1. 引言
作为常见的金属结构材料,铝合金具有优异的力学与物理性能,广泛应用于各个行业。其中,2A50铝合金在航空领域中作为构造用材使用,常用于制作形状复杂的中等强度零件。但铝合金在使用环境中易发生局部腐蚀和磨损,需对其进行喷丸、滚压、超声冲击或微弧氧化等表面强化处理,以赋予其更为优异的功能特性 [1] [2] [3] [4]。微弧氧化(Micro-Arc Oxidation, MAO)或等离子电解氧化(Plasma Electrolysis Oxidation, PEO)是一种表面改性技术,可通过微弧放电在轻质合金(Al,Mg和Ti)表面生成氧化物陶瓷涂层 [5]。与典型的阳极氧化涂层 [6] 相比,MAO陶瓷涂层具有优异的性能,例如耐磨性 [7],耐腐蚀性 [8],抗热震性 [9],光催化性能 [10],生物相容性 [11] 和湿度敏感性 [12]。铝及其合金的微弧氧化过程中生成的高硬度陶瓷层具有很高的粘附力,这种陶瓷涂层可在高负载的工况下充作保护层,进而降低工件的磨损程度,大幅提高铝合金的耐磨性。国内外对微弧氧化技术做了大量研究,发现微弧氧化的工艺参数如电解液、电参数(电源模式、电压、电流密度、占空比及频率等)、材料的成分等对陶瓷层的性质有较大影响 [13] [14]。Hussein等人使用发射光谱研究了电流模式对Ti-6Al-4V合金基底上的等离子体和氧化物涂层的影响,发现与单极性电流模式相比,脉冲双极性电流的施加导致高温尖峰和平均等离子体温度的降低,能够延长放电时间与增加火花密度,从而得到致密、硬度高且粘附力强的陶瓷层,提升了陶瓷层的耐蚀性 [15]。Mustafa等人使用微弧氧化技术探究了阴极高压脉冲持续时间对铝合金在碱性溶液中形成的涂层性能的影响,认为短脉冲,即低占空比有助于获得高质量的厚致密层,然而相比于提高占空比,延长微弧氧化时间或增加阴极脉冲电压更容易进一步增加陶瓷层的硬度与致密性,但绝不能通过增加占空比来实现 [16]。Lu等人经探究发现,较低占空比条件下,涂层生长速率逐渐增加 [17]。陈喜娣等人探究阴阳极占空比对6061铝合金微弧氧化膜层结构与耐蚀性的影响,发现阴阳极占空比为25/75的膜层结晶良好,耐蚀性强 [18]。国内外学者针对占空比对微弧氧化过程和所生成陶瓷层的影响进行了大量的研究工作,但针对2A50铝合金进行微弧氧化并考察正向占空比对陶瓷层耐磨性能的研究还不多。另外,在电参数的研究中针对正向占空比的研究仍有待细化,故本研究采用双极性脉冲电源,在恒压工作模式下,控制负向占空比不变,改变正向占空比(5%~30%),制备微弧氧化陶瓷层,探究了正向占空比对微弧氧化陶瓷层的微观结构、硬度与摩擦磨损性能的影响。
2. 方法及结果
采用尺寸为20 mm × 30 mm × 3 mm的2A50铝合金(成分:Si:0.7~1.2、Fe:0.7、Cu:1.8~2.6、Mn:0.4~0.8、Mg:0.4~0.8、余量为Al)作试样,经800-2000目水砂纸与金刚石研磨膏打磨至镜面后,使用乙醇超声清洗10 min以确保每个样品具有相同的初始表面条件。电解液采用硅酸盐体系,成分为Na2SiO3 (11 g/L)与KOH (1.7 g/L)。微弧氧化实验利用双极性脉冲电源,电源输出参数控制示意图如图1所示。T为脉冲周期,ton(+)和ton(−)分别表示在一个脉冲周期中,正、负脉冲所占的时间。则正、负占空比可表示为:
(1)
采用恒压模式,2A50铝合金试样作阳极,不锈钢作阴极。为严格有效探究正向占空比对微弧氧化陶瓷层的影响,实验设置负向占空比为5%不变,正向占空比分别为5%、10%、15%、20%、25%、30%,正、负向电压分别恒定为400 V、−50 V,频率均为100 Hz,微弧氧化时间30 min。使用磁力搅拌器保证电解液的均匀性,使用循环冷却水系统控制电解液温度在40℃以下。最后,从电解液中取出样品,用足量去离子水洗涤,冷空气流干燥。
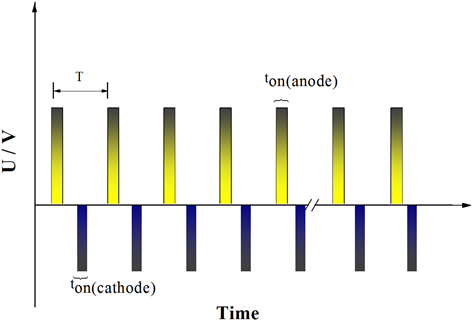
Figure 1. Schematic diagram of controlling of parameters on power source
图1. 微弧氧化电源输出脉冲示意图
采用日立TM3030台式扫描电镜观察微弧氧化陶瓷层表面和截面微观形貌,荷兰PANalytical的EMPYREAN-X射线衍射仪(射线源为Cu的Kα射线,步长为0.02˚,范围为2θ从20˚至80˚的扫描)研究涂层相组成,HVS-1000A华银数显显微硬度计测试陶瓷层硬度,载荷500 g。采用球盘摩擦磨损仪(MS-T3001)测试陶瓷层的耐磨性,摩擦副为40Cr钢球(Ф = 3 mm),无润滑干摩擦,旋转速度V = 200 r/min,载荷G = 300 g,测试圆周直径6 mm,对磨时间t = 60 min,试验温度为室温,相对湿度为30%左右。在摩擦磨损测试前对陶瓷层的表面进行了打磨与抛光处理,处理后的膜层粗糙度约为0.3 μm。摩擦磨损试验后,使用表面轮廓仪(TR200)得到磨痕的截面宽度d、深度截面积S,带入公式(2)中计算得出磨损速率ν [19]。
(2)
3. 结果及讨论
3.1. 电参数
图2为试样表面电流密度与时间的关系曲线。实验初期,试样表面形成的钝化膜 [20] 被迅速击穿,电流急剧增加并迅速到达峰值,形成峰值电流,此时陶瓷层进入快速增长阶段,在试样表面出现大量均匀分布的细密白色火花;之后进入稳定增长阶段且持续时间较长,电流逐渐下降并趋于平稳,该阶段不断产生的无定形氧化物薄膜在体系的高温高压环境下转变为稳定的晶体结构;微弧氧化末期,试样表面火花密度与移动速度降低,电流进一步降低,进入熄弧阶段。从图2不难看出,峰值电流随正向占空比的增大先增大再减小,以正向占空比为25%的峰值电流最高。另外还可看出,在正向占空比为20%、25%时,分别在8 min与16 min时出现了电流、电压突然急剧升高的异常放电现象。这是由于陶瓷层表面微区的不均匀放电导致的剧烈击穿现象。可能原因是正向占空比过高,导致放电时间过长,而负向占空比过低,不能起到很好的中和作用,从而在陶瓷层表面凸起微区积累了大量电荷,出现了尖角效应 [21] (试样表面电场分布不均匀,电流倾向于集中在试样表面的尖锐微区,导致尖角上更强烈的火花,被称为尖角效应)。
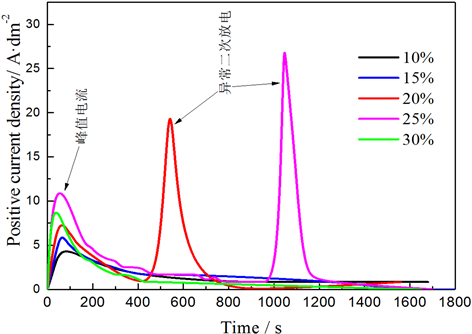
Figure 2. Curve of anode current density versus time for micro-arc oxidation of aluminum alloy
图2. 铝合金微弧氧化正向电流密度与时间的关系曲线
3.2. 陶瓷层相组成
为清楚的观察MAO陶瓷涂层中各相(γ-Al2O3与Al)的变化趋势,在图3中展示了陶瓷层在不同正向占空比下陶瓷层的各相的XRD图谱。可以看到明显的Al、α-Al2O3与γ-Al2O3的衍射峰。Al的衍射峰来自铝合金基体,当正向占空比小于25%时,随占空比增大,2θ = 38˚处α-Al2O3的衍射峰的半高宽变小,峰值增大,2θ = 39.276˚处出现了新的γ-Al2O3衍射峰。说明占空比增大所带来的高能量脉冲提供了高度电离的高温瞬变场,可以促进微弧氧化前期陶瓷层的快速形成,且易造成陶瓷层沉积层分布不均,导致了尖角效应,加快了无定形氧化物和亚稳态氧化铝向热稳定晶相转变,这些成分的高温相变过程如公式(2)所示。
但在正向占空比为30%时,氧化铝的峰值降低,2θ = 39.276˚处的衍射峰几近消失。这说明随正向占空比的进一步增大,陶瓷层的结晶度降低,电量利用率反而降低。
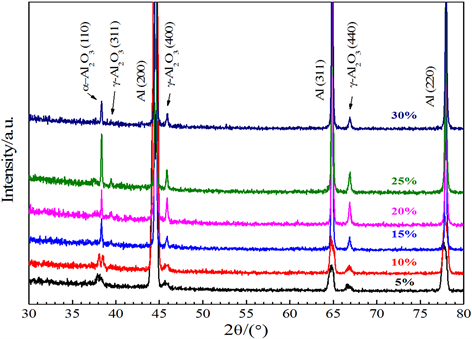
Figure 3. XRD spectra of ceramic coating surface prepared at different duty cycles
图3. 不同占空比下制备的陶瓷层表面XRD图谱
3.3. 陶瓷层表面形貌
图4显示了不同正向占空比下微弧氧化陶瓷层的表面形貌,陶瓷层具有微孔、氧化物颗粒和裂纹等特征。与低占空比下制备的微弧氧化陶瓷层相比,占空比较高条件下制备的陶瓷层拥有更少但更大的微孔,且大孔周围的微孔分布更为细密均匀。可以认为在占空比为5%~25%范围内,增大占空比,可降低铝合金微弧氧化陶瓷层的微孔尺寸,使陶瓷层大部分区域更为致密,陶瓷层的孔隙率降低。但占空比较大(20%, 25%)时,陶瓷层表面出现了尺寸较大的大孔,大孔周围存在一定规模的瘤状氧化物,可归因于实验中出现的异常放电现象。微区的不均匀放电,在铝合金基体与氧化物间产生了规模较大的放电通道,产生的大量熔融态氧化物在高温高压下部分喷出,在通道口冷淬,进而提高了陶瓷层的致密性。而正向占空比为30 %时,单个脉冲的过长时间持续放电造成膜层内应力过高,导致陶瓷层表面微孔的尺寸与数量反而增大,膜层表面出现了大规模贯通的裂纹,陶瓷层的粗糙度增大。改变正向占空比,即改变了液态氧化物形成和凝固的规模与分布,随正向占空比增大,陶瓷层的孔隙率先减小后增大。
图5为不同正向占空比下陶瓷层的截面形貌。在每个陶瓷层上选取十个位置,使用Photoshop软件的Ruler Tool计算截面厚度,并计算平均值作为陶瓷层的厚度。具体数值如表1所示。陶瓷层的厚度先随正向占空比的增大而增大,在占空比为25%时陶瓷层最厚,而在占空比进一步增大至30%时,陶瓷层的厚度反而降低。占空比低(5%至20%)时,陶瓷层内部结构较为疏松。
3.4. 陶瓷层硬度
对不同正向占空比下制备的铝合金微弧氧陶瓷层的硬度进行表征,见图6。5 N载荷下,陶瓷层硬度均高于铝合金基体(75 HV0.5)。陶瓷层的硬度随占空比增大总体呈上升趋势,正向占空比为25%时陶瓷层硬度最高(1107 HV0.5)。但正向占空比为30%时陶瓷层硬度大幅降低。可能原因是,击穿放电时间过长,放电微孔中喷射到陶瓷层表面的熔融物越多,陶瓷层比较疏松。结合陶瓷层的XRD图谱,占空比为25%下制备的陶瓷层中氧化铝的含量较大、结晶度较好,故硬度较高。
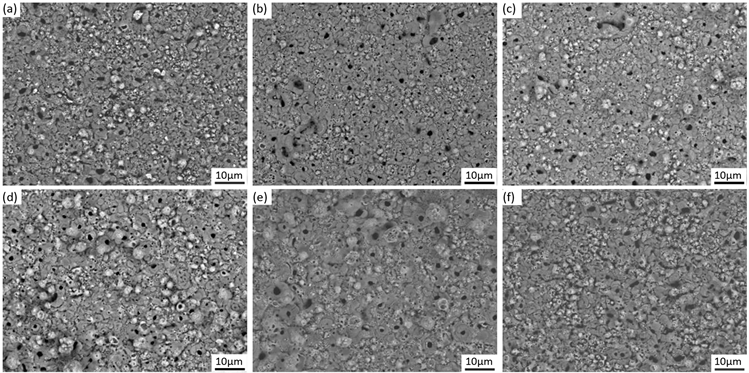
Figure 4. Surface morphology of ceramic coatings with different anode duty cycles: (a) D+ = 5%; (b) D+ = 10%; (c) D+ = 15%; (d) D+ = 20%; (e) D+ = 25%; (f) D+ = 30%
图4. 不同正向占空比下所得陶瓷层的表面形貌:(a) D+ = 5%;(b) D+ = 10%;(c) D+ = 15%;(d) D+ = 20%;(e) D+ = 25%;(f) D+ = 30%
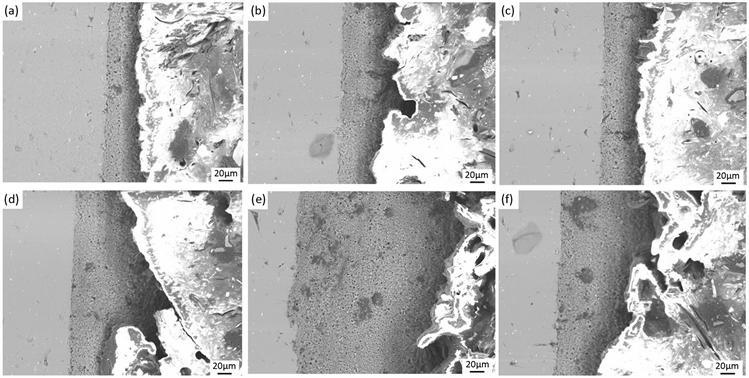
Figure 5. Cross section morphology of ceramic coatings with different anode duty cycles: (a) D+ = 5%; (b) D+ = 10%; (c) D+ = 15%; (d) D+ = 20%; (e) D+ = 25%; (f) D+ = 30%
图5. 不同正向占空比下陶瓷层的截面形貌:(a) D+ = 5%;(b) D+ = 10%;(c) D+ = 15%;(d) D+ = 20%;(e) D+ = 25%;(f) D+ = 30%
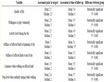
Table 1. Thickness of MAO ceramic coatings
表1. 微弧氧化陶瓷层的厚度
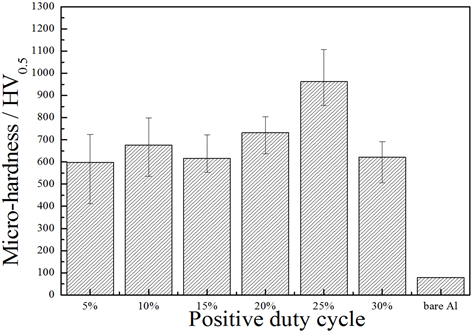
Figure 6. Hardness of micro-arc oxidation ceramic coatings at different duty cycles
图6. 不同占空比下微弧氧化陶瓷层的硬度
3.5. 陶瓷层摩擦磨损性能
图7为经摩擦磨损试验60 min后得到的陶瓷层摩擦系数曲线。各陶瓷层的平均摩擦系数为μ5% = 0.5719,μ10% = 0.4578,μ15% = 0.5344,μ20% = 0.4804,μ25% = 0.5400,μ30% = 0.4933。不同正向占空比下其摩擦系数曲线存在明显交叠,从平均摩擦系数来看,10%与30%的正向占空比的陶瓷层的平均摩擦系数较其他陶瓷层略低,但整体相差不大。
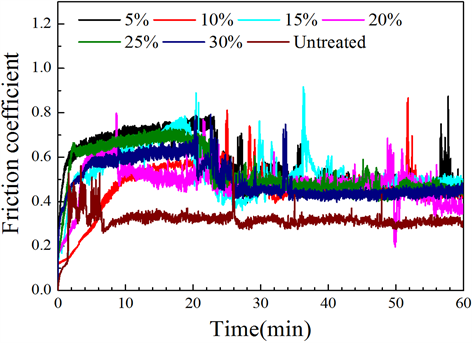
Figure 7. Friction coefficient of micro-arc oxidation ceramic coatings
图7. 微弧氧化陶瓷层的摩擦系数
从整个摩擦系数曲线看,各陶瓷层均明显存在磨合与稳定摩擦阶段,陶瓷层摩擦系数均高于铝合金基体。占空比为25%时磨合阶段用时最短,且稳定磨合阶段较长,摩擦系数相对稳定,这是因为高硬度的陶瓷层抵抗弹塑性形变的能力越强,同时陶瓷层表面的瘤状隆起最先与对偶件接触,这两点能够大大降低陶瓷层的磨损程度;产生的磨粒与对偶件和陶瓷层迅速形成了高质量的稳定摩擦系统,使陶瓷层在22 min时由稳定摩擦阶段平稳进入下一个稳定摩擦阶段,陶瓷层较耐磨。占空比为10%时,磨合阶段用时最长(约10 min),表明此阶段大规模的低硬度的陶瓷层被切削、磨平;摩擦后期,摩擦系数出现剧烈波动,陶瓷层相对占空比为25%的陶瓷层受损严重。其他陶瓷层的摩擦系数总体波动较大,在不同的摩擦时期显示出一定弊端,如:占空比为5%时,稳定摩擦阶段摩擦系数偏高;占空比为15%的摩擦系数整体波动较大;占空比为20%的稳定摩擦时间稍短(约为5 min);占空比为30%的摩擦系数在20~36 min阶段波动较大等。
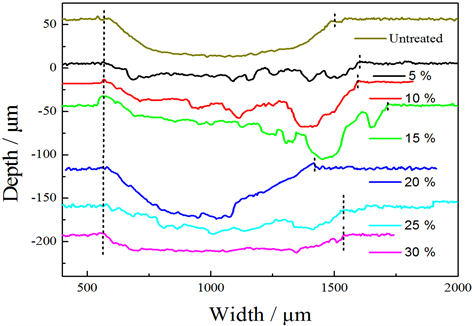
Figure 8. Abrasion profile of micro-arc oxidation ceramic coating
图8. 微弧氧化陶瓷层的磨痕轮廓
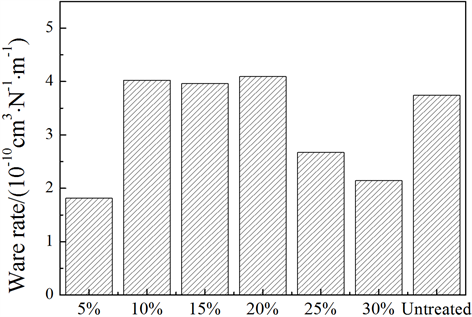
Figure 9. Wear rate of micro-arc oxidation ceramic coatings
图9. 微弧氧化陶瓷层的磨损率
图8为2A50铝合金在不同正向占空比下陶瓷层摩擦磨损60 min磨痕轮廓图。图中显示,在相同磨损条件下,未处理的铝合金磨痕轮廓最宽且深。进行微弧氧化处理后,正向占空比为5%和25%时磨痕宽度相差不大,且其磨痕较浅。正向占空比为10%的磨痕部分地区磨痕较深,对应于其较长的磨合阶段可知,摩擦过程中出现了剥落磨粒对陶瓷层的深度切削行为,陶瓷层受损严重。正向占空比设置为10%~20%时,制备得到的陶瓷层的磨痕较深,这是陶瓷层结晶度低造成的。将磨痕轮廓数据带入到磨损率公式计算后,可得到磨损率,如图9所示。在正向占空比较低(5%)或较高(25%, 30%)时,陶瓷层的磨损率较低,且远低于未进行微弧氧化处理样品的磨损率。
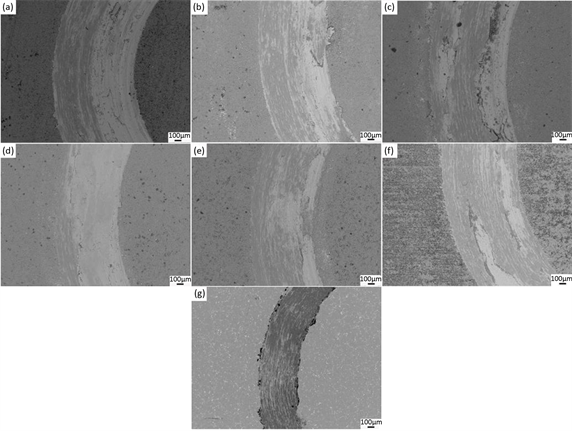
Figure 10. Surface morphology of worn tracks of the micro-arc oxidation ceramic coatings: (a) D+ = 5%; (b) D+ = 10%; (c) D+ = 15%; (d) D+ = 20%; (e) D+ = 25%; (f) D+ = 30%; (g) Untreated
图10. 微弧氧化陶瓷层的磨痕表面形貌:(a) D+ = 5%;(b) D+ = 10%;(c) D+ = 15%;(d) D+ = 20%;(e) D+ = 25%;(f) D+ = 30%;(g) Untreated
然而,由图10对陶瓷层的表面磨痕进行分析可知,25%的陶瓷层的磨痕宽度最窄,边缘未见明显磨屑堆积,磨痕未见明显犁沟,表明此参数下制备的陶瓷层,够能在以较少的切削量在接触面形成连续、平整且高粘附力的高质量转移保护膜,进而使陶瓷层平稳进入第二次稳定摩擦阶段直至摩擦磨损试验结束,其磨损机制为轻度的粘着磨损,具有最好的耐磨性。而磨损率较低的5%与30%的磨痕表面反而存在大规模的犁沟、破裂、与磨粒特征,说明初期的磨粒能够在摩擦行为中形成不耐磨的转移膜,此时磨损机制由磨粒磨损转至粘着磨损,而低硬度的转移膜在摩擦后期出现剥落,与新的磨粒对陶瓷层进一步破坏,磨损机制再由粘着磨损转至严重的磨粒磨损,陶瓷层相应的摩擦系数也出现了明显的波动。此过程中大量陶瓷层被重新磨碎碾压在陶瓷层表面,导致了磨损严重但磨痕轮廓较浅的假象。
4. 结论
在恒压模式下,控制正向占空比在5%~30%的范围内,固定负向占空比为5%不变,探究陶瓷层的耐磨性。随着正向占空比的增大,峰值电流先增大后减小。膜层主要相组成为α与γ相氧化铝。正向占空比小于25%时,氧化铝的衍射峰随正向占空比的增大而趋于尖锐,峰值增强,表明陶瓷层结晶度高。正向占空比为25%时,脉冲能量利用率最高,产生的高温瞬变场促进了α相氧化铝的产生,并生成了新的γ相氧化铝,陶瓷层结晶度最好。正向占空比高于25%时,陶瓷层结晶度降低,电量利用率反而下降。随着正向占空比的增大,陶瓷层的孔隙率先减小后增大,膜层厚度先增大后减小,实验过程中的异常放电现象增加了陶瓷层的厚度但未降低陶瓷层的致密性。在正向占空比为25%时,陶瓷层微观结构最为致密。正向占空比为25%时膜层硬度最大,为1107 HV0.5。正向占空比为25%时陶瓷层综合耐磨性最好,摩擦系数最为平稳,存在2个稳定摩擦阶段。平均摩擦系数较低,为0.4804,磨损率为2.67 × 10−10cm3∙N−1∙m−1,磨痕轮廓规整,无磨屑堆积,能够在摩擦接触面形成耐磨且粘附性高的润滑性保护膜,磨损机制为轻微的黏着磨损。
基金项目
国家自然科学基金(51101080),辽宁省“兴辽英才计划”项目(XLYC1807170);辽宁省“百千万人才工程”培养经费。