1. 引言
适用于长距离输送的多档索道由于考虑到中间支架的强度和稳定性,承载索与支撑鞍座之间会随着运载货物的移动而发生滑动 [1]。
对于索道承载索与鞍座的滑移摩擦参数研究问题,国内外鲜有文献对其进行相关分析和研究。通过调研与之类似的实际工程,比如悬索桥主缆与鞍座间的摩擦滑移以及预应力钢索与孔道之间的接触摩擦,可以看出,绳索同鞍座的接触摩擦滑移是高度非线性问题。大多数学者采用模型试验设计或借助于商业软件进行数值计算等手段进行相关摩擦特性研究。文献 [2] 设计了悬索桥主缆与鞍座间摩擦系数模型试验,在试验中,考虑了实桥在使用阶段索股的主缆与鞍座间的实际接触应力对摩擦系数的影响;文献 [3] 设计并实施了对弯曲孔道接触的模拟试验,运用CT技术及ANSYS软件计算得到了所需的接触区域应力值,分析讨论了转角、曲率半径、索拉力、摩擦等因素与法向应力分布的关系;文献 [4] 通过对弯曲孔道拱角预应力钢索进行自平衡计算,得到接触压力荷载公式,根据公式将索力和接触压力分布荷载施加在物体的有限元模型上,通过将有限元计算结果与试验结果进行比较,验证公式的适用性;文献 [5] 分析了弦支夸顶环索连续贯通的摩擦问题。以上方法针对具体工程条件进行了结构摩擦分析,可以为索道承载索钢丝绳与鞍座间的摩擦分析提供指导。
本文在现有接触理论的基础上,提出适用于承载索与鞍座的摩擦系数,并在有限元模型中进行数值仿真计算,与试验结果进行对比分析。
2. 承载索与鞍座接触摩擦
1) 接触特点
货运索道承载索与鞍座的接触问题属于一种较为复杂的接触形式:
a) 接触物特殊。作为相互接触的物体之一,承载索一般采用柔性较好的“6 × 7钢丝 + 1纤维芯”钢丝绳,其接触形态不同于实体。
b) 接触区域呈空间弧形窄条。承载索与鞍座接触类似于以轴线平行方式接触的两圆柱体接触问题,但两圆柱体也沿纵向有弯曲,如图1所示。所以接触区域是空间的弧形窄条。这种独特的接触区域没有固定的切平面,给几何学描述造成了极大的困难。工程实际中,此类问题大多选择简化到承载索中心线所在的yz平面进行二维接触分析,如图2所示。
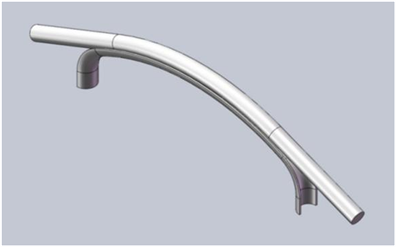
Figure 1. Contact relationship between load-bearing cable and saddle
图1. 承载索与鞍座接触关系
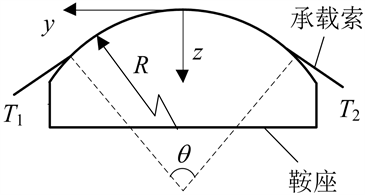
Figure 2. The yz plane where the centerline of the load-bearing cable lies
图2. 承载索中心线所在的yz平面
2) 接触摩擦系数
影响摩擦系数的因素很多,如正压力的大小、材料种类、滑动速度、表面粗糙程度、表面膜、变形温度等等,所以摩擦系数的值一般由实验来确定。
a) 滑动速度
为了简单起见,经常假设动摩擦系数与滑动速度无关。根据本课题的需要,测试的承载索与鞍座间的摩擦系数应为承载索刚好发生滑移瞬间的最大静摩擦系数。所以对摩擦系数的研究不会涉及到滑动速度对摩擦系数的影响。
b) 表面粗糙度
非常粗糙的表面,表面须越过另一表面的微凸体,摩擦系数高。而非常光滑的表面摩擦系数甚至更高,原因是非常光滑的表面实际接触面积大,分子间相互作用增强,从而对相对滑动的阻碍作用更强。在塑性接触下,实际接触面积总是与载荷成正比的,表面粗糙程度对摩擦系数的影响并不大。
本文在承载索与鞍座摩擦力试验测量结果的基础上进行,承载索与鞍座间的摩擦系数已由承载索两端张力与鞍座压力的比值获得 [6]。
3. 滑移摩擦力仿真计算
3.1. 接触摩擦分析有限元模型
利用ANSYS有限元分析软件模拟承载索与鞍座摩擦滑移模型试验,建立“6钢丝股 + 1纤维芯”钢丝绳模型,截面如图3所示。分析承载索在鞍座槽内的摩擦行为,得到试验过程中的摩擦力大小。
根据钢丝绳实际参数特性,钢丝股设置为各向异性材料,中间的纤维芯设置为刚度较小的各向同性材料,具体材料参数设置如表1所示。
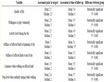
Table 1. Wire rope material parameter table
表1. 钢丝绳材料参数表
有限元进行接触分析时是采用建立接触单元的方式来求解两构件之间的接触问题的,有时也称为界面单元,也就是有限元接触分析中接触对的概念。承载索与鞍座接触摩擦行为属于面面接触,二者均采用实体单元划分网格,接触单元分别为CONTACT174和TARGET170单元。建立模型如图4所示。
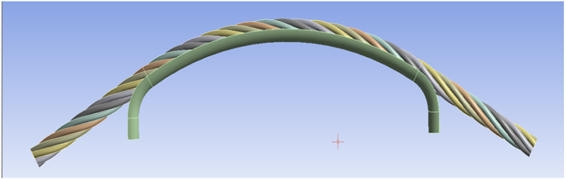
Figure 4. Contact friction model of load-bearing cable and saddle
图4. 承载索与鞍座接触摩擦模型
3.2. 接触摩擦力计算
将测量得到的摩擦系数 [6],输入到有限元模型中。通过有限元模拟计算获得承载索与鞍座间的摩擦力大小,同试验数据形成对比,验证试验数据的准确性。
为了减少数值模拟的工作量,本文应用正交试验方法选取9种工况对Φ20 mm钢丝绳的摩擦力大小进行数值模拟计算,具体工况见表2。
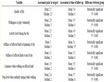
Table 2. Numerical simulation condition table
表2. 数值模拟工况表
3.3. 结果分析
通过模拟计算得到不同工况下钢丝绳同鞍座的接触摩擦力。从图5可以看出,摩擦应力在钢丝绳同鞍座接触中心应力最大,沿着中心线对称两侧逐渐减小。
摩擦力试验测量结果与仿真模拟计算结果的对比如表3所示。
从表3可以看出,应用ANSYS软件模拟计算得到的摩擦力大小同试验值较为接近,除第一个工况为8.42%,其他工况误差均在5%以内,考虑到试验操作误差,可以认为数值模拟与试验的相对误差在可以接受的范围内,说明试验数据及模拟方法均是正确的。
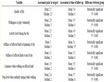
Table 3. Numerical simulation error analysis
表3. 数值模拟误差分析
4. 总结
承载索和鞍座摩擦试验方案设计工况和结果数据,应用数值方法对二者的摩擦特性进行了分析。通过理论公式计算得到承载索与鞍座不同工况下的摩擦系数,代入有限元模型中进行数值模拟计算。最终,将获得的摩擦力模拟数据同试验数据进行了比较,误差相对较小,验证了计算方法的正确性。如有必要,在该数值模型基础上,可以将承载索与鞍座的接触摩擦行为推广到更普遍的工况。
基金项目
国家电网公司科技项目“基于高精度数据的索道路径规划及部件选型一体化技术研究”(SGSDJS00TGJS2000185)。