗折强度下降,吸水率升高。与S1有所不同的是,R1的变化趋势较为缓慢,明显生成气孔的温度也更高,1180℃后各项机械性能趋于平缓,密度最低可达到1.00 g/cm3。从图6可以看到,R1在1160℃才开始形成边缘不规则的气孔,1170℃时形成边缘明显且规则的大孔,孔与孔之间相互合并形成更大的孔。当温度升至1180℃时,坯体形成了与S1在1160℃时相似的形貌,但是在相同的放大倍数下可以看到R1的孔壁要比S1的孔壁更厚。图7展示了样品R1在不同温度下的XRD结果,可以看到,在R1与S1相似的成分配比的情况下,R1的主晶相为透辉石、钙长石和赤铁矿,石英的特征峰在1180℃下才基本消失,赤铁矿的峰没有明显变化,但有一部分Fe3+与钙硅结合生成钙铁榴石。
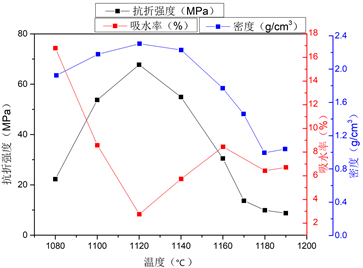
Figure 5. Flexural strength, water absorption and density of R1 sintered at different temperatures
图5. 不同温度下R1的抗折强度、吸水率和密度

Figure 6. The microstructure of R1 sintered at (a) 1140˚C, (b) 1160˚C, (c) 1170˚C and (d) 1180˚C
图6. R1在(a) 1140℃,(b) 1160℃,(c) 1170℃和(d) 1180℃下烧结样品的微观形貌
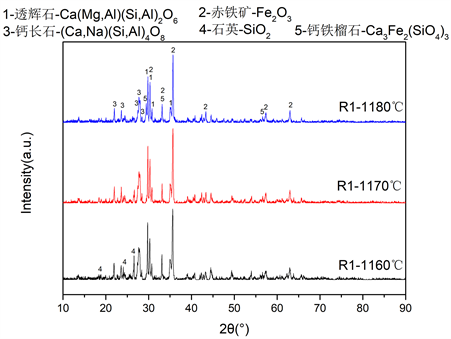
Figure 7. The XRD results of R1 sintered at 1160˚C, 1170˚C, 1180˚C
图7. R1在1160℃,1170℃,1180℃下烧结样品的XRD结果
3.3. 发泡机理讨论
为进一步讨论两种固废对发泡效果的影响,分别对S0、S1、R0、R1进行热分析,其TG-DSC曲线如图8所示。图8(a)中可以看出700℃时S1相对于S0的失重减少了2.0%,到1300℃时失重差达到了2.5%。S0在1180℃时有一个吸热峰,即S0在1180℃熔化,在1180℃之前处于有液相生成的熔融状态;S1的吸热峰则提前到了1150℃,且峰形变缓。图8(b)中同样显示出R1相对于R0的失重有明显的减少,减少量达到了1.0%,到1300℃时失重差达到了3.4%。同时R0和R1的吸热峰均出现在1180℃,R1的吸热峰比R0的吸热峰更加明显。
图8中失重的减少可能是由于SiC在缓慢氧化的过程中反应生成的CO2抑制了碳酸盐等成分的分解 [18],随后随着温度的升高,SiC的氧化反应开始快速进行,使S1和R1的曲线叠加了一个增重的过程,因此S0与S1、R0与R1之间的失重差逐渐增大。此外,钢渣配方中的Ca2+或Fe2+等组分能够使SiC的氧化反应温度提前,且反应变缓,这有利于SiC缓慢充分放出气体,实现对发泡程度的控制;而赤泥配方与SiC的混合对反应温度没有影响,但是能促进反应的进行,使1100℃以后的反应更剧烈,失重差达到3.4%,这种现象可以使发泡过程快速完成,但容易导致反应的快速进行而不易控制。
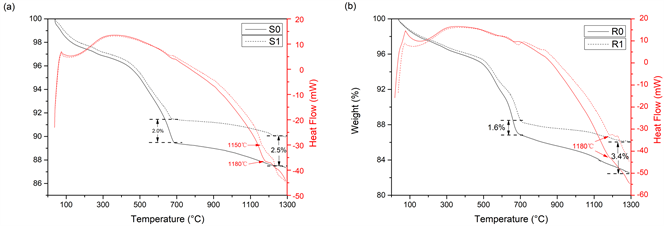
Figure 8. The TG-DSC result of (a) S0 and S1, (b) R0 and R1
图8. (a) S0与S1,(b) R0与R1的热分析曲线
结合图2和图5可知,赤泥发泡陶瓷在烧结过程中的抗折强度始终高于钢渣发泡陶瓷,但高温下赤泥发泡陶瓷的密度不如钢渣发泡陶瓷低。可能由于其中形成了钙铁榴石矿相,使赤泥发泡陶瓷产生的液相比钢渣发泡陶瓷形成的液相更稀,无法实现气体被熔融状态的陶瓷坯体包裹,于是气体更易逸出,导致成孔不佳。
综上所述,钢渣更适宜制备发泡陶瓷产品。从两者对比来看,钢渣与SiC的混合能使反应温度提前并降低反应的剧烈程度,易于对发泡过程进行控制,能制备更低密度的发泡陶瓷;赤泥与SiC的混合对反应温度没有影响,但是能加快反应的速度,有利于发泡陶瓷的快速烧成,但赤泥陶瓷中碳化硅氧化过程集中,气体释放量大,同时液相形成区间短,不利于发泡过程的控制。
4. 结论
钢渣和赤泥均可以用于制备发泡陶瓷,钢渣发泡陶瓷在1160℃下的主晶相为辉石、钙长石和硅灰石,抗折强度可达到2.60 MPa,密度可达到0.50 g/cm3;赤泥发泡陶瓷在1180℃下的主晶相为透辉石、钙长石和赤铁矿,且生成了钙铁榴石,抗折强度为9.91 MPa,密度为1.00 g/cm3。
发泡陶瓷形成液相的温度与SiC的氧化温度相一致时,两者发生反应,在热分析曲线上表现为增重,且形成了明显地吸热峰。当发泡陶瓷达到烧成温度时,坯体开始产生液相,此时陶瓷坯体中的Ca2+或Fe2+等组分能够促进碳化硅的氧化反应,该氧化反应形成大量气体在陶瓷液相中形成气孔,获得较低密度的发泡陶瓷产品。由于钢渣陶瓷的烧成温度低于赤泥陶瓷烧成温度30℃,SiC的氧化温度在钢渣发泡陶瓷中为1150℃,也相应比赤泥发泡陶瓷低30℃。
与赤泥陶瓷相比,钢渣陶瓷更适宜制备发泡陶瓷。但是钢渣发泡陶瓷在相同密度下力学性能更低,其液相形成区间大,能够形成更低密度的发泡陶瓷产品。在烧成过程中,钢渣中的二价铁在发泡陶瓷的反应过程中参与反应形成辉石,赤泥中的三价铁则以赤铁矿的形式存在,仅有少部分三价铁在1180℃时进入了钙铁榴石相,该转变可能是赤泥陶瓷液相大量增加而不能继续成孔的主要原因。
基金项目
国家自然科学基金资助项目(51474027);国家重点研发计划资助项目(2016YFB0601304)。
NOTES
*通讯作者。